You just cant live without bits, blades and cutters
Clifton, N.J., is known for being the childhood home of David Chase, the creator of “The Sopranos.” It’s also home to Forrest Mfg. (www.forrestblades.com), which has been a mainstay of…
Clifton, N.J., is known for being the childhood home of David Chase, the creator of “The Sopranos.” It’s also home to Forrest Mfg. (www.forrestblades.com), which has been a mainstay of the woodworking industry for more than half a century.
The only other thing that Forrest has in common with “The Sopranos” is that they both know the rigors and rewards of a family-owned businesses. The company’s newest offering is an 8” diameter thin kerf dado set that was designed for clean-cutting 3/16” wide grooves. These are primarily used in applications such as backer-boards or drawer bottoms. The set is comprised of two 24-tooth outside saw blades and also comes with shims for making minor adjustments. (These might be needed when dealing with plywood thickness anomalies.) The company also offers the product in a three-component option that includes a 1/16”, four-tooth chipper so it can plow exceptionally clean 3/16” to 1/4” wide grooves.
An hour’s drive east of Clifton on Long Island, lies the village of Farmington. Here, good carpentry is a longstanding tradition. The first European to settle the land (in 1687) was a rum dealer and later town constable named Thomas Powell. He built a house on what would eventually be known as the Hempstead Turnpike and the structure survived for more than two centuries until 1931. Powell built a second, very similar home on Merritt’s Road about a decade after the first one and that building is still standing proud.
Today, Farmingdale is home to the corporate headquarters of Amana Tool (www.amanatool.com), a company that produces solid-carbide and carbide-tipped cutting tools for the woodworking industry. Founded some 285 years after Powell staked his claim, Amana continues his tradition of excellent construction by producing industrial-quality saw blades, router bits, shaping cutters and boring bits. Among the more recent offerings from Amana is the AMS-139, which is an 18-piece general-purpose CNC router bit collection with 1/2” shanks. Along with wood, the set is designed to mill non-ferrous metals, foams, melamine, MDF, plastic laminates, acrylics, veneers, plywood and other products used in woodshops and sign making.
Also new from Amana is the RC-2247, a planing and rabbeting bit designed specifically for woodshop applications. With its 1-1/4” diameter, this bit is ideally suited to get into tight corners. The design contains two cutting flutes and two up-shear scorers and these four inserts combine to provide a smoother finish at the bottom of the cut than traditional two-knife router bits. The depth of cut is 27/64” and the bit comes with a 1/2” shank. Such an evolution in technology makes one wonder how old Tom Powell got everything done with hand tools and how much an industrious Yankee could have achieved with access to a CNC machine.
Three hours northwest of Long Island, in a sleepy little hamlet in Sullivan County that’s a stone’s throw from the Pennsylvania line, there’s a collection of buildings at the end of a tree-lined, winding side road. Located just outside Barryville, N.Y., on the aptly-named Sawmill Road, the world headquarters of Esta-USA Inc. has been enjoying rural solitude at its finest for more than 30 years. The company (http://estausa.com) is the sole factory-direct source for Dispoz-A-Blade throughout North, Central and South America. The staff has only one goal: to provide woodshops with a planer and jointer knife that anyone can change accurately, quickly and economically. The system replaces original factory-issue products with double-edged disposable knives.
How it works is simplicity itself. The knives slip in place and set themselves. Self-Set knives (available in all lengths up to 36”) install in the machine’s ordinary stock cutterhead. They require no machine modifications or the use of jackscrews, springs, setting gauges, jigs or measuring tools. No special skills are needed to quickly change knives with precision every time.
A Midwestern mindset
Not every old-fashioned craftsman lives in New York. In the woods of northern Wisconsin, surrounded by sawmills and veneer factories, two brothers continue a long family tradition of producing high-quality cutting tools for the woodworking market. Back in 1992, Ron and Mike Serwa got together and created the Vortex Tool Co. In the ensuing decades, the company has become one of the most diversified sources of quality cutting tools in the industry. A lot of its business involves custom tooling and the innovative nature of that process often spills into its standard product line. The Vortex engineering team constantly comes up with really interesting new ideas, which eventually appear in the company’s downloadable catalog (found at www.vortextool.com).
One of their most recent projects is a line of XP (Xtreme Performance) cutting tools. After extensive in-house testing and a survey of woodworking customers, Vortex has ascertained that XP series tooling delivers three to five times more tool life than standard tool geometry. Originally designed for cutting high-pressure laminates and melamine, users have found that they also deliver excellent results in particleboard and MDF. They are available in two and three flute compression style geometries, as well as down-cut spirals.
Vortex’s team has been so impressed with their performance that several XP products are now included in one of the company’s startup packages for new CNC router owners. The No. 5000 Kit is a 26-piece collection of cutters complete with accessories that are designed to get new users off to a running start.
Any woodshop manager thinking of building dovetailed boxes in-house — or wanting to change the way they’re currently being done — might enjoy taking a look at Vortex’s flat table dovetail drawer system (Kits Nos. 7500 and 7600). Engineered around a couple of innovative insert profiles, the system allows users to quickly and easily make dovetail drawer components with a nested base format. A single shaft can be used to mount either one of two different insert profiles, delivering a traditional sharp-cornered tail or an elegantly round-cornered one.
There is no word in English that rhymes with orange and that uniqueness is a fitting way to describe Greensboro, N.C., manufacturer CMT Orange Tools (www.cmtutensili.com). Actually, the U.S. location is a branch of a Pesaro, Italy-based parent company that has been delivering fine European engineering to woodshops since 1962. Because of an intense investment in advanced technology (the company’s entire production facility is now completely automated), CMT is able to offer prime industrial tooling in the U.S. at an affordable price.
In January, CMT introduced several new cutting tools. Its laser-point router bits are designed to make fine incisions so precise and delicate that they look as though a laser cut them. A new pattern/flush-trim router bit with insert knives comes with both top and bottom bearing guides. There are new solid carbide up- and down-cut spiral bits, new V-grooving bits for Alucobond and even new router bits built specifically for Festool’s Domino joiners.
Another manufacturer that is heavily invested in state-of-the-art technology is Charles Schmidt & Co. Inc. (www.cggschmidt.com). Its new HSK corrugated cutterheads are constructed from alloy steel with a hardened and ground HSK locking device. Rated for 12,000 rpm, they will run on any HSK machine and are made for 1/4”, 5/16” and 3/8” thick knives. The two-knife heads are available with a 12- or 20-degree cutting angle, and custom lengths, cutting angles and HSK arbors are available. They are also certified by Weinig USA to run on its molders.
Since the 1970s, Freeborn Tool Co. (www.freeborntool.com) in Spokane, Wash., has been a leading manufacturer of tooling for the woodworking industry. Now the engineers at Freeborn have come up with a new three-piece cope and pattern insert set that is designed to avoid any loose tongue and groove issues due to spindle misalignment. This set allows a woodworker to adjust the cope side as needed to compensate for any loose fit.
Service and silence
When those knives get dull and you didn’t go disposable, it might be time to get hold of Jim or Dan Povinelli. The father-son team leads what is widely regarded as the Northeast’s premier tool-sharpening service. Connecticut Saw & Tool (www.ctsaw.com) has been owned and operated now by four generations of the same family. They and their team of 18 employees precisely grind profile knives for all shapers and molders and ship them nationwide. It carries a large inventory of bits, blades and cutters from manufacturers such as Amana, Freeborn, CNC Tooling, CMT, Freud, Whiteside, Onsrud, W&H, Wisconsin Knife Works and most other leading brands. And Connecticut Saw & Tool provides service or sharpening for every single product it sells.
Lyndhurst, N.J., is home to Ridge Carbide Tool Co. (http://ridgecarbidetool.com), another highly reputable sharpener of blades, bits, cutters and knives. And the team at Ridge Carbide also makes custom tools in a hurry. They build custom router bits, shaper cutters and profile knives so fast that their website claims it’s “practically overnight.” Just mail, email or fax your drawings to the addresses on the website and they can build router bits (large and small), CNC bits, William & Hussey knives, Shop Fox profile knives, corrugated back knives, groovers and slot cutters.
The German manufacturer Leuco Tool Corp. (www.leucotool.com) has four U.S. locations with a regional headquarters in Villa Rica, Ga. The company’s latest innovation is a line of “no-noise” saw blades. The design of both the tooth geometry and tool body provides excellent quality cuts in almost all conventional wood-based panels, as well as solid woods. Leuco Diamax tips offer very long tool life and guarantee two sharpenings. Smaller chip gullets lead to that low sound level — up to 6 dB less noise when idling — which makes it just a little more comfortable to work on the shop floor.
Machines might do the heavy lifting, but bits, blades and cutters make all the difference in the quality of a job. It’s what you put on the arbor that counts. After all, a planer without a knife is just furniture.
As Tony Soprano was fond of saying: “What use is an unloaded gun?”
This article originally appeared in the June 2015 issue.
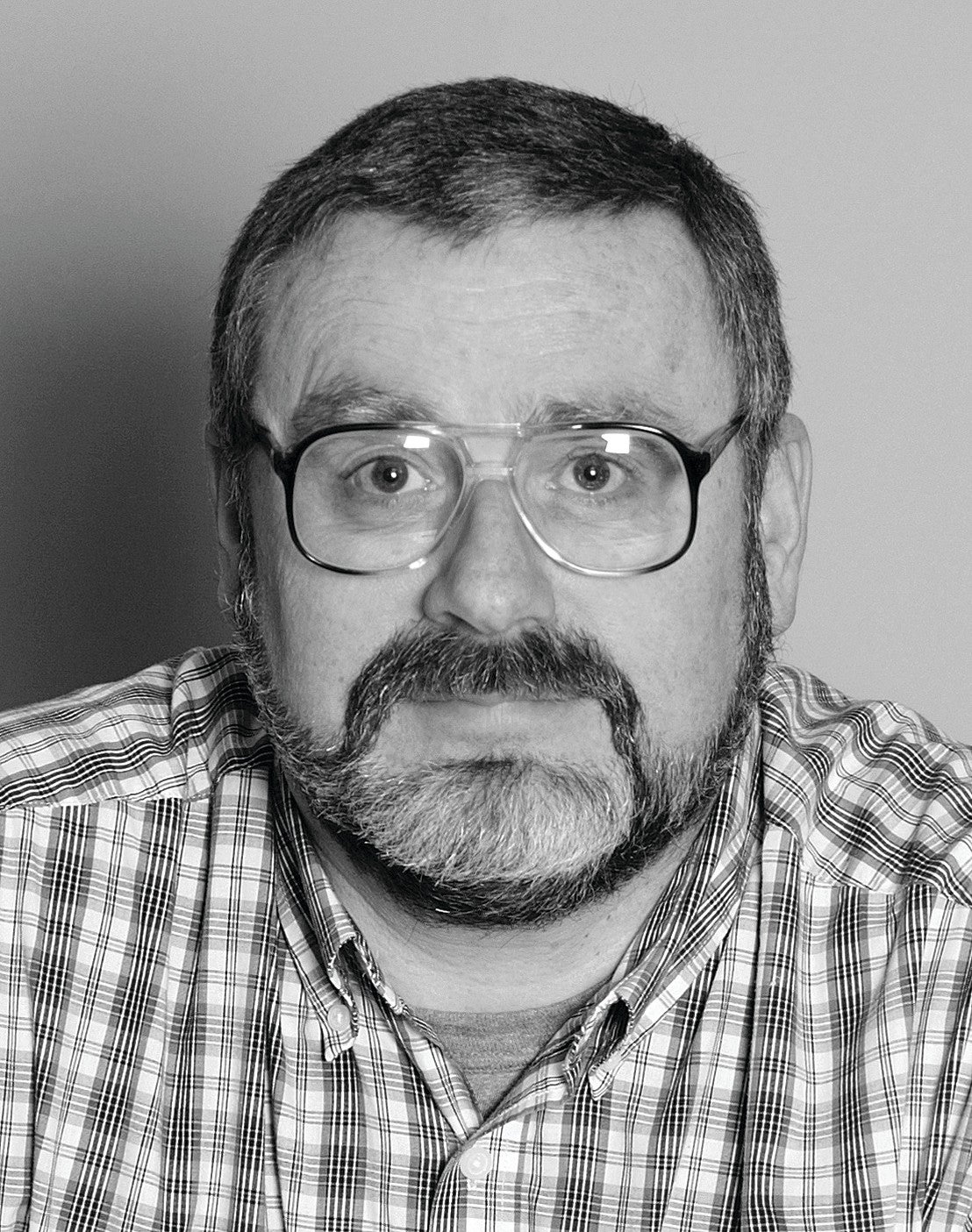