Next Generation Materials
The future is now for straw-based MDF, glass countertops, modified wood and other new technologies.
America was just a fable beyond the horizon until a bunch of nosy Europeans went looking for it. Once they arrived and displaced the locals, they invented a plethora of new industries such as tobacco growing, beaver hunting and silly hat manufacturing. The common thread here was that they found new materials onsite, and then worked out ways to market them.
We’re still doing that. Innovation is the core of our economy and has been the key to America’s global dominance in manufacturing for the past century. The pace isn’t slowing any, either, especially in the wood world. In fact, one of our core materials is about to undergo some fundamental changes. California-based CalAg LCC has almost completed a new, state-of-the-art manufacturing plant for the processing of rice straw into MDF. The company has invested more than $315 million at a location in Willows, a town of about 6,000 residents that sits a hundred miles north of Sacramento, and the German engineering giant Siempelkamp is supplying the machine technology. Rice straw is available in large quantities in North America, as the U.S. grows approximately ten million metric tons of rice every year. When construction is completed during the third quarter of this year, CalPlant will become the world’s first commercial-scale producer of rice straw-based MDF, annually supplying approximately 140 million sq. ft. of no-added-formaldehyde MDF to woodshops and other manufacturers.
Also in North America, Great Plains MDF Production Inc. announced on July 15 that it will be building a $750 million plant in Stettler, Alberta to make MDF out of surplus wheat straw. The company is led by Alberta native Brian McLeod who has had a long career in the Canadian forest products industry. The new plant will use a non-formaldehyde polyurethane resin that is environmentally friendly, to add strength and durability to the straw. There will be no toxic emissions emanating from the product. The factory will enclose a million square feet and be the world’s largest MDF plant once completed. Estimates are that it will produce 500 million sq. ft. of 3/4” product each year. About 2,500 metric tonnes of straw fiber will be needed every day at peak capacity, saving millions of trees that take 25 to 40 years to mature. The straw is, of course, an annual product. There are only two other straw-based MDF plants being planned worldwide, both of which are in China.
Once that new MDF starts flowing, the folks at North American Plywood Corp. have plans for some of it. Their DesignPly is a digital, high definition inkjet staining and finishing system that prints directly to a substrate (plywood, particleboard, MDF, etc.), and is UV top-coated. The custom image panels can come in sizes up to 63” x 123”, and up to 2” thick. Whether you need one panel or thousands, this fully automated process can deliver custom designs with perfect color matches and custom cutting, finishing, routing and laminating. The system lets woodshops offer commercial, institutional and even high-end residential customers a choice of casework with essentially what amounts to unique photo or artwork panels. NAPC has locations in California and New Jersey, and there’s a video on the website that shows robots making the product.
In another effort to replace traditional MDF, the University of Maine was issued a patent in July for a process to create construction materials that are bound with cellulose nanofibrils (CNF). The process focuses on a replacement for particleboard that’s used in furniture and countertops. It eliminates the use of formaldehyde as a binding agent, replacing it with a CNF slurry. The resulting product tests higher for fracture toughness and also sequesters carbon and oxygen into the building product for its lifespan, which typically is decades. Cellulose nanofibrils can be refined from wood waste products, and the University of Maine is actively seeking a development partner for the technology.
Overseas innovations
There’s a lot of interest in cross-ply innovation that uses state-of-the-art resins and glues to create both panels and structural alternatives to solid lumber or traditional laminated beams. Early last year, the German hardwood company Pollmeier added spruce laminated veneer lumber to its beechwood line. The new product is used for non-visible standard components in structural timber construction, while its beech laminated veneer lumber is primarily chosen for visible timber structures. The company offers the spruce product in various strength classes in longitudinal as well as cross plies. Some of the new, high-strength laminated materials are actually stronger than steel.
Several companies are also offering new heat treatments for wood that augment their natural properties and offer new levels of resistance to decay. Lignia Wood Co. is located a few minutes west of Cardiff, on the south coast of Wales in the United Kingdom. The company has just signed an agreement with Hardwoods Specialty Products, which has 24 distribution centers in North America, to stock its unique products. Among them is the namesake Lignia Fire lumber, which has a Class A fire rating and carries a 50-year above ground warranty against rot and decay. This is real FSC-certified softwood that is modified so that it has the durability, looks and performance of tropical hardwoods. Nick Smith, senior general manager at HSP, notes that Lignia also has excellent working properties. It’s easy to machine, coat and glue, and is very sustainable. Both Lignia and Lignia Fire are suitable for flooring, siding, outdoor decking, furniture, cabinetry, millwork and other applications.
A company in Turkey is also now using thermal treatment to alter the properties of wood and make it more resistant to harsh climatic and physical conditions. Tantimber (tanmtimber.com/en) sources FSC wood and uses two types of process, open and closed, that both use steam boilers. The open system transfers heat through radiators and is eminently controllable, while the closed system is more direct. The process changes the color of the wood and its moisture content parameters.
Innovative products such as Lignia and Tantimber allow woodshops to offer lower cost, easy to work alternatives to sustainable-challenged high-end species such as teak and some tropical exotics.
Naturally new
We’ve seen a surge in clever countertop alternatives over the past few years and a move away from laminates and solid surface materials toward stone – everything from quartz to soapstone and concrete. Metals are making their mark, too, but not just your standard old stainless. One of the hotter trends is copper, perhaps because of its ability to age gracefully and also its hygienic properties. Zinc, too, is getting a lot of looks lately, but copper may turn out to be a headliner because of a hidden superpower. According to The Smithsonian magazine, “the SARS-CoV-2 virus endures for days on plastic or metal but disintegrates soon after landing on copper surfaces.” The article by Jim Morrison at smithsonianmag.com was published in April 2020 and goes on to say that the EPA has registered about 400 copper surfaces as antimicrobial. It’s a fascinating article and well worth a read if you build casework for clinics, hospitals, schools, or even wealthy hypochondriacs.
But despite those leanings, the next generation of countertop materials was beginning to look like a comeback for natural wood a year ago. The pandemic seems to have changed that in a fundamental way. The porosity and organic qualities of butcherblock are being swapped for impervious and easily decontaminated surfaces, and one of the new megastars seems to be glass.
Solid glass countertops can come in some impressive thicknesses. A company called ThinkGlass (thinkglass.com) now offers them in options up to 18” thick, and the customer can add embedded LEDs for some startling effects, especially if the glass is colored or patterned. The handmade and highly custom counters, even the thin ones, come with a very hefty price tag.
It takes a lot of high tech to create a thick glass top with lights inside it, but when it comes to next generation materials it’s not always about science. Sometimes it’s just about responsibility. The Urban Wood Network (rbanwoodnetwork.org) is an organization with branches in Illinois, Michigan, Missouri, and Wisconsin which is funded in part by the USDA Forest Service. The Network harvests wood exclusively from trees that have died naturally from pests and disease, or have otherwise succumbed to construction and human related circumstances. All of the sound material from each log is processed locally and is highly sustainable. The lumber has been compared to Italian marble in the sense that no two pieces are alike, so it is prized by art furniture builders who appreciate both its unique looks (urban trees tend to grow differently than species in a natural forest), and the fact that it often comes with a story. The variety of species may include elm, ash, cherry, maple, walnut, white oak, honey locust, red oak, pine, hackberry, catalpa and more. Many of the logs are available as live edge boards and slabs.
This article was originally published in the September 2020 issue.
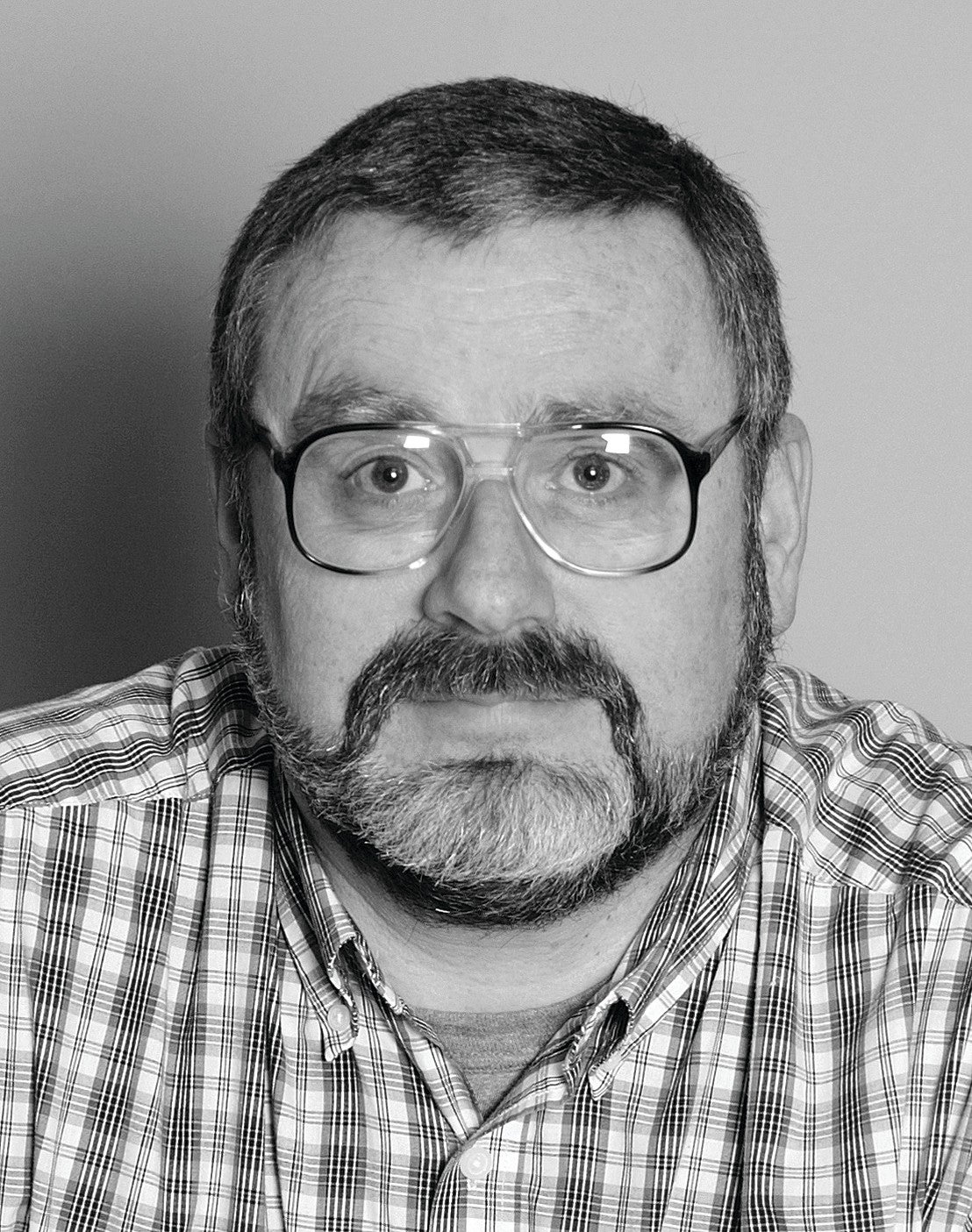