Ready to use
While many woodshops use prefinished hardwood veneered panels to cut down on construction time, there has been resistance among others to jump aboard because of a belief that the coating will scratch in transit or use, and also because of an impression that the choices are limited to a clear UV on natural veneer.
While many woodshops use prefinished hardwood veneered panels to cut down on construction time, there has been resistance among others to jump aboard because of a belief that the coating will scratch in transit or use, and also because of an impression that the choices are limited to a clear UV on natural veneer. Here, as in almost every aspect of the wood industry, technological norms are changing those preconceived notions.
Prefinished panels have been around a long time, and today the term has become a little more fluid and all-embracing. Many panels, for example, are not so much ‘finished’ as they are ‘ready to use’. There are still lots of suppliers who manufacture a coated wood veneer panel, and the quality of the topcoat has improved dramatically over the past few years. Shops have traditionally just used them for low wear surfaces such as cabinet interiors, drawer parts and sometimes shelves. But given that over half of the new cabinets being built today are non-woodgrain, shops also need to know about options for high wear surfaces that involve printing wood patterns, or powder-coated MDF, or even pre-applied plastics.
Real wood options
In its literature and online resources, Timber Products Co. (timberproducts.com) makes a very good case for prefinished panels. The company notes that its ultraviolet curing technology on natural woodgrain panels is one of the most environmentally conscious ways to finish a product. UV curing contains no formaldehyde and no harmful volatile organic compounds. Plus, the overall cost for UV-cured panels is well below traditionally applied coatings.
Timber Products’ flat line process helps reduce waste by allowing excess finish to be recycled and reapplied. That keeps the purchase cost for a woodshop in check. And the shops also experience direct cost advantages after purchasing because of improved in-house production times, lower spray equipment and inventory requirements, and the fact that some employees are now freed up to focus on specializing in other areas of production rather than finishing such as design, machining and assembly. As evidence of the way the industry is moving, Timber Products’ Sierra division (sierrafp.com) carries an extensive assortment of hardwood plywood and composite panels including MDF, LVL and PB, plus decorative surfaces including TFL, HPL, veneer and FRP options. Its prefinished hardwood panels meet AWI, KCMA and miscellaneous ANSI standards.
Columbia Forest Products (columbiaforestproducts) makes a prefinished product called the FinishLine, a hardwood plywood with four coating options designed to save fabricators time and money on cabinetry component; UV Wood with a durable, VOC-free, UV-cured, clear topcoat, and FirstStep, a pre-primed panel.
Richwood Industries (richwoodind.com) distributes domestic, pre-finished, UV-coated veneer core plywood in 1/4”, 7/16” and 1/2” stock thicknesses (custom sizes are available), and with a variety of face grade veneers. The company also makes UV-cured doweled or dovetailed drawers.
Pre-finished Nova panels from States Industries (statesind.com) are used primarily on interior vertical surfaces such as cabinets, closets, fixtures and architectural interiors, particularly where finish consistency across a large number of panels is important. The company’s Nova Peak line is pre-stained and finished, and Nova Lab is a laboratory grade prefinished panel. States also offers prefinished and edge banded components.
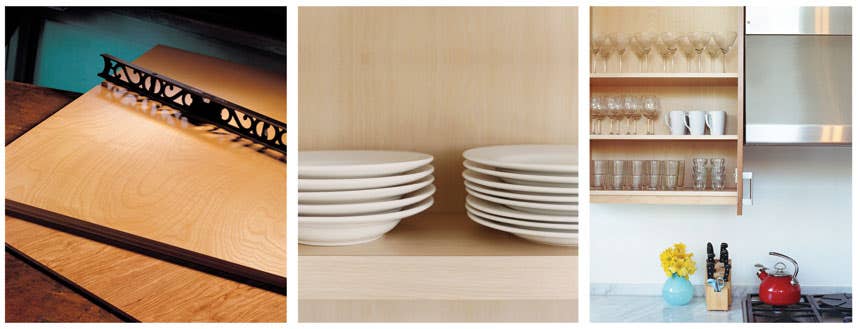
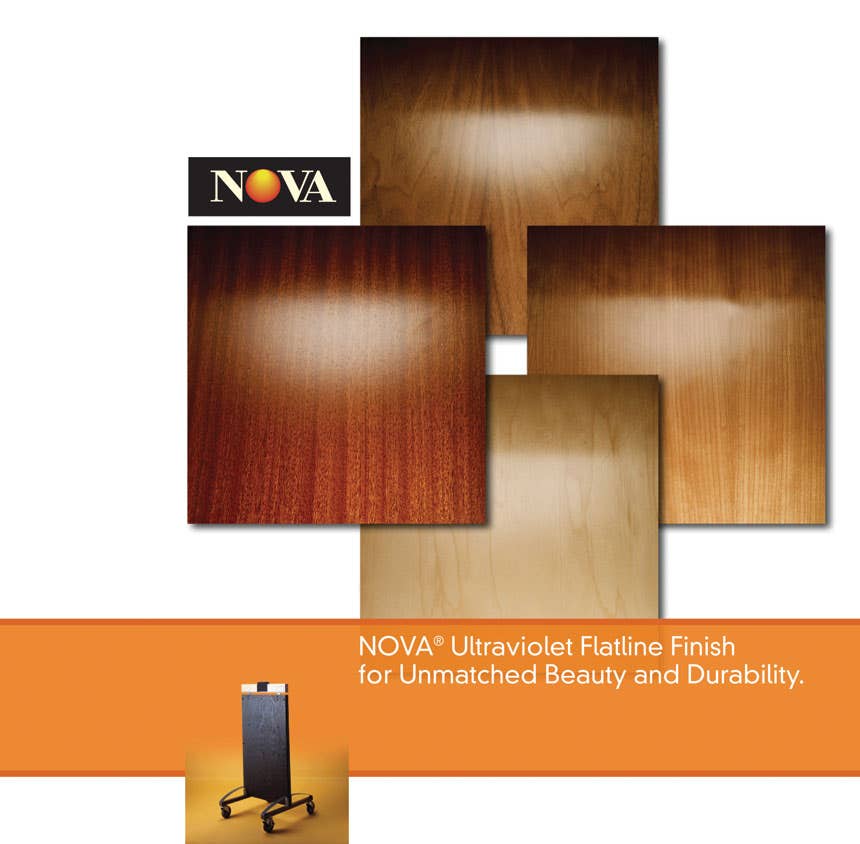
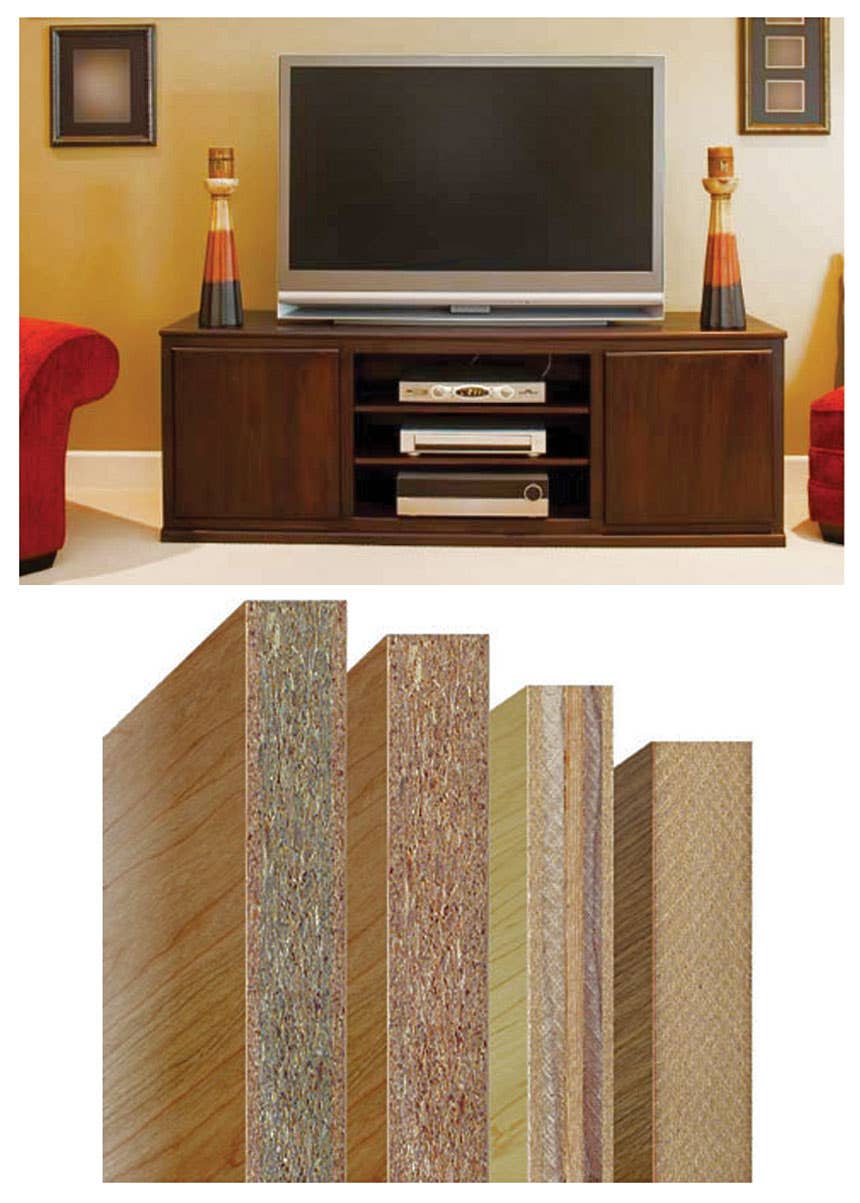
Murphy Plywood (murphyplywood.com) offers PermaGuard UV clear top-coating for the panels that it manufactures, and the company says it’s more durable than catalyzed coatings. Murphy also has the ability to apply transparent or solid color stains, sealers, primers, toner and water-based colors to wood panels. The company has a commercial spectrometer and software system in place for color matching.
Some pre-finishes aren’t simply clear coats. North American Plywood (naply.com) makes DesignPly, which uses digital staining technology to print veneer grains, stains, and graphics onto substrates such as plywood, MDF and particleboard. Robots and a huge inkjet printer make quick work of the process. And Indiana Architectural Plywood (iaplywood.com) manufactures uniquely sized architectural panels that can be ordered pre-finished and machined. They are used for blueprint matched applications that range from wall systems and doors to furniture components, inlaid conference table tops and even aircraft interiors.
For large volume buyers, the Spanish company Garnica (garnica.one/en) offers UV varnishes, high pressure laminate, and a panel called Prime that is coated with a water-based acrylic paint primer. Royal Plywood (royalplywood.com) offers a LEED-certified UV coating on birch, maple and exotic prefinished panels, while Far East American (feaco.com) offers an imported white birch UV-finished plywood panel in B-2, C-2 and C-3 face grades. Shelter Forest International (issuu.com) makes QuadraPro, a four-coat UV-cured epoxy acrylate plywood with a coating that’s twice as thick as the industry standard, and comes in semi-gloss or satin.
Seemac Inc. (seemac.com) offers prefinished hardwood components including panels, drawers and doors. And Plywood Express (plywoodexpress.com) offers customized high-end wood panel product manufacturing.
Most mills offer an in-house coating or can recommend a subcontractor that can custom coat panels, pre-cut and mill them, too. It’s a good idea to check with your regular salesperson before beginning a search for a new prefinished panel supplier.
High traffic panels
With a global trend away from natural wood toward either paint or plastic (laminates and foils), panels that require no further finish are becoming a larger market segment every year.
Ecotech (ecotechpanels.com) is a prime example. The company is a Latin American manufacturer of laminates and related products. Among its offerings are JoyMac and Pertech panels. The former includes high gloss, matte, veneers and woodgrain options. The Pertech line includes Color Core, which has a core the same color as the surface. That means a shop can deliver essentially invisible joints without edge strips. It is available in white, black, red, gray, beige and taupe.
Funder America (funderamerica.com) is a composite wood products company in Mocksville, N.C. The company makes thermally fused laminate (TFL) panels that are available in a broad spectrum of sizes, thicknesses, textures, and designs. It recently expanded its Elme textured series from five colors to eight. At the 2016 IWF, Funder launched the Cabrera texture, which has a deep, rich grain. Extremely durable, non-wood color and texture combinations such as these are replacing natural wood as the quality and aesthetics improve. Suppliers are beginning to hedge their bets and offer both choices. For example, California-based American Laminates (americanlaminates.com) offers a full catalog of TFL panels, plus 14 wood-textured HPL options.
Bonlex (bonlex.com) is another enticing choice. It’s a rigid thermoplastic PVC foil (RTF) gives woodshops a nearly unlimited selection of colors and finishes. The laminate is manufactured by the Japanese company C.I. Kasei Co., which prints a digitally enhanced woodgrain, or a solid color or other pattern on an inner layer of the PVC, blending it to decrease the appearance of cylinder lines.
Vesta panels from the Trupan division of Arauco can be ordered with a TFL finish from the company’s Prism collection (prismtfl.com), and Arauco has recently added five new woodgrains to the menu. The new patterns (Alabaster, Argento, Gibraltar, Kodiak and Palomino) reflect the gray overtones so popular right now.
Based in Quebec, Uniboard (uniboard.com) offers a collection of more than 120 TFL colors in 11 finishes, while Georgia-based Arclin (arclin.com) offers more than 75 stock designs and custom options, too. Plus, Collegewood (collegewood.com) in Lincoln, Calif., offers a line of rift cut grain patterns in deep embossed panels that seem to pick up on flooring trends, and translate that linear grain to casework.
Despite the march of plastic, patterned paint on wood is still a viable option. For example, Roseburg (roseburg.com) says that its UltraFinish panels are produced with a clear, solid or woodgrain pattern that’s painted directly onto the substrate. UltraFinish complements the company’s line of Duramine panels for drawer bottoms and cabinet backs, for example. And CompactWood (compactwood.com) is architectural quality wood that’s encapsulated within a phenolic compact sheet. Showing grain, it is designed to withstand harsh environmental conditions.
Other considerations
One of the more interesting options with ready-to-use panels – and one that should soon be available widely in the U.S. – is a new process from Merino (merinolaminates.com). The Indian company’s Digital Laminate lets a woodshop customize panels with images. So, for example, a shop might incorporate a private client’s family portrait on flat panel closet doors, or superimpose a product image on a landscape in the background of a retail space. It’s essentially custom-made plastic laminate with photography.
For designers who want to use prefinished panels to add drama to a space, Interlam in Mt. Airy, N.C. (interlam-design.com) is a designer and manufacturer of high-end sculpted, carved, decorative and ornamental wall panels. Among those is a through-colored engineered fiberboard known as ForesColor, and the company also supplies a number of wood and metal weaves that can add texture without having to run them through the spray booth.
This article originally appeared in the April 2018 issue.
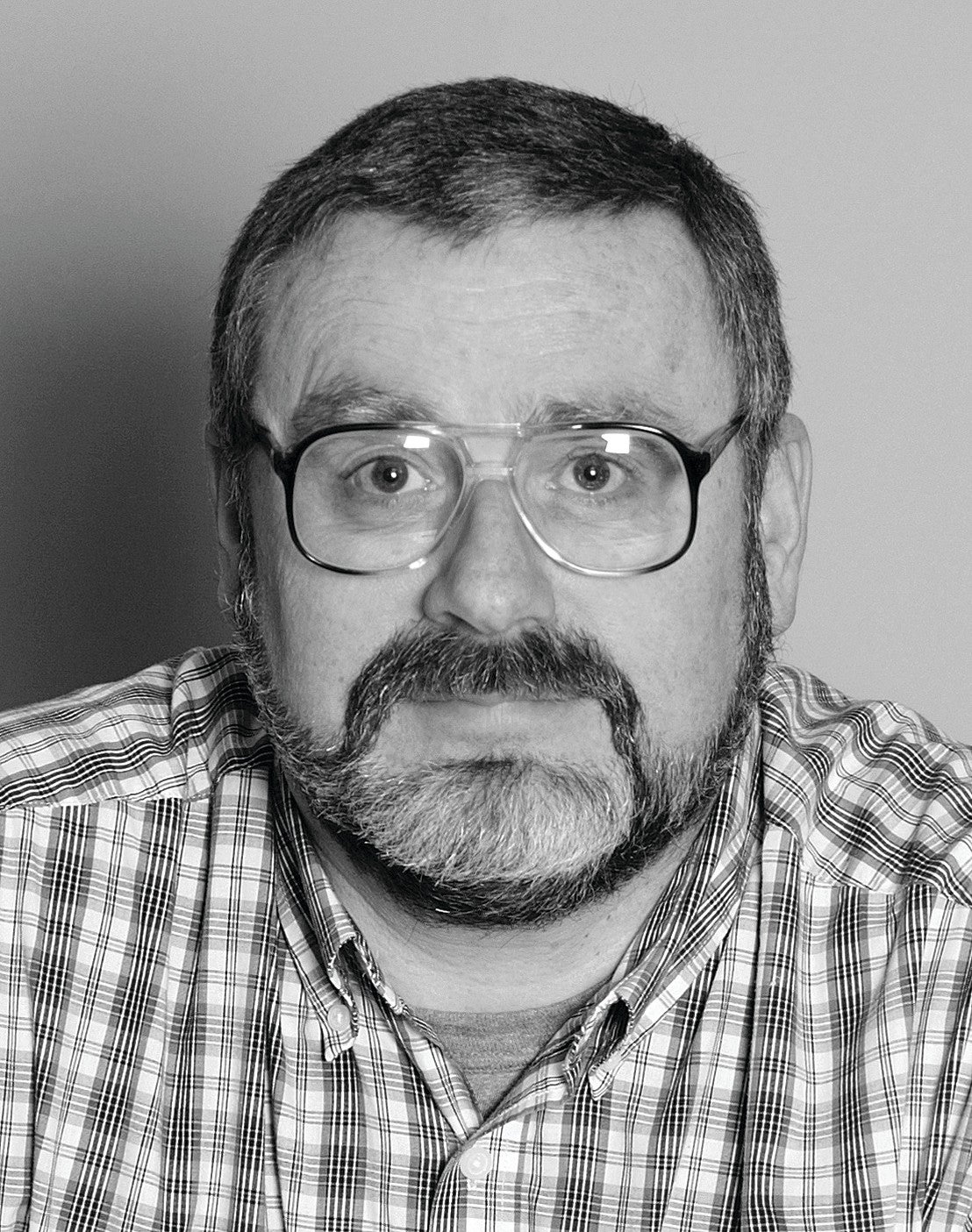