Airing their differences
An explanation of how compressed air systems operate and what works best for a particular application
In lay terms, a positive displacement air compressor basically pumps air into a tank until it meets a certain pressure. The air is then regulated by a valve as it is released. That should sound familiar to most carpenters and small woodshop owners. It’s Grandpa’s compressor, and we still use them every day.
A dynamic displacement compressor, on the other hand, is simpler in theory but more sophisticated in practice. It uses bladed impellors (more on those in a minute) to basically push the air through a diffuser, which is a spiral-shaped circular chamber with a small opening. Dynamic compressors are usually smaller than positive displacement models that are doing the same work, and they’re also less likely to vibrate. That makes them more appealing for sensitive equipment. They also create a constant flow of compressed air within a very narrow pressure range. The concept is something like having just a pump and no tank on your jobsite compressor.
Dynamic compressors are ideal for all-day work when they’re hooked up to a tool or machine that needs constant and steady pressure. Because they don’t have to use a tank (and in some applications they do), they don’t need to cycle as it fills and empties. Dynamic compressors can also work in stages where the air is compressed and then pushed by another impellor through another diffuser, and so on, to build up the pressure.
There are a couple of different types of dynamic compression. Centrifugal units are by far the most common, but some applications do better with axial compression.
Centrifugal compressors have those impellers mentioned earlier. These look like a flat plate on one face, with wings and swirls on the other and a hole down the middle. The massive one (in photo at right) was used for compressing and moving water at the Grand Coulee Dam on the Columbia River in Washington. The photo shows a crew installing the impeller in an upgrade on the dam in 1947. Called a waterwheel, this impeller was so large that it had to be made by ship builders in Newport, Va. who were used to making ocean-going ships’ propellors. If you’ve ever looked inside a small dust collector, its shape will look familiar. In addition to forcing air to compress, impellers also change the direction of the airflow.
Axial compressors have a shaft running the length of the compressor cylinder, and there is a series of small fan blades that slide onto an axis that stretches from one end to the other. So, axial compressors don’t change the direction of the air. They just hurry it up as it passes through, following the direction of the axis. The air is accelerated and then run through the diffuser to increase the pressure.
The very familiar reciprocating or piston compressor that can be found in every small woodshop and on most jobsites uses positive displacement. These machines are relatively inexpensive, and there are dozens of major manufacturers to choose from. They’re simple machines with just a motor, a pump, and a tank, so they’re easy to fix and maintain. Any one of those three elements can usually be replaced, even on a unit that is decades old, and can probably be done on the jobsite.
On the downside, reciprocating units are generally quite bulky and weighty, so most models above the pancake size need to have built-in wheels and larger units are just not portable. Plus, the ones you can move are a pain to get up and into the back of a pickup. That sheer mass is one reason that battery-powered tools have replaced many of the nailers, staplers, caulk guns and other tools traditionally used in conjunction with a compressor. But reciprocating compressors still deliver more power than batteries, and they are still far more popular than cordless or plug-in tools in some applications such as the spray booth. Many high-volume cabinet shops also prefer pneumatic guns because there’s no downtime charging and changing batteries, and the pressure is constant and reliable.
Rotary compressors
The next most popular option, the rotary screw compressor, has evolved quite a bit over the last few years. This type of compressor traps air between two large bolt-like screws that are meshed or synchronized together to form a seal as they rotate. The threads run in opposite directions, so the point of contact moves as they revolve. Air is pushed ahead of the point of contact into an ever-reducing space, where it is compressed into a smaller volume. There was a time when rotary screw compressors never got to travel outside the shop, but they’re getting smaller and easier to use.
The traditional rotary screw compressor used oil injection as a lubricant and seal, which was fine when they were providing air in automotive or industrial environments. Wood doesn’t like oil, so a new generation of rotary screw compressors used in the wood industry are oil-free. Unfortunately, they cost a bit more than their oily relatives because they need to add a compression stage to be as productive. Larger versions of the rotary screw concept are more industrial in nature and are valued for longevity, durability and reliability. They usually have a free-standing lube system (it can be finicky), and they can deliver a higher volume of air under pressure in continuous use. And even though larger ones often have a high initial cost, a new unit will probably outlive most woodworkers.
The other type of rotary compressor uses moving vanes instead of a pair of screws to create compression. Think of a hollow cylinder with a shaft (called a rotor) inside it that is slightly offset. As the shaft rotates, it’s just about snug to the wall of the cylinder at one side, so there’s a gap at the other side. There are slots in the shaft, and each one (usually at least three of them) has a floating vane in it. These vanes are just flat sheets of carbon or graphite, and as the shaft rotates the centrifugal force that it creates makes the vanes slide out from the center. They trap the air, and they squeeze it into a smaller space as they rotate. This type of compressor has been around for hundreds of years and is usually found in compressors that don’t require a very high psi. The rotary screw compressor is more efficient at higher pressure.
Pneumatic tools
For the most part, the pneumatic tools used in woodshops and on jobsites don’t really care about the source of their compressed air because they’re not that sensitive to undulations in pressure. Most of them operate at significantly lower pressure than the generator can produce, so the only real concern is volume – having enough air. Run several framing guns off a pancake compressor and you’ll understand very quickly about volume: it presents itself as long periods of waiting for the compressor to recharge.
One-man woodshops running on a small compressor, or large shops with a stationary beast and piped air rarely need to play that jobsite catch-up game. The pneumatic tools most used in woodshops (pinners, staplers, etc.) don’t require a great deal of compressed air. Unlike the air-gulping pneumatic sanders used in autobody shops, the wood industry primarily uses electric random orbit sanders.
There is a new generation of tools that are technically pneumatic, but they don’t require a compressor. These are guns with little battery-powered motors than compress air into cylinders right inside the tool, so they act and feel like a compressor-fed gun but without the hoses. Other manufacturers use small gas cylinders and minute explosions to generate enough power to let a tool go cordless.
This article was originally published in the June 2022 issue.
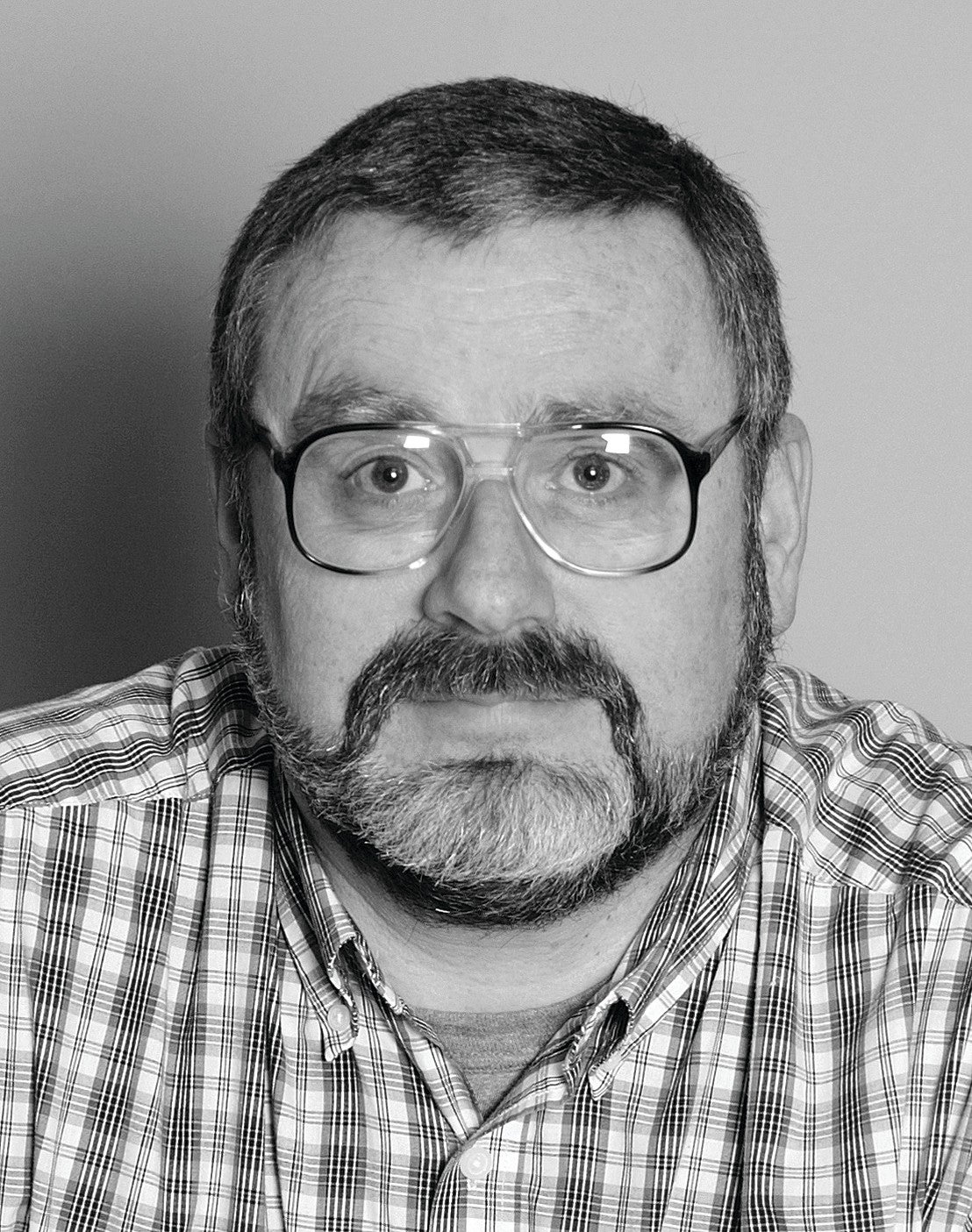