Happy employees, happy boss
Enhancements to the work shop environment, making it safer, easier and more productive, will pay off.
CareerBliss calls itself “an online career community designed to help you find happiness in the workplace and your career.” Granted, such outfits might not hold a lot of sway in the rough and gruff world of woodworking, but the company publishes a list every year of the happiest places to work in America. And cynical, mercenary people such as financial magazine editors and mutual fund managers sit up and take notice when the list is published. That’s because companies with happy employees tend to outperform their markets, and do so quite handily. Satisfied, fulfilled, self-actualized people produce more and better work.
You can see the latest list of happy workplaces at Careerbliss.com. And the first thing you’ll notice is that there isn’t a single woodshop on the list. That’s because most of them are giant multinational corporations or financial pillars of Wall Street. But the underlying logic applies to businesses of all sizes. Keep your employees happy and your bottom line will be healthier. People who feel like they belong to a team will often put the collective interest above their own and make an extra effort to ensure communal rather than just individual success.
In a woodshop or other hands-on environment, many of the ways that we can improve loyalty, effort and teamwork are grounded in such mundane issues as dust, heat and materials handling – physical comforts that engender a sense of wellbeing. When people feel an employer is taking care of them, they usually reciprocate in kind.
And the reverse is also true.
Dust and other hazards
Sometimes it’s a bit of a shock for employers to find out that their workshop environment isn’t exactly up to par in their employees’ eyes. This fall, the Occupational Safety and Health Administration responded to a complaint at DuBell Lumber Co. of Medford, N.J., and cited the company for exposing employees to combustible dust and other hazards. As of Oct. 3, 2018, DuBell faced $106,432 in proposed penalties because it “failed to properly control combustible dust resulting from wood processing; train employees on how to control the release of hazardous energy; and use lockout/tag-out procedures and machine guards to protect employees from amputations.”
In Greenville, Ala., OSHA cited Structural Wood Systems Inc. in September for exposing employees to multiple hazards. The company faces $85,362 in proposed penalties because it failed “to ensure employees used protective eyewear and respirators, implement a respiratory protection and permit-required confined space program, and use guards on a motorized roller conveyer table; and for allowing combustible wood dust to accumulate, exposing employees to fire and explosion hazards.”
And in Idaho, OSHA cited Merritt Bros. Lumber Co. in August for exposing employees to multiple workplace safety hazards at its Athol facility. Proposed penalties in the amount of $189,221 were levied because OSHA said that the company failed “to use machine guards on trim saws and conveyors, install handrails on stairways and walkways, use lockout/tag-out procedures to control hazardous energy, and train employees on hazardous chemicals. OSHA also cited the company for allowing sawdust and other combustible materials to accumulate.”
If these examples of OSHA enforcement are making your palms sweat, you’re not alone. When dealing with a giant government agency, it’s hard to know what’s required and what’s acceptable. But there is help and asking for it shouldn’t get a woodshop owner in trouble.
OSHA’s On-Site Consultation Program (at osha.gov) offers “no-cost and confidential occupational safety and health services to small- and medium-sized businesses in all 50 states, the District of Columbia, and several U.S. territories, with priority given to high-hazard worksites. On-Site Consultation services are separate from enforcement and do not result in penalties or citations. Consultants from state agencies or universities work with employers to identify workplace hazards, provide advice for compliance with OSHA standards, and assist in establishing and improving safety and health programs,” according to the site.
Heating and cooling
Not every aspect of creating a better workshop environment will result in Big Brother looking over one’s shoulder. All of those citations above were for health and safety related issues, where employees potentially faced some physical danger. Many woodshops just struggle with maintaining a comfortable atmosphere in the building, whether that’s avoiding chills in Minneapolis or perspiration in Miami. Here, the solution can sometimes be quite simple – curtain walls. Isolating workstations by surrounding them with transparent curtains seems like an unsociable thing to do. But in the average woodshop, most of the work is carried out in a couple of small areas while a furnace or central air conditioner is trying to heat or cool an entire building. A few curtain walls and a little creative ductwork by a HVAC contractor can deliver the perfect temperature and moisture conditions on hardworking skin, and avoid spending large amounts of the shop’s profits on seeking the same exacting conditions in what is essentially warehouse space.
As every woodworker knows, humidity is a critical component in handling wood and wood products. Expansion and contraction, warping, splitting and similar problems are all related to the amount of ambient moisture in the air. But humidity is also a major concern for employees, and adding or subtracting it can change the way that people feel, and work. Forced air furnaces can dry out skin and cause mild dehydration in employees, leaving them feeling a little tired, unfocused and unmotivated. Adding a central humidifier to the ductwork is not a very expensive option and it can often dramatically improve the workshop environment, and the level of effort being made by the people who occupy it. The reverse is true, too. Hot, heavy and damp air in midsummer slows people down more than the temperature alone. A dehumidifier can sometimes do as much good as an air conditioner. It’s not the heat, it’s the humidity.
Oh, my aching back
Materials handling has come a long way over the past few decades, from training employees to lift with their legs (rather than their backs) to installing automatic loading and unloading on a CNC. There are all kinds of devices on the market for handling full sheets of plywood or MDF. Some of them are just a pair of wheels that let an employee move a sheet across the shop, while others are mechanical carts that raise, lower, tilt, load and unload sheet goods without relying on an operator’s spine.
One of the more recent offerings for small shops is the Material Mate from Rockler Woodworking and Hardware (rockler.com). Listed at $250 (item No. 56889), it will smoothly roll sheet stock from a storage rack or the back of a pickup truck to the table saw or the lumber rack, and it can also be used as a mobile workstation. It has a tilting top that lets it pass through standard doors in the vertical position, and then it flips horizontally to slide the sheet onto a machine.
At the other end of the spectrum are the robotic loading and unloading options available in the latest generation of CNC routers. Most come with an automated system that reduces the required personnel to a single operator, and the robots also align the sheet on the bed so the whole operation is hands-free. And best of all, many of these are retroactive. That is, they can be added to an existing CNC router.
Robotics are popping up everywhere in the wood industry, and they’re not just moving things around. Earlier this year, the Massachusetts Institute of Technology created a robotic carpenter called AutoSaw that it says “could make the creation of custom furniture and fittings safer, easier, and cheaper.” The machine will autonomously pick up materials, cut them to shape and stack them for assembly. And in April, a Singapore university revealed a robot that could assemble an Ikea chair. So, while larger shops and outsourcing suppliers are already using robots extensively to handle materials, that technology is beginning to trickle down. A visit to AWFS in Las Vegas this coming summer (awfsfair.org) should be a real eye opener as this technology matures and becomes more affordable and more applicable.
Speaking of material handling, one of the most innovative and clever suppliers in that field is an Irish company called CombiLift (combilift.com), which has offices in North Carolina. The company makes side loading and multi-directional forklifts that can slide sideways down narrow aisles in warehouses, or spin full circles on a dime (all of the wheels can turn independently, as shown in movies on the website). The factory will custom build for any application, and in any of several fuel systems. CombiLift even offers a huge straddle carrier with a mobile gantry for moving and loading things such as large trusses or beams. And the company’s Aisle-Master can operate in aisles as narrow as 62” while reaching vertically up to 50’.
All of these innovations have one thing in common – they enhance the workshop environment and make it safer, easier and more productive for woodworkers to do what they do best.
This article originally appeared in the December 2018 issue.
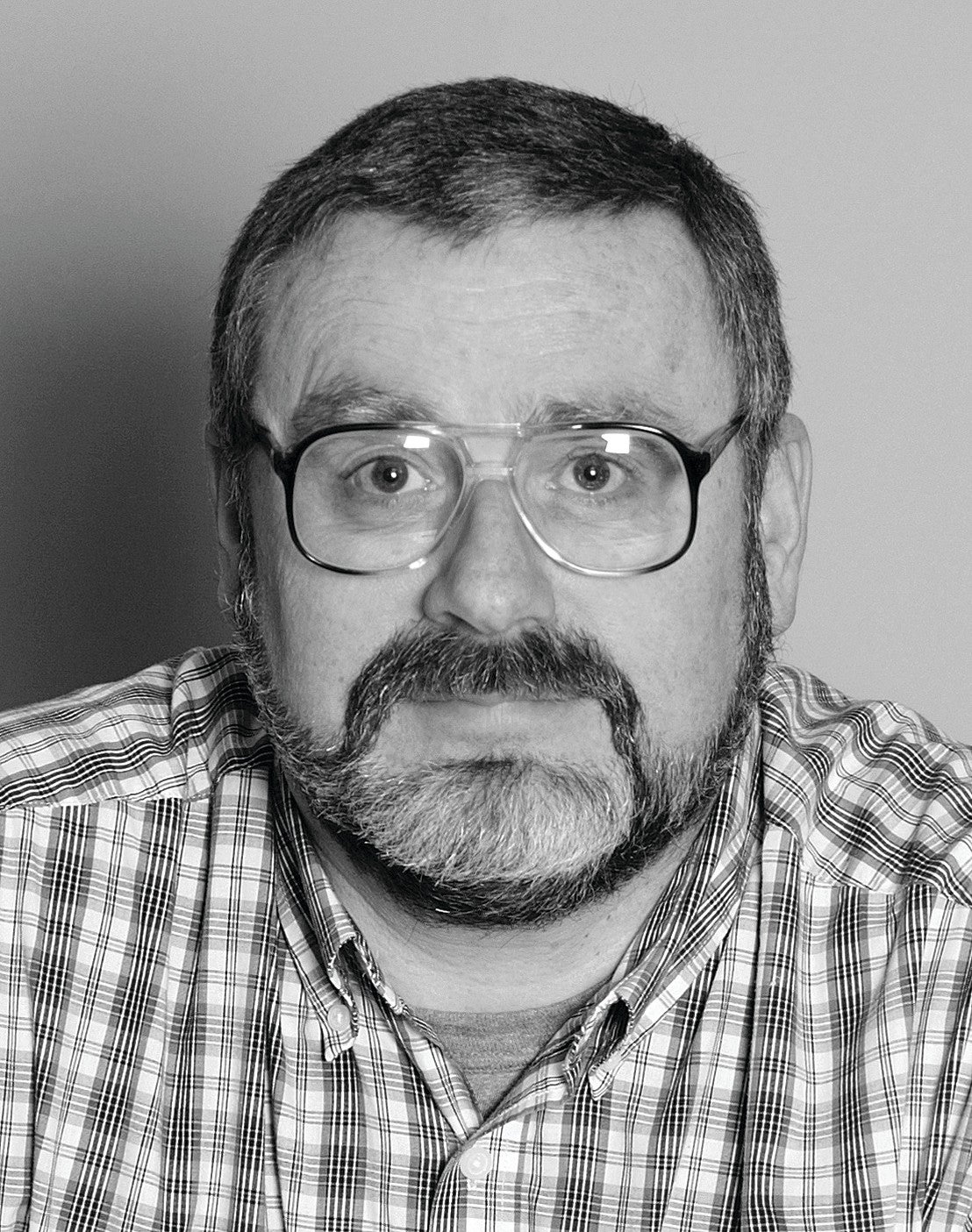