Staying on the straight and narrow
Physicists and fans of the CBS comedy “The Big Bang Theory” are familiar with particle accelerators, those massive machines that propel charged particles to incredible speeds in a confined orbit….
Physicists and fans of the CBS comedy “The Big Bang Theory” are familiar with particle accelerators, those massive machines that propel charged particles to incredible speeds in a confined orbit. While they use electromagnetic fields to make molecules move, woodshops use air pressure to achieve a similar end.
Essentially what happens in the shop is that a large volume of air is compressed into a confined space (a hose or pipe) where the negative pressure at one end exceeds the positive pressure at the other. Woodshop dust is moved by vacuum, rather than pneumatics where the air is first compressed and then moves toward a low-pressure environment. The mechanics involved in a vacuum transfer of pressure are volume and velocity: how much air needs to be moved and at what speed?
Think of a large log sitting in a mountain streambed, where only a trickle of water is flowing. It doesn’t matter how fast that tiny volume of water runs, it will never move the log. Now imagine that there is plenty of water, but it’s a very lazy stream. The log is suspended (floats) in the water, but barely moves. We now have volume without velocity. After a storm, big waters rush through and carry the log away. That’s volume and velocity.
The first key here is suspension. Nothing happens until the flow is large enough to lift the log. So there needs to be enough air in a dust-collection system to pick up and carry shavings, chips and all sizes of dust particles and suspend them in the air flow. Suspension is achieved by creating the correct balance between the volume (the size of the pipes or hoses) and the velocity (speed) of the air. The latter is determined by the strength of the fan less resistance.
If our mountain stream flows down a steep grade in a straight line, it will flow fast. However, if it has to navigate through a canyon with innumerable twists, navigate Class 5 rapids and deal with beaver dams, the speed will be both reduced and uneven. At times, it will accelerate and at others it will create almost still ponds behind obstacles like those dams.
The more twists, hard corners, ribbed flexible hose and other obstacles that we throw in the way of a woodshop’s dust collection system, the more we disturb the flow. The optimum option is to perfectly size individual collectors to each machine and connect them with a single length of straight pipe. As that’s almost physically impossible, woodshops have through the years resorted to attrition rather than finesse. We simply increase the size of the system until it overcomes the obstacles. We use bigger pipes and bigger fans to compensate for sharp bends and poor planning. That costs us money in both electric bills and floor space. A little fine-tuning can save some dollars, but also deliver much better dust control.
The primary options for improving performance are to upgrade the filter bags, change ribbed hoses to smooth pipes, reduce the number and severity of direction changes, size the ductwork correctly and the big one — control vacuum loss.
Bigger and better bags
Upgrading filter bags can play a huge role in improving any system where the air in the shop runs through a dust collector to be “scrubbed” and is then returned to the shop. American Fabric Filter, located in Wesley Chapel, Fla., has spent the last couple of decades designing and fabricating custom bags and sleeves for everything from home hobbyist collectors to 100-plus-hp factory bag house systems. The company maintains that “a small collector’s performance can improve dramatically with increased filter area.” The idea here is that a larger bag on a small shop’s single or two-stage collector will allow more “clean” air to escape back into the shop, so the net effect here is usually a considerable increase in the number of cubic feet of air being processed.
Commercial shops might require a little more effort and investment. To operate more efficiently, large bag systems usually need larger filters with thicker fabrics, and sometimes American Fabric Filter even adds extra (sister) bags to get the proper air flow without creating more back pressure.
One way to describe back pressure is that more air is coming in than can escape. As this pressure builds up, the velocity of the air flow reaches its peak farther and farther away from the filter bags. If the air is slowing down before it reaches the bags, it will begin to drop its cargo.
Bill Pentz, an expert in this field (online at billpentz.com), has ascertained that it takes 4,000 cubic feet per minute (FPM) to keep dust and chips in suspension (that is, floating rather than settling). That speed requirement is so high because most systems include at least some stretches of vertical pipe where the effort to lift the debris involves more than air flow: the collector is also combatting gravity. If your filter bags are too small, your system can’t generate enough speed. If the inside surface of the bag(s) is clogging too fast, the system will slow down. And if the bags are undersized, they clog faster. It’s a vicious cycle.
Depending on the material you’re processing (mainly MDF or perhaps hardwoods?), you might also need to look at the weave — that is, the size of the holes in the filter bags. Small holes collect finer particles, but clog faster. Fine powder builds up on the inside of the bag and works in two ways: it partially clogs the holes and thereby reduces air flow, but it can also intentionally reduce the size of the holes and still allow air to flow. It’s a delicate balance, but well worth a conversation with a bag designer. The smaller the particles you can efficiently trap the better, as these are the most dangerous for workers to breathe. But if the system is too tight, the air flow is reduced at every machine and a lot of those tiny particles will remain suspended in the shop’s ambient air.
There is no magic micron number here. The bag filter rating depends on the size of the fan, the diameter of the ducts, the weave of the bag and the materials being processed. Every shop pretty much requires a custom evaluation.
The hose hindrance
Yes, there are a few very well-engineered flexible hoses on the market that cause almost no resistance when properly installed. They’re expensive and generally share one characteristic: the inside of the tube is relatively smooth.
Remember those river rapids? Well, cheap corrugated hoses have much the same effect on air flow as rocks do in water. They cause turbulence. At the edge of the flow, each rib catches a little of the air and turns it back on itself. Over a long stretch, there’s a cumulative effect that can slow down velocity and thus volume.
And it’s not just the ribs. Every curve in a flexible hose is another obstacle to air flow. A much better option is to use metal pipe or grounded plastic pipe.
If the ductwork has to change direction, then the turn needs to be made in a slow, graceful curve rather than a sharp turn. Asking air to dramatically change direction causes a backwash. There aren’t too many naturally occurring 90-degree bends in rivers and air behaves in much the same way water does. It’s a good idea to physically walk the dust collection lines in the shop, just to see if there’s anywhere a transition can be improved by evening out a sharp curve.
Is your ductwork sized correctly? Yes, it gets smaller the farther it is from the bag, but are the diameters a matter of convenience (that’s the stock pipe size that was available) or intentional design? Once all the machines are in place and their dust port sizes are known, it might make sense to measure the lengths of the runs, check the CFM rating on the collector and then give a professional designer a call. Odds are that, in most shops, some stretches of ductwork are either too wide or too narrow.
Control vacuum loss
Attrition can be described as throwing more and more resources at a problem until the sheer volume of the solution overcomes the challenge. Yes, you can upgrade the bags and tweak the ductwork and maybe even invest in a bigger, better collector. But the largest potential efficiency could be a lot simpler: just shut the gate.
Blast gates are a pain. There’s no getting around that and woodworkers have a long history of just leaving them all open because the task at hand “will only take a few seconds.” We’re human and the only sensible solution is to completely automate the entire system’s blast gates. That’s not as big a challenge as it sounds: most small shops can get by with a wireless system that costs less than a decent miter saw and can be installed in an hour or two. It’s a solid investment that saves time, money … and lungs.
This article originally appeared in the October 2016 issue.
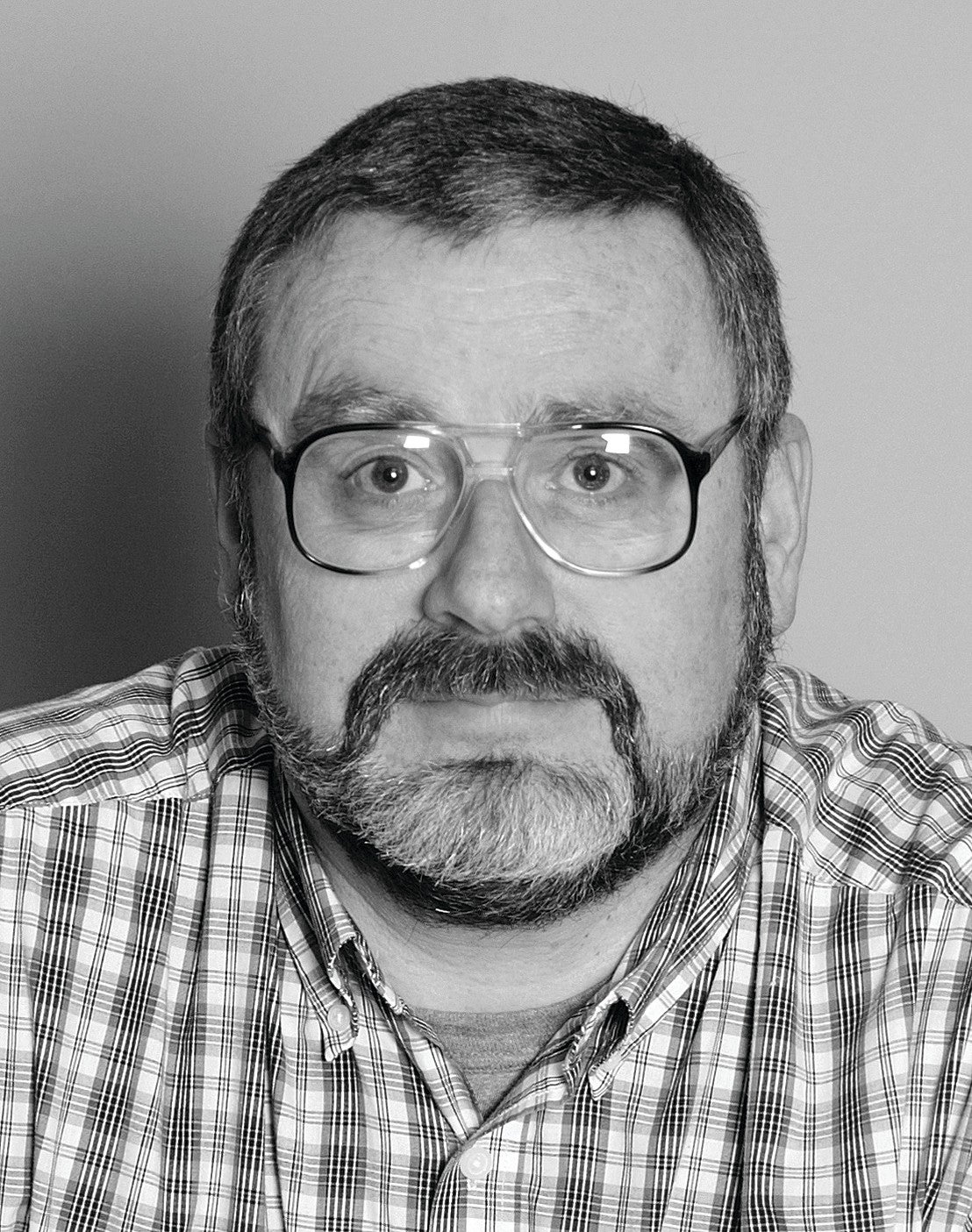