You dont need to work in cramped quarters
Woodshop inventory comes in three forms. There are raw materials such as plywood, hardwoods and hardware. Then there is work in progress, which is anything from individual parts to fully…
Woodshop inventory comes in three forms. There are raw materials such as plywood, hardwoods and hardware. Then there is work in progress, which is anything from individual parts to fully assembled and unfinished casework. And finally there are completed jobs that are ready to be loaded and delivered/installed.
Each of these three phases requires a completely different approach when it comes to both warehousing them and moving them around the shop. There’s an entire industry that caters specifically to these needs and knowing what’s available can really help a woodshop become more efficient.
Intuitively, one would like to have raw materials at one end of the shop and finished cabinets or furniture at the other. But, in practice, things are usually a little more challenging. Most woodshops are not planned on paper and then built: they evolve through many years as we add machines, products and people. The majority of shop owners will buy, rent or build a space and then start filling it by placing the biggest machines in the center of the room. Or we’ll line them up so the dust collection works best. That makes a whole lot of sense and it’s perfectly workable when it comes to changing the way that materials are handled. It’s just not as flexible as a blank sheet of paper, so a little thought and planning are required to make things more efficient.
Exactly what are you doing?
Staging (how we store things) has changed for a lot of shops in the last few years because of two industrywide trends. The first is the addition of CNC capabilities and the second is the number of shops that now outsource components such as boxes, drawers and doors. A few years ago, the typical staging area for raw materials was a plywood rack, a hardwoods rack, a set of shelves for hardware and a small room where finish, sandpaper and other supplies were kept. The process was cut, mill, assemble, sand, finish and install.
Today, the boxes might be shipped in a flat pack to the customer’s home and assembled on site. Or they could arrive at the shop already finished and just need assembly and hardware. A lot of custom cabinet shops pass jobs through where there is virtually no in-house cutting or milling at all. But their people are still working in a shop where a sliding table saw sits in the middle of the room and all of the exterior walls host other machines because that’s where the wiring was.
Is it time to reorganize? Is it time to consider the possibility that your shop’s activities now have more to do with handling materials than manufacturing them? With a lot of shops, at least part of the process has changed and perhaps it’s time to take a look at that.
Changing the workflow can be as simple as moving some storage racks and using the pallet jack to rearrange a few piles of wood. But, for most of us, things aren’t quite that simple. One option a lot of shops are choosing is adding conveyor tables, so the guys don’t need to physically pick up parts from the saw and haul them to the CNC or load carts full of drawers and push them across the shop to get drilled for pulls. Perhaps a few inexpensive conveyor tables could take care of some of that? Companies such as Grainger carry a wide variety of these in different shapes, sizes and heights and most of them are simple, stand-alone frames with a platform on top that’s composed of a series of ball-bearing rollers.
Moving parts from one workstation to the next on roller tables does a few different things. First, it saves time because it can be a one-man job. A crewmember doesn’t have to interrupt somebody else and get help lifting cabinets onto and off shop carts. Next, it reduces the chance of injury when somebody lifts with their back instead of their legs: now, they’re barely being asked to lift at all. It also frees up shop space because you’re not parking a bunch of unused carts. And finally, it establishes pathways. That is, once the rollers are in place, that’s where the materials will travel. Jobs aren’t on carts all over the shop or stacked against the side of the saw or blocking aisles. Roller tables can even be organized like railways — they can have sidings so that one job is parked out of the way while another passes by. The tables are inexpensive enough to make this feasible.
Roller tables don’t have to be three feet off the floor. They can be installed without the legs and used to move entire cabinets from one workstation to the next, just inches off the ground. Again, it no longer takes two guys to carry cabinets around the shop. It’s a smarter, safer and less expensive way to handle many materials. And a little planning can use them to make a current shop configuration work better without having to move machines, walls, electrics, dust collection and so on.
Accessible inventory
In most shops it takes several minutes for a woodworker to find an empty cart, walk to the storage room, pull handles or slides, load them on the cart and then push it back to his/her workstation. You’re operating a cabinet shop, so why not build a cabinet for all the hardware, put it on big, smooth castors and park it where it’s needed? When UPS delivers a carton of knobs or shelf supports, the cart can be pushed to the loading dock or door and the new inventory can instantly be checked in and warehoused in its own mobile storage unit. Put doors and a padlock on the cart and the inventory is secure. Build a couple of carts and the crew can have one for slides, one for handles, one for finishing supplies, etc. Or each crewmember or workstation can have an individual cart — whatever works best to meet a shop’s specific needs. Big, readable signs that can be seen from across the shop are very inexpensive to have printed and avoid any confusion if the carts/cabinets all look alike.
Inventory that doesn’t fit in a cabinet requires different solutions, but even large items like plywood can be stored on mobile platforms that allow employees to work smarter, and safer. Thomas Mfg. in Girard, Kan., (www.thomasmanufacturing.com) is a member of the Wood Machinery Manufacturers Association, so the company is familiar with cabinet and furniture shop processes. Thomas makes several material-handling products and one of the most interesting is a heavy-duty adjustable work platform designed specifically for cabinet assembly stations. The height can be adjusted from 16” to 42” with a hand crank or hydraulically and the unit can be outfitted with wheels or casters to make it mobile (which would, of course, change the height). Built when ordered, sizes are completely customizable, so these platforms can handle anything from end panels to 5’ x 5’ sheet stock.
When a pallet of plywood arrives at the shop, one of these carts could be pulled to the loading bay and the stock could be placed on it. Then it could be rolled to a spot close to the CNC platform or the table saw and the height could be matched to the in-feed table of the machine. One person could safely slide the top sheet onto the machine and then adjust the height so the next sheet is lined up and ready to go. The sheet goods would be stocked flat with adequate support, so there would be no bowing as there can be over time in a vertical rack. The entire inventory can be moved from saw to router or another station (perhaps for plastic laminating) and done by one person.
Adjustable platforms also make a whole lot of sense when a cabinetmaker is assembling carcasses, because the height adjustment allows access to the top and bottom without having to roll the cabinet (which often requires stopping another worker to help). And they are ideal in the finishing room as they can be rolled around for 360-degree access and adjusted up and down for top and bottom access. They can even be rolled out to the delivery truck and raised, so large cabinets can be loaded easily, and more safely.
The Fairbanks Co. (www.fairbankscasters.com) in Rome, Ga., also supplies innovative solutions to the woodshop industry. Among its latest ideas is a series of small dollies that are ideal for moving casework around the shop. The largest is 18” to 30”, rated for 1,000 lbs., is only 4-9/16” off the floor and runs on 3” Polyolefin wheels. Another one is triangle-shaped with 20” sides and a set of four can handle even the largest assemblies such as library and entertainment center cabinets. The dollies have handles cut into them, making them easy to carry, and they all weight less than 18 lbs. Round corners make them safer for both casework and shins.
This article originally appeared in the December 2014 issue.
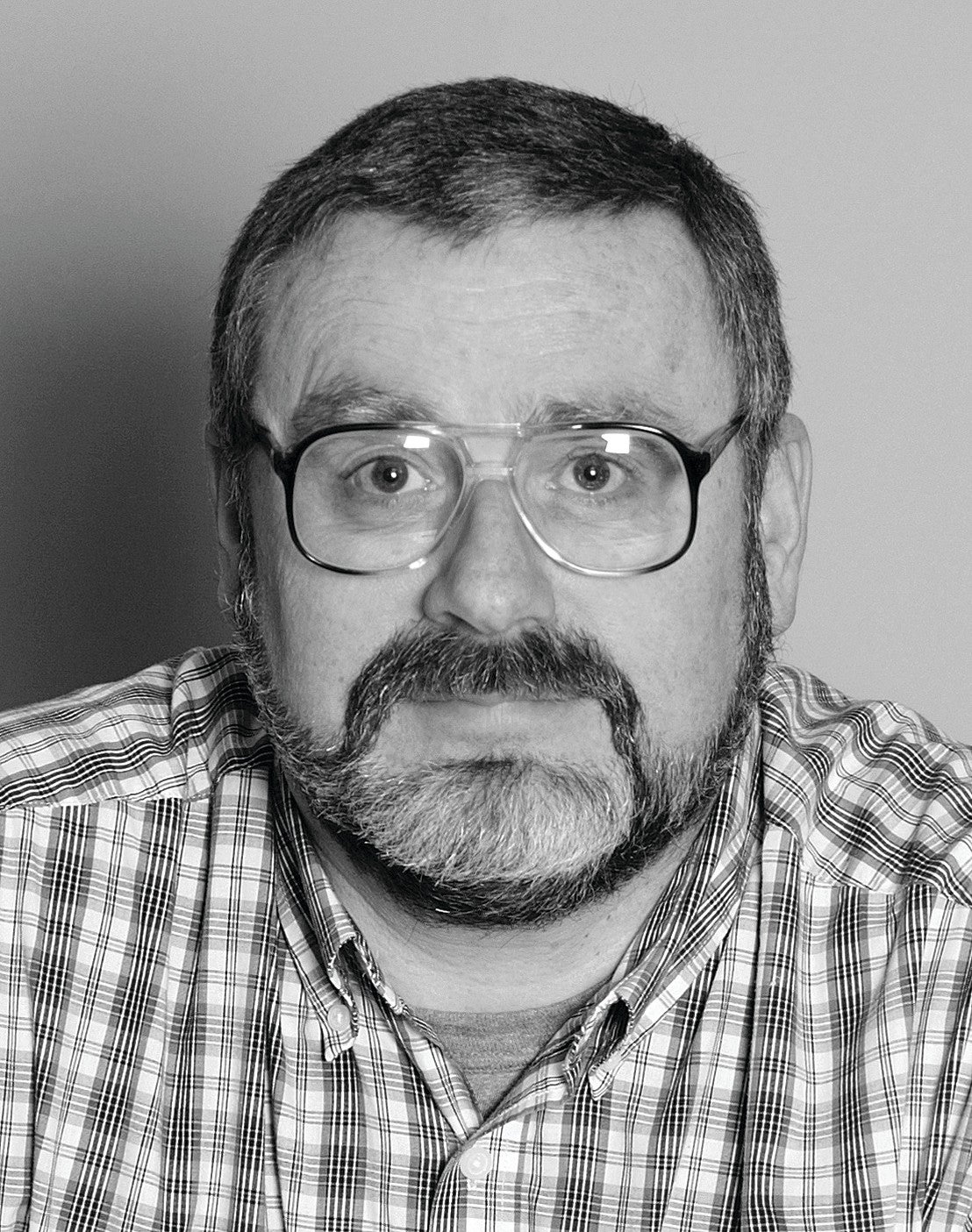