Troubleshooting protocols
As the old saying goes, if I had a nickel for every time I got a call to tell me that something is not working at the shop, I could…
As the old saying goes, if I had a nickel for every time I got a call to tell me that something is not working at the shop, I could have retired long ago.
More often than not these calls end up being unnecessary. And they invariably come at the most awkward moment, right in the middle of trying to close a sale, for example, or just when you are trying to merge onto a busy freeway. So I have established a basic protocol for troubleshooting that circumvents 90 percent of these calls.
When an employee flips the switch on a machine and nothing happens, he should make the following checks before calling me:
Is it plugged in? No? OK, plug it in.
Is it turned on? No? OK, turn it on.
Is it working now? No? OK, now you can call me.
I can promise that if you adopt this protocol, you will find that the aggregate number of phone calls you get from your shop will be dramatically reduced. Of course, this protocol only applies to tools that are plugged in. For cordless tools, the protocol is a bit different.
Is there a battery in it? No? OK, put a battery in it.
Is the battery charged? No? OK, try a charged battery.
Is it working now? No? OK, now you can call me.
D.D.
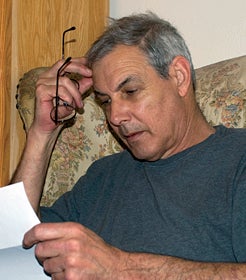
David DeCristoforo possesses an extensive resume as designer/maker of fine furniture, high-end cabinetry and architectural woodwork. His experience in professional woodworking spans a period of 35 years. For the past 20 years David DeCristoforo Design has been located in Woodland, California. During this time David's shop has ranged in scope from a "full on" cabinet production shop with as many as 15 employees to a small fine furniture and custom millwork shop, working with his son, David RBJ, a highly skilled maker in his own right.