Time machine
The folks who teach business theory have a big challenge. They need to reduce something as incredibly diverse as the global economy to a concept that can be nicely packaged…
The folks who teach business theory have a big challenge. They need to reduce something as incredibly diverse as the global economy to a concept that can be nicely packaged in a few textbooks. Every time somebody wins a Sveriges Riksbank Prize (the Nobel Prize in economics — and 45 of them were awarded between 1969 and 2014), boardrooms and classrooms on every continent have to adjust curriculum. Sometimes we just find new words to describe old habits, but every now and then there is a gem of originality.
The strongest theory from the last 50 years is called lean manufacturing. There are a number of definitions for it, depending on which school of business or industry is speaking, but the overall concept is incredibly simple: reduce waste.
OK, that’s a little simplistic. Lean manufacturing isn’t just a single act. It’s an entire systemic method for reducing and eliminating waste. It’s a corporate philosophy that starts with the CEO and works down through every employee, where everybody is doing everything possible to identify and eliminate wasteful practices.
One definition is that lean manufacturing focuses on getting the highest throughput with the least inventory. An example of that would be a woodshop that orders its hardware, sheet goods and hardwoods so efficiently that the materials arrive just before the job starts and at the end of the project there are no leftovers.
Disciples of lean philosophy have spent several decades both formulizing and formalizing it. They have given distinct names to various elements and these are often based on the concept’s Japanese roots — words such as Kaizen (continually improving), Gemba (the physical location of an activity) and KanBan (a signal, such as a card placed in a stack of parts that tells somebody when to reorder).
One element of lean manufacturing that has a somewhat familiar ring to it is the work cell, which is also referred to as cellular manufacturing. Even without reading a textbook, most of us can guess that this describes a group of people working together.
Or does it?
Work cells defined
Actually, no it doesn’t. A work cell describes the way that the workplace has been designed, so that people using it are doing so in the most efficient manner. In manufacturing situations such as woodshops, the cell often takes the form of a horseshoe, which the academics have decided to call a U-Shaped Cell. The idea is that machines or assembly stations are set up in a U-shaped pattern so that employees can gain the maximum benefit with the least amount of effort. Because each element (think perhaps workbench or table saw here) is physically close to the next element, time spent traveling from one to the other, or more importantly moving parts from one to the other, is cut to a minimum.
These cells are often created as sub-groups of the process. For example, there might be one cell for sawing, another for milling or box assembly, drawer assembly, sanding, face-frame construction and so on. Each cell is self-contained and can be quickly adapted to create a different part or handle different dimensions.
While none of this is Earth-shatteringly new, implementing the concept does force a manager or a shop owner to think about how things are done and how they might be done more efficiently. That efficiency, in lean manufacturing, is measured in terms of waste. How much employee and management time, materials, utilities (heat, light, power etc.), insurance, finance charges, training costs, machinery and other resources are being spent and is there a way to trim all, some or even one of these to reduce waste?
The shape of the cell doesn’t necessarily need to be a U. Some processes work better in a linear (straight-line) configuration, where materials come in one door and finished products leave through a bay at the opposite end of the building. Other work cells are H-shaped or can be described as circles, arcs or even parallel lines. While the U-shape seems to meet the needs of most manufacturers, even polygons or squares sometimes work best. The U just seems to consume the least amount of floor space and worker time/motion.
Time and motion
Some processes take longer than others. When a manager is designing the layout of work cells, this is an important consideration. For example, it takes less time to clamp a drawer together than it does for the glue to dry. Because lean manufacturing is a top-to-bottom philosophy, it assumes that the manager will actually use his or her team to help design the cell. People on the shop floor know how long small tasks take and how critical each one is and a manager who ignores this resource will pay for that choice by having to spend more time tweaking and adjusting the model for greater efficiency later on.
Sometimes the disparity in timing (clamping as opposed to curing) requires that the woodshop create more than one cell. The first might have somebody applying clamps, the second might have somebody else stacking clamped drawers on carts and the third might have another team member removing the clamps. If the first person gets the empty clamps from a rack and the last person puts those clamps (now empty again) back on the same rack, one can see the potential for a U-shaped process.
Timing can play a role in staffing a cell. Perhaps it is more efficient to have two people clamping — one stacking and two removing clamps. Cells are generally created for a single worker, but can ideally be adjusted to accommodate more people for specific tasks. That is, the most popular format for a cell is Load-Load, which means a single worker moves parts through his or her U-shaped station. But a work cell can have several stations with a worker at each one and, in this case, timing is critical. Each worker’s task must take the same amount of time as everyone else’s or the workflow will be interrupted.
Another efficiency that can be derived from breaking the production process into work cells is the elimination of redundant equipment or the more efficient sizing of equipment. For example, if a shop has two kitchens completed and the spray booth is busy, this type of bottleneck can be caused by a piece of equipment at some stage of the process (in this case the size of the booth) not keeping up with advances in other areas (where, perhaps parts are now being made on a CNC table rather than manually). Function can play a role here. Unfortunately, if the booth isn’t carrying its load, there isn’t a whole lot a shop can do about that in the short term other than perhaps adding a second shift. But if the wasted time is showing up at the milling stage, then perhaps a cell that is usually making drawer sides can be switched to make cabinet sides.
Work cells and waste management
In the most basic terms, lean manufacturing recognizes seven different areas of waste. The first of these is overproduction, where a shop makes more parts than it is selling. For example, one would think it’s a good idea to stock up on cabinet sides or even drawer boxes in slow times and use available workers to build inventory for busier days. Lean proponents would suggest that paying employees who are not directly contributing to current needs is inefficient. Their answer would be to create work cells where tasks are defined in such a way that workflow can be turned on and off, much as a spigot controls the flow of water. If employees are trained to work in more than one cell or if the function of cells can be quickly realigned to meet production needs, then management becomes in essence a function of simple arithmetic (how many do we need now?) rather than a matter of conjecture (how many might we sell in the future?).
Efficient work cells that can be activated or adjusted quickly can also help a shop tackle the second area of waste: delay. This is the situation where a project needs to be put on hold because the shop is waiting for something to be built or finished or even for outside parts to arrive.
Work cells can be used to help manage the third defined area of waste — transportation — which involves wasted time and effort that goes into moving parts around the shop or from cell to cell. This sometimes ties into delay (above). When a kitchen needs to be stopped while it waits for something, it also needs to be moved out of the way so that something else can be built at the various work cells and it needs to be stored somewhere and then brought back when the missing ingredient arrives or is built. All the time and effort spent in that moving around is, well, waste.
Work cells are very good at reducing or even eliminating the fourth defined area of waste — over-processing. This is when a worker is doing more work on a part than is really needed. For example, if the bottom of a cabinet has been sprayed with a sealer to create equilibrium (moisture balance), then there is no need to sand that sealer as it will only ever face the floor and will never be seen or touched. Such unnecessary tasks become very apparent when the entire process is divided into work cells and the workers on the shop floor are responsible for keeping up with other stations or cells. While this example is blatant, more subtle savings will certainly present themselves over time.
For example, an employee might realize that a specific edge doesn’t need to be broken on each unit and this saves a few seconds on every part that goes through that cell. While this seems very insignificant, the cumulative benefit during the course of a year might be a whole day of workshop time saved. When half a dozen cells eliminate a similar volume of waste, the shop has saved six work days a year — more than a week’s worth of wages. If the shop is operating on a 10 percent margin, the savings are the equivalent of 10 times that in gross sales. If the employee is making $20 an hour ($960 over six days), the company needs to sell nine times that ($8,640 in cabinets) just to match the benefit to the bottom line. And that doesn’t take into account marginal savings such as withholding taxes, workers’ compensation insurance and even the slight savings in overhead such as light bulbs that don’t need to burn during that week that isn’t worked.
Work cells can help a company control the fifth recognized area — inventory waste — by being flexible. This type of waste ties up both storage space and cash flow that has to be spent on materials. When a shop has too much inventory on hand, the physical results might include having to rent/heat/cool/insure a larger workshop than is necessary because the business is maintaining unnecessary storage rooms to house the excess. By being able to control the rate of work flow through the use of work cells, production can be switched to efficiently create inventory only as it is needed.
The sixth form of waste — motion — refers to physical efforts that are needed to complete parts and move them through the production process. Here, work cells shine. By reducing the square footage required to perform tasks and by creating an efficient configuration that reduces the number of steps a worker has to take within that square footage, a work cell can effectively save hours each week — and even weeks each year — on the work being done in a specific cell. Going back to the earlier example of clamps, if each bar clamp has a place to go when it is removed (perhaps a clamp rack on casters) rather than being dropped in a pile on the workbench or the floor, then that clamp only needs to be handled once. The worker doesn’t need to spend so long cleaning up the station before the next cabinet arrives. That sounds incredibly basic, but it is astonishing how many tasks in the average woodshop require more “motion” than necessary.
And every single movement that an employee makes while he or she is on the clock — even just picking up the same clamp for a second time — has to be paid.
The last area of waste that lean manufacturing defines is defects. This describes the situation where a woodshop makes parts that are either beyond recovery and have to be trashed or else need to be reworked before they can be resold. In the first case, the labor and materials are lost. In the second, more labor (and possibly more material such as sandpaper and other supplies) has to be purchased. The incidence of defects is dramatically lower when a specific employee and a specific work cell are used to manufacture the same parts over and over again. When several people at different workstations are all making the same part in different areas of the shop, the chances of them all being identical are slim and the odds of them all being of high quality also decline.
The bottom line
Very few business are completely aboard the lean manufacturing philosophy, but an increasing number are using elements and even large helpings of the theory to reduce waste, which reduces cost and augments profits. More and more American and Canadian businesses are taking a page from the Japanese book. They are accepting the concept that tweaking small tasks for greater efficiency can add up to large savings. During the last decade, a lot of companies adopted lean concepts to eliminate enough waste so they could survive the recession.
Woodshops that are practicing some variant or measure of lean manufacturing are almost universally using work cells to organize the manufacture of specific parts or groups of parts. The trend is more apparent in larger shops and especially those that supply other woodshops with outsourced components. These work cells are generally set up so that their function can quickly change to produce a different part using the same equipment and skill set. Cells are designed to enhance the uninterrupted flow of work through a shop and to reduce wasted effort, materials and time. They usually capitalize on proximity: keeping things close together — especially in a U-shape that is specifically designed to eliminate wasted walking — can really help with efficiency and allow parts to move from station to station with a minimum of motion.
Work cells are not stagnant. One doesn’t just set them up and walk away, expecting complete efficiency. Each cell must work with the cells in the process that lie before and after it and it must be both self-regulating (switching tasks as needed) and self-improving. The latter is essential: the cell must be designed and maintained in a way that allows both workers and managers to easily see ways that processes can be constantly improved and waste can be reduced or eliminated.
This article originally appeared in the April 2015 issue.
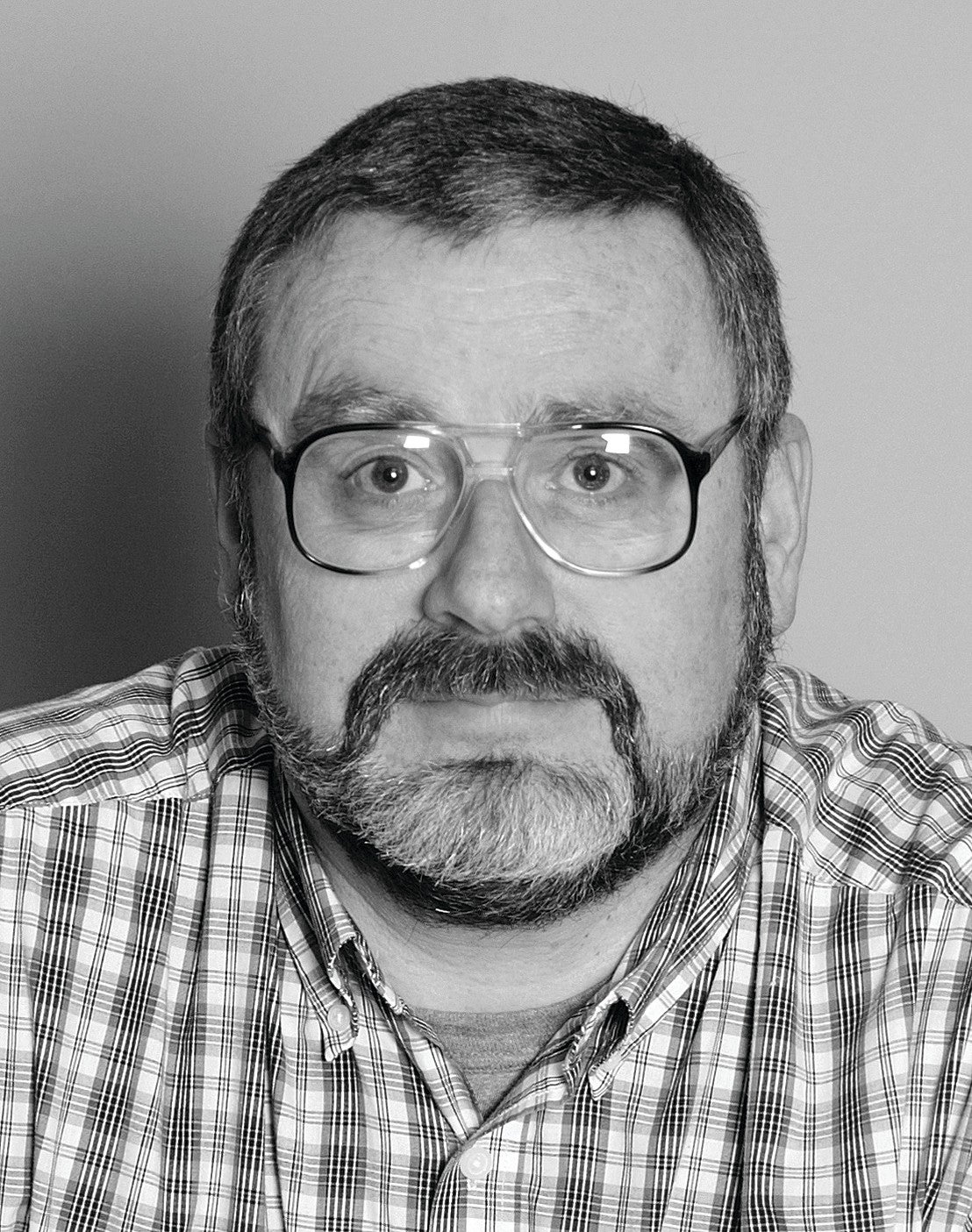