Moving On Up
Shops of all sizes can benefit from an improved floor plan and the addition of material handling equipment.
Moving inventory and parts around the shop is an expense. Unlike milling, assembly or finishing, this task has no profit potential. It’s all cost, so it needs to be as efficient as possible. And streamlining doesn’t start with a new forklift or an automated robot, but with layout and workflow.
That begins with a floorplan.
If your business has grown the way most do, the original equipment is still where it was on day one. Everything else has grown up around it. You may have added a showroom, finishing bay, or built an annex for storage. Perhaps you purchased the empty building next door and use that as a warehouse.
The reason that shops grow is that they’re busy. Every day spent on remodeling is a day when no cabinets are built. That makes it very hard to think about moving machines around, especially when the system has been working well. So, new space tends to be dedicated to new processes or machinery, and existing spaces are disturbed as little as possible.
The controlled mayhem of that kind of evolution often defies the logistics of workflow. If you need to send somebody to another building with a forklift to feed the CNC, or carry casework all the way across the shop to load it on a truck, it may be time to blow the dust off the floorplan and rethink some sequences.
Evolving machinery is also part of the equation. When the original shop was set up, panel lifting, turning and loading were probably all manual. If you’re thinking of adding automation, consider how it fits into the overall workflow rather than just how it serves a single machine.
Maybe that machine needs to be moved.
Automation options
There’s a beautiful precision in the way that a machine picks up a large sheet from a stack and drops it exactly where it’s needed on an infeed table. As the processing machinery has evolved and CNCs have become the norm, sawing and profiling have gained a lot of ground. Speeds are up and defects are down. But moving sheet stock into and out of these machines hasn’t kept pace. The robotics were cumbersome and expensive, and the software lagged. Now, all that has changed and larger shops are rapidly eliminating the manual slowdown between machines.
A leader in this field, Stiles Machinery (stilesmachinery.com) in Grand Rapids, Mich., summarizes the situation this way on its website:
“Material handling now features technology that matches the sophistication of the machines that prepare the pieces. Swing arm panel feeders ensure continuous operation; panel stackers provide many options for storage and retrieval; robotics transfer pieces from machine to machine; conveyors and lift systems speed the transfer of materials with a minimum of human involvement; fully automated stacking/de-stacking machines easily handle input from multiple conveyors and trolleys – and you can purchase material handling systems that match up seamlessly with many of the machines you have, or plan to purchase in the future.”
But what about small- and medium-sized shops? Well, there has been a bit of a revolution there, too. Somewhere between complete automation and a trip to the chiropractor, there are several options that can speed up production and reduce injuries and damage. This melding of high technology and manual labor can provide an affordable way for smaller shops to perform larger tasks more efficiently.
For example, Stiles carries the Schmalz Jumbo Ergo, which is a stand-alone unit that picks up sheet goods with a vacuum, and an operator then manually steers it to move the stock where it’s needed. The lift has a motorcycle throttle control and can lift up to 660 lbs., so it can move entire cabinets. The company also makes units that can lift several thousand pounds.
Hendrick Mfg. (hendrickmanufacturing.com) offers a similar solution, the Vaculex lift. It helps operators pick up heavy materials and move them onto elevated surfaces much more easily, while offering maximum flexibility in movement. Such lifts can work in places and situations where a lift table might not quite fit.
Hendrick also carries Southworth’s lift tables, which are designed for small shops or for specific workstations in larger environments. They can lift, tilt and position panels and parts, which lets them safely load materials onto machines for processing.
Loading MDF isn’t the only challenge for material handling machinery, and there are numerous task-centric, tech-manual hybrid solutions on the market that can reduce both fatigue and failures. For example, Homag’s entry-level return conveyor, the Loopteq 0-200 (which used to be called the Boomerang), makes it possible to operate a single-sided through-feed edgebanding machine with only one person. The part slides through the bander, is picked up by a conveyor table, moves it sideways away from the machine, and then sends it back to the operator.
James L. Taylor Mfg. (jltclamps.com) has a number of conveyor solutions for small- to medium-sized shops. They include units for edgebanders, wide belt sanders, shapers and rip saws. One nice aspect of these smaller systems is that they are easy to customize. For example, Taylor’s wide belt solution comes in 60”-, 84”- and 96”-long options and the roller width choices are 24” or 36” so they can handle material up to 50” wide. And because these are modular sections, a shop can pretty much build a return system of any length it needs.
Shops that cross-cut a lot of parts (such as cutting door stiles and rails to length) can make a big dent in the time required to manage and move those elements by automating the stop system. For example, TigerStop (tigerstop.com) makes an automated material pusher and stop gauge. Just punch in or download a cut list, and the stop will move to one of several positions. Instead of an operator handling the material a couple of times and using a tape measure on every cut, he/she just drops the stock in place and cuts when the fence stops moving.
For basic hauling of sheets and parts around the shop, Saw Trax (sawtrax.com) has a range of very affordable, customizable carts and dollies, including rough terrain and tilting versions. The company’s Panel Express is especially well suited to moving countertops around the shop and the jobsite. A rubber-lined, self-adjusting clamp holds material up to 3” thick and the dolly has locking casters and maintenance free foam tires that never go flat or need air.
Large-shop solutions
High production shops can’t often buy a single material handling machine and just pop it into the process. There are software challenges, compatibility issues, volume and speed considerations, training and other aspects of the production cycle that require a systemic solution.
Suppliers such as SCM, Stiles and Biesse will sit down with a shop’s management team and garner enough information to build a comprehensive plan that includes potential for future growth. For example, Biesse says that it “collates all kinds of technical data such as plant layout, product type, manufacturing specifications, quality objectives, quality and production standard controls, as well as the study of software integration. Once such data has been analyzed, a technical and commercial specification is drafted.” The company’s Winstore is an automated solution for larger shops that can be integrated into nesting and sizing cells, and deliver a significant increase in productivity.
The Store-Master 5110 from Weinig/Holz-Her (holzherusa.com) is another state-of-the-art solution for larger shops. It combines storage bins and a delivery system with impeccable software. It will work with a wide variety of panels and decorative finishes, and exactly the right panel is selected every time. The panels can be rotated up to 90 degrees, which means they can stored in any orientation. Damage to the panels is essentially ruled out due to automatic, computer-controlled transport – no more wobbly forklifts. Plus, multiple machines can be served, and as many storage bins as desired can be set up for storage and retrieval.
SCM Group NA (scmgroup.com) also offers a catalog of material handling solutions. They run the gamut from simple panel rotation and conveying machines to entire systems such as the Flexstore el that delivers automated 3 axes storage. It can be integrated in production lines for nesting and/or sizing cells, with a significant increase in productivity and considerable reduction of costs. It manages homogeneous and mixed stacks (that is, panels of different dimensions and colors), and raw panels all the way down to 3 mm thickness.
One nice facet of most of these larger systems is that they use vacuum technology to pick up and deliver panels or parts, so the materials are not sliding across the sheet below them and causing scratches.
For shops that understand the need for better material handling, but are intimidated by the cost of state-of-the-art electronics and controls, there are several reliable suppliers such as Hermance Machine Co. (hermance.com) that supply used equipment – everything from scissor lifts to vacuum lifts, carts and fork lifts.
CombiLift (combilift.com/us) is an Irish company with U.S. headquarters in Greensboro, N.C. and it builds incredibly versatile forklifts including multi-directional vehicles that combine the features of a counterbalanced forklift, side loader and a very narrow aisle truck in one vehicle; side-loader forklifts for long loads such as glue lams; and a number of other unique load handling solutions.
This article originally appeared in the February 2019 issue.
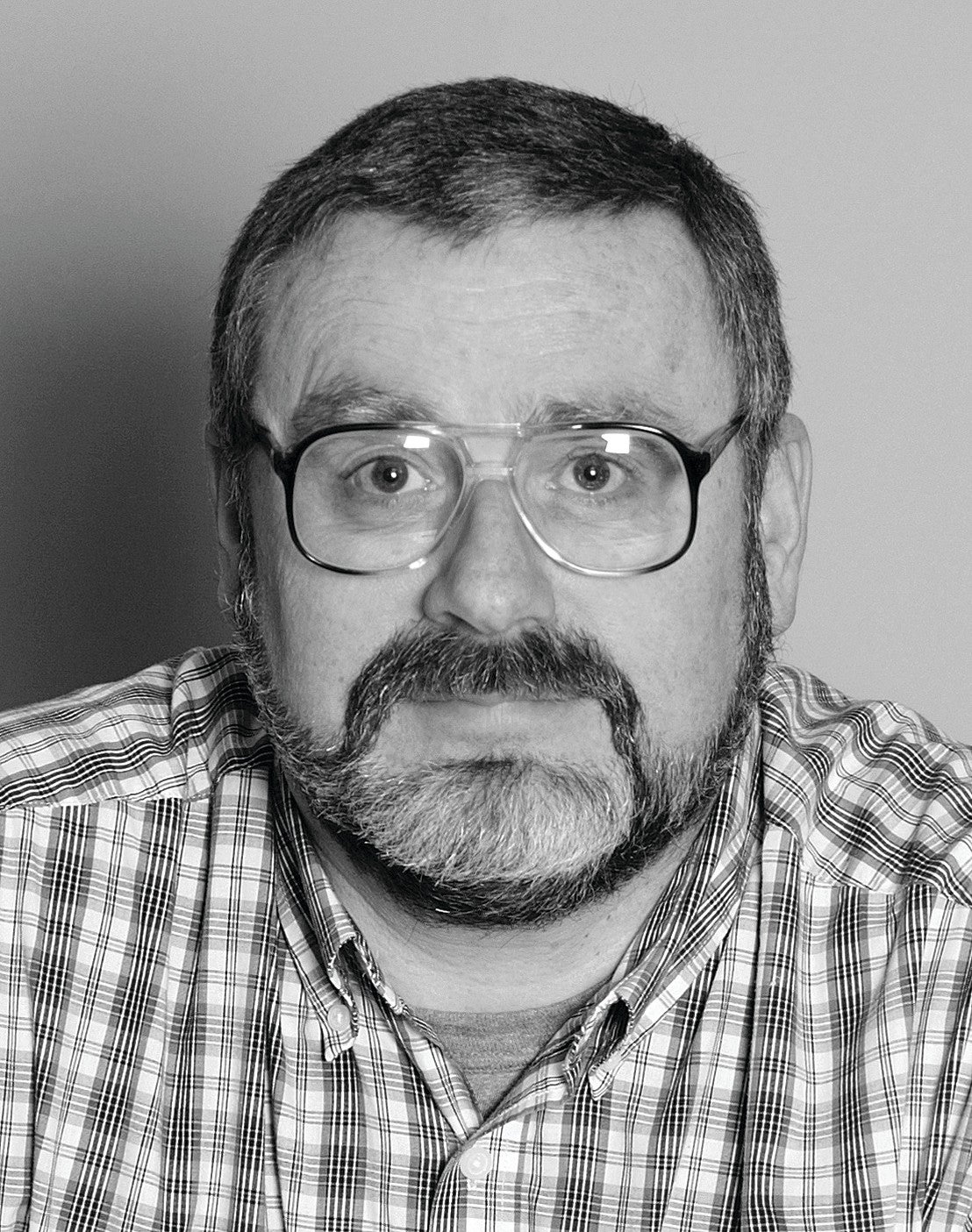