The additive advantage
Since the Industrial Revolution, factories have used a process called subtraction to manufacture precision parts. One starts with something a little larger than the final piece and whittles away at…
Since the Industrial Revolution, factories have used a process called subtraction to manufacture precision parts. One starts with something a little larger than the final piece and whittles away at it with routers, saw blades, grinders, sanders and other abrasive or incisive (cutting) machines, until what’s left is what’s needed.
One problem with that approach is that all those bits and blades get dull, so the last parts made are not always as precise as the first ones. And, of course, there are work stoppages while cutters are sharpened or changed.
Additive manufacturing is a little less wasteful and more precise over time. The process makes a three-dimensional solid object in almost any shape, using a computer-generated model or pattern. The most obvious example of the technology today is the 3-D printer, but the concept can be found in virtually every aspect of manufacturing. Additive manufacturing eliminates a lot of noisy, violent machining and delivers exact parts time after time. On the downside, most additive processes are physically small, because a confined space is required to control the material delivery. That’s changing. Big Area Additive Manufacturing (BAAM), which is basically 3-D printing on steroids, has arrived.
Getting bigger
Since 1959, R&D Magazine has been published for research scientists, engineers and technical staff members at laboratories around the world. The editors describe the publication as “written by scientists, for scientists.” It’s also one key place where the U.S. industrial complex looks to track global trends and to identify important concepts for innovation and growth. In late 2015, the magazine awarded its Editor’s Choice Award to a collaborative effort between Cincinnati Inc. and Oak Ridge National Laboratory for Big Area Additive Manufacturing technology.
While BAAM makes things out of plastic (polymers and composites) rather than wood, its development is a benchmark for almost every other manufacturing process, including wood. A bigger platform means bigger prototypes and larger parts. Instead of using 3-D printers to design small drawer pulls or slides, manufacturers will soon be able to use them to design and build entire casework projects. This is going to revolutionize the way woodshops provide custom solutions for specific niche markets such as hospitals, restaurants and laboratories. We will no longer be confined by the physical attributes of materials, such as plywood dimensions or the bendability of hardwood species. While the actual machines will initially be cost-prohibitive for small shops, the new technology is already somewhat accessible. A woodworker can now design a part in-house and then send the file to an outsourced manufacturer to build it.
And even though some woodshop owners will dismiss the whole concept as far-fetched and futuristic, the birth of BAAM means that the next generation of this technology is actually already with us.
Getting cheaper
Banja Luka is the second-largest city in Bosnia and Herzegovina, smaller only than the capital of Sarajevo. In June 2015, the University of Banja Luka hosted an international conference on engineering, where professor Milan Sljivic presented a paper on behalf of the mechanical engineering faculty. In it, he discussed cost optimization of additive manufacturing in the wood industry. Basically, he was comparing new additive technology to the subtractive CNC technology we now employ. He was looking at how much it costs to make parts with each process and the material used in the study consisted of 40 percent recycled wood and 60 percent polymer bonding.
Some of the findings in the paper are insightful. For example, many additive processes can now use free software for 3-D modeling to reduce cost and, because the operator of the machine is often the designer as well, labor costs are minimized. The speed of the process is increasing rapidly as more and more machine builders enter the market and competition engenders higher standards. The same is true of both accuracy and overall quality.
When it came to a comparison of the investment in building the same part on a CNC and a 3-D printer, the lab compared cost, time and results. Depending on the dimensions of a part being made, additive manufacturing had a few significant advantages over the subtractive process. One of these was that a woodshop might theoretically make thinner parts that are stronger, which could have a significant impact on our industry. Thinner parts use less material so they’re cheaper, but they can also radically change design decisions. Going thinner is possible not only because the wood/polymer option is physically more rugged than wood alone — especially in compression (along the grain), although not so much in shear (across the grain), but also because reinforcement can be built right into an additive part during the build. One could even add steel (think skinny rebar) that would completely eliminate any disadvantage in shear strength. A cabinet component, for example, could be made strong enough to carry a weighty countertop such as granite and yet be very thin. This opens up a whole new world of aesthetic possibilities.
The additive technology process that is analyzed in the Banja Luka University paper is based on fused deposition modeling, or FDM. Various materials (wood and plastic) are “fused” together as they are deposited to build a part. The study concluded that the new technology is still “at the border of profitability,” but it’s obviously moving very rapidly toward economic viability. Sljivic says that 3-D printing exhibits a great advantage, especially for prototyping, and it is already cost-effective for many small production runs:
“Traditional technologies need extremely expensive tools and, for production of a small number of parts, 3-D printing is a good choice. In the future, a significant decrease in the prices of printers can be expected, leading to a significant increase in FDM technology.”
Getting creative
Just north of Seattle, a revolution is taking place in the woodshop world. A highly innovative and creative company called 4AXYZ is already using additive technology to produce wood products. It’s an effort that is being led by the company’s CEO Samir Shah, who is an architect, designer and longtime consultant to the woodworking industry. He and his team have developed what they call Stratified Additive Manufacturing, which is a process that allows the company to “build” wood into myriad shapes and usable forms. The system is modular in that it uses several machines. Each one is capable of making various forms, shapes and products, either separately or simultaneously. The finished product is usually ready within 15 days.
Getting replaced
What is significant is that additive technologies are no longer being considered within the confines of creating prototypes. They are now on the cusp of being used to manufacture actual product on production lines. One factor that facilitates this is the same concept that makes CNC so attractive to woodshops: program it and walk away. While the machine does the basic legwork, the woodworker can be doing other more creative tasks such as planning, designing and installing. In a couple of decades, even moderately-sized custom woodshops will look a lot like a modern day auto: banks of robots cutting the straight parts and assembling them, while 3-D printers use wood composites to make anything with a curve or a challenge. Additive technology can also embed electronics, sensors and conductive metals inside wood parts — 4AXYZ is already doing this. The company invites us to imagine building wood windows that are controlled by a thermostat linked to a phone app or walls that can sense and automatically zap fungus growing inside the cavity.
Woodworkers’ skill sets are going to change rapidly in the very near future. During the last few decades, we’ve gone from physically pulling a radial arm saw to programming CNC routers. Now we are going to become ever more proficient at design. Our days will be spent using our knowledge of species, movement, color and grain to be more creative, returning in a way to an era where woodworking was more art than craft. During the next two decades, we are going to leave more and more of the repetitive tasks to machines.
This article originally appeared in the March 2016 issue.
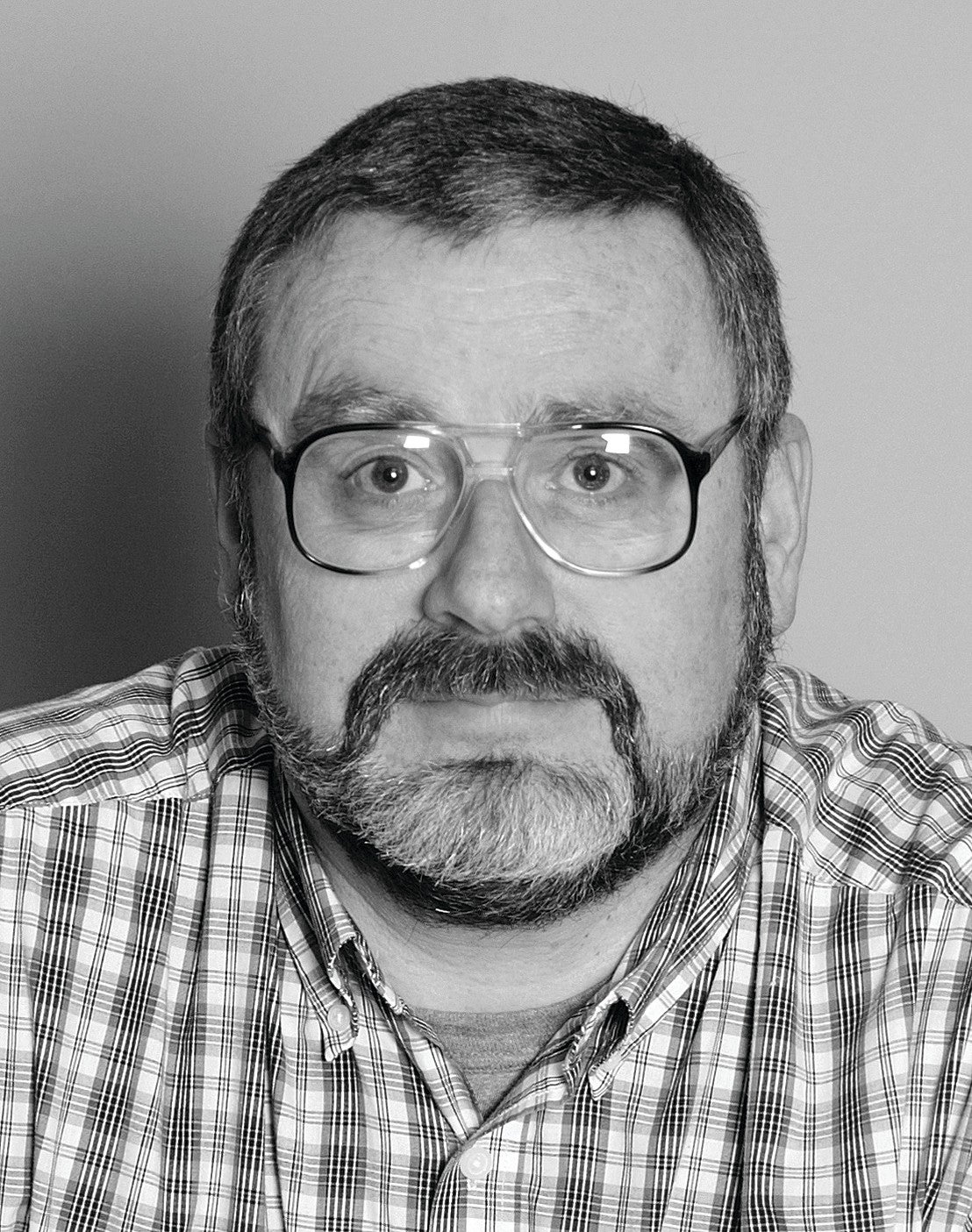