The 2017 Wood Market Report
Everybody in construction knows that framing lumber prices are up more than 20 percent over a year ago, and the rebuilding effort after California’s fires and some major hurricanes will only strengthen that market over the next year.
Everybody in construction knows that framing lumber prices are up more than 20 percent over a year ago, and the rebuilding effort after California’s fires and some major hurricanes will only strengthen that market over the next year. But supply will probably lag, at least for sheet goods and softwoods, as mills and processing plants continue to find it difficult and often impossible to hire skilled people. The politics of Canadian and Chinese imports are creating big waves in the wood market, too.
There’s a lot happening.
Trends and technology
One aspect of the wood market worth noting is the ongoing technical convergence of the softwood and hardwood sectors. Historically, there was a conception that softwoods were construction-related while hardwoods were more confined to casework and trim. However, woodshops are seeing design trends continue to move from solid hardwoods to paint-grade and melamine finishes, much of which are built upon a softwood core. That’s having an effect on demand for softwood products, a sector that is currently seeing high levels of Chinese imports. What happens with pine will also impact the bottom line of casework builders because so much sheet stock depends on conifers for its core.
Technologies are also affecting the wood market. For example, the phrase “plywood on steroids” is a catchy nickname for cross-laminated timber (CLT) that is being used instead of concrete and steel to build commercial buildings.
“Cross-laminated timber is a large-scale, prefabricated, solid engineered wood panel,” according to the Engineered Panel Association. “Lightweight yet very strong, with superior acoustic, fire, seismic, and thermal performance, CLT is also fast and easy to install, generating almost no waste onsite. CLT offers design flexibility and low environmental impacts.”
Proponents of CLT also point out that it has a much lower carbon footprint than many traditional building materials and will create manufacturing jobs, particularly in the Northwest. That bodes well for a regional industry that has been dealing with a number of challenges of late, from Chinese imports to labor shortages and even wildfires. And those problems are not confined to the Northwest, as woodshops all across the country use core and sheet stock that is manufactured from both softwoods and hardwoods.
Industry predictions
Despite any air of uncertainty, most industry specific publications post an upbeat picture of the hardwoods sector, and their take is based in part on trends in the broader construction industry.
There’s no denying that cabinetmaking, flooring, millwork and furniture building are intricately related to how many houses are being built, so that has historically been a pretty decent barometer. Unfortunately, housing starts aren’t quite as healthy as they were a year ago, and that’s definitely something worth watching. The numbers are published around the middle of each month by the U.S. Commerce Department, and the October 2017 report revealed that building permits in September for privately owned housing units were down 4.5 percent over August, and 4.3 percent from September 2016. Permits reflect the short-term future picture. A more immediate view is that actual physical starts were down 4.7 percent from August. However, they were actually up 6.1 percent from a year ago, which is encouraging. And completed projects were up an impressive 10.3 percent over a year ago.
Taken together, the numbers suggest that construction is up over last year, but slowing.
Cranes in the air
Timber Products (timberproducts.com) in Springfield, Ore., owns 114,800 acres of forestland in northern California, which is managed under the strict standards of the Sustainable Forestry Initiative and Forest Stewardship Council programs. Timber Products also operates 10 manufacturing facilities across the country, and specializes in hardwood plywood and wood panels with decorative overlays. The company offers a wide variety of wood products from veneer to ultra-light MDF and particleboard.
“Fires haven’t directly impacted our operations but of course there has been an effect on the price and supply of logs. And that has impacted prices regionally,” Rick Montoya, the company’s vice president of sales and marketing, said in an interview with Woodshop News. “But one of the bigger domestic challenges is the continued growth of Chinese imports of wood products.”
Montoya isn’t alone in his concerns. According to the Hardwood Plywood & Veneer Association, Chinese hardwood plywood imports surged from $54 million in 2001 to nearly $1.1 billion in 2016. The U.S. International Trade Commission is considering whether or not to impose massive duties on Chinese hardwood plywood imports, opposed by the Alliance for Hardwood Plywood (see story, Page 8), an organization of American importers, distributors and manufacturers of hardwood plywood.
Montoya also noted that he sees more softwoods being used in the cabinet and furniture industries, especially in a retro design trend that includes a rustic look. He added that changing demographics in the U.S. and the aging of the Baby Boomers has led to a healthy uptick in recreational vehicle sales. That in turn has increased demand for decorative and veneer panels from companies such as Timber Products.
Another change he sees is the continuing trend toward outsourcing, where many smaller shops are concentrating on design and installation, rather than component building. And an increase in the use of melamine products has also led to less onsite finishing. Robotics are becoming ever more important in the handling and conveyance of sheet stock in manufacturing plants, and he sees this trend as one major component in the wood industry’s response to a shortage of highly skilled workers.
Montoya is also quite encouraged by the realization within the industry that there is an immediate need to train technicians, and he pointed to the opening of the new Manufacturing Industry Learning Lab in Colorado Springs, Colo. (see story, Page 30).
All in all, Montoya is optimistic about 2018, while reserving judgment on 2019 and beyond. His work involves extensive travel, and he says he is encourages by all the “cranes in the air” that he sees all across the country.
HARD TO PREDICT
“Here in the Northeast, I’ve noticed a lot of inconsistency in the demand for lumber from month to month, quarter to quarter,” says Rick Lang, president of Highland Hardwoods in Brentwood, N.H. “What is most perplexing is putting your finger on the reason why. After the economy collapsed around 2008, things were pretty flat for several years. Unlike past recessions, this time there was there was no bounce-back recovery. The market just eventually stabilized, and then ever so slowly moved forward.
“What we’re seeing now is that high-end construction is strong, both residential and commercial, and especially along the seacoast region, around Boston and Cape Cod. There’s also a pretty strong renovation market that we are benefitting from, where homeowners are improving homes by installing hardwood flooring, fixtures and other millwork upgrades. We did see a bit of a drop-off last fall right after the presidential election, when there were levels of uncertainty in the air.
“How well we do as a supplier of hardwoods is based on how well our customers are doing. Over the last few years, the market has been fast for a while, and then has slowed down for a time – there hasn’t been a lot of consistency. And the challenge for us, and also for our woodworking customers, which include cabinet shops, furniture builders and flooring installers, is this: How do you plan for a two- or three-month decline that you don’t see coming? It’s hard to figure out why there are bumps, so it’s hard to predict trends. Some of that has to do with the way the market has changed over the last few decades. We now feel global effects regionally, more than we used to, and more immediately, too.
“It’s important to add that one of the biggest challenges of all is being able to hire qualified people. The shortage of skilled labor affects us because it’s holding back our customers as well. When our customers are short on good people, they end up with more work than they can handle. And I think one aspect of that shortage is the physical requirements. A job where physical work is involved is less appealing to many people who can find an easier way to make a living and do so at the same or higher pay. That, too, can vary regionally. And that factor is preventing many companies from growing and developing their potential.”
CONSIDER THE SOURCE
Scott Roberts, owner of Roberts Plywood in Deer Park, N.Y., says he isn’t having any trouble recruiting skilled workers. Most of his crew has been with the company for more than a dozen years. But he, too, is catering to a busy construction sector, both residential and commercial, and among the hotter species right now are walnut and white oak.
“Woodshops are using white oak in every format,” he says. “They’re buying every grade from clear to knotty, and every cut from rift to quarter and plain. It is being used in cabinets, stairs, trim and flooring – most in contemporary design, and there’s a slight throwback to Stickley, too. Much of it is being bleached and wire brushed, and the coatings are a gray or fumed look.”
When asked about the ITC hearings on Chinese plywood imports, Roberts very firmly stated that he never buys anything from the Chinese.
“They are undermining North American mills on price because they use illegal Russian logs, don’t pay workers a fair wage, and they have very lax laws on safety and environmental issues. They are aggressively buying logs in the U.S. and Canada, and not just sawn lumber and veneer. That’s threatening jobs in our mills, and many have already closed their doors.”
Woodworkers interested in where certain species come from, and how they are harvested, might like to visit the International Tropical Timber Organization (itto.int), an intergovernmental organization promoting the conservation and sustainable management, use and trade of tropical forest resources. Its members represent about 80 percent of the world’s tropical forests and 90 percent of the global tropical timber trade.
Another resource, the International Wood products Association (iwpawood.org), believes in properly supporting the legal and sustainable harvesting of international wood products. By building understanding and demand in North America for globally sourced wood products, the association says it is “supporting sustainably managed forests and local economies throughout the world, while supporting jobs and industry in North America.”
This article originally appeared in the December 2017 issue.
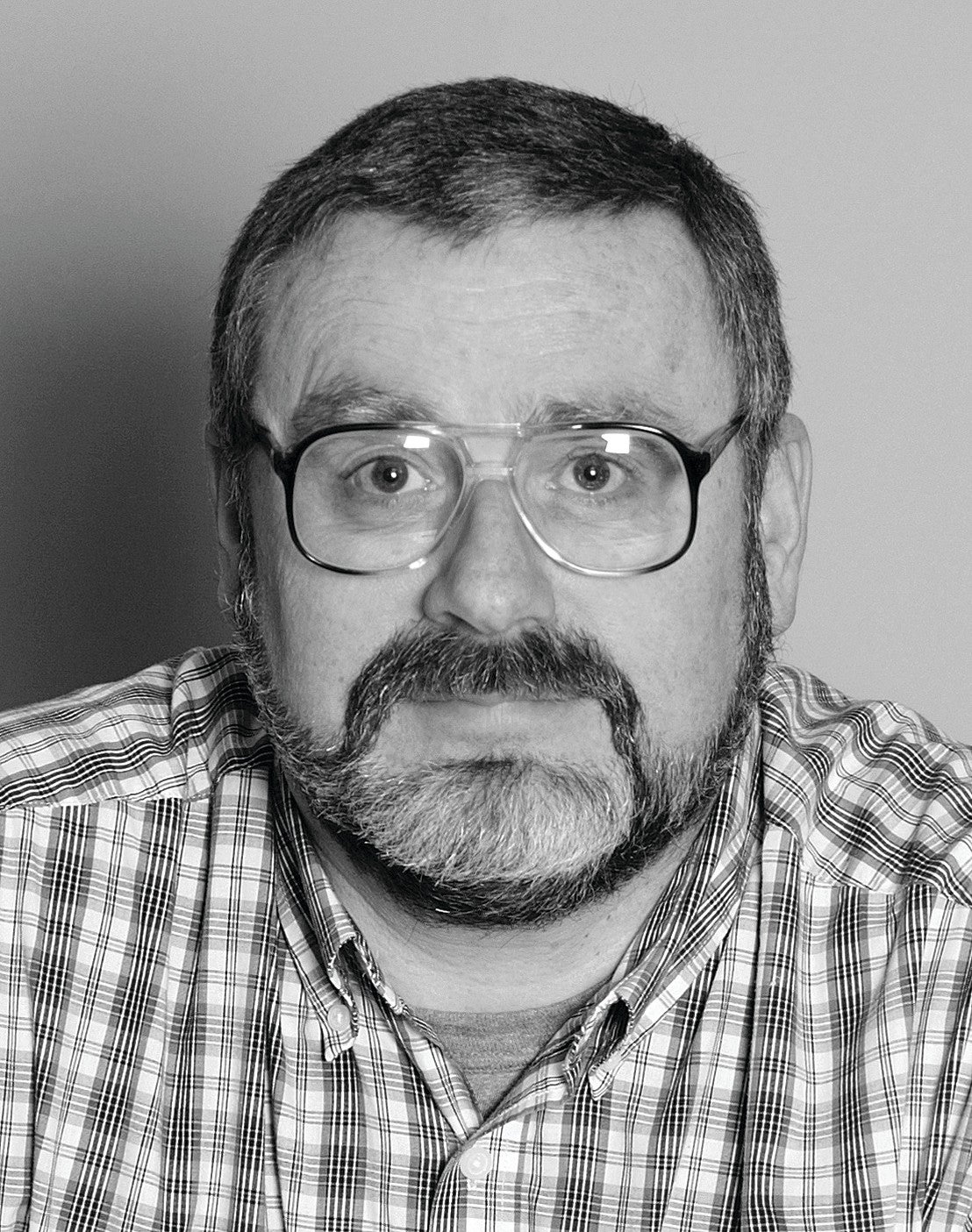