Process and profit
Familiar tasks such as milling profiles or assembling doors are part of production, so it’s easy to see how they can affect the bottom line in a positive way. But…
Familiar tasks such as milling profiles or assembling doors are part of production, so it’s easy to see how they can affect the bottom line in a positive way. But it’s harder to envision any profit in moving materials around the woodshop. This is nothing but a chore — and an expensive one at that.
Or is it?
In business, profit can be generated in two ways. A woodshop can either increase sales or trim expenses to expand the gap between costs and revenue.
Intelligent materials handling can make a big dent in the amount of time that machine operators spend locating and selecting the right raw materials and then moving them from station to station around the shop. Saving time saves money and that builds profits. Since Henry Ford began using assembly lines in earnest a century ago, the woodshop industry has paid attention to methods developed in other industries and adopted some technologies that work well in larger shops. But mass-production environments such as automobile and appliance manufacturing have a distinct advantage over custom woodshops when it comes to conveying: the panels and frames that they make don’t have to change with every job. We can’t run 10,000 identical doors.
However, there’s certainly enough similarity in custom casework projects to allow for a decent amount of streamlining. The key is to be systematic and to consider each step as one part of a greater whole.
The steps
The first step in creating a more efficient workshop environment is layout — that is, planning the flow of work. Sacrificing a little more floor space to create navigable lanes through the shop can be emotionally challenging, especially when you’re asking a veteran team member to redo his or her workstation and give up some footage. But this step is crucial to success. Traffic needs to flow in both directions and there simply has to be enough room to do that. In shops without conveyor belts, the lanes must be wide enough for two handcarts or forklifts to pass each other or else there must be built-in passing lanes that facilitate passage without causing delays.
Perhaps the hardest aspect here is training people not to leave carts, cabinets and countertops in that incredibly inviting empty space. Taping or painting lines on the floor to define pathways is necessary, but enforcing traffic laws is absolutely critical. Here’s an astonishing little time-management tidbit: a single employee wasting a single minute every hour adds up to almost one entire workweek every year (about 35 hours). If you’re paying an average of $20 an hour, a one-minute per hour traffic slowdown is costing you $700 a year per employee. If you’re operating at a 15 percent margin, it takes more than $4,500 in sales to cover that waste.
The second step is organizing storage, both in terms of location (where to put inventory) and logistics (how to store it on shelves, pallets and so on). Some shops bring materials in one door and load finished work for delivery at the other end of the shop. Other facilities work in a circle that leads back to the loading dock.
Whatever the layout, the location needs to make it easy to import (accept delivery) and also to dispense (move materials to each workstation as needed). There is a great deal written about the mechanics of lean management in this area. One of the most significant tenets is that an operator shouldn’t have to shut down production at a machine to go and collect more materials when he or she runs out. A new pallet of plywood must arrive and do so just in time. What this suggests — especially for shops that are large enough in terms of personnel — is that it might be time to designate a single employee whose sole purpose is to constantly refresh materials at every workstation throughout the shop. The notion here is that a CNC operator should operate a CNC and not a pallet jack, which is in line with Ford’s concept of specialization. Restricting the refreshing function to a single person defines and attributes responsibility, which makes the task more accountable and therefore more likely to be done right. But it also brings specialization to materials handling, which almost always results in more efficient methodology. If people do the same thing every day, they tend to get very good at it over time.
The third step is providing the people who are handling materials with the technology that they need to be successful. Today, that begins with learning how to use inventory software so they can find and deliver what’s needed in an efficient manner. It also implies that a woodshop needs to empower these employees (with a degree of oversight) to either manage or at least influence purchasing decisions directly. They are on the front lines and can see what needs to be ordered, and in what quantity, before supplies are depleted and cause interruptions in workflow.
The last technology element is the provision of physical machines and tools — everything from vacuum clamps and conveyors to simple dollies and carts. Solutions here can vary widely across the industry. High-volume shops, where economies of scale can justify a large investment, will have access to some incredibly sophisticated machinery that moves and feeds materials. For the vast majority of woodshops, where the roster includes one, two or just a few woodworkers, that’s not an option and even a forklift can be a bit of a luxury.
Machinery options
For big shops, large and familiar equipment suppliers such as SCM Group (scmgroupna.com) and Stiles Machinery (stilesmachinery.com/material-handling) offer a wide range of stackers, feeders, carriers, flippers and conveyors that deliver work to machines or make it more manageable to move things around. The big advantage to exploring solutions with these companies is that they understand the entire woodworking process and how materials handling can fit into either existing or future workflows.
There are also a number of companies that don’t sell CNCs or beam saws, but specifically just help woodworkers handle awkward and heavy materials. For example, Creative Automation in Abbotsford, Wis. (creative-automation.com) has been working with woodshops since 1971. The company’s areas of expertise include pallet storage, conveying (air flotation, belts, chains, rollers, gravity-based, slats, 90-degree transfers, jump and telescoping), feeding and stacking, flipping, rotation and sequencing.
And there are several reputable suppliers who carry large inventories of specialized workshop environment machinery, such as Hermance Machine Co. in Williamsport, Pa. (hermance.com), or Black Bros (blackbros.com), which has headquarters in Mendota, Ill. The latter offers a comprehensive array of equipment including scissors lifts, pneumatic panel feeders and stackers. Some of these suppliers specialize by brand. For example, D.S. Brown Machinery (dsbrownmachinery.com) in Winchester, Vt., is a dealer for Schmalz automation handling and clamping technologies (as is Hermance). The Schmalz lines include suction pads, grippers, vacuum generators, switches and related equipment.
There are some machinery companies that build a catalog of general woodshop equipment and then offer one or two material-handling products that work well with their line. These are often regional manufacturers that are better known by word of mouth than through ad campaigns. For example, Northfield Woodworking Machinery in Northfield, Minn. (northfieldwoodworking.com) manufactures the model 1700 Panel Stacker, which is fully automated and will handle a wide range of panel sizes and thicknesses. For shops that supply outsourced parts, it can build a load up to five feet tall on skids or pallets and can be ordered with a unique attenuating device that stops the forward movement of the panel and lowers it slowly to the pile.
Most of the larger workshop environment machinery manufactures have a presence, either through their own booths or their distributors, at the major woodworking shows and these are great forums for woodshop managers to kick the tires and see how adding some equipment might save that minute per hour mentioned earlier.
Small shops, or specialized workstations in larger shops, can find a host of innovative and relatively inexpensive material handling equipment on websites such as Rockler.com, Daytontoolcrib.com, Uline.com and Acmetools.com. Their solutions include ways for one person to handle full sheets of stock, plus they offer parts carts, dollies, lifts and a multitude of specialty jigs. Among the latter is the handy little Speed Skate from Woodworkerssupply.com, which is just a pair of wheels with a little platform between them (the whole unit is only 5” long) that is used to roll 4x8 sheet stock from the bin to the saw or router.
To search on CPO Outlets website (cpooutlets.com), follow the menus to Tools & Equipment, then Material Handling, and finally Warehouse & Dock Equipment. There you’ll find the Saw Trax PE, a small cart that can handle odd-shaped granite countertops and other awkward components up to 700 lbs., which could be a gift from the gods on some installs. Also, check out other very innovative carts at Sawtrax-online.com.
To see more ideas, enter the words “material handling” in the search box on the sites mentioned above. And while you’re online, don’t forget to visit resourceguide.woodshopnews.com and click on Materials Handling in the list of categories.
This article originally appeared in the August 2016 issue.
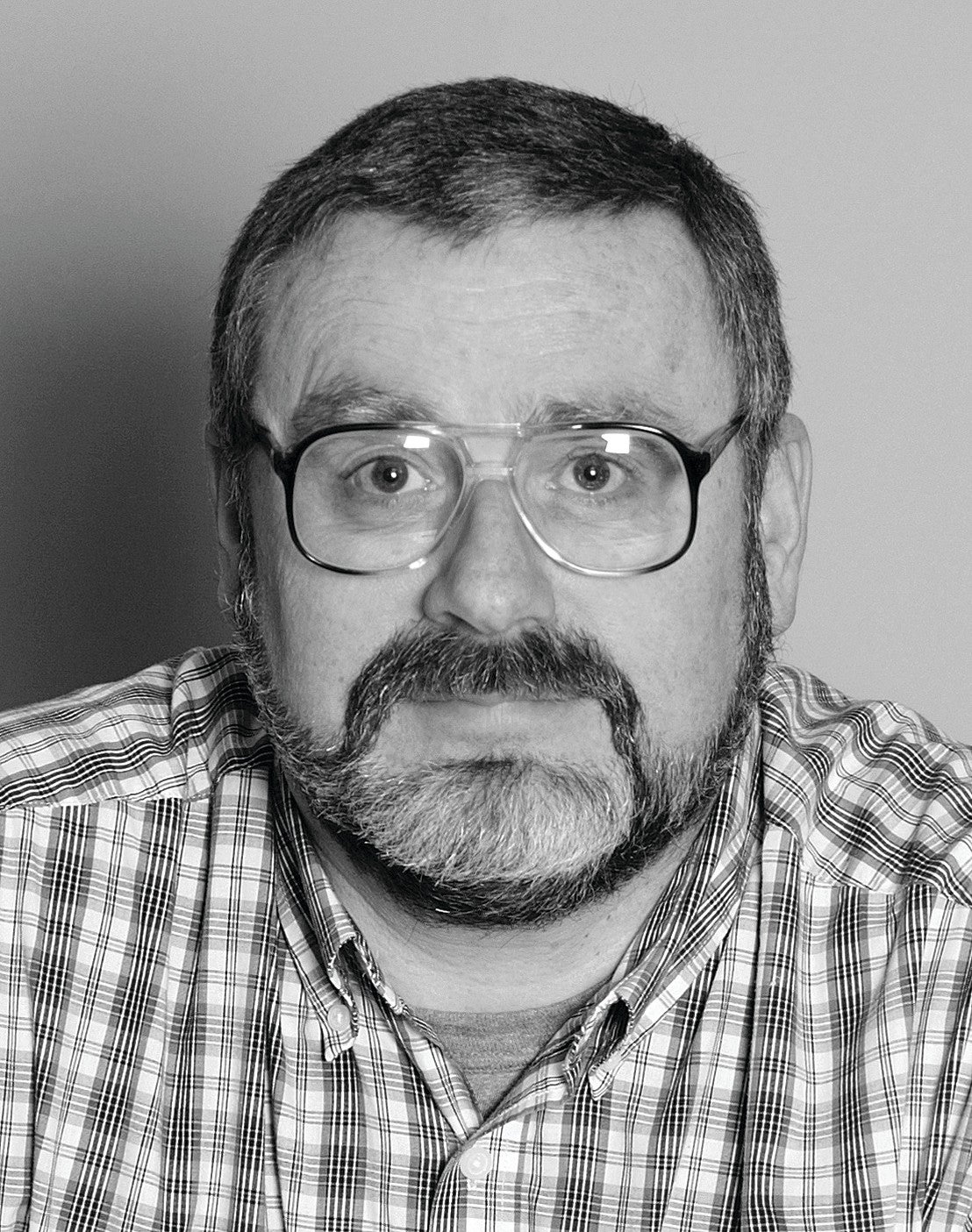