Aggregate heads: A new angle of approach
An aggregate head is essentially a 90-degree gearbox that is designed to allow a CNC to be set up with more than one tool and/or more than one angle of…
An aggregate head is essentially a 90-degree gearbox that is designed to allow a CNC to be set up with more than one tool and/or more than one angle of approach.
That is to say, a basic CNC router works vertically and runs one tool or bit, just like an overarm router. The tool is chucked in the bottom of the spindle and the entire assembly moves down toward the work when told to do so.
An aggregate head can be simple or complex. It might accommodate more tools for sawing, routing, drilling and shaping or give you the option of working horizontally (for example, on the side of a part, rather than on the top) or do both. Some adjustable heads also offer the option of choosing an angle somewhere between vertical and horizontal.
Think about how handy it is to be able to use a right-angle drill attachment in the confines of a cabinet. Well, an adjustable aggregate head is that on steroids. They attach to the spindle and accommodate knives, saw blades, molders and bits. The ability to add more tooling means that several setup processes a day can be eliminated which, of course, avoids excessive parts handling and the potential for nicks and scrapes.
Do the parts being made on your CNC router need to go to another workstation (perhaps a shaper, router table or molder) to have their edges milled? If so, you might want to look at an angle head.
Not all CNC routers will accept one. Call your dealer to check on a machine that you already own or lease or one that you are about to purchase. Some CNCs will only accept certain brands or models of aggregate heads — often because the physical space is simply not large enough. Others might require the addition of a C axis (a large offset plate that attaches to the spindle). Before you buy one, check to make sure there are no other options available at a lower cost.
For an angle/aggregate head to work properly in the spindle, it needs to be locked in a way that doesn’t allow it to spin, usually with an anti-rotation steel pin. Some heads can be physically rotated with or without a C axis: you have to stop, make the adjustment, lock the pin and then fire up again. Some tool holders and carousels might not be able to accept aggregate heads and others might not be able to handle them automatically, but will accommodate manual insertion. Again, check before you buy.
For and against
In general, a small shop using a CNC to just mill casework parts might only gain a limited benefit from investing in an aggregate head. If one falls in your lap, you’ll certainly find ways to put it to work, but for the rest of us the investment requires some thought.
If, on the other hand, a woodshop is milling parts with lots of profiles or angles (for example, corner china hutches), an aggregate head can be a gift from the gods. It will, for example, run a saw blade at a 45-degree angle, which is a lot more efficient than chewing waste off the edges of cabinet sides with a chamfering bit. And the tip of a pointed bit, if used for grooving and chucked in a vertical spindle, has virtually no cutting power. But chuck a grooving bit in a horizontal head and it has a lot more edge contact with the work, so it will cut cleaner and faster.
Aggregate heads can make a lot of sense in the furniture-making world, too. If a shop has the resources, adding a sophisticated aggregate/angle head to a CNC router can allow it to mill angled contours, which opens up a whole new range of shapes and three-dimensional manufacturing possibilities.
But while these heads can speed up production and reduce materials handling, there are some issues to consider before making a purchase. Even though they are not far removed from the primary power source (the vertical spindle), they are still an extension so they have limitations when it comes to drag. Check with the manufacturer and mention how deep the cuts will be, what materials are being milled (in terms of both density and resins) and how long the bit will be buried in the wood. Too much heat build-up can be detrimental to the aggregate head and could cause excessive wear or even failure. That’s because many of the manufacturers use aluminum and other lightweight components, so the heads aren’t too physically heavy for tool changers. There’s a power-to-weight tradeoff here.
Many heads use grease as a lube and excessive heat can break down the viscosity of grease, causing it to thin and actually evaporate. Take a look at oil-cooled heads if this is going to be an issue. There, the teeth on the gears are submerged in a bath of lube that can tolerate much higher temperatures. Think about your automobile: grease is used on the chassis, but oil is used in the engine.
Aggregate heads usually spin faster than the original spindle powering them, so check that the tooling you are using is appropriate for the speed. Some heads come with an option to reduce the delivered velocity and this might be appropriate for larger cutters and saw blades. Think, too, about the speed at which the tool traverses the path: an adjustment here might also be appropriate. Your tooling and head/spindle suppliers can offer specific advice.
Supplier offerings
For more than six decades, engineers at Benz Inc. in Hickory, N.C. have been designing and building angle heads for all kinds of applications. The company suggests that, when choosing an angle head, one should consider the spindle motor size. Benz maintains that the absolute minimum is 5-hp, which makes sense as you’re asking the machine to do more work. If your spindle motor connection isn’t one of the most common versions (HSK 63F, HSK 63E, ISO 30, SK 30, BT 30, BT 35 or BT 40) the company might be able to supply an angle head for a spindle that has a simple nut-and-collet style connection.
Regarding automatic tool changes with an aggregate head, you should refer to the maximum weight capacity of your tool carousel. And keep in mind that, when placing an angle head in the carousel, it’s not uncommon that the tool holder position on either side of the angle head might be lost simply because of size. Be sure to check that there is enough clearance around the carousel so that the tooling doesn’t start milling your CNC.
Many angle heads are simply too heavy for a tool change carousel, but these can often be manually inserted into a spindle motor. Benz suggests contacting the router’s OEM for a custom solution that will allow automatic tool changes, such as an independent aggregate “garage” that is typically located at one end of the machine table.
Based in Indianapolis, Techniks designs and distributes industrial cutting tools including aggregate heads, and offers a comprehensive range of aggregate heads through its SmartLine, FunctionLine and UltraLine brands.
SmartLine aggregate heads have a compact, lightweight design and are intended for operations where improved clearance or maneuverability is required. FunctionLine offers the widest selection of heads and are among the company’s most versatile grease lubricated aggregates. UltraLine aggregates are oil-bath lubricated for continuous operation in extreme conditions.
GDP Guhdo manufactures heads with HSK63F, SK30 and ISO30 connections. It offers a wide variety of saw blades for grooving and sawing, complete with the required countersunk holes for mounting on an aggregate head connection. Specialized tooling, including disposable insert and polycrystalline diamond (PCD) is also available, as are grooving heads for the Lamello Clamex P system. The company’s aggregates fit most CNC machining centers including those made by Weeke, Holz-Her and Homag, as well as point-to-point machines.
For aggregate head supplier information, visit the online Resource Guide at www.woodshopnews.com.
This article originally appeared in the May 2016 issue.
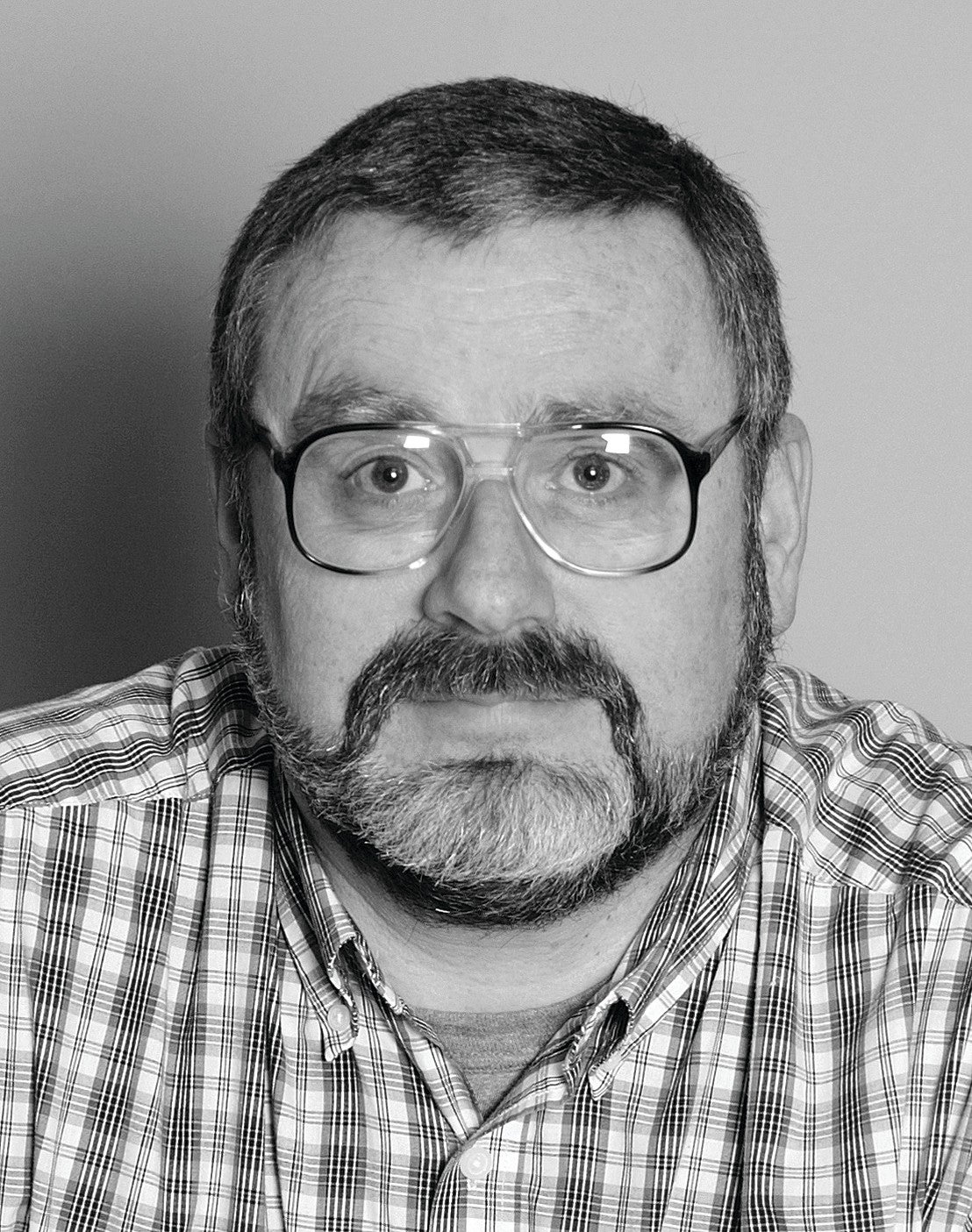