Spindles, aggregate heads open a world of possibilities
Spindles, aggregate heads open a world of possibilities.
Spindles can be confusing, especially for woodworkers just getting into CNC machinery. An indication of the scope of available options is that Precision Drive Systems (spindlerepair.com) lists a staggering 150 spindle brands that it repairs.
Most woodshops tend to stick with the spindle that came with their machine, at least for a while. But this is a rapidly evolving technology and it pays to check back with the router’s manufacturer every now and then, just to see what’s new. For example, there might be an auto lube upgrade available. Some older spindles use a series of pressurized grease shots to lube their bearings, while newer ones generally use a constant oily mist that’s carried by compressed air. Bearing failure and wear is still a big issue with spindles, but less than it used to be. And too much lube is about as detrimental as too little. Heat buildup from the workload is an issue, too, and shops might want to check if there are any advances in water or air-cooled systems for their specific spindle. Some manufacturers are now leaning toward air even on their smaller units (although there may be a trade-off in RPMs), plus the cost of a water pump and delivery system can become an issue.
Small shops considering a first CNC or upgrading a small machine might seriously consider going with a spindle over a portable router. Some of the advantages include less noise, more intricately controllable speed (which is determined by software, not a rheostat, so it can be varied even in the middle of a task), and less run-out. There are also more power and more collet size options – especially if you’re using small cutters for tasks such as engraving that come in something other than a 1/4” diameter shank. And there are definitely more opportunities to upgrade. Entry-level spindles are surprisingly affordable, but as with most advanced technology, you get what you pay for. If you have an inverter, a 3-phase spindle will deliver more torque at lower speeds, for all-day tasks. The most common type of variable frequency drive (VFD, a device that is used to control the speed of AC induction motors) is a voltage source inverter that actually converts single phase to 3-phase.
And if you can find a local expert or spindle repair shop to change out a router for a spindle, that usually makes a lot more sense than having to learn the entire process yourself. The software alone can be a big challenge.
Consider adding some spindle alarms, too, if your machine didn’t come with them. The most common are thermal (heat sensing) and some general alarms that react to travel issues (where the tool might cut into the machine, or travel too fast), excess run-out, and other speed/torque issues.
Larger shops might want to temper spindle investment decisions by also considering what is happening in robotics. Collaborative robots (also known as cobots or co-robots) are machines that physically work with and alongside human workers. Outfitting a robotic arm with a spindle turns it into an incredibly versatile tool because of the arm’s dexterity and ability to move in all planes.
But robots are expensive, and a woodshop that doesn’t see one in its future might want to consider upgrading the standard CNC spindle by adding an aggregate head.
Aggregate heads
When a woodworker is buying a table saw, there’s only a short list of parameters to consider – table size, horsepower, blade diameter, tilt and so on. But when a shop invests in a CNC router, that list becomes a whole lot longer. Many of the items on it are related to future growth and adaptation, rather than immediate needs. With the table saw, upgrades over the years are usually going to be limited to a better fence, a few jigs and perhaps some more efficient dust collection. But the bottom line is that the saw only performs three or four linear tasks – crosscuts, rips, grooving and maybe some limited molding cuts. And that’s all it will ever do. The work needs to be fed to the blade. Saws obviously have an essential and highly valuable role to play, but they’re just not that versatile.
With a CNC workstation, the options are a lot more complicated. Most cabinet shops initially invest in a CNC router just to release flat casework parts from sheet stock. But it doesn’t take long to realize that, because the tool moves to the work, this equipment has a lot more potential. The first job the shop takes on that demands some complex joinery, or perhaps turned components, will undoubtedly have an operator exploring how the CNC can work in more than three axes. Woodworkers soon tire of repositioning and re-securing parts so that the tool in the spindle can reach a different face of the workpiece. It’s time-consuming and eats away at accuracy. And it’s downright disappointing to have to revert to that old table saw because the spindle can’t make a cut at a specific angle.
The answer to these frustrations is probably an aggregate head, which in essence adds another axis to the machine. It’s a device that attaches to the spindle and uses a set of gears to swivel and turn in ways the standard spindle can’t. It lets a woodworker use the CNC router to run a saw blade, rout or carve vertically instead of horizontally (that is, work on the sides of a part rather than just the top and edges), and perform more machining tasks without having to move the part. Essentially, a standard spindle holds tools perpendicular to the table and aggregate heads can hold them at various angles. Some aggregate heads require the addition of a C axis, or at least benefit from one, but many are modular and can rotate manually. Most shops explore the aggregate option because being able to complete more processes without dismounting or re-clamping the work leads to reduced material handling, and faster production times. But not all small CNCs can be adapted to accommodate an aggregate head, and this is something to consider, and ask about, when purchasing a router.
Not all spindles can handle an aggregate head, and if a shop is working with a salesperson on specs for a new router, this may be something to invest in right away. If not, the spindle may need to be upgraded down the road. You’ll need to match the aggregate head to the collet system. They’re usually available for standard connections such as HSK63F, SK30 or ISO30.
And not all toolholders can handle an aggregate head, while others only accept them in some locations. Some CNCs can have the tool bar modified, such that the factory spec tool bar won’t allow the mounting of an aggregate head, but the modified one will. And sometimes a woodworker can make a manual tool change, just inserting the aggregate head manually. That can also be an option if the head is simply too large for the carousel.
Speed bumps
Aggregate heads aren’t a magic solution for every situation. They do have some potential limits. For example, they’re not always as sturdy or durable as the simple, straight spindles that hold them, so the shop needs to talk with the salesperson about how they will be used. Most aggregate heads work best on short milling or cutting operations, rather than consistently being asked to perform hi-torque tasks for a long period of time.
The tooling is an issue, too. Because of resistance, router bits, saw blades and profiling tools or even engraving tools all cause heat to build up in different ways, as does the density and workability of the material (MDF, hardwoods, plastics) that is being milled, cut or shaped.
It’s important to discuss with the salesperson, or probably more appropriately the supplier’s service department, how the head is to be cooled and lubed, and consequently to institute a regimen in the shop whereby operators understand any required procedures and abide by them. Grease can burn off at a pretty low temperature and leave the gears running metal-on-metal with no lube. That’ll make the head heat up exponentially.
While many heads come with a gauge attached, if an alarm is available too it can be a good investment. Or the shop might consider upgrading to a head that is equipped with an oil bath, and these generally have a larger body that helps to dissipate thermal build-up.
Unfortunately, that latter consideration can also be a trade-off. Because the aggregate head will be attached to the spindle and stored in the toolholder’s carousel, its size and weight may well become a limiting factor. Most heads are built with lightweight metals such as aluminum or cast alloys, and while these are usually quite adequate for most tasks, they lack the shear, shock and compression resistance of steel. So, they need to be a bit bulkier.
There’s a lot to think about when shopping for an aggregate head, but there’s also a lot that one of these devices can do for a smaller shop that wants to get the most out of its CNC router.
This article originally appeared in the September 2019 issue.
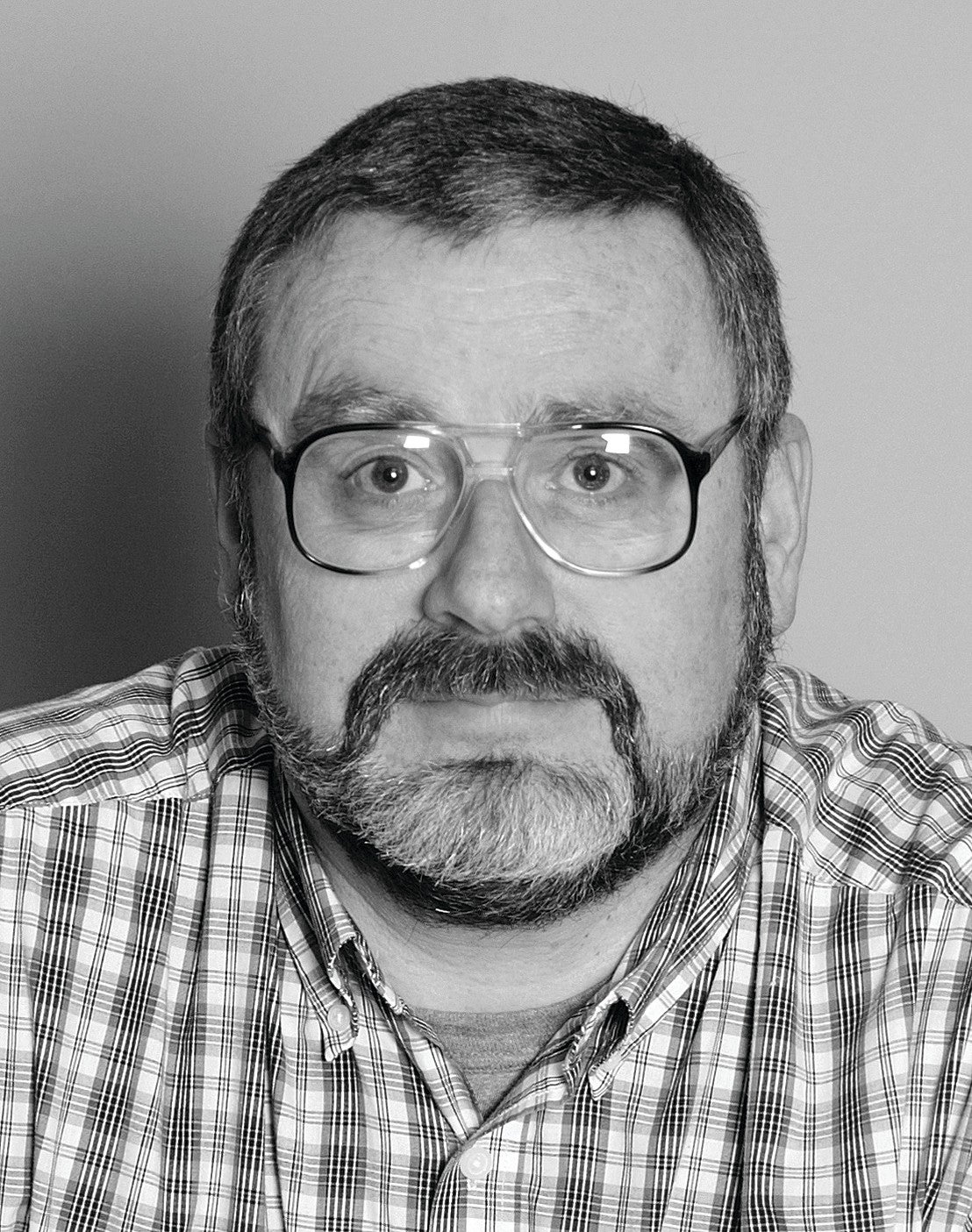