Getting to know abrasives
Choosing the best abrasive for a specific task begins with an understanding of how they’re made and perform.
Given how fast technology moves, keeping up with abrasive options can be a challenge.
When cabinetmakers or furniture builders are choosing the best abrasive for a specific task, they need to consider the material’s physical properties, its grit size and the nature of the backer (paper, fabric etc.). It helps when a manufacturer volunteers lots of information up front, but woodworkers still need to know some basics just to interpret what they’re being told.
A good example is Festool USA (festoolusa.com), which describes its Granat abrasive as hardened aluminum oxide, synthetic resin and closed coated. But that also describes several of its other sandpapers, including Brilliant, Rubin and Titan. All three of those are also built with aluminum oxide and synthetic resin, but the differences lie in the treatments they receive. Brilliant has an anti-static coating that works well with waterborne finishes, while Rubin has a special coating that sheds wood fibers. And Titan has a high-quality latex coating on its backing that increases flexibility, which in turn allows it to adapt to surface contours. Another Festool product, Vlies, can be ordered with either aluminum oxide or silicon carbide abrasive, and Festool offers a stearate option on the silicon carbide version. (Stearate is a soapy ingredient that reduces clogging.)
Given so many variations on the same theme, it’s easy to see why a woodworker needs to know something about abrasive technology before making informed choices. And that information needs to cover aspects such as a sandpaper’s durability, resistance to clogging, the ability to self-renew, its scratch patterns, and its cost.
One of the first choices relates to density. Most abrasive discs and belts have open coat structures where there is less abrasive and more space between the grains. Closed coats deliver fewer scratches but clog up faster than open coats. With more material on them, closed coats can erode faster than open coats, so they are often used to fine sand coatings and tight-grained hardwoods. The voids on open coats are designed to relieve clogging, so open coatings are more appropriate in the earlier stages of sanding. They are also more suited to sanding resinous woods such as pines, and resinous coatings such as paint.
The main choices for backing are paper, cloth/fabric, and film. Paper is flat, which makes it ideal for sheets. It’s also flexible, and how much so depends on its thickness. That is graded using letters, where A is the most flexible. Stiffer paper gives less, so it cuts faster and deeper in the coarser grits. Thin paper is used in fine grit grades because the granules of abrasives can move slightly, and act in a gentler manner. Thin papers are also better at working profiles such as moldings and round-overs.
A lot of belts and random orbit discs use a cloth or fabric backing, which is usually infused with a resin. Most cloth backers are relatively stiff (denoted as X), such as the belts in a portable belt sander. Highly flexible cloth backers are identified with a letter J, and there are further variations within each category that are also described using letters.
Film is essentially a plastic backing and is most often used in fine and very fine grits because it offers such a flat and even base upon which to build. It’s very common in the autobody industry where it can be used with soaps and other liquids.
Types of abrasives
The least expensive, and probably the least effective abrasive choice, is old-fashioned brown flint paper. It’s not very common anymore and is really not a commercially viable solution for production shops. One indication of an abrasive’s durability is how easy it is to crush and grind it to create the ‘sand’ on sandpaper. Flint doesn’t do well here – it comes in at last place after zirconium, aluminum oxides, silicon carbide and emery.
The next cost option, garnet, is one of the more widely used abrasives among hobbyists, and especially so for hand sanding. That’s probably because it’s inexpensive to manufacture as a sheet or disc, so marketing may have as much to do with its popularity as actual results do. This orange-red material occurs naturally and is mined and ground but is not usually altered much beyond that. It’s more aggressive than flint, but many professional furniture builders find that it wears down too quickly when used with electric sanders. Garnet is essentially a rock so it can be found in several chemical varieties, including iron and magnesium-based aluminum silicates.
A finer and more durable choice, aluminum oxide, is very popular in most facets of woodworking and is also relatively inexpensive. This is a manmade material that lasts longer and abrades better than garnet. It’s not very crystalline in shape, and under a microscope it looks more like a series of wide-based, narrow topped spikes than traditional crystal forms. Because of that, it doesn’t always renew by breaking down to expose new facets (that is, it’s not overly ‘friable’). In fact, the abrasive edges can round over before they shatter, and that can lead to some clogging. Overall, this is a great choice for working wood.
Another bauxite derivative, alumina zirconia, is a manmade abrasive that has distinct crystalline facets and these allow it to renew its edges. Unfortunately, it works best in coarse grains, so it isn’t the abrasive of choice for final passes. But it does a great job of removing stock in a hurry. Zirconia is a manmade diamond and can be used as a stand-alone abrasive as well as being incorporated into compounds. Diamond abrasives can also contain low quality (impure) natural industrial diamonds, including dust and chip residue harvested from other commercial processes. Diamonds are incredibly hard, which is both good and bad. It means that they last a long, long time, but it also means they can cost a lot. Ceramics are produced in a somewhat similar manner, and they continue to grow in popularity.
Silicon carbide is another manmade abrasive, and this material is known for its brittle, crystalline nature. It is both very hard and sharp, and renews well, so it’s perhaps a better choice for finish sanding. It’s also a bit more expensive, but that seems to even out because of the time it saves, and the avoidance of re-working. It can usually be used wet or dry (depending on the backer) and is generally black in color. There is a slight chance that the dark grains will dislodge and become visible on some light-colored wood species, but this usually isn’t a problem.
Emery is technically an abrasive but is often considered more of a polishing agent. It’s a natural aluminum oxide corundum, and it can be purchased in very fine grits. It’s most often used between coats in built-up finishes. However, it can have an uneven texture and may leave visible lines in a finish. Plus, it can sometimes have an adverse effect on tannin in woods such as oak, where it may alter the color over time. Very fine grits of silicon carbide and even aluminum oxide will deliver fairly comparable results.
Another cloth, sometimes but not very often employed to polish a coating, is crocus. It’s a fabric that is used to apply a rouge (such as is used in sharpening). Crocus is more commonly used as an abrasive among silversmiths and the like than in woodshops.
Restorers, rather than production cabinetmakers or even furniture artists, are more familiar with older solutions such as rotten stone, pumice and powdered glass. These abrasives often have very narrow applications and are perhaps more of an art than a craft solution. Also popular with hand sanding artisans and sometimes wood turners are steel wool and abrasive sponges, but some furniture and casework shops try to avoid these because of residue and rust issues.
Sources
Many woodworking abrasives were born in body shops. For example, the Cubitron family of abrasives from 3M (3m.com) was originally created to meet the needs of metalworkers. It has 3M’s patented Precision-Shaped Grain, which is designed with sharp, angular structures that continuously fracture to form points. These allow the abrasive to slice faster, run cooler, and last longer than other abrasives that can generate heat buildup, and thereby have a shorter life. 3M says that its latest generation of Cubitron II products can cut faster and last up to twice as long as competitive products.
Over the past 30 years, Mirka USA (mirkawoodworking.us) has grown into one of the world’s largest producers of coated abrasives. Its product range includes not only familiar abrasive products such as Abranet and Deros, but also tools, accessories and polishing components.
Uneeda Enterprizes in Spring Valley, N.Y. (sandpaper.com) offers “the widest range of abrasive products for the woodworking industry, from wide belts to sanding discs,” according to the company.
SuperMax Tools (supermaxtools.com) carries a full range of abrasive wraps for its drum sander line.
Gator/Ali Industries (gatorfinishing.com) has a large catalog of power and hand sanding products, and Ali also offers premium, professional quality abrasive products through its Shopsmith brand (shopsmithabrasives.com).
Klingspor (klingspor.com) has been manufacturing abrasive technologies since 1893 and offers a huge range of discs and belts.
Keystone Abrasives (keystoneabrasives.com) in Reading, Pa. offers belts, discs, sheets, drums and other abrasive products.
Maryland-based 2Sand.com is an online supplier that carries a wide range of sanding discs, sanding belts, sandpaper sheets, specialty products and sanding accessories.
Sungold Abrasives (sungoldabrasives.com) also manufactures a full line of sanding belts, sheets, discs, rolls and related products.
Indianapolis-based Sandpaper America (sandpaperamerica.com) offers a similar range of products. And for contour and detail sanding, Opti-Sand (opti-sand.com) offers machines and abrasives in a flexible finger format.
This article originally appeared in the January 2020 issue.
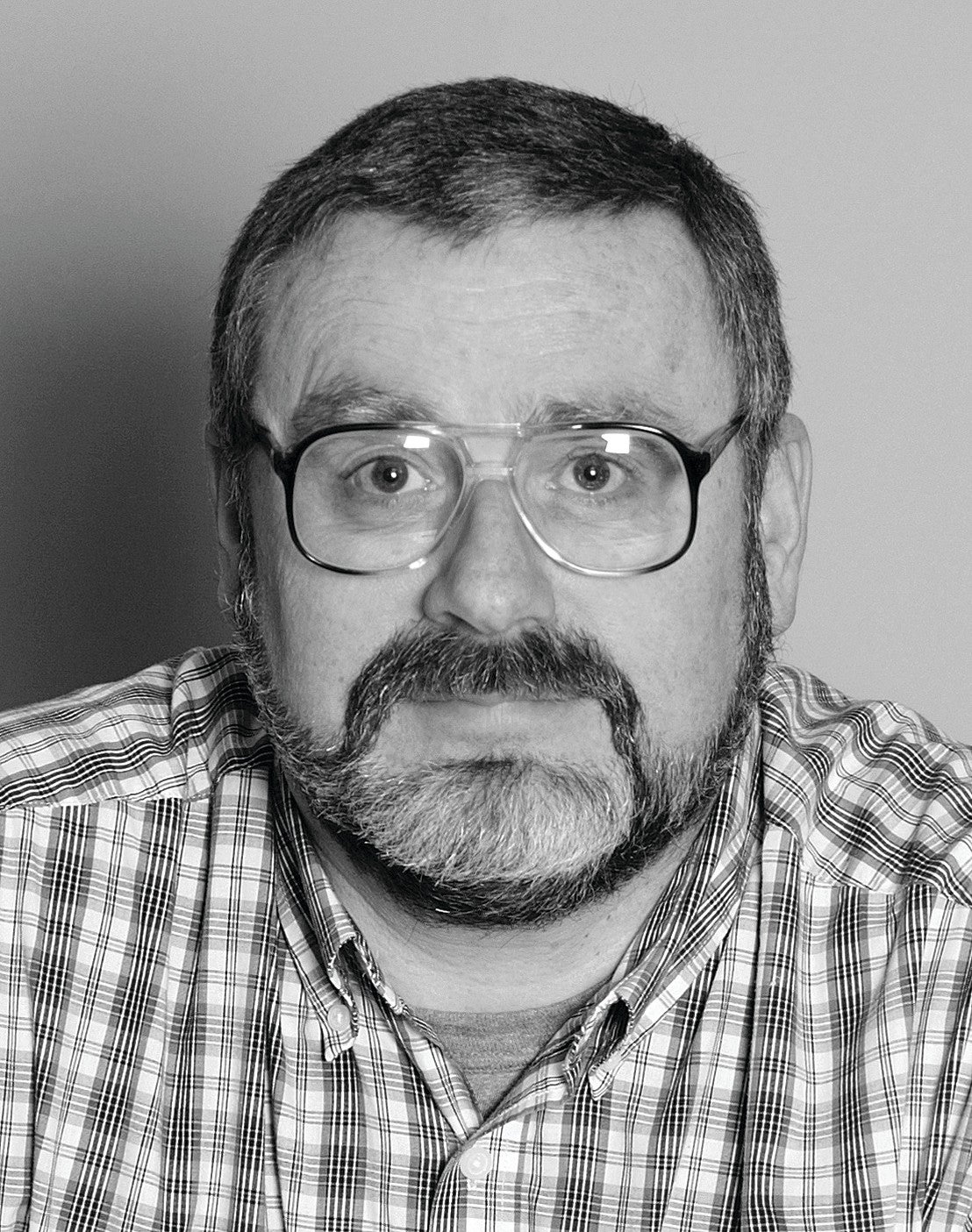