Updates to an Ancient Art
Newer joinery options incorporate automation, dedicated equipmenmt and more.
The oldest known woodworking project on the planet is a 7,490-year-old timber framed lining in a water well near Leipzig, Germany. It’s held together with pegged tenons and half lap joints – all made in oak timbers using Stone Age tools! The archeologists who made the discovery in 2012 said that a total of 151 oak timbers that were preserved in a waterlogged environment have been carbon-dated to between 5469 and 5098 BC, and reveal “unexpectedly refined carpentry skills”. A similar well was discovered in the Czech Republic in 2018 and scientists estimate that one was constructed from oak that was harvested around 5255 BC, which would make it 7,276 years old.
What’s surprising is that those same joints are still in widespread use in the custom furniture market. Industrial cabinet joinery uses various types of plastic and metal hardware, but furniture builders still rely heavily on traditional joints such as dovetails or mortise and tenons. True, these are more often machined nowadays than hand cut, especially with the evolution of portable CNCs and floating tenon tools. One must expect some progress over seven millennia.
A woodshop looking for strong, easily made, repeatable and aesthetically pleasing joinery might first wish to take stock of its current resources and then design accordingly. For example, a shop with a CNC router obviously has more options than one with only a workbench and some hand tools. Larger factories producing high volumes of casework in dedicated work cells will have a different approach to joining than woodshops that are making a few dozen drawers every month, or furniture artists who rarely even build a box.
So, the type and volume of work combined with a shop’s physical resources tend to determine joinery options.
Mechanical joinery
Colonial Saw (csaw.com) has Lamello’s new Divario P-18 starter set (Item 145551, $325) that allows the installer to insert shelves or dividers in completed cabinets, simply by sliding them in place. The connector makes it possible to assemble components at the most cost-effective stage in the chain — whether at production, storage, transportation or assembly. It can be either fully or partially fitted on site and is detachable for transportation.
The new Claw Connector from Häfele America (hafele.com) can really simplify drawer joinery. A woodworker just needs to drill a couple of holes, pop in the connectors and then fold out the drawer-sides like a book. The connectors lock into the back of the drawer face with no need for tools, glue, clamps or even much more than a few seconds of time. The one-piece, zinc alloy connectors are designed for stock that is at least 1/2” thick, so they will work with thin fronts. They’re even removable. A shop can manually or CNC drill a 3/16” hole in the end of the drawer side and a 5/16” hole in the back of the drawer face, and that’s all there is for joinery. A matching tool-free connector (the RPC D 5/24) can be used to pop the back panel in place. Together, these two connectors can reduce drawer assembly time to a few seconds.
Knapp Connectors recently introduced the Quick-Set, a two-part locking dowel system for joining cabinet parts. It’s a snap-together system that’s available in a free sample pack from knappconnectors.com.
Blum (blum.com) has released EasyStick, a new ruler system that is designed to deliver fast and simple machine setup for installing Blum hardware on cabinet parts. It works on the company’s three MiniPress machines manufactured after 2007 and is essentially an automated stop block.
BeA Fasteners USA in Greensboro, N.C. (beafastenersusa.com) makes nail guns and supplies. One of its product lines, Autotec, is a way to mount nail, pin and staple guns in machines with the capacity to shoot a large number of fasteners without reloading. It’s an ideal doorway for shops that are thinking of adding robotic parts nailing or stapling. BeA has guns that work on collaborative robotic arms.
Pocket power
Castle USA in Petaluma, Calif. (castleusa.com) offers a unique solution to woodshops that are building face frame cabinets. The company’s line of pocket cutting machines range from a small desktop model to a large, high-volume machine with automatic pocket screw insertion. What’s special here is the angle of approach. Castle’s pocket screw holes are made in a two-step process that uses a drill for the pilot hole and a router bit for the pocket. The screw approaches the work at a very low angle – just 6 degrees. This means the parts don’t shift as the screw is drawn tight. It’s also strong because the fastener is almost horizontal as it enters a stile from a rail, so the tip doesn’t travel too close to either face as the screw seats. The company’s recently updated benchtop model 110 is very rugged but weighs just 13 lbs., so it’s a solid solution for jobsite joinery. Another Castle benchtop machine, the TSM-12, is more shop-bound at 65 lbs. It’s a 110-volt machine that can handle stock up to 1-1/2” thick and has both a 4” and a shop vacuum dust port.
Kreg Tool (kregtool.com) has completely redesigned its pocket hole jigs. The new 720PRO ($149.99) automatically changes clamping and hole alignment for different thicknesses of wood from 1/2″ to 1-1/2″ thick. There’s onboard storage for accessories such as drill and driver bits, and the jig comes with a Docking Station that provides support wings for large pieces.
Celtic connections
OVVO has been winning lots of awards at European woodworking shows over the past few years for its joinery solutions. The company (ovvotech.com) distributes product in the U.S. through E.B. Bradley Co. in Los Angeles. OVVO has now introduced three new products in its V-1230 drilling range, and all three of them use standard 32mm centered 8mm holes without the use of tools or glue. The first is a releasable version with a 25mm leg. Then there are permanent versions with 20mm or 10mm legs. They use the company’s Push-Click-Connect and work with equipment from most major manufacturers, including Homag, Felder, HolzHer, Laguna and CNC Factory.
OVVO’s connectors also work with the PantoRouter (pantorouter.com), a tool that delivers highly precise and repeatable joinery in a budget-minded format that bridges the gap for smaller shops between hand-held routers and CNCs. This joinery option can mill single and multiple mortise-and-tenon joints, simple and compound angled joints, custom shaped joints, plus fast and accurate dovetails and box joints. The PantoRouter uses an ingenious guided bearing system to follow a template, and it is especially well-suited to furniture projects such as chairs where angled joints are common.
Another joinery machine, the JDt75 from Cantek America (cantekamerica.com), is an automatic dovetailer that can handle parts up to 59” long and 16.93” wide. The spindle rotates at 21,500 rpm for an extremely fine finish, and the high speed allows for precise machining of both plywood and solid drawer sides. There’s independent adjustment of both the tenon and the mortise depths, for precise fitting of the dovetail joints. The JDt75 has a dust hood, a safety rail in front of the spindle, and high-quality pneumatics for smooth feeding. There’s a cast iron base to absorb vibration, and automatic lubrication for the spindle stroke. It has three cycle speeds for getting the best results in various materials and thicknesses.
Woodstock International (woodstockint.com) offers two small-shop dovetailers in its Shop Fox brand. The W1804 accepts workpieces as large as 28” long x 11-1/4” wide and as small as 7-7/8” x 2-3/8”. It includes templates for four different dovetail sizes. And the larger W1805 is for work that measures up to 59” x 16-1/2”.
A similar machine from Laguna Tools, the DT18, can cut the pins and tails separately or at the same time to speed up production. Individual pneumatic clamps allow users to cut two joints in one pass or to work on wide panels for furniture. The centralized control panel makes the operation easy and automatic; the operator just needs to load the parts and start.
Laguna (lagunatools.com) also offers the SmartShop LD4, a CNC router built specifically to drill and insert fasteners for manufacturing cabinets, drawer boxes, closets, desks, solid wood furniture and many other applications, including OVVO and LockDowel.
Felder USA (felder-group.com) presents the Kappa 590 e-motion, a table saw that can tilt 46 degrees left or right. That opens up a host of joinery possibilities and cuts down on jig making, setups and errors due to reversing parts for compound cuts.
SCM Group USA (scmgroup.com) has the Compex angular cutting guide for its Class table saws, useful for shops building with angles other than 90 degrees. The entry-level Class Si X sliding table saw has a blade that tilts left or right and now comes with automatic positioning of the overhead blade guard, which means the operator doesn’t need to make adjustments for safety when the setup for cutting is changed.
Mortising and more
Rikon’s benchtop X-Y Mortiser, model 34-260, features a sliding X and Y axis table. Front controls move the table either forward, back or side-to-side along dovetail ways.
Few tools express the melding of ancient joinery with modern technology as the family of Festool Domino joiners (festoolproducts.com). The DF 700 XL EQ Plus (item 574447) is a complete package for creating mortises with floating tenons. The patented cutting action rotates and oscillates to create perfect, clean and repeatable mortises every time. The woodworker can adjust the mortise width with the turn of a dial. The tool can use tenons up to approximately 5-1/2” in length.
The ancient concept of using floating tenons was perhaps in part the inspiration for all of the plastic and steel joinery options now available. From Fastenlink’s ingenious dowel system to Hoffmann USA’s clever dovetail inserts and Lockdowel’s comprehensive family of fasteners, casework and furniture joinery has come a long way since those Neolithic carpenters built their oak-lined water wells.
This article was originally published in the April 2021 issue.
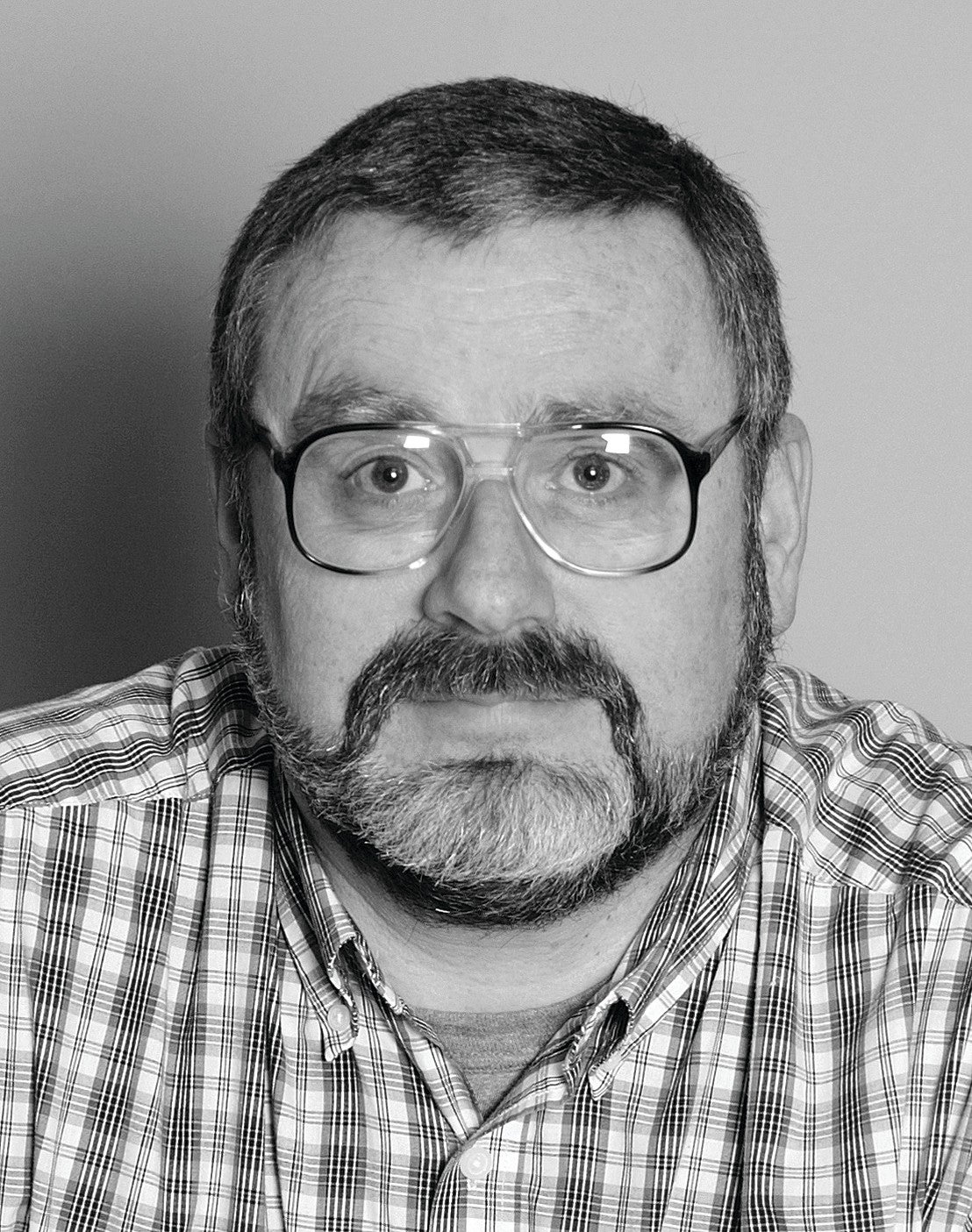