Drawer construction
If you make cabinets, you gotta make drawers. Lots of drawers. A lot of shops are buying their drawers from specialty shops now but most of us still make our…
If you make cabinets, you gotta make drawers. Lots of drawers. A lot of shops are buying their drawers from specialty shops now but most of us still make our drawers in house. I, for one, don't see any reason to give the work to someone else, especially now when things are a bit tighter than they have been in the past.
I have always preferred to build my drawers out of solid stock. I've done a lot of jobs where budget constraints called for plywood drawers. But, for the most part, I favor solid wood with plywood bottoms. The big question is always what joinery to use. More often than not, dovetailed drawer joints enter into the conversation.
Most people suffer under the delusion that dovetails represent the highest order of fine craftsmanship. But in truth, dovetails require only that the craftsman be able to accurately cut to a line with a chisel and saw. Those are (or should be) pretty basic skills. The real reason dovetails became ubiquitous for drawer construction had much more to do with the unreliability of the available adhesives than with any desire to exhibit high levels of skill. When woodworkers were limited to animal hide glue, the question was never if the glue would fail but when. So a mechanical interlock was necessary to prevent the drawer from simply falling apart once the glue gave up.
Also, drawers were typically of much heavier construction and the weight combined with the friction of the wood runners resulted in a lot of force being exerted on the joints that held the front and sides together.
Once we got to the point where we had more dependable adhesives and steel ball bearing hardware glides, these concerns were no longer an issue. But the practice of dovetailing drawers has persisted and, even though 99 percent of all dovetail drawer joints are formed with routers and jigs, people still see the dovetailed drawer as an indication of a quality piece, regardless of how cheap or low quality the thing actually is.
The joint of choice for drawers in my shop is the rabbet and groove. Over the last 20 years I have made thousands of drawers with rabbet and groove joints and I have yet to have one fail. In fact, they are virtually impossible to take apart without destroying the drawer. These joints are very easy to make and do not require any tooling other than a small straight cutter for the groove and a bigger one (or a rabbeting bit) to make the rabbets. I like to stop the groove a quarter of an inch from the top of the sides and "nip" the tops of the tongues formed by rabbeting the sides. That way, you cannot see the joint. Also, I will often make the sides a half inch or so taller than the fronts and backs and run a small ogee along the top edge of the sides which creates a very nice looking drawer.
I use the same joint for all four corners. Some shops will use dados to let the backs into the sides and nail the joints but I could never see any advantage to using a different joint for the backs. Maybe if you were hand-cutting dovetails, the dado at the back might make sense. But for machined joints, it never made sense to me to have to go through a bunch of different setups.
Now that I have totally "dissed" dovetails, I should add I do use them. But only on my best work and then they are always hand cut and always with very small pins so that there is no way they could ever be mistaken for machine made joints. OK ... there is one other condition under which I will make dovetailed drawers. If the customer insists on it and if I really want the job and the issue of drawer joinery becomes a deal killer, then I'll haul out my dovetail jig.
D.D.
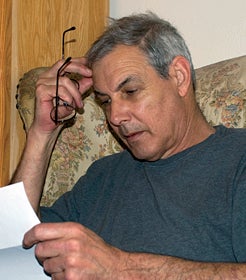
David DeCristoforo possesses an extensive resume as designer/maker of fine furniture, high-end cabinetry and architectural woodwork. His experience in professional woodworking spans a period of 35 years. For the past 20 years David DeCristoforo Design has been located in Woodland, California. During this time David's shop has ranged in scope from a "full on" cabinet production shop with as many as 15 employees to a small fine furniture and custom millwork shop, working with his son, David RBJ, a highly skilled maker in his own right.