Perception vs. reality
Cabinetmakers and furniture builders often look at finishing in very different ways. The former usually spray lacquer or varnish, while the latter often apply wax, oil or shellac by hand….
Cabinetmakers and furniture builders often look at finishing in very different ways. The former usually spray lacquer or varnish, while the latter often apply wax, oil or shellac by hand. Both, however, are looking for a delicate balance between aesthetics (appearance) and protection (durability).
The advent of environmentally conscious coatings has been a bit of a bumpy road for both professions, as water-based finishes didn’t always start out well. But they have come a very long way in a short time and most shops now recognize their value.
Choosing a coating is not a quick decision. It involves some experimenting, a little networking with other professionals, a few conversations with salespeople and quite often a chunk of time spent in online research. The options become more confusing as manufacturers blur the lines, adding some of one finish to another in an attempt to provide shops with the ultimate solution — one that is easy to apply, tough as heck, simple to repair, brings out that deep glow in the wood, never wears thin, is impervious to water — and is affordable. No coating does all of those things superbly, so a shop needs to choose among options and decide which qualities are most important.
The fundamental changes in coating technology during the last few years have evolved as a response to both government and market concerns over environmental issues, but also as a reaction to improving technologies. Manufacturers don’t just want their products to be perceived as friendly to the planet and responsible. They also want them to actually be those things.
The dichotomy is this: while our woodshop customers are often concerned that the manufacturing process is green, they rarely ask deep questions in this area. A couple buying a kitchen for their new home are usually more preoccupied with door styles and stain colors. The marketing aspect of green, while important and growing, is not yet the dynamic driving force behind purchasing decisions. And because it’s not the quintessential concern of buyers, it’s often not the first concern of woodworkers, either. The more immediate relevance of low VOC coatings for most shop owners is the safety and health of their employees around volatile chemicals.
Say cheese
Greg Hebert understands where shop owners are coming from. Hebert is part of the production team at Vermont Natural Coatings, which is based in Hardwick, Vt. (www.vermontnaturalcoatings.com). The company produces a line of furniture and casework coatings that uses a surprising alternative to traditional toxic components such as benzene and formaldehyde.
“[Our company’s] lynchpin ingredient is whey protein,” Hebert says. “It’s a byproduct of the cheese industry. Our PolyWhey products have superior natural bonding characteristics and produce a finish that is closer in durability to varnish than lacquer.”
Because of its dramatically low VOC content, PolyWhey is the very epitome of today’s safer, easier-to-apply, water-based finishes. A VOC is a volatile organic compound and these are compounds that have low boiling points so they tend to evaporate quickly at room temperature. Most of the things we smell are VOCs. Usually, harmful VOCs are not immediately toxic, but have long-term health effects that can show up years after exposure.
The challenge for woodshops is finding an environmentally sound coating that meets the very highest ecological standards and still gives our customers everything they need in a finish. Woodworkers often balk at the cost per gallon of such high-end natural finishes, but Hebert points out that his product’s coverage (square feet per gallon) is a lot higher than traditional finishes, so shops usually find that their investment ends up being about the same. And if there is a difference, it is more than made up for by the neutral odor, excellent flow characteristics, quick drying times (one can usually recoat in two hours) and easy cleanup with just soap and water. With practice, spraying waterborne coatings can take less time because of issues such as cleaning up and that should be part of the cost calculation. So, too, should the way in which these finishes lower a shop’s legal exposure to health-based lawsuits, which might be a cost savings decades down the road.
Types of finish
There are two kinds of finishes for wood: evaporative and reactive. Those words describe the way in which the finish, once applied, cures over time. Evaporative coatings are dissolved in solvents and they cure as a hard film once the solvents evaporate into the surrounding air. Examples are shellac and lacquer.
In water-based finishes, solids don’t dissolve in the water: they remain in suspension. The water allows the spray equipment to deliver the finish and then it evaporates into the surrounding air, just as a puddle on the floor eventually dries up. Water is essentially a carrier rather than a solvent.
Reactive finishes are also delivered in solution (that is, they travel from the spray gun to the wood in a liquid carrier), but they don’t just sit on the surface after the solvent evaporates. They chemically react with the air and sometimes with a hardener that is added before they are sprayed. Examples are oils, catalyzed lacquer and oil-based varnish.
Varnish is an umbrella word that describes a vast array of compounds, but for the most part it refers to linseed or tung oil in a resin of urethane (ethyl carbamate, which is a byproduct of fermentation), phenol (carbolic acid, which is a petroleum byproduct) or alkyd (a polyester base that has fatty acid additives). As a rule of thumb, the more oil in a varnish, the softer it is. Varnish dries slower than most other coatings, but is more durable than most when cured.
One difference between evaporative and reactive finishes is how they respond to the solvent or thinner once cured. Evaporative finishes will still dissolve in the solvent, while reactive ones won’t.
What’s new?
Global warming or climate change, fracking for oil, Middle Eastern wars, hybrid cars and most of the other things that have kept us awake at night during the last few years all have a common thread — energy and our environment. We are concerned about our kids and the world that we will hand over to them. The woodshop industry is at the forefront of many concerns because we use a resource that creates the oxygen we breathe, naturally renews itself but not as quickly as we use it, and is coated with chemicals when we’re done chopping it up.
So almost everything that’s new in coatings is driven by the need to be environmentally responsible. During the last 16 years, the U.S. Green Building Council and its Leadership in Energy and Environmental Design (LEED) program has monitored that responsibility in the construction world. While LEED doesn’t rate products, it does have standards for indoor air quality. The way it works is that every aspect of construction is rated using a points system that indicates how well the process involved can satisfy green building requirements. The number of points that the project earns will determine its level of LEED certification. When a woodshop sprays more environmentally conscious coatings, its cabinets and furniture meet more of the LEED certification requirements. Every year, more and more municipalities, school districts, government construction projects and architects are placing a stronger emphasis on LEED certification. The council invests more than $30 million a year to maintain, operate and improve LEED and its efforts are changing the way the construction industry is doing business. Using something like a whey-based natural coating as opposed to one that has a petroleum byproduct solvent is becoming a significant choice for woodworkers. The former can help a shop meet LEED standards for indoor air quality.
Many of the new waterborne finishes have better natural adhesion than their predecessors and their low VOC content makes them a lot safer to handle, too. They eliminate or minimize a lot of concerns such as employees breathing toxic fumes or rags spontaneously combusting. By using natural biodegradable materials and simple water to create their resinous solvents/carriers, they reduce the risk of cancer and pulmonary diseases, make cleaning up so much quicker and easier and still deliver a finish that flows well, settles evenly and resists water, chemicals and scratches. The biggest downside in the shop is that they can’t be allowed to freeze.
Every major manufacturer including AkzoNobel, Henkel, PPG, Sherwin-Williams (and its Minwax subsidiary), DuPont, BASF, RPM, Valspar and 3M has its own line of water-based finishes. One of the abiding concerns for these companies is that there is a high probability that the government will eventually mandate this approach (hey, they don’t let us make incandescent light bulbs anymore). Before that happens, manufacturers need to have a strong history of field experience with water-based and natural coatings. By then, they must also have earned the confidence of users such as woodshops. So the coatings industry is investing a great deal of time and money in their efforts to research and develop products that meet both environmental goals and our shop standards.
Spend a few minutes on any online forum such as Woodweb and you’ll hear some woodworkers complain about the quality of water-based finishes. However, many of the comments were made a couple of years back and quite often they’re from people who haven’t yet tried the latest coatings. The perception about the quality of the newest generation of coatings lags a little behind the reality.
This article originally appeared in the April 2014 issue.
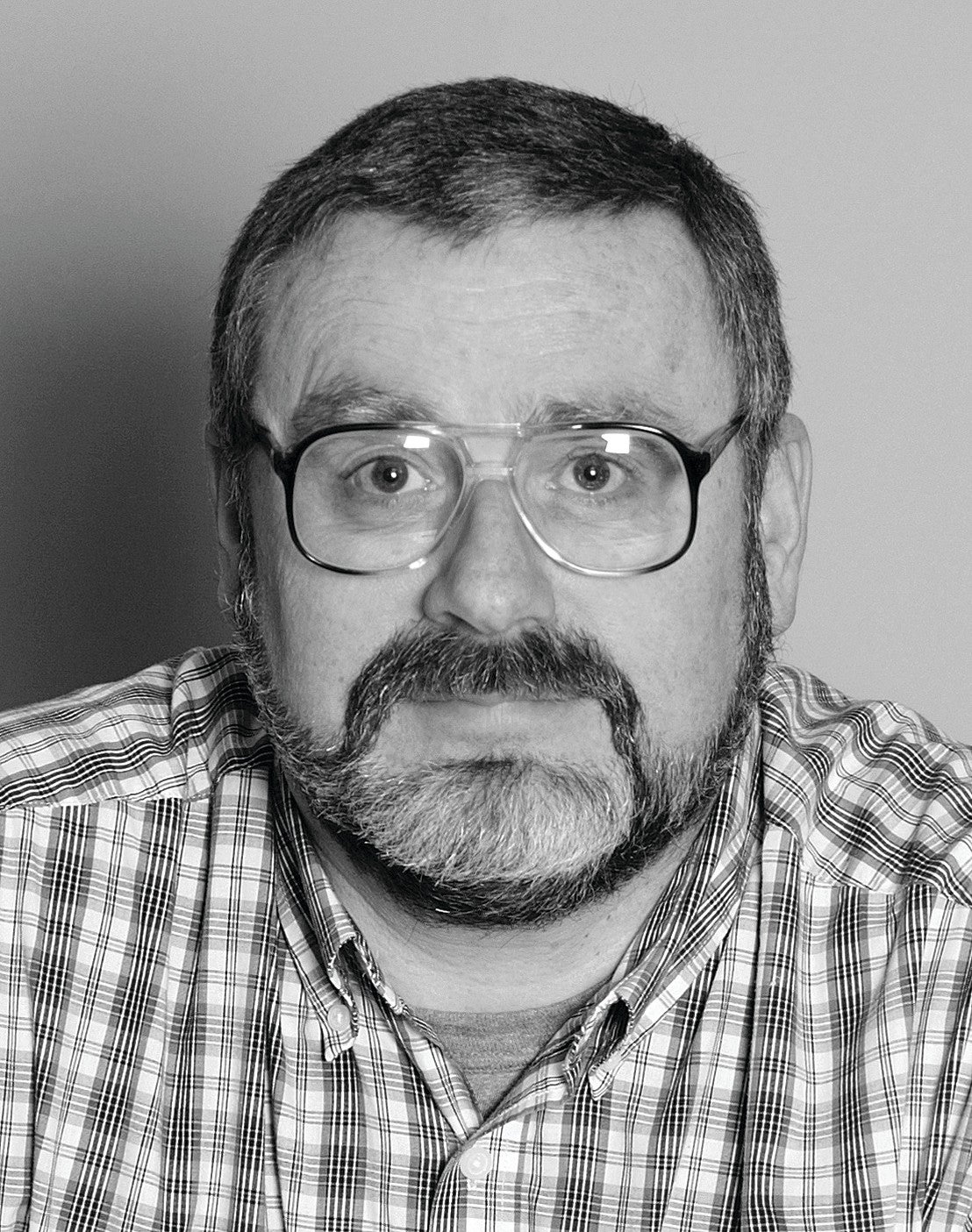