Choosing abrasives
Save time and money by understanding the different types and backers available.
Consumables.
That’s a scary word for woodworkers because it means that the shop is essentially burning up dollar bills. One of the most obvious forms of consumable is sandpaper, and it hurts just as much to replace dozens of discs as it does one wide belt. So, woodworkers have come up with many ways to try to use every grain of abrasive. They cut off the unused sections of sheets that are held under the clamps on small sanders and use them for hand detailing. They rub resin bars on moving paper to unclog between the abrasives. They buy rolls of sandpaper and use a template to cut their own discs or detail sander triangles. But all of these penny-pinching solutions use up a different and often far more valuable consumable – time.
The smartest way to conserve is to buy the best and most appropriate abrasives in the first place. And choosing the right product means discovering the differences between cost, wear, clogging and other factors. And that can be confusing. For example, Grizzly Industrial (grizzly.com) offers 385 aluminum oxide sanding belts, 28 silicon carbide belts and five zirconia aluminum varieties.
Abrasive types
Every woodworker is familiar with traditional garnet paper, which is made with a naturally occurring material (today, most abrasives are manmade). Garnet isn’t friable – that is, it doesn’t break down the way other manmade abrasives do, so it tends to clog faster and cease to work properly. It’s not as tough as its newer cousins, so manufacturers don’t embrace it as a material for discs. It is relatively expensive, but when one balances the initial cost against its limited life, it probably doesn’t offer much of a saving. Garnet paper is still widely available because big box and local hardware stores like being able to offer the lower price point, but it doesn’t have too many fans among younger woodworkers who need to remove stock quickly. It does, however, enjoy some popularity among finishers as it seems to allow stains to penetrate more evenly, especially on wide-grained species. One limiting factor is that it isn’t widely manufactured in finer grits (320 is about the finest) because of the natural grain size.
Emery can be a naturally occurring alternative that picks up where garnet leaves off. It was originally just ground emery stone (corundite), but today’s version is a crystal form of aluminum oxide that is combined with clays and other metals to make a fine grit abrasive. Wet/dry versions can be used with liquids (oils, water) to create a sludge on finishes, producing a glassy surface as one works through progressively finer grits. Emery cloth is exactly that – a more flexible (and expensive) version of the abrasive than paper-backed, and it can be used to work around shapes and profiles.
Aluminum oxide is the most common abrasive in the woodshop. In its purest natural form, this is an odorless powder made up of tiny crystals that takes the form of corundum, bauxite and other minerals. It is thermally stable and won’t dissolve in water, plus it’s exceptionally hard and that makes it difficult to wear down. That’s critical here. Normally, the grit doesn’t wear much or fracture to expose new edges. Rather, it lasts a long time before the edges become dull. There are more expensive versions that have been treated in furnaces that will break away and reveal new cutting surfaces, and those friable options are slowly becoming more affordable.
Silicon carbide is harder than aluminum oxide, and under a microscope it looks like a shattered window. But hardness alone doesn’t cut or last, and its brittle edges make it too friable for most initial wood sanding operations (it’s the preferred option for metal). However, that quality also makes it the perfect choice for working between coats, and for rubbing out finishes. It’s perhaps most familiar as black wet/dry sandpaper sheets.
Technically, some of the other abrasives would qualify as ceramics, as the word simply describes a solid compound that is primarily held in ionic and covalent bonds. But when woodworkers talk about ceramic abrasive, they are referring to expensive, manmade, non-friable, coarser grit coatings on belts. These ceramics are sometimes combined with industrial diamonds to create a fast-acting, very aggressive product.
Chromium oxide is most often used as a pigment, but it also used as an abrasive in stropping and sharpening compounds. It also appears as a very fine paper-backed abrasive that is used more for sharpening hand tools than sanding wood. For example, Lee Valley & Veritas (leevalley.com) offers a one-half micron sized grit on an 8-1/2” x 11” sheet (item 54K95.01) that gives metal a mirror finish.
Backers and bonds
Paper, fabric, foam, plastics, polyesters and many other sheet materials are used as backers for sandpaper. One of the key factors here is stiffness. For flat sanding, a stiffer option offers obvious advantages. For curved surfaces and tools that bend the backer (such as belt sanders), a far more flexible option is needed. Paper backers range from A to F (light to heavy) and cloth grades are J, X, Y, T and M, with the latter being the most substantial. Some very fine operations also use emery or chromium oxide abrasives and these are often bonded to a Mylar (polyester) backing.
After grit, the bonding agent is perhaps the most critical aspect of the manufacturing process for sandpaper. The bond needs to hold the abrasive steady, so that it doesn’t roll or fall off the surface. It needs to be made from a material that won’t transform from a solid to a liquid as it heats up. It needs to be a material that won’t bond with the wood fibers or finish particles, and clog quickly. Many of the products now offered have a stearate added to the bonding agent. Think of it as soap, or lube. Some papers have an open coat, where there is more room between the abrasive particles for waste to accumulate. Of course, that means there are also fewer particles, so the job takes a bit longer.
Last September, Mirka introduced a couple of interesting new abrasives. Iridium is paper backed and Novastar is a film-backed, waterproof and non-clogging product. Both come in 80- to 600-grit versions. What’s intriguing is that they seem to represent a shift in technology, with new optimized grains, new coating and curing techniques, and new multi-hole patterns for dust extraction.
Not all backers are paper, fabric or film. Ekamesh discs (24 to 2500 grit) from Uneeda (sandpaper.com) have a unique net pattern that’s designed to improve dust removal. The aluminum oxide abrasive is attached with a resin, but the open weave of the backer allows for impressive dust extraction.
More and more, suppliers are recognizing that woodshops need different abrasives for different tasks. For example, Festool (festool.com) now offers four families of abrasives. Rubin (40 to 220 grit) is a close coated, aluminum oxide product that’s bonded with a synthetic resin and has a special coating that sheds wood fibers. Granat (40 to 1500 grit) is designed for long life and is the company’s highest performing abrasive. Saphir (24 to 100 grit) is for aggressive stock removal and heavy stripping jobs of hard, stubborn and thick coatings. And Platin 2 (500 to 4000 grit) is an open-coat, silicon carbide abrasive that was specially developed for high-gloss finishes.
The grits are changing, too. Ceramics may be the future of sanding, although they need to see some improvement at the finer end of the scale. But combining ceramics with tried and true solutions seems to be one way forward. For example, Saint-Gobain has a new generation of abrasives that includes a ceramic alumina that the company says cuts faster and lasts up to twice as long as standard abrasives.
Hermes Abrasives Ltd. (hermes-schleifwerkzeuge.com) has a nice interactive resource on its website that allows a woodshop to select the material, abrasive tool and machine (portable or stationary), and then see the company’s catalog of products that are designed for that application. SIA Abrasives publishes a downloadable catalog of its wood sanding options at siaabrasives.com.
This article originally appeared in the February 2019 issue.
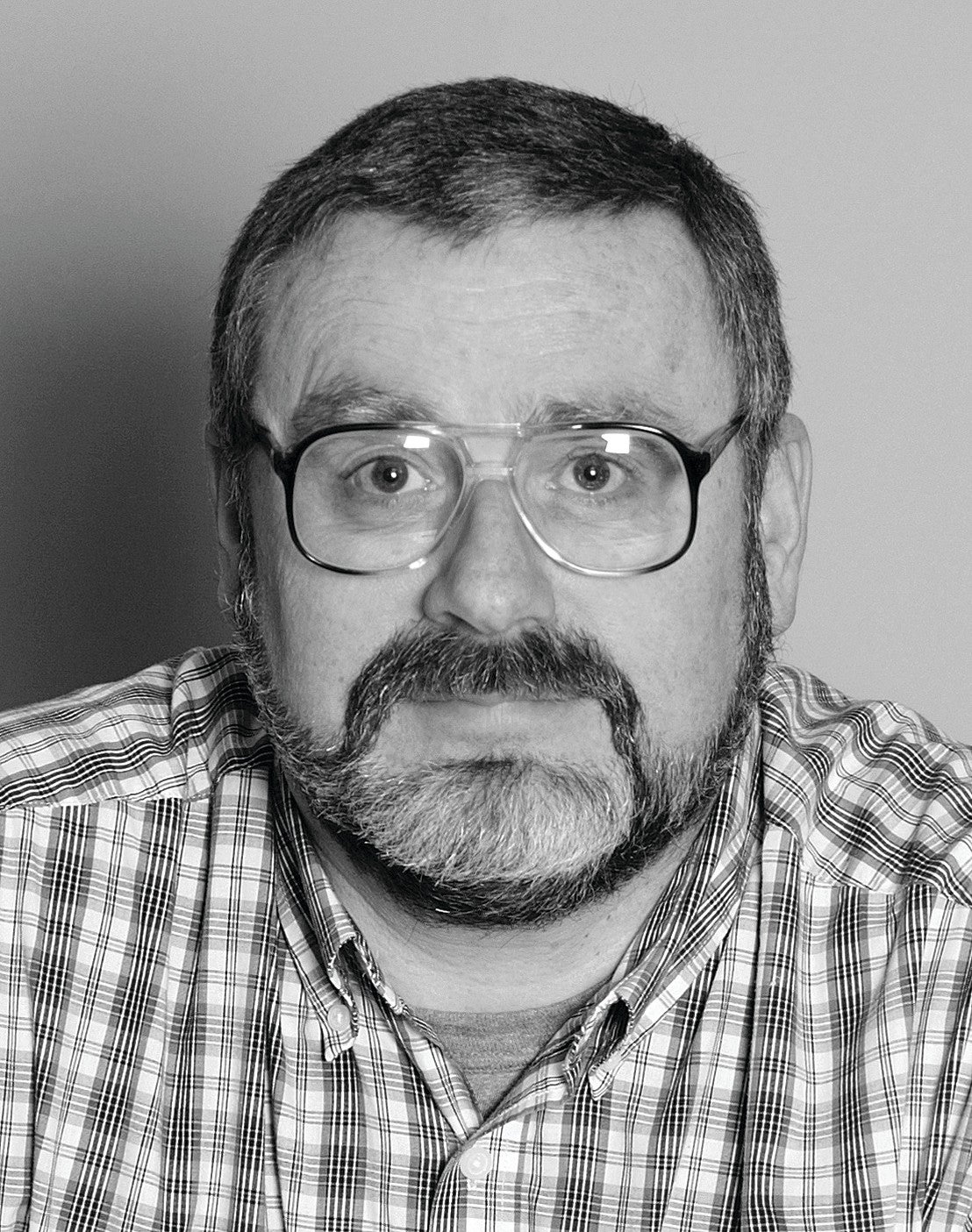