Something in the air
There will always be debate about whether a hand-applied finish or a sprayed one is better and there are advantages and disadvantages to both. As the volume of work in…
There will always be debate about whether a hand-applied finish or a sprayed one is better and there are advantages and disadvantages to both. As the volume of work in a shop increases, woodworkers tend to lean more toward the speed of sprayed coatings over the personal experience of rubbing on oil or shellac, or even brushing lacquer and varnishes. If you’re switching from pads or brushes to spraying, here are a few notes that could help with finishing equipment choices.
Almost every woodworker has used a spray gun at some time. While guns are generally not too expensive, there are a lot of different types and systems available, so it helps to understand their function.
Spray gun tips are designed to atomize liquid finish. That is, they reduce the liquid to very small droplets that are light enough to become airborne. In most systems, pressurized air flows through a hose from a compressor into a channel inside the gun. The air gains velocity as it exits through the tip, because the orifice (opening) is smaller than the channel. Changing the tip to one with different-sized holes or holes in slightly different locations can change the pattern of the air as it escapes. That in turn changes the shape and/or volume of vaporized finish being delivered to the surface.
Traditional spray guns are not very efficient. Roughly three-fourths of the finish ends up in places other than on the furniture or cabinet. That can change depending on how experienced the operator is and on the equipment he or she is using, but by and large three-fourths is a good rule of thumb. The problem with traditional systems is this: if the flow of finish is delivered in a small, efficient pattern, it is traveling so fast and with such force that it doesn’t lay down gently on the surface: it pools, flows and dams, causing runs and uneven patches. When the spray pattern is enlarged to reduce the pressure (same volume, bigger area), most of the droplets in the pattern are delivered outside the target. They either overshoot or fall short. They also contaminate the air, so the booth’s fan has to evacuate huge amounts of preheated or cooled air to the outside. Depending on the season of the year and the shop’s location, this can be expensive and it is not very environmentally sound.
An industry-wide move toward water-based finishes has helped dramatically with environmental issues, but a new type of delivery system has also revolutionized the way we spray.
HVLP and conversion guns
Most small- to medium-sized woodshops have switched to HVLP turbines during the last couple of decades. Very large shops use expensive, fully automated systems to apply and dry the finish almost instantly. But most shops are still spraying by hand and they have embraced HVLP technology. The acronym stands for High Volume, Low Pressure. These machines deliver a lot of vaporized finish, but the air carrying them isn’t moving as fast or as aggressively as the stream delivered by traditional guns.
The core of the system is a self-contained air pump or turbine. Most of these run on household (110-volt) current, so wiring isn’t an issue. Unfortunately, these small units don’t have a lot of power, so they can experience resistance when trying to spray thicker, heavier fluids. Thinning, and subsequently the need to apply more coats, is routine.
A newer arrival on the scene is a bit of a mongrel: it combines aspects of the old standard guns and the newer HVLP systems. Known as a conversion gun, it has the power to spray thick and thin finishes because it uses compressed air rather than a small electric turbine. The gun is modified to convert high-pressure, compressed air into high volume, low-pressure air. So it delivers a gentle pattern with a lot of finish on board. But there is one drawback. For larger jobs such as casework, you’ll need to have a fairly sizeable compressor with a large storage tank to keep up with the amount of air it uses. If you already own one, then this is probably the best way to go for most shops.
When shopping, you’ll notice that the guns are configured in a number of ways. Some have a hopper on the top and this feeds the finish to the tip by gravity. The weight of the fluid pushes finish through the bottom of the hopper into the airflow. Other guns have a bottle attached to the bottom and this uses pressure to force-finish up a tube into the air flow. And a third version uses a hose attached to a regular drum of finish or a special drum that incorporates a pump. Hoppers and bottles use small amounts of product (the typical hopper capacity is about the size of a large coffee at a gas station), primarily because the operator would experience fatigue if he/she had to hold up a lot of weight for a long time. The logic here is that 15 or so fluid ounces will actually go a long way on most spray jobs, so the hopper only needs to be topped up a couple of times. However, the hose arrangement allows non-stop spraying of an entire project and probably with less fatigue — although those hoses can get heavy, too. The disadvantage is that two hoses aren’t as flexible as one, so movement is somewhat curtailed. But an open-topped hopper imposes limitations on physical movement, too.
The size and number of jobs a shop processes has a lot to do with which system works best.
Booths
There are lots of reasons to hesitate when thinking about installing a finishing spray booth. Among them are explosion-proof fans and city permits, insurance premiums and fire exposure. But the advantages of having an in-house booth are considerable, especially in terms of time spent finishing, but also when it comes to quality. A well-sprayed finish is both durable and beautiful. And by not shopping out the finishing, at least one employee is going to become pretty good at spraying. That can be a real boon when it comes to warranty and repair work.
The booth itself doesn’t have to cost a fortune: there are some quite affordable versions on the market. For example, Grizzly’s G0532 open-face spray booth is under $2,000. And paint-booths.com has 16 models on its woodworking page, starting with an 8’ x 7’ x 6’-5” deep unit at $2,899.
There are several configurations for booths. Some vent out the back, others through the roof, and some pump air out while others pump air in. That is, some systems (downdraft) increase the air pressure inside the booth and the only way it can escape is through an exhaust duct, while other booths (cross flow) suck air out of the booth, creating a vacuum that is made up when shop air flows into the booth through filters, usually in the walls or doors. An open-faced booth would be categorized as cross flow.
If a woodshop wanted to build a booth from scratch, the Carl J. Busch Co. in Rochester Hills, Mich. (www.carljbushcompany.com) sells explosion-proof paint booth extraction fans.
Make-up air is a big issue, especially in smaller buildings. When a fan expels a couple of thousand cubic feet of exhaust through the wall, that’s the equivalent of all the air in an average office leaving the building every minute. It doesn’t take long to cool down a shop with that kind of air flow. A designated make-up air heater (one source is Grainger) can run two or three times the price of the spray booth, so it might be less expensive to add an auxiliary furnace if there is going to be a lot of spraying. Check with a licensed HVAC contractor who will know local regulations and will be able to assess any potential dangers.
The loss of treated air can be mitigated somewhat if spraying is done on warmer days in cold climates or in the evenings in places where air conditioning is an issue.
An alternative to installing a booth is to make arrangements with a local body shop to rent its booth by the hour. This seems to work better when the woodshop brings its own equipment (perhaps an HVLP turbine and guns), so cleanup or damage/wear-and-tear don’t become issues. If the cabinet spray job is started at the end of the normal business day, the woodshop crew won’t be in the body-shop workers’ way. Plus, any finishes that need time to cure can stay there overnight and get picked up in the morning. Renting a neighborhood booth can be a good way to learn what works best for the types of jobs being sprayed, before the woodshop invests in buying or building a booth.
One last thought: there is a learning curve associated with spraying. With that in mind, this might be a good time to build some shop storage cabinets or perhaps a new showroom display, rather than experimenting on a client’s expensive kitchen.
This article originally appeared in the March 2015 issue.
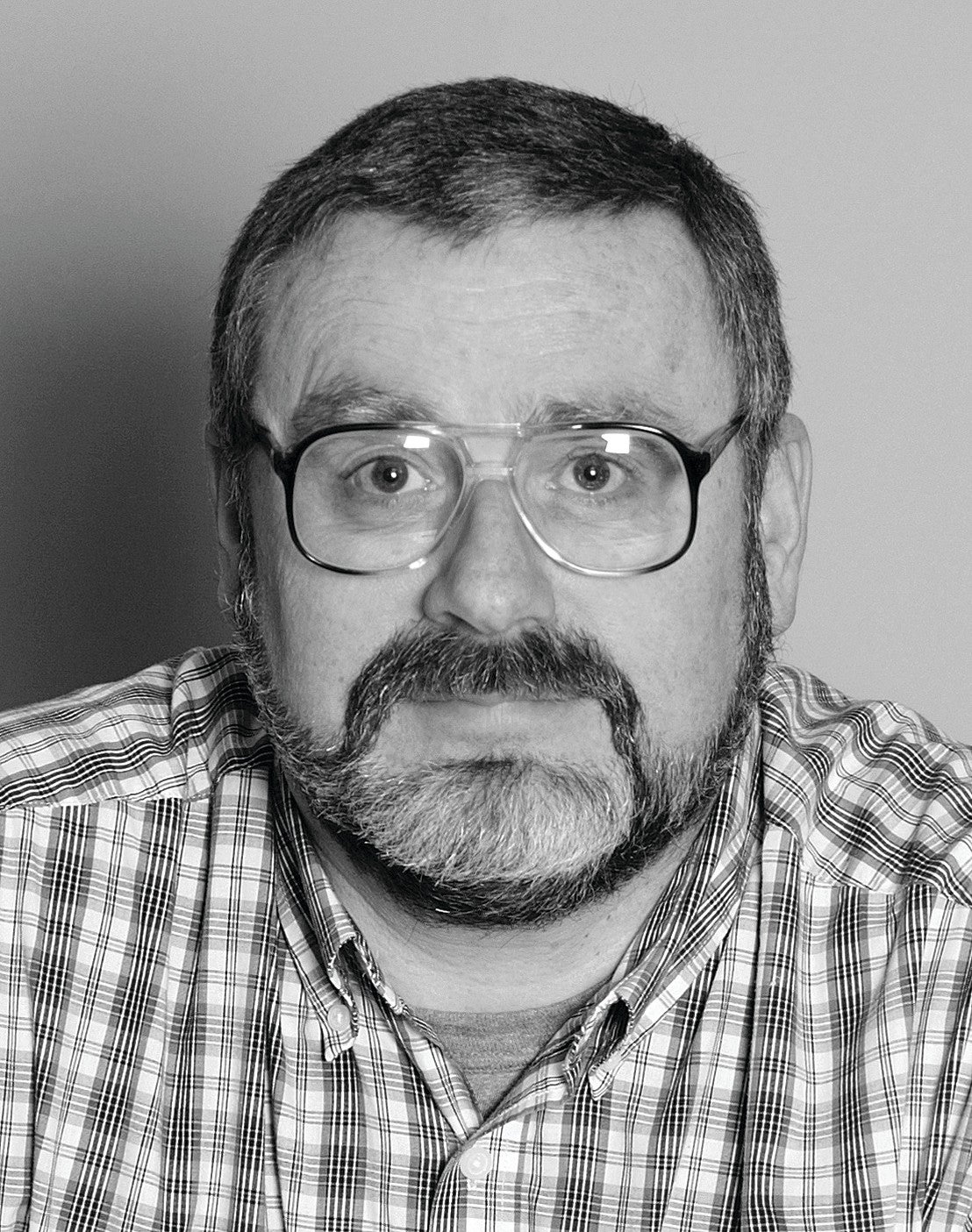