Deal with the moisture to minimize its adverse effects
Seventy-seven-year-old Ken Froelich used to run a furniture repair shop in Rapid City, S.D. It was a half-hour from Ellsworth Air Force Base, where soldiers, airmen and even some diplomatic…
Seventy-seven-year-old Ken Froelich used to run a furniture repair shop in Rapid City, S.D. It was a half-hour from Ellsworth Air Force Base, where soldiers, airmen and even some diplomatic corps personnel would arrive home from overseas tours.
Those who had been residents abroad for some time often had furniture with them. And frequently, those pieces had been built and had spent many years in subtropical climates, especially when the U.S. was more heavily involved in Southeast Asia. When this furniture arrived in western South Dakota — one of the driest places in America — the tables and chairs and cabinets would literally fall apart because the wood had shrunk so much that the joinery failed.
Rod Schaeffer runs semi loads of hardwoods from the Appalachians to places on the other side of the Mississippi River. One of the product groups he ships is large oak timber (8x8 and 12x12) for use as shoring in the mines and oilfields out West. On the 2,000-mile trip, the wood, which is harvested green, is strapped to flatbeds with no tarps. By the time it arrives, the gross vehicle weight can be as much as 40 percent less than it was when the product was loaded in Pennsylvania. Depending on the weather and time of year, the air-drying process induced by travel can remove almost as much water as there is wood in terms of weight.
Things have changed a bit since Froelich was reassembling the furniture of Korean, Vietnamese and Malaysian woodworkers. Most of the furniture nowadays is mass-produced from kiln-dried stock and uses aliphatic resin glues rather than traditional versions of hide adhesives or friction-fitted joinery. But one thing hasn’t changed: wood still moves with moisture and woodworkers need to accommodate that. This is especially true if a furniture builder is buying local lumber or harvesting stock from downed trees. And it’s a concern for shops building cabinet doors with floating panels, or using wide hardwood boards in counters, seats or even shelving.
Moisture is a bigger issue in solid hardwoods than it is in MDF or plywood panels or substrates. Fiberboard contains moisture-resistant resins and the wood particles are so fine that they don’t have the same constitution or behaviors as wooden boards. Plywood is laid up in alternating, cross-bonded layers, which take advantage of one of nature’s quirks: wood moves dramatically across its width, but almost imperceptibly along its length. As the grain in each layer of plywood alternates 90 degrees in direction to the layer above and below it — and the laminations are thin to begin with — the various movements tend to counteract each other. Both types of sheet stock are manufactured from materials that have been dried mechanically and, while there is marginal movement in any wood product, it is relatively restricted in these. They still move, but not much.
All solid wood contains some moisture. People new to the field are amazed at the high levels of water in wood. A freshly cut oak board in the Midwest, measuring just 1” x 6” x 8’, will have about a gallon of water in it. Oak is about 65 to 70 percent moisture content when felled. A thousand board feet of green oak weighs roughly two-and-a-half tons and the same load dried to 6 percent is about one-and-a-half tons.
Basic rules
The first guideline is that bowl turners and landscapers like to use green wood, but almost nobody else should. Green wood is lumber that has been felled and milled (cut down and made into boards), but has not yet been thoroughly dried. A good rule of thumb for hardwoods is that they should be in the 6 to 8 percent range before they are made into casework or furniture. That means the amount of water in the board needs to be reduced to the point where it physically weighs about 7 percent of what the wood weighs. (In some species, the water in freshly harvested logs can weigh more than the wood, so the moisture level is actually more than 100 percent.) The wetter the boards are, the more they move when they dry. And the more they move, the more they twist, cup, warp, bend and crack, too.
The next rule is that shop owners buying hardwoods from a local mill need to have a handle on the drying process. Too wet and too dry are both problems, as is the rate at which moisture is asked to evacuate. Wood generally won’t be too dry for long, because as a fibrous, cell-based product it will eventually absorb some moisture from the air around it (a process called gaining equilibrium). Bringing stock into the shop and allowing it to acclimate for a few weeks before milling is a good idea. It will move (in width) to a point where it is comfortable and thus better behaved.
While it’s hard to get it too dry, wood can most certainly be too wet. And just to confuse us, there are actually two kinds of moisture in a freshly milled green board. Free water sits in the voids of the cells and bound water sits in the actual walls of those cells. Free water will evaporate quite rapidly after sawing and this will bring most species close to the level desired in framing softwoods (a little under 20 percent moisture). But that bound water is a little trickier: in the majority of commercial species, it takes about a year per inch of thickness to evaporate under cover (such as a tarp or a shed). The traditional air-drying process requires that the boards are stickered (small spacers at regular intervals), that the ends are sealed with paint or PEG (Polyethylene Glycol) to avoid checking and that there is fairly even airflow and good venting around the stack to carry the moisture away.
Commercial kiln drying (and there are dozens of different types of kilns) reduces the process to a matter of weeks. The actual time depends on the species, the thickness of the boards, their width, the fuel being used (solar, gas, electric etc.) and other attributes such as how much air-drying occurred before the wood was placed in the kiln, where in the country the kiln is located and even the altitude and aspect of the kiln (which way it faces in terms of sunshine and winds). Higher altitudes tend to be drier.
Many kiln operators say that their speedy process (faster than air drying) affects and even locks in the color of the wood. But too speedy a drying process can also cause major problems. If the kiln operator doesn’t really understand what he/she is doing, the result can be checks, splits, warps — and an evil outcome known as case hardening. This is when the outside faces of the boards are dried quickly and shrink and then the moisture in the center of the board heats up and expands. It’s like a fat guy in Spandex. Something’s gotta give.
Shop guidelines
Woodshop owners can do a lot to minimize the adverse affects of moisture. Boards stored flat will behave better than boards standing against a wall at an angle. The residue of moisture in the cells allows wood to be a little flexible and over time boards that are only supported at the ends (such as those leaning against a wall) will begin to bow in the middle as the cells closest to the wall expand slightly in length.
When storing boards flat, the base needs to be flat. If a stack of hardwoods is resting on three skids and one of the three is a quarter of an inch thinner or thicker than the others, the whole stack will eventually bow as a result of gravity.
It’s a good idea to monitor the humidity in the shop, especially in locations with large seasonal swings. The 6 percent to 8 percent moisture content in a board is measured as absolute humidity, which is just the amount of water vapor in the air expressed as a percentage of the amount of dry air. Relative humidity, on the other hand, can be confusing. It measures the current absolute humidity as a percentage of the highest possible absolute humidity. In other words, how much moisture is in the air now compared to how much moisture the air could possibly hold at its wettest. People like the air to be around 50 percent relative humidity. The hotter the air in the shop is, the more moisture it can hold. If the relative humidity is 100 percent, then the air can’t hold any more moisture and, outdoors, this triggers rain. If the air is cool, say 50 degrees Fahrenheit, it takes less moisture to get to 100 percent humidity than if the air is 90 degrees.
The bottom line here is that we should try to keep the shop air somewhere in the middle. In summer, dehumidifiers or air conditioners work well in regions of high humidity and swamp coolers work in drier parts of the country. In winter, adding a humidity pump to a furnace not only helps the hardwoods, it could also make workers less lethargic and more productive. Generally, what’s good for people is good for wood when it comes to dealing with moisture. If your skin is dry in December and you’re getting static shocks around the shop, the forced air furnace might be removing too much moisture. And if your shirt is soggy in August, the hardwoods in the shop are probably feeling the humidity as much as you are.
This article originally appeared in the February 2015 issue.
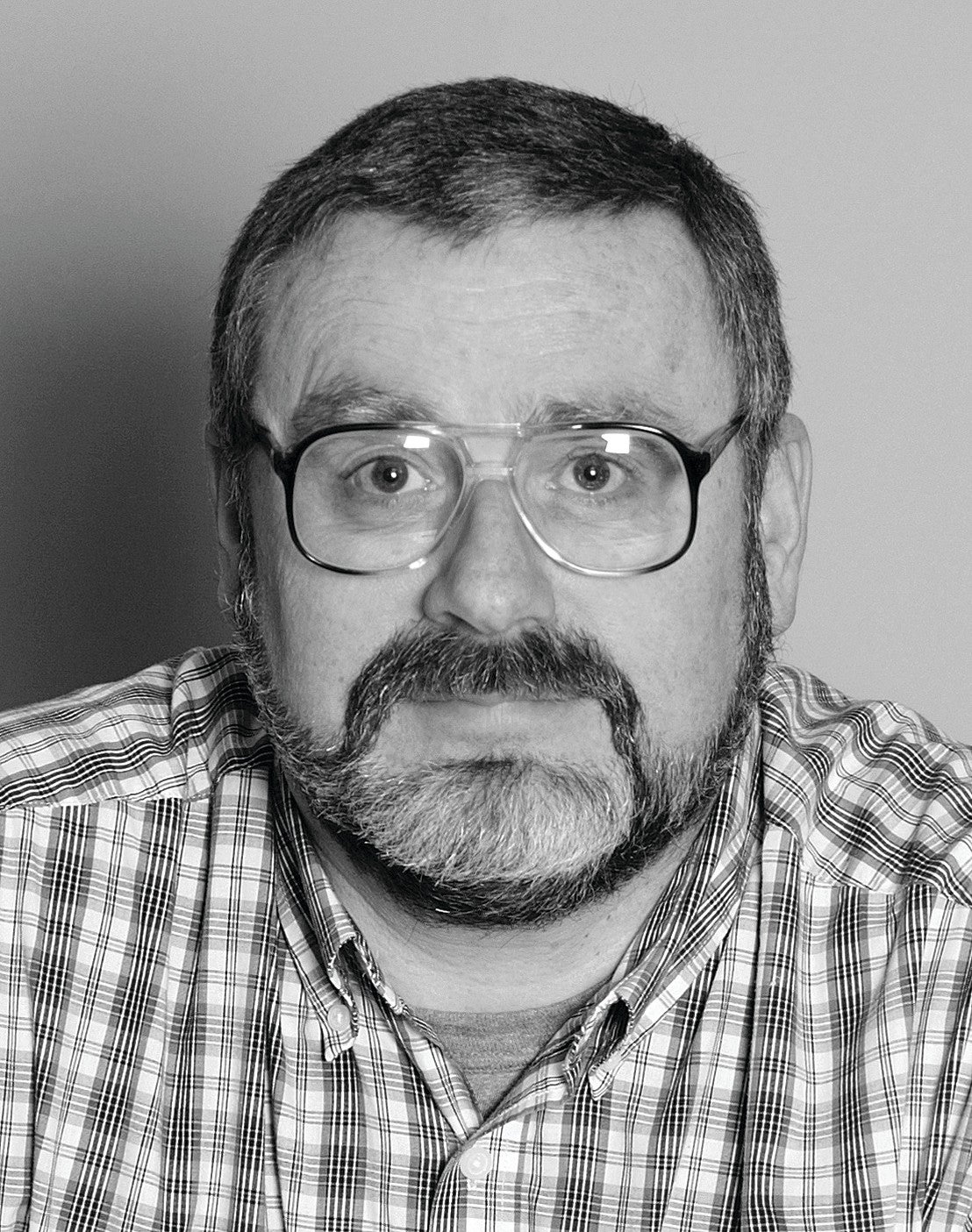