TigerAngle makes angles automatic
TigerStop has automated the process of cutting compound angles with the new TigerAngle. The TigerAngle is an entire miter saw station featuring TigerStop’s material length and angle positioning systems, operational…
TigerStop has automated the process of cutting compound angles with the new TigerAngle.
The TigerAngle is an entire miter saw station featuring TigerStop’s material length and angle positioning systems, operational software, a material clamping system and safety innovations.
“TigerAngle automates the angle cutting process for different manufacturing processes. If you’re working in furniture, cabinetry, windows, it’s going to automate the compound miter process by making it simpler and more precise,” marketing manager Dominick Olavarria says.
“Manufacturers using crosscut applications who are manually setting stops and setting angles are often checking and rechecking, miscutting and then doing it all over again. This product eliminates setup, test cuts and parts and adds true dynamic optimization to the manufacturing process.”
The TigerAngle comes with a Graule saw retrofitted with TigerStop drives. It shines in a high production environment, but is also capable of making single, repeatable cuts with great accuracy in smaller shops, according to Olavarria.
Other features include a pusher foot that automatically feeds material, a safety hood or protected zone where the cutting occurs and a built-in clamp system.
The supplied Beamworks software, developed by TigerStop specifically for TigerAngle, allows the operator to create or download cut lists directly to the tool’s computer, receive operator feedback with visual representations of materials, and store repeat jobs.
The TigerAngle starts at $50,000. Upgrades can bring the price to $70,000.
Contact: TigerStop. Tel: 360-254-0661. www.tigerstop.com
This article originally appeared in the May 2014 issue.
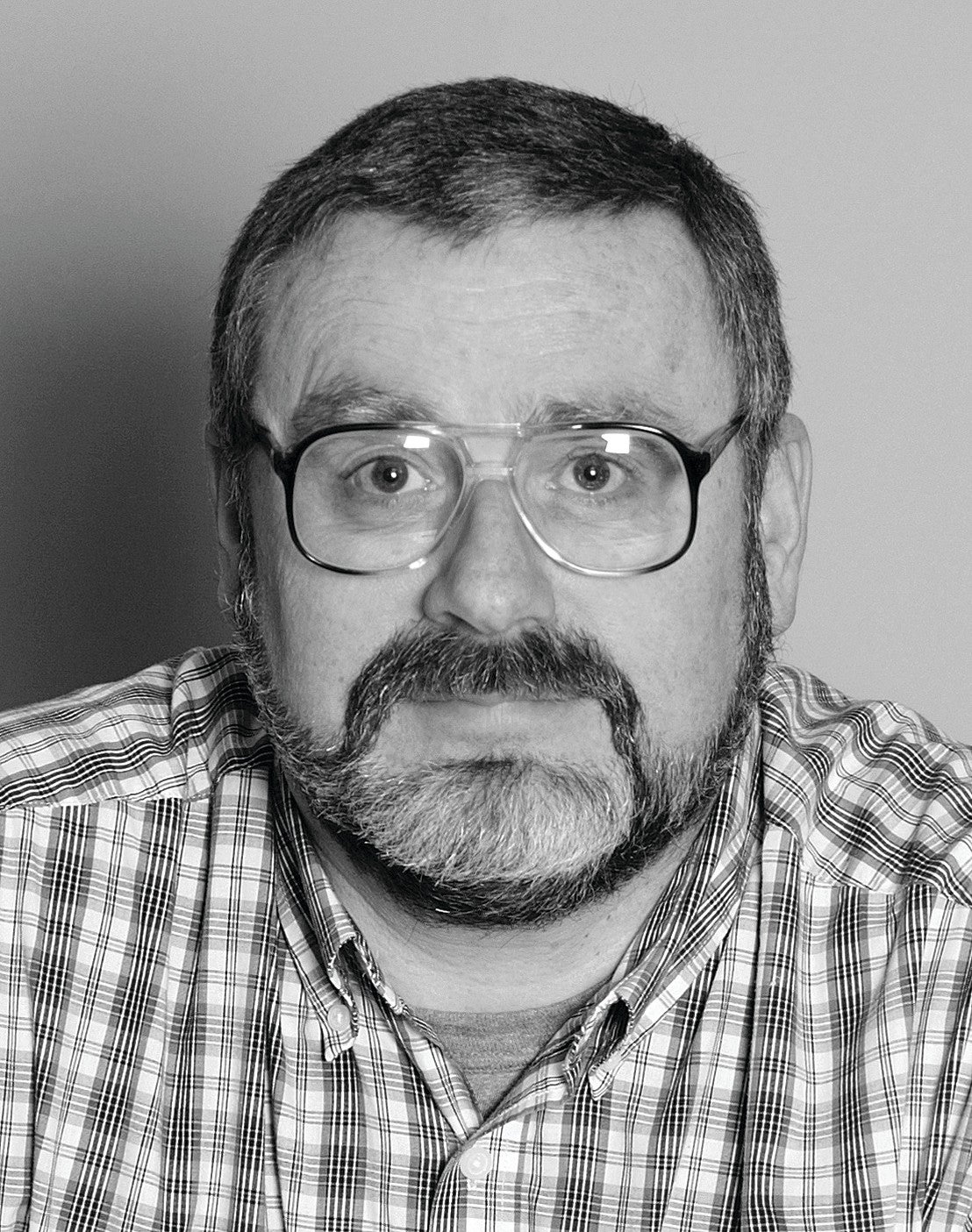