Wood movement
During my recent foray into economics and politics (good rip-roaring discussion there!) someone commented that I should forget all that and offer some advice about wood movement. Maybe that was…
During my recent foray into economics and politics (good rip-roaring discussion there!) someone commented that I should forget all that and offer some advice about wood movement. Maybe that was a "tongue in cheek" comment but I'm going to presume not.
So, just to lighten up a bit, here is a little anecdote about wood movement.
Some years ago, we were building a bunch of stuff for one of those over-the-top houses that seemed to be designed expressly to see how much expensive material could be consumed in the construction of one house. This job was all bird's-eye maple. And we needed a ton of it. Since most of the good bird's-eye goes directly to the veneer mill, there was a lot of veneering in this job. There were also a lot of very large pieces with big rounded corners, some of them having a six inch or larger radius. Much of the work was done with built up layers of moldings and much of that was cut and laminated from solid stock. But a lot of it had to be veneered and, because of the configuration of the pieces, much of that had to be done after the pieces were built.
We had hundreds of square feet of bird's-eye veneer that we had ordered with a phenolic backing. We figured that a lot of the veneering was going to be done with contact cement and everyone knows how risky it is to lay up raw or paper-backed veneers with contact cement.
So we had a shop full of massive pieces of casework being veneered and everything was going well. But one night a storm came in and the humidity went off the charts and most of the veneer was still unsealed. I was horrified the next morning to see that, in spite of the phenolic backing, the moisture had bubbled the veneer on over half of the radiused end panels. There was no way we were going to be able to remove and replace all that veneer. My wife asked if there wasn't someone we could call. I said, "Well, actually, I'm the one they call!" We had a very excited conference and decided to try some tricks. I knew that contact cement can be reactivated by heat and I also knew that aliphatic resin glue could be heat activated and that there was a good chance that heat and pressure would dry and shrink the veneer. So we got a clothes iron, a heat gun, a veneer hammer, some glue and a few syringes.
We spent the next three days heating and pressing and injecting glue under the stubborn spots. Some of the bubbles laid down again with very little effort. But some were stubborn, requiring us to slit the veneer and work glue underneath. It was a nerve-wracking couple of days. We sealed all of the veneer as we worked so that there would be a moisture barrier. That was risky in itself because we had talked about dying some of the pieces and the sealer would probably wreak havoc on that process. But we were using a lacquer-based sealer and figured that alcohol-based dyes would penetrate.
When I look back at times like that, I think it was a testament to stubbornness that I even stayed in business. But there was a certain satisfaction in overcoming such an obstacle and the job did turn out fine. Plus, I've always been a bit of a glutton for punishment.
D.D.
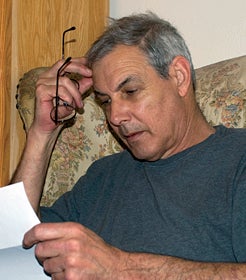
David DeCristoforo possesses an extensive resume as designer/maker of fine furniture, high-end cabinetry and architectural woodwork. His experience in professional woodworking spans a period of 35 years. For the past 20 years David DeCristoforo Design has been located in Woodland, California. During this time David's shop has ranged in scope from a "full on" cabinet production shop with as many as 15 employees to a small fine furniture and custom millwork shop, working with his son, David RBJ, a highly skilled maker in his own right.