Too much is never a good thing
There are several categories of waste in a woodworking business that require attention and action
The tired old phrases are everywhere, such as “one man’s trash is another man’s treasure” or “a dollar saved is a dollar earned”. Nobody disputes that reducing waste can add to profits. Persuading people of that is not the problem.
Finding intelligent ways to control waste, now there’s a quandary.
Woodworking is a custom business, so it’s no surprise that different shops have different types and volumes of waste. But there are a number of universal practices in the business cycle that can be separated, examined, and perhaps upgraded.
First off, let’s define waste.
The immediate response here is usually that waste is using a resource carelessly while failing to conserve it. For example, not sealing a gallon of finish so it evaporates, or leaving the shop lights on all night. In that same vein might be discarding materials unnecessarily, or regarding cut-offs and excess inventory as unusable. In other words, being too eager to fill the dumpster.
What’s interesting here is that definition doesn’t address the largest volume of waste in most production processes – man hours. The concepts above refer to physical resources that are generally quite inexpensive when compared to salaries and wages. But short boards and glue bottles are far more visible than lost time, so it’s no surprise that most woodshops tend to lean toward physical discards first when auditing their waste. It may be time to think of waste in a new way.
So, should a shop owner spend any of that valuable time on devising ways to control waste?
That’s an easy question to answer because it’s actually quite quantifiable. Bookkeepers say that gross profit is what’s left from sales revenue after subtracting the costs of production and distribution. Net profit is that number, less all of the woodshop’s other expenses. Most businesses are satisfied with a 10 or 12 percent net margin (the taxable profit after all costs and expenses are subtracted from revenues). Poorly run companies will realize less than that, and well-run affairs can achieve 15 or even 20 percent net profit.
At 12 percent, it takes $833 in cabinet sales to realize $100 in net profit. So, to make $100 profit, the shop can either sell, build, finish and deliver another $833 in product – or find a way to trim $100 from its costs. This makes controlling waste an imperative.
There is, of course, a limit to how much one can control or reduce costs, but there’s also a lot of unrealized potential to do so in most businesses. It’s important to learn exactly how profitable the shop is before undertaking any cost-cutting efforts. An operational audit can tell the shop owner which steps in the buying, production, administration or even delivery processes are costing more than they should. Such an audit can also reveal whether outsourcing is a smart step from a financial point of view. If it’s less expensive to order in some components than to make them in-house, and the quality is the same or better, then outsourcing is step one in controlling waste.
Let’s talk lean for a moment. In these troubling times with interruptions in the global supply chain, just-in-time doesn’t always work as well as it used to. Plus, lean cells aren’t as efficient when a shop can’t hire operators, and lean purchasing is hard to manage when the cost of materials is climbing at rates up to 300 percent annually and the warehouse shelves are empty. Lean works best in a well-oiled, evenly paced industry. In extraordinary times, it has a few hiccups.
The basic principles are still sound. It’s still incumbent on shop owners and managers to reduce waste to an absolute minimum. It’s just not always practical in a dynamic market.
A smart shop owner will keep that in mind when purchasing. It’s tempting to indulge in the exuberance of a post-pandemic recovery and to become part of the regional red-hot real estate and building booms. But price hikes in materials should be signaling to shop owners that an old enemy may soon rear its head. Inflation plays havoc with purchasing in a lean manufacturing environment. The lean concept is all about controlling waste, but it doesn’t seem to have an answer for 2021. Is it smart to buy a bunk of plywood now, anticipating further price hikes? Or are we nearing a crest where mills and shippers are recovering thanks to vaccines and other measures, so supply will soon be able to satisfy demand? Many analysts seem to think the latter, but those are the same experts who failed to predict the current price trends. We had a short recession last year, and we’re having an uneven recovery.
Human resources
As the most expensive element in most production processes, paid time should be near the top of any waste control list. There are the simple solutions – hire a part-time college kid to sweep the floor and empty the dust collectors, rather than paying a skilled cabinetmaker to perform such tasks. Use a faster drying glue, or a process that requires shorter clamp times such as UV or LED cured adhesives. Take a look at how jobs move through the shop. Are the tasks broken down into timed units so that nobody is standing around waiting for parts? Are skilled people wheeling carts around when a simple conveyor could be saving their time?
Shop owners are very much aware that there’s a shortage of trained labor in the woodworking industry. There are two ways to tackle that. The first is to hire people and train them in-house so that they have skills that are related directly to that specific woodshop’s needs (rather than the general skills learned in classrooms). That can be expensive. Even though new people are somewhat productive during training, they’re also using up some of their skilled co-workers’ expensive time, plus the supervisory staff’s time. In the long term, such an investment can certainly pay off, as long as they stay with the company.
The other alternative is to increase automation, which can have a dramatic effect on reducing wasted man-hours while simultaneously addressing the labor shortage. Shops with access to multiple axis CNCs, aggregate heads on lesser platforms, and collaborative robotic arms should keep an eye on the constantly evolving solutions in hidden connectors. The wrong connection hardware can slow processes down, while the right one can accelerate the pace of assembly. The type of connector largely depends on whether a shop is building ready to install or ready-to-assemble casework. One and two-part connectors can seriously reduce assembly time and downtime for clamping and curing. They can also save a lot of time on job-site installations, and many can be automatically inserted on the CNC and clipped together on the job. It can be faster, and consequently less expensive and less wasteful to move a flat-packed pallet or two than it is to move an entire kitchen of completely assembled cabinets.
Beyond assembly, virtually any repetitive task can be automated – whether that’s having a robotic arm spray finishes or pick hardware, installing a programmable stop system on a miter saw station, or using an aggregate head to mill slots and holes for pulls and slides. All of these tasks reduce man hours. Taking that to the next step, a shop can create a work cell that integrates edge banding, and several CNC manufacturers have now created more affordable self-contained cells that do, by adding conveyors and better control interfaces.
Optimizing software has come a long way, and it definitely reduces waste when it comes to sheet stock. A good program will include an inventory module that tracks partial sheets, so that the CNC operator isn’t always starting with a full sheet and can use cut-offs to replace any rejected parts after the job is run.
Good marking (stamps or labels) can save a great deal of time during assembly, and it can also help orient parts correctly so that there are fewer defects. The only thing more frustrating than mistakenly banding an edge that belongs in a dado is discovering that somebody did so on a whole batch of parts.
All of these measures are already in place in many larger woodshops, but technology is evolving fast enough to make many of these options affordable and viable for even one-man shops.
Dumpster dilemmas
After wasted time has been addressed, a manager can take a look at wasted materials. Here, the first step is to find out exactly what goes in the trash.
It may be worthwhile separating waste before it is discarded, especially if recycling is an option. Some waste processors will distinguish between hardwoods, raw MDF, and foil or paint coated cut-offs. They may charge less to process certain categories of waste, and a shop might even find a secondary buyer who will actually pay for waste. Some larger shops and plants burn waste to generate heat or electricity, and these may accept and even purchase waste from smaller shops.
Small shops may also discover that the local high school’s woodworking program will accept donations of hardwood and plywood remnants, and this could possibly be deductible.
If there’s enough waste, it may be worth exploring the option of purchasing a biomass pelletizer or briquette press – or coordinating with several other local shops to do so. It’s not just the cost of the machinery here, but also the operation of it. There’s crushing, drying, milling, cooling and packaging to consider. Then, what do you do with the pellets or briquettes? It takes more time and dedication to market, sell and ship those products, too. This type of waste processing requires quite a bit of planning.
Disposing of sawdust in other ways can be tricky. It doesn’t always lend itself to animal bedding because of contaminants such as resins, toxic or allergenic species (for example, many animals are allergic to cedar or walnut), and the grain size and absorbency characteristics. Plus, a lot of what we process already has some kind of coating. Pine works well for animals, but it needs to be clean. Poultry farms may be interested in buying pine dust, chips and shavings.
Sawdust also works for cleaning up many commercial and industrial spills or residues such as oil and detergents, and there are several ways to use it as an ingredient in compost. Some of those involve reducing it to charcoal, while others require aging to begin the degrading process. Sawdust introduces carbon to balance the nitrogen that is inherent in the vegetation waste that is used to make compost. It can also alter the pH balance of acid and alkali in garden soil, so it may need to be balanced with the addition of lime or gypsum. Too much sawdust can cause a nitrogen deficiency, so it’s a good idea to have the soil tested. Chips are better than fine dust here, because they don’t absorb the nitrogen as quickly.
Another popular secondary use for sawdust is as a mulch, but again contaminants can be a problem if the plants being mulched will become a food source. Some species such as walnut can actually kill plants including tomatoes and some fruits. Mushroom growers prefer shavings to fine dust.
Regional MDF factories may buy sawdust if it’s in sufficient volume and meets specs.
Other considerations
In larger woodshops, installing a fully automated blast gate system can mean significant savings on the electric bill. Dust collection uses a lot of juice to move large volumes of air at speeds that will keep waste in suspension. If a shop is only paying for fans to operate in ductwork that’s being used, fewer fans with fewer active hours are required. Small shops can also gain some savings, but in one- and two-man businesses the central vac isn’t usually running all day long. The main advantage there is simply more suction and better dust control.
For shops that use a lot of solid hardwood, it can pay to have somebody sort through the inventory and re-classify it. This may allow the shop to buy lesser grades for many processes. Not all hidden parts need to be select, and sometimes a lower grade board can yield select shorts between the knots for parts such as cabinet door rails.
The U.S. is back in the Paris climate accords and woodshops are going to see a lot of new regulations over the next few years regarding how they control waste.
One opinion being expressed about such regulation is that there will need to be a new category of professionals that woodshops can hire to manage relationships with government agencies and handle all the reporting paperwork. While the regulations will most certainly make shops think about how they control waste, and how that can become more efficient, any financial gains from tweaking will probably go to hiring those professionals.
Finding intelligent ways to control waste is all about buying well, designing to the material specs, disposing smartly and choosing processes that create fewer emissions. Global competition, supply bottlenecks and increased government regulations are forcing woodshops to be smarter and leaner. Material prices and supplies will gradually nudge their way back to something we can call normal, but this market and indeed the entire world is never again going to look exactly like it did just a couple of years ago.
This article was originally published in the July 2021 issue.
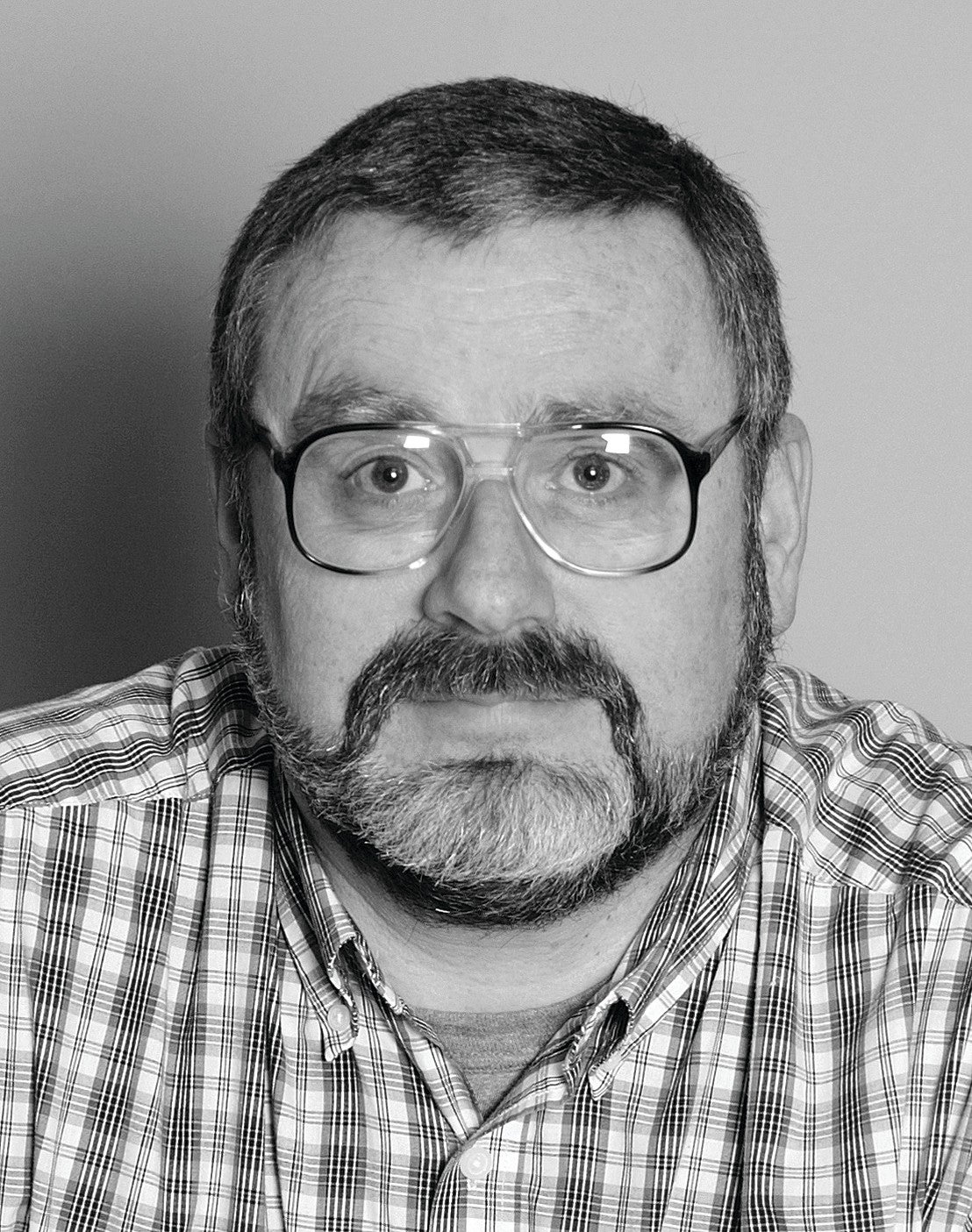