Leftovers
Big woodworking projects have one thing in common with Thanksgiving dinners. There always seem to be leftovers. Sometimes, it’s just a few pieces of wood that might be just a…
Big woodworking projects have one thing in common with Thanksgiving dinners. There always seem to be leftovers.
Sometimes, it's just a few pieces of wood that might be just a bit too big to throw in the scrap bin. Or maybe they have some interesting figure that you think you can "do something with." Other times, you end up with extra doors, drawers, pullout shelves, or even entire cabinets. These may be the result of fabrication errors, things that just did not meet your quality standards or changes in the overall plan that were not made until after you had completed that part of the job. And then there are the "leftover" moldings, two or three sticks of something you made specifically for that project that you will probably never make again. Not enough to really do another project with but too much to toss out. These usually get bundled up with the thought that "one day" you might use them.
All of these leftovers get pushed into corners or piled (neatly or otherwise) on shelves or racks until, one day you realize that you are using a lot of your shop to store things that you "might use some day" but somehow, never do. At that point, you have to decide what to do with all the stuff.
There are various ways to deal with this problem. The most obvious is to simply haul it all to the dump (or the recycling center). But that seems counterproductive since you already decided that, for one reason or another, the stuff was worth keeping. My shop is in an area where things left outside have a tendency to vanish. So often, I will leave things like odd sized cabinet doors, stacks of small pieces of wood and the like outside in the hope that whoever is doing the scavenging will take a liking to whatever I have left unguarded and take it away in the night.
Every now and then, my son and I will round up all of the odds and ends of mismatched pieces and parts and try to figure out what we could make out of them. We have actually come up with some interesting pieces by cobbling together various doors and moldings and cabinet parts. My son made a china cabinet using two matched walnut panels that had huge knots right in the center making them unsuitable for use on the job we had bought the walnut for. I have a router table that is made up of three walnut Mission-style cabinets with mahogany interiors that got sidelined by a last minute change in the island layout on that particular job. The top is made from an inch and a half thick hunk of maple "butcher block" counter top left over from another project.
Last week, I made a new bedside table using pieces and parts leftover from at least four separate projects. I worried a bit that my wife might think it was too big. The top was the lynchpin of the design, being a slab of bubinga that I did not want to cut down. The frame was made from some pieces of 8/4 walnut left over from a set of entry doors we made a few years back and, instead of drawers, I use up three really nice walnut pullout trays that had to be remade because the client wanted to make one of his closet cabinets bigger. It actually turned out rather nicely and my wife didn't think it was too big at all.
D.D.
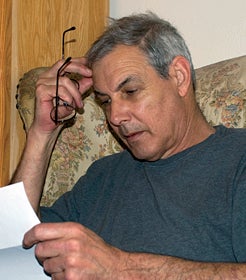
David DeCristoforo possesses an extensive resume as designer/maker of fine furniture, high-end cabinetry and architectural woodwork. His experience in professional woodworking spans a period of 35 years. For the past 20 years David DeCristoforo Design has been located in Woodland, California. During this time David's shop has ranged in scope from a "full on" cabinet production shop with as many as 15 employees to a small fine furniture and custom millwork shop, working with his son, David RBJ, a highly skilled maker in his own right.