Go with the flow and organize your shop
One of the best things about woodshops is that no two are alike. And one of the worst things about woodshops is that no two are alike. It’s a lot…
One of the best things about woodshops is that no two are alike. And one of the worst things about woodshops is that no two are alike.
It’s a lot of fun to wander through several shops and see the huge variety of things we make — furniture, cabinets, turnings, carvings, moldings, millwork and so on. But trying to come up with a set of guidelines for managing shops that share one thing (wood) in so many different ways can be a real challenge. Most businesses like grocery stores or restaurants or car lots have a certain flow and logic to them. Our world is a mix of one-man shops and large production facilities, artists and artisans, sheet goods and natural edges.
But one thing we all have in common is that things flow through our shops. Managing that flow can be either chaotic or controlled. And how well it is managed is often the key to how well a business is doing. If the shop is organized well, then the odds are that marketing, production and sales are all in tune, too.
The logical way to organize is to divide the flow of materials and product into three zones: raw, in process and complete. That sounds remarkably simple, but most shops don’t do it. For example, does your shop have more than one plywood pile? While most of it is in a main rack, are the cutoffs stored across the shop under the stairs and are there several sheets in a back corner somewhere — or perhaps up on a balcony? Moving materials and product efficiently around the shop is inextricably tied to storage.
A place for everything
In the decades before the Civil War, a Yale graduate named Charles Goodrich became a Congregational minister in Worcester, Mass. He also became a widely read author. In 1827, when he was still in his 30s, he published an article on neatness in the Ohio Repository, a Canton newspaper that’s still published today. In that article, Goodrich forever became part of Americana when he adopted the catchphrase “a place for everything and everything in its place.”
Almost two centuries later, that’s still the key to moving stuff around in the shop. By first organizing storage, things tend to get moved just twice — when they’re added to inventory and when they’re used.
Big shops generally have the space to store things efficiently. One- and two-man shops are almost always cramped for space, so while storage is more challenging it’s also more important. With no spare square feet, moveable storage is an often-overlooked option. For example, cutoffs and single boards of rarely used species can be stored in a lumber cart rather than a lumber rack, so it can be moved out of the way when needed, and even moved to a workstation or the table saw when several small pieces are required. The same is true of clamps: storing them on a wall behind each workstation makes sense in a large shop with enough clamps to go around, but storing them on a mobile cart is a lot more logical in a small shop with limited resources.
Having parts (door stiles, drawer sides, etc.) on carts also makes a lot of sense. Instead of stacking them on a stationary workbench and then walking a few feet from there to the machine with each part, it makes a whole lot more sense to move the inventory to the machine.
And having cutoffs, clamps and inventory all on carts also makes it a whole lot easier to create a highway system. It’s not the Eisenhower Interstate Highway System, but a simple system of established walkways through the shop makes life a whole lot easier. Marking these with yellow painted stripes engenders a feeling of sacrosanctity: people are less likely to block the aisles when they see where the aisles are.
Those walkways need to be wide enough for the method being used to move stuff around the shop. In many cases, that’s a pallet jack. Pallets are fairly inexpensive and the jacks are widely available both used and new. Storing everything possible on pallets — from full sheets of plywood to ready-made parts and even completed cabinets — can really help the flow of materials through the shop. One cabinetmaker I knew in South Dakota years ago even went so far as to use a pallet (often with a half sheet of MDF screwed to the top) as his workbench and he would jack it up in the air when assembling cabinets, to save his back a little. Then he’d lower the pallet and leave it right there with the clamped-up assembly drying, while he moved to the next cabinet on the next pallet. There was no downtime clearing the workbench between assemblies and he never needed a second pair of hands to move a large sink-base or pantry.
If a pallet jack isn’t an option and the shop is too small for a forklift, the options are two-wheel carts, freight carts (also called warehouse carts: www.easyrack.org offers several options) and large biceps. Freight carts have been around almost as long as the wheel, but they are perhaps most familiar to modern Americans as the lumber carts at the big-box stores. By adding a platform to a warehouse cart and raising the bed to perhaps two feet off the floor, they make excellent parts carts for woodworking tasks.
Lifting right
Learning how to lift properly by using the legs rather than the back is something that should be reviewed every now and then with employees. Too many back injuries happen because a shop manager didn’t take 15 minutes a year to go over this basic technique.
Here are some lifting tips:
• Wear gloves if splinters, nails, metal straps or sharp edges are involved and steel-toed boots if frequent lifting is part of your job description.
• Suck in your gut: doing so actually adds some support to the lower back.
• Make sure the weight is distributed evenly and, if not, be aware of where it is heaviest and lightest so you’re not surprised.
• Can the object be tilted or carried sideways in a safer manner?
• Remove any obstacles from the intended path before you pick up something heavy.
• Get solid footing and sweep the floor first if there’s a chance it could be slippery (as in sawdust on a hardwood floor).
• When bending down and raising up, use the knees rather than the spine. Your back should be as vertical as possible and your body should be centered over your boots.
• Avoid twisting your spine while toting heavy objects. Move your entire body (including feet) to the right or left and not just your torso.
• Don’t be a hero: ask for help if the job is too big for one spine.
• Get a good grip.
• Shoulder straps, such as those used by appliance movers, are quite inexpensive and they transfer the weight to the strongest part of your body.
• Don’t be lazy and reach over your head: go get the ladder.
Other methods
Two-wheeled handcarts are great for moving vertical stuff around the shop, but not so great for items with a wide footprint such as base cabinets. There is an unusual option that woodshops can borrow from mechanics: the engine hoist. They’re remarkably inexpensive and can handle very heavy loads. For example, The Home Depot offers a 2-ton foldable engine hoist for about $400. It could conceivably be used to move a strapped pallet of hardwoods or plywood.
If the space is available, it really helps to have a staging area close to the main freight door in the shop. As materials come in and completed pieces leave, it’s very handy to have enough room to be able to move them past each other, especially when the same door is used for both. Erecting walls, even clear plastic ones, around this staging area obviates a number of minor problems. By separating the shop from the great outdoors, there are fewer air exchanges during expensive heating and cooling seasons. That thermal trap also cuts down on changes in humidity that are introduced when moving stuff in and out of the shop and it reduces the number of cottonwood seeds and other contaminants that migrate to the finishing room.
One final note: if you’re a one-man (or woman) shop, stop by the library on the way home and check out “Working Alone” by John Carroll (Taunton Press, 1999). It’s written for carpenters, but there’s a whole lot in there about lifting large and/or cumbersome items without straining your back — or your patience.
This article originally appeared in the November 2012 issue.
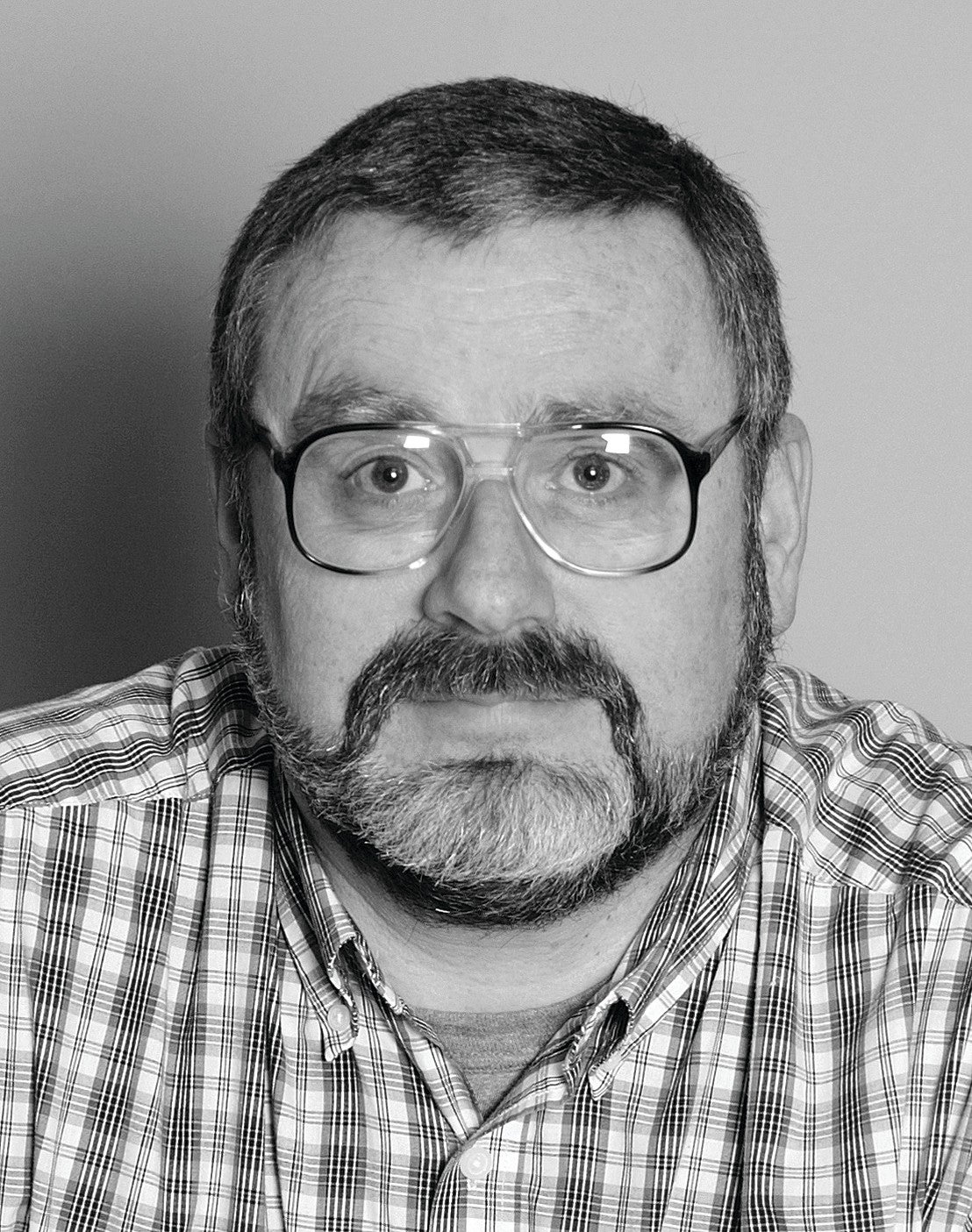