Edgebanding enters a new era
Commercial edgebanding is the application of plastic, wood or resinous materials to the edges of doors or panels. The process uses a heat source, pressure (usually rollers) and a hot…
Commercial edgebanding is the application of plastic, wood or resinous materials to the edges of doors or panels. The process uses a heat source, pressure (usually rollers) and a hot melt adhesive. Edgebanding gives a woodshop the option of using a very flat, manmade substrate (such as plywood or MDF) to create doors that are more uniform and stable than natural wood. It eliminates the need for stile and rail frames on door panels, thus reducing manufacturing time and, of course, cost. Non-wood edgebanding doesn’t usually require any topcoat and some natural bandings (that is, wood veneers) come already finished.
The machines that have been developed to apply edgebanding can usually trim the edges and ends flush and then break the edges with a gentle buffing to avoid sharp corners. Edgebanding is an excellent choice for institutional casework such as hospitals and clinics where a hermetical/non-porous seal is required to meet health regulations and also for schools and offices where plastics can withstand hard use better than natural wood. It is also a viable choice when applying natural wood veneer to the edges of face-veneered panels.
The glue
This can be water-based or solvent-based and is sometimes used in conjunction with a primer that helps the adhesive bond to the substrate. Ethylene vinyl acetate (EVA) glue is soft and flexible, dries clear, has a gloss finish, is durable at low temperatures, doesn’t crack or shatter easily, is essentially waterproof and resists UV radiation, making it a good choice for commercial casework in bright locations. It has a distinctive vinegar odor.
PA (polyamide) hot-melt glues are also found on some banding. These are used extensively in the textile world because they hold up well in laundry cycles, and they are somewhat fire-retardant so they have uses in the electrical field, too. PA adhesives are tough, flexible (a good characteristic for a shop doing bending/curved casework), resistant to heat and will bond to PVC and other plastics. They become brittle at low temperature and soft/pliable at high temperature.
Some adhesive is polyurethane-based and is typically rolled on at pretty high temperatures (about 250 degrees Fahrenheit). Polyurethane glues dry very quickly and cure to full strength over several days. These are very strong glues that can handle relatively high temperatures during the life of the furniture/casework. However, their longer dry time can sometimes be a challenge. Historically, this type of adhesive has been used in the bookbinding industry. It polymerizes when applied: that is, it becomes a compound with high molecular weight and the way in which the molecules are then bonded together lend it extra strength.
Polyolefin glue has high heat stability, adheres to more substrates/materials than most hot melt adhesives at a wider range of temperatures, sprays well, can remain flexible at relatively low temperatures and has one other very valuable trait: the manufacturer can adjust the formula to substantially change the open time (the amount of time one has to work with the adhesive before it begins to set). They can make it cure quickly or slowly.
Amorphous polyolefin glues have a long open time, high heat resistance, are not tacky when they set (making them easier to work with and clean up), offer great strength depending on the substrate and are relatively inexpensive compared to many other hot melt alternatives.
While all of these glues do a great job when properly applied, it’s a good idea to check which one is being used because of their slightly different properties. If there are several suppliers offering a woodshop similar banding, then the type of glue being used might become a factor when it comes to choosing between options.
The tape
Banding can be purchased with or without a glue coating on the back. Some edgebanding machines can apply adhesive and some applications require that the substrate, not the banding, is coated. However, most banding comes pre-glued. Some are peel-and-stick, but the majority is hot melt and requires a heat source. Small quantities can be applied with a household iron or a designated banding iron, but in general, tape is applied using a designated machine.
Options for banding material include plastics (PVC and ABS), natural wood veneers, metals, polyester and melamine. Larger suppliers can provide a woodshop with tape that exactly matches a huge variety of melamine, plastic laminate and thermo-foil colors from manufacturers such as Wilsonart or Formica. Several suppliers also offer custom colors on their PVC, ABS and even wood banding.
The two most common plastics used in banding, ABS (acrylonitrile butadiene styrene) and PVC (polyvinyl chloride), are very similar. ABS can possibly deform in strong, direct sunlight and PVC tends to require a little longer for an adhesive to bond to it, but both are excellent materials for banding. While ABS is more impact-resistant, PVC is more flexible and often more expensive. Both plastics are highly resistant to both household chemicals and water. There are some emerging environmental concerns related to PVC. For example, PVC-coated electric wires have been found to create hydrochloric acid fumes if they catch on fire and some studies also indicate that plasticizers could leak from PVC over time. As a result, the European Union has already banned PVC in some common applications.
What’s new
The German company Doellken-Woodtape, which has a regional office in Brampton, Ontario, launched a new product in 2013 called 3D Edge. It’s made of transparent acrylic that is printed on the reverse side, rather than on the face. This means that any impact or scratch won’t mar the pattern and it also avoids the thin white line (called a picture frame effect) that results when a standard tape has its edges milled or broken.
A large number of manmade edgebanding products (as opposed to natural wood veneers) are certified by GreenGuard. This is a business unit of the Underwriters Laboratories and it helps manufacturers create — and buyers identify — interior products and materials that have low chemical emissions. The goal is to improve the quality of the indoor air in which the products are used. UL acquired GreenGuard in 2011.
Finding the right match for a plastic laminate is relatively easy. Most of the larger suppliers offer online tools to help a shop do this. For example, Charter Industries (www.charterindustries.com) in Grand Rapids, Mich., has a three-step interactive menu where a woodshop buyer can choose between veneer and PVC, click on a manufacturer such as Nevamar or LaminArt, and then enter the color or laminate number to find a match.
Rehau (www.rehau.com) was founded in 1948 in Bavaria, Germany, and today is one of the world’s leading materials suppliers to the furniture industry. In December 2013, the company began production in North America of a line of laser applied, adhesive-free, non-PVC edge banding called LaserEdge. The product is applied with highly efficient laser, plasma or hot-air edgebanding equipment that melts a color-matched functional layer on the reverse side of the edgeband and welds it to the carrier board. The resulting seam-free board offers increased aesthetic appeal with no joints to stain or discolor, as well as superior heat- and moisture-resistance and an overall more efficient manufacturing process when compared to EVA glue, according to the company.
Following the European lead, the U.S. edgebanding industry will experience some major technical and environmental changes in the next few years. Lasers are being used more often to cut edges and to strategically apply heat. And governments around the world are taking a new look at gases emitted by indoor, plastics-based panel and edge treatments, the composition of the substrates to which they are applied and the adhesives used to bond them together.
This article originally appeared in the September 2014 issue.
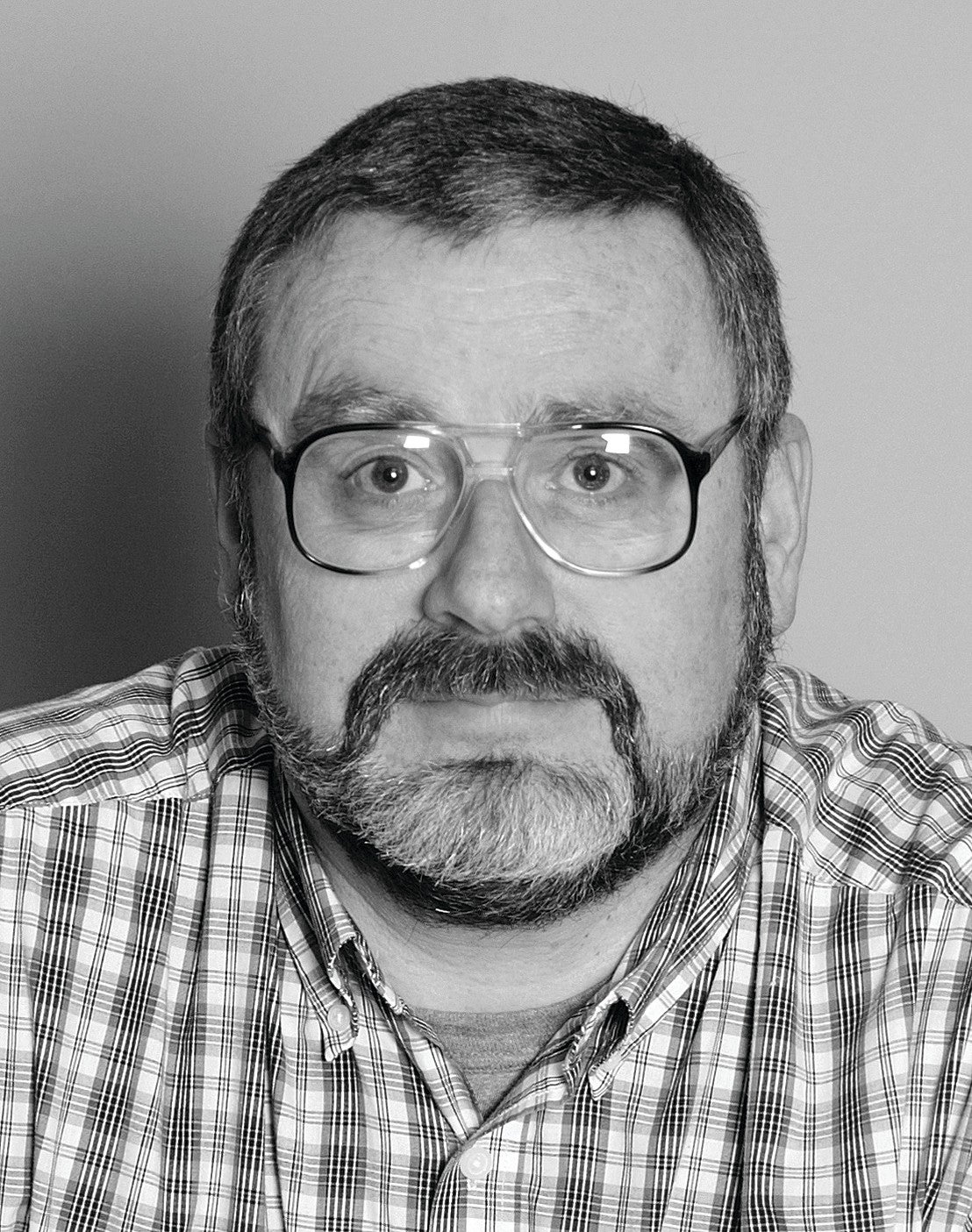