Stick to a schedule
Sharp tools and well-tuned machinery makes for a safer and more profitable shop.
Tools are expensive, but tools that don’t do their job well are very expensive. They cut slower, create lots of re-work and touch-ups, and even present some dangers. Basic maintenance can go a long way toward eliminating those negative effects.
Almost every tool in a woodshop will benefit from occasional cleaning with a pitch and resin remover. This liquid or aerosol solution can be used on bits, blades, tables, bearing guides, splitters, riving knives, even zero clearance inserts. Proper dust collection is another key aspect of tool maintenance, not only for your own well-being but also for the longevity of honed edges. Without it, we’re often asking tools to cut the same material more than once. And guide bearings on router bits and shaper cutters need to be occasionally cleaned and lubed. There are slip lubes for tables that don’t contaminate wood or cause finishing problems, and special treatments for V-belts that prevent slipping. Replacing some V-belts with segmented link belts can also reduce vibration and drag, both of which can help tools and edges last longer.
All this maintenance can be organized into three loose categories – hand tools such as chisels and planes; dimensioning tools that include saw blades and planer knives; and milling or profiling tools such as router bits, shaper cutters and CNC tooling.
Hand tools
On a recent fall afternoon, Ken Froelich watched as his shop cat, Trip, stretched languidly across his workbench. The man is surrounded by hand tools, and I swear both he and the cat were purring.
Froelich, a furniture artist and master craftsman, thinks he knows why so many shop aprons have empty tool pockets nowadays. It’s not just because machines are more efficient, but also because woodworkers no longer feel that they have the time to invest in sharpening.
No matter how much Industry 4.0 seeps into woodshops, Froelich maintains that there will always be a need for a few hand tools. He also notes that woodworkers who know how to sharpen and maintain tools always seem to accumulate – and use – more of them. Even those who show little respect for manual methods will usually have at least a block plane and a few bench chisels lying lazy in a drawer somewhere. Froelich thinks it’s time to drag them out and tune them up. His point is there’s not really all that much to their maintenance. It takes a little time to sharpen and tune tools, but the payoff is that it usually takes a lot less time to bring a sharp hand tool to the workpiece than it does to carry the part to a machine and process it. That’s because there are so many steps in machining such as setting fences, locking in the depth of cut, hooking up the dust collector, running the board through and perhaps making more adjustments before bringing it back to the bench.
Time saved isn’t the only benefit, according to Froelich. Breaking an edge with a freshly sharpened block plane is definitely more satisfying than using sandpaper. It’s also more accurate and controllable. The resulting tiny chamfer looks so much more professional than a crude round-over that was gouged by garnet.
Sharp tools are safer, smoother, faster and more enjoyable. And sharpening is no longer the chore that it was back when Ken (who is currently enjoying his ninth decade) learned his trade. For establishing a primary bevel, a slow-speed bench grinder (available from companies such as Rikon and Grizzly) that’s equipped with a Norton white wheel is a good combination for minimizing heat. And for honing a secondary bevel, there’s an inexpensive solution from Rockler called the plate glass system (item GRP5983_2).
If you’re doing some serious hand tool work, then take a look at Tormek (tormek.com/usa/en). This slow-speed and highly accurate Swedish system will not just tackle bench tools, it will also work for many machine knives and blades.
The bottom line here is that there are all kinds of jigs and machines available for sharpening, so the guiding principle is to find one that keeps tools cool as it grinds. Woodturning forums are great places to pick up brand recommendations, because turners need to sharpen constantly. That means they’ll know the options for sharpening hand tools better than most machine-biased woodworkers will.
Dimensioning tools
The first step in maintaining tools for ripping, cross-cutting, thicknessing and dressing is to invest properly and buy the best. These knives and blades can last an incredibly long time if they are built with the right quality carbide and steel. Upgrading to industrial saw blades from top grade manufacturers such as Forrest, Carbide Processors, Total Saw Solutions or Freud can elevate both the processes and products of a woodshop. These blades can handle more work, more sharpening and more heat than mass market versions. And when they do eventually go dull or have damage to a tip, most of these industrial manufacturers offer service and sharpening that meets the original factory specs.
A well-tuned and adjusted machine will help tools and blades last longer. Improperly aligned tables and fences make the knife or blade work harder, burn hotter, and wear unevenly. They’re also unsafe. High quality aftermarket fences can upgrade a contractor saw to a thing of beauty. The factory fences and miter gauges on these machines often feel like an afterthought, while the table, motor, shaft and trunnions are all quite acceptable. Adding a highly accurate and reliable fence can really improve their performance. Some brands worth exploring are Vega, Incra Precision Tools, VerySuperCool Tools, Delta and Shop Fox. When it comes to miter gauges, Brad Witt’s Woodhaven makes a dandy version, too.
Blade stabilizers can reduce wobble in thin-kerf blades. These are essentially giant washers that are slipped onto the shaft on either face of the blade, adding an element of sturdiness.
Knives can often be sharpened in-house, and sometimes even while they’re still on the machine. For example, several manufacturers such as Wood River (Woodcraft) make aluminum oxide hones for touching up jointer knives without removing them. And if the long, flat knives from jointers or planers need to be sharpened off the machine, that’s also pretty easy to do in-house.
After removing them, degrease them with an industrial aerosol. Then use any of dozens of jigs from manufacturers such as Grizzly or Rockler to touch up the bevels. Woodworkers who like to make simple shop jigs will enjoy an article on the Paoson Woodworking website (paoson.com) that outlines a simple wooden jig used to sharpen planer knives.
Band saw blades are rarely worth sharpening, either in-house or sent out. Once again, the key here is to buy the best blades your budget will allow. Adding aftermarket blade guides can seriously upgrade the performance of many small- and medium-sized band saws. If possible, try to stay away from using band saws to cut solid surface materials. It initially feels like they’re cutting through butter, but the blade dulls quickly and won’t follow a straight line afterwards when you try to cut wood. If it’s an option, use a router to machine these materials.
Many models of band saw can be retrofitted with a wheel brush that removes sawdust build-up from the tires. And those tires tend to wear out, too. Some of the new aftermarket replacement tires are easy to change out and can really help tracking.
Profiling tools
While sharpening saw blades in-house doesn’t usually pay for itself (all those tips can take a long time to process properly), woodshops that profile a large volume of manmade sheet stock such as multiply or MDF might want to look into in-house sharpening of router bits. Here, the concern is usually just two to four faces rather than dozens of tips as it is with a saw blade. The core requirements of an accurate sharpening system are a diamond-tipped cone and a vise that holds the bit at the correct angle. Once set up for a specific bit, workers on the production line can usually touch up a handful of bits in a few minutes. The resulting fine dust would need to be evacuated properly.
Another approach is to purchase tooling with carbide insert cutters that can be rotated or replaced as they become dull. Shop owners are often surprised by the discounts offered on bulk quantities of inserts. And they’ll sometimes find that several different tools can share the same size insert.
Standard twist drill bits can be sharpened many times in-house using an inexpensive benchtop sharpener such as the Drill Doctor models or grinding guides from companies such as General Tools that hold the bit at the correct angle for a grindstone.
The internal cutting bevels on a Forstner bit can be honed, but one shouldn’t touch up the exterior edge as this will alter the dimensions of the hole being drilled, and possibly take the bit out of round. Run a mile from inexpensive Forstner bits – they’ll burn and wander and ruin your day.
If a Forstner bit needs to be used in a portable drill (most manufacturers recommend only using them in a drill press), it’s a good idea to drill through a piece of 3/8” plywood first, and then align that with the hole to be drilled in the workpiece. Clamp it in place and use the plywood as a jig that will guide the bit and prevent wandering.
It’s hard to remember to perform maintenance tasks. One solution is to mark a day on the calendar every three months as the seasons change and spend eight hours doing nothing but tuning and sharpening.
Such a regimen can be as relaxing as watching a cat stretch on a workbench.
John English is the author of “Woodworker’s Guide to Sharpening” and “Bench Planes & Scrapers”, both of which are available from www.woodworkerslibrary.com (item Nos. 14-509 and 14-511).
This article originally appeared in the December 2019 issue.
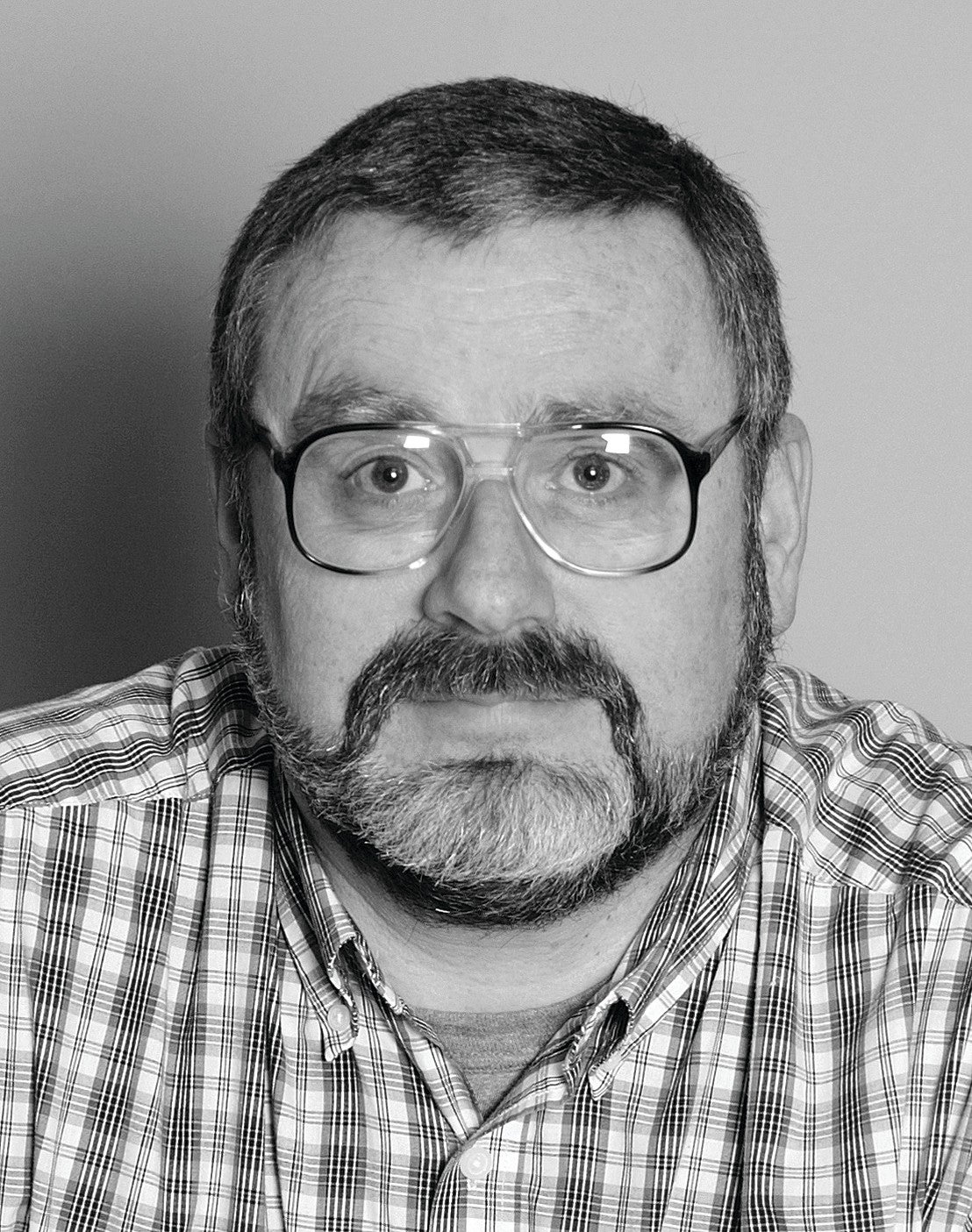