Who ya’ gonna call?
There was this one project we had that was in bird’s-eye maple. It was a completely over-the-top project with a lot of very large pieces, embellished with built up moldings….
There was this one project we had that was in bird's-eye maple. It was a completely over-the-top project with a lot of very large pieces, embellished with built up moldings. And curves, lots of curves.
Not just radius, corner-type curves, but S-curved footprints, circular pieces all of which did, of course, have radius corners. Anywhere from 3” to 12”, these corners were everywhere. Flat panels made up about 25 percent of the doors; the rest were curved one way or another. And since most of the curves were different, tons of forms were needed.
At that time, bird's-eye maple was in huge demand overseas where it was commanding premium prices. This seriously affected the availability of clean, heavily figured wood, which is what the client insisted on, not to mention the price, which, fortunately, he considered to be no object, at least when it came to paying for the material! So the demands of the configuration combined with the cost and scarcity of material resulted in a lot of veneered work. We bought miles of veneer, much of it in the form of paper-backed sheets.
Wherever we could, veneer was applied with aliphatic resin glue and vacuum pressed. But there were a lot of pieces that were simply too large for this method to be practical. I tried hammer veneering with hot-melt glue that works well on small- to medium-sized pieces but was a real pain on the larger ones. I tried the technique where you coat both surfaces with aliphatic resin, let it dry and then use a hot iron and a veneer hammer to bond them. That worked pretty well, but again, not too well on the big stuff. So we finally decided to go against my better judgment and try contact cement. I was aware of the risks of using it with wood veneer but this was backed veneer.
To my surprise the contact cement worked well and the veneer stayed put. Except for one spot. Right at eye level on the biggest, most impressive and most prominent piece in the whole house! A large bubble appeared and it frustrated every attempt to get it to stick down. In fact, it seemed like the more we worked it, the worse it got. This piece was needed on the job site and the client was not a patient man! At the end of the day, I went home in panic mode and my wife, trying to chill me out, asked me why I didn't call someone for advice. That's when it hit me. I'm the one they call! I'm supposed to be the expert, the guy with all the answers. Who would I call?
At around two in the morning I awoke with an idea. I was at the shop at five with a hair dryer and a syringe with a fine needle. I figured I had one more shot. If this didn't work, I was going to have to strip the entire piece and start over. I thinned down a bit of glue and injected it under the veneer. There was a small crack in the bubble from our messing with it so I was able to work the needle in pretty easily. I worked the glue under the veneer as best I could and then started to slowly heat it with the hair dryer. As the veneer warmed, it shrank a bit and the glue began to dry. I started pressing with the veneer hammer, working slowly so as not to tear the thin veneer. I was finally able to get the bubble pressed down and the fix was almost invisible except for the hairline crack which I could easily camouflage if only the veneer would stay in place.
By the time the rest of the crew arrived, the veneer was still stuck with no sign of coming loose again. We touched up the crack, loaded up the unit and bought it to the job site. It weighed a ton and took six strong men to get it into the house. The veneer was still staying put but I still worried over it. The piece was installed and finished and still looking good so I gradually began to relax. But every time the client called, my stomach did flip-flops until I realized that the call was not to tell me there was a bubble in the veneer.
As far as I know, it's still stuck down!
D.D.
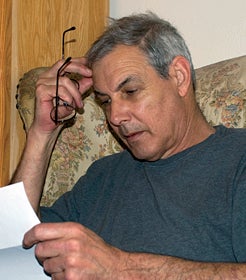
David DeCristoforo possesses an extensive resume as designer/maker of fine furniture, high-end cabinetry and architectural woodwork. His experience in professional woodworking spans a period of 35 years. For the past 20 years David DeCristoforo Design has been located in Woodland, California. During this time David's shop has ranged in scope from a "full on" cabinet production shop with as many as 15 employees to a small fine furniture and custom millwork shop, working with his son, David RBJ, a highly skilled maker in his own right.