Dont be alarmed, but be ready for shop disasters
On Jan. 3, 40 firefighters responded to a call at a woodshop in Frederick County, Md. The first response unit encountered heavy smoke in the 75’ x 100’ metal building…
On Jan. 3, 40 firefighters responded to a call at a woodshop in Frederick County, Md. The first response unit encountered heavy smoke in the 75’ x 100’ metal building at Celebration Farms in Libertytown. No injuries or deaths were reported and the building was saved. According to Capt. Kevin Fox of the Frederick County Division of Fire/Rescue Services, the cause of the fire was “combustible materials located too close to a wood stove.”
Lots of people chop down trees for firewood because it’s one of the most combustible materials on the planet. For that reason, there aren’t a whole lot of woodshops anymore that heat with wood stoves.
On Jan. 25, 2013, Joe Dunphy Custom Woodworking in Prince Edward Island in Canada wasn’t as lucky as Celebration Farms. Dunphy’s shop burned to the ground. The seven-man, 30-year business builds custom kitchen and bath cabinets.
“That was the worst day of our lives,” co-owner Lisa Dunphy said. Thirty-five firefighters responded, but lost the battle. After the fire, something amazing happened. The Dunphy’s friends, and even their competitors, lent tools and shop space 30 minutes away, so Joe and Lisa could keep their employees working. Although it took a year to rebuild the facility, they were actually back in business within days.
Would you be?
Got a plan?
Neither of the disasters mentioned above resulted in injuries or deaths because they both took place when the shops were closed. But the first concern for any disaster plan needs to be protecting life. Joe Dunphy is a wonderful example of the fact that buildings and equipment can be replaced. People can’t be.
A short safety meeting on the first Monday of every month can save lives. Just reminding staff to drop everything and leave, if it’s done often enough, can actually train people to do just that. One great way to conduct such a meeting is to have a fire marshal or firefighter walk through the building once and help develop a checklist and then once a month have the staff do a walkthrough to make sure everything on the list is in order. Concerns such as proper storage of combustibles and keeping escape lanes open might top the list. Checking smoke alarm batteries, learning the locations of fire extinguishers and testing emergency lights above exits can also help prevent a disaster or save lives in the event that one occurs.
Almost every state offers a template for creating a customized fire prevention or disaster plan. Most insurance companies also offer packages that help woodshops write and implement such a plan. Insurance providers and states work together on this issue, too. For example, the Texas Department of Insurance offers a sample fire prevention plan as a public service at www.tdi.texas.gov.
Most plans begin with escape routes. These are often marked with tape or paint on the shop floor. A good plan has at least two escape routes from each part of the building. Local codes generally require a light above each exit, supported by a battery pack so it works if the power fails.
The next element in a plan usually involves conducting fire drills that teach people how to use the escape routes and find exits. Plans also involve placing fire extinguishers at strategic locations, training people how to use them and having them inspected and recharged at set intervals (usually once a year). There are different types of extinguishers for different types of fires, and employees need to know which one to use. The three most common are A, B and C and some extinguishers will handle all three (ABC) while others only work on one type of fire. Read the labels.
Class A: Paper, wood, cardboard and most plastics.
Class B: Liquids such as gasoline, kerosene, grease and oil.
Class C: Electrical — machines, wiring, circuit breakers, outlets, etc.
There are also Class D extinguishers that are found in industrial and lab situations where one might find combustible metals such as magnesium, titanium, potassium and sodium. And Class K fire extinguishers are designed for commercial kitchens where they work on cooking oil and fat fires.
Smoke alarms can be a challenge in woodshops because fine dust can set them off and they can’t be heard above the sounds of dust collectors and routers. There are hard-wired, battery backup units available that work on the rate of rise of heat in the building, rather than detecting smoke. However, most fire experts advise installing an alarm that is part of an integrated security system, where a signal is sent to an offsite monitoring service. In addition, there are alarms that flash bright red lights instead of, or in addition to, the siren and these will catch the attention of workers who are running noisy machines.
Sprinkler systems can be designed with zones, so a small fire in one location doesn’t cause all the inventory in another unthreatened area to be destroyed by water.
Causes of fires
While wood stoves account for a significant percentage of woodshop fires, there are many ways to burn down the building, too. Dust collection systems are vulnerable to sparks and fine dust can ignite and even explode if the system is inadequately grounded. Buildup on the walls and surfaces in a spray booth can be very volatile, especially if the shop is spraying lacquer and oil-based products. A small electrical short can cause such buildup to combust and that’s a fireworks show worth watching. Improper storage of flammable liquids (they need to be in a fireproof cabinet) causes a lot of shop fires. Oily rags will spontaneously combust if they have the right mix of oxygen, fumes and heat — and it doesn’t take much heat. Pilot lights on furnaces and gas appliances are sources of ignition, especially close to spray booths.
One other problem sometimes rears its head, too. The neighbors. Many fires in commercial properties are caused during the night when neighboring chimneys or even trash-burning barrels send sparks through the air.
In forested areas, woodshops need to clear combustible materials away from the shop building (check with the local fire station for guidelines) so that natural fires caused by lightning don’t take too high of a toll.
Other disasters
Fire is the most immediate disaster a woodshop needs to consider, but there are other emergencies, too. Natural phenomena like Hurricane Sandy remind us that floods, high winds and even heavy snow loads can threaten our lives and livelihoods. During the last few decades, the insurance industry has managed to separate flood and water damage from other issues such as fire, hail and wind damage. Check with your agent before the storm arrives: you might need a separate policy for flood insurance, even if the shop isn’t located in an official flood zone. While you’re there, ask how water damage from a sprinkler system, plumbing emergency or even a fire truck hose is covered. You might be surprised to find that it isn’t.
In the woodshop industry, another type of disaster happens frequently. Not as dramatic as a conflagration, personal injury in the woodshop can still be extremely costly for both employees and employers. One of the major causes of injury, kickback, can be reduced and virtually eliminated with adequate training. Teaching workers not to machine warped stock is a good place to start. A training program should also include learning how to check fences for alignment, not reach across blades or cutters, use push sticks on the jointer, remove chuck keys before turning on the drill press and not to underestimate the power of a band saw. One shop in the Midwest has a large photo of beef being sawn pasted to the top door of its band saw, just to remind employees that this seemingly safe machine is used in the food industry to cut through skin and bone.
Clean workstations, adequate training and keeping safety guards in place all go a long way in preventing personal injury disasters. So do dust masks, air filtration systems and water-based spray finishes and adhesives.
Insurance
Ask your agent about the difference between replacement cost and market value. If the shop is in a historic district, this can be an issue. The building might be worth a lot more or a lot less than the amount the insurance company thinks will replace it because they might be thinking OSB when what you have is sandstone.
Deductibles are a great way to reduce premiums as long as they are reasonable (don’t take them too high). A woodshop is in a fairly unique position to take advantage of higher deductibles. If the shop has to pay the first $5,000 of any claim rather than just the first $500, the monthly premium will often be a lot lower. And woodworkers can often handle those $5,000 repairs themselves, rather than hiring a carpentry crew. They usually have all the equipment and knowledge to replace windows or cabinets or maybe do a little framing or even roofing.
Find out what is excluded in the shop’s insurance policy. Today, that often means floods and water damage (mentioned earlier) and also acts of terrorism.
One last suggestion for shops that are concerned about avoiding or surviving a woodshop disaster is to visit the local fire department, invite them to the shop for lunch some day and give them a tour of your facility. That way, the responders are at least somewhat familiar with the building layout. And while that might save a lot of equipment and inventory, it might also save a fireman’s life.
This article originally appeared in the April 2014 issue.
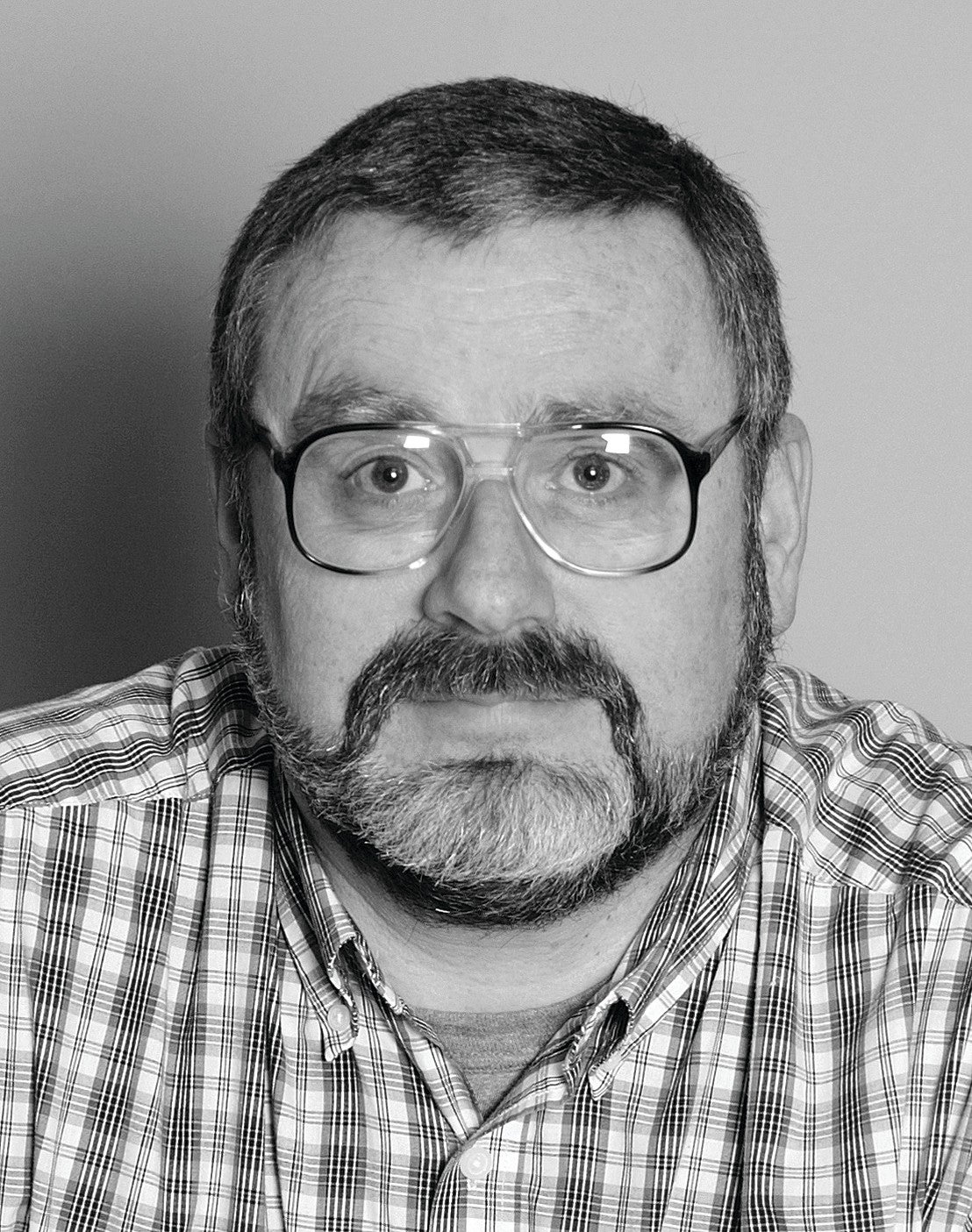