Measuring up to your expectations
In the first in a two-part series, we take a look at how hardwood is measured, sized, dried and sold to consumers There aren’t a lot of specific terms in…
In the first in a two-part series, we take a look at how hardwood is measured, sized, dried and sold to consumers
There aren’t a lot of specific terms in the hardwoods industry, but even a short new vocabulary can be confusing (like that first day on the golf course when somebody mentions an eagle and you look up). There are basically just two sets of words to know: those dealing with measurement and those describing character. Once learned, understanding hardwoods is relatively easy.
Measurement
There are really only two types of measurements in regards to hardwoods. The first is thickness and the other is volume.
The hardwoods industry describes the thickness of boards in “quarters.” A board that is 1” thick is referred to as “four quarter,” and everything else takes its cue from this. Boards that are 1-1/2” thick are termed “six quarter,” while a 3”-thick slab would be “twelve quarter.” Visually, the written versions of these are what one would expect: 4/4, 6/4 and 12/4. The numbers run anywhere from one quarter to a maximum of about 12 or 14 at most suppliers, although thicker boards are certainly available.
The key here is that the measurement describes rough boards. A 4/4 board was a little more than 1” thick when it emerged from the saw at the mill. It may only be 3/4” thick when a customer sees it in a kitchen. Or it may be 15/16” thick (7/8” at some yards) if it has just been passed quickly through a planer to remove some of the thin, seasoned outside layer. This is done to reveal a hint of its color and grain and the process is called “hit or miss.” Woodworkers like this because they can see whether a board has a lot of defects (more on these in a minute) or whether they are getting sapwood or heartwood. Lumberyards like it because the boards are a little lighter (a consideration in shipping large loads) and because their customers are not as easily surprised or disappointed when they start planing the stock back at their shops. So the quarter system means that the thickness of lumber is consistently measured in units of 1/4” when rough. According to the National Hardwood Lumber Association, “the finished thickness for lumber of 1-1/2” and less can be determined by subtracting 3/16” from the nominal thickness. For lumber 1-3/4” and thicker, subtract 1/4”.”
The second part of measuring is volume (also called cubic area). This is calculated using a unit called a board foot. The easiest way to visualize this is to imagine a rough board that is 1’ wide and 1’ long, but only 1” thick. Stretch that board (hey, we’re still imagining here) and it can become 6” wide and 2’ long, and still only contain the same amount of wood. Stretch it some more to 3” wide and 4’ long, and the volume is still the same.
If it’s 8/4 material that is 3” wide and 4’ long, there will be twice the volume of a 4/4 board (that is, two board feet). If you’re buying from a mill or kiln operator, “net tally” is the board feet of lumber measured after kiln drying, while “gross” or green tally is the board feet measured before kiln drying. There’s a difference of about 7 percent because boards shrink across their width during the kiln-drying process.
Calculating the board feet in a piece of lumber is less complicated than one might suppose. Simply multiply the number of inches in the width, length and thickness by each other and divide the result by 144. For example, let’s calculate the board feet in a board that was 1” thick, 6” wide and 8’ long before planing. Multiply 1x6 and then multiply the result by 96 (the number of inches in eight feet). The result is 576 cubic inches. To reduce that to board feet, simply divide it by the number of cubic inches in a board foot (144). The result is four and this is usually written as 4 bf.
Random sizing
The cookie-cutter boards available in home stores are all uniform in size. That is, they come in standard widths and lengths. They are nominal 1x2s (3/4” x 1-1/2”), 1x4s (3/4” x 3-1/2”) and so on. They also come in standard lengths, which are usually in two-foot increments from 4’ to 12’ long, although many stores only carry 8’ long boards.
Lumber sold like this is called “dimensional lumber,” and outside the hardwood racks at the big-box store, the industry reserves this terminology and sizing for construction lumber (softwoods such as spruce, pine and fir). Its predictability is comforting, but it is wasteful and always expensive. The sawmill, or more likely the wholesaler, had to throw away a lot of material to reduce those boards to standard dimensions.
Hardwoods, on the other hand, are most often sold in random widths and lengths. The boards in a specific bundle (called a “bunk” in the trade) will all be of the same nominal thickness, such as 4/4 or 8/4. Unless ordered in specific widths, they will be of varying (“random”) widths, which can be anywhere from 2” to 20” or more, depending on the species. Poplar and mahogany boards, for example, are sometimes close to 2’ wide, while quartersawn white oak will usually be in the 4” to 8” range.
Random lengths can run from 3’ to 16’ or more. Whenever lengths are specified, the price goes up. As with widths, it’s less expensive to specify a range than to demand specific lengths. However, there are times when specific widths actually save money. For example, if a shop is going to make lots of 4” wide molding, the buyer won’t want to buy a lot of 6”- and 7”-wide stock because of the amount of waste (called “drop”).
Rough-sawn hardwood boards are often 2” or 3” longer than their nominal length. For example, an eight-footer may be 99” long. This is because the logs go into the mill at that length and, unlike softwoods, the ends are not usually trimmed. When calculating the board feet to charge you, most yards will include those three inches as long as the end isn’t split or otherwise damaged.
When figuring out how much lumber to buy or use, keep in mind that narrow strips can often be edge-glued to make wider boards, but it’s virtually impossible to turn short boards into long ones. There are a few router bits that create end joints (example at right), but the results usually aren’t very pleasing to the eye. A rule of thumb is to buy 15-20 percent more stock than the project requires in order to allow for waste.
Kiln- and air-dried lumber
All wood contains some moisture. When buying hardwoods, it pays to know a little about moisture levels. The industry measures this in terms of the weight of the water expressed as a percentage of the weight of the wood. For example, imagine an oak board that weighs 42 lbs. without any water in it at all. That same board in a lumberyard in the middle of the country will have a moisture level of about 6 percent after it has been kiln-dried (humidity varies with location and time of year: think Seattle and Death Valley, Calif.). At 6 percent, there will be 2.52 lbs. of water in the board, for a total of 44.52 lbs. The water weighs 6 percent of the net total that the lumber weighs.
This number is important to wholesalers who transport lumber because fresh logs can have upwards of 30 percent moisture levels, which means that the trucker can only load about two-thirds of the weight he could legally carry if the load was completely dry.
This number is also important to the woodworker because lumber above about 9 percent tends to misbehave. It splits near the ends, warps, bends and generally has a mind of its own. The moisture isn’t evenly distributed — the center of a board is generally wetter than the surfaces — and this can play havoc with the wood when the water expands as it heats up during the day and then contracts as it cools at night.
For comfort, people like to control the indoor ambient humidity (the amount of water in the air in a room). We like our air to be around 30 to 50 percent relative humidity and, fortunately, lumber likes the same range. Relative humidity below 20 and above 75 percent can cause problems with wood. Lumberyards that keep dried hardwoods stored inside are a much better option than mills and yards that store them outdoors.
Lumber is dried in two ways. It can be kiln-dried in a gas, wood, electric or solar oven, or it is seasoned. Seasoning means that the lumber is stickered outdoors, usually under a shed roof or some plastic, and allowed to air-dry. Typically, seasoning takes about one year for every inch of thickness, while the average kiln run is just 20 to 40 days, depending on species, kiln size, moisture content and thickness. Stickering means that the boards are stacked with 1/4”-thick sticks between them to allow air to flow around all six surfaces. If the sticks are not of the same species as the boards, they can often leave shadow marks every few feet across the boards, where chemicals in the two species react with each other, and this is something to be aware of and look for when selecting boards.
Boards being kiln-dried are usually sealed on the ends because the open cells of end-grain will lose moisture more quickly than those of side grain. The seal slows the process and can be used as a color code to quickly identify species or cuts.
Color and grain
Boards of the same species can diversify widely when it comes to overall color and general appearance. Oak growing in northern Minnesota has a much shorter growing season than oak grown in the southern Appalachians. The minerals in the soil, the angle and intensity of the sun, rainfall levels, pollution in the air and quality of the groundwater all affect the way a tree grows and the color of its heartwood. Whether or not the tree has neighbors can play a big role, too. A tree growing alone in a field spreads out to catch as many rays as it can, while one living in a forest needs to grow straight and tall so that it can poke its head out above its neighbors.
Hardwoods are by nature dendritic, which means they divide into branches and then twigs. (In biology, it also describes the way that cells divide and crystals grow.) Curtailing this tendency by planting trees close together is one way to make them grow straight, a deliberate practice that is often associated with mahogany and teak farms in tropical climates.
In America, northern hardwoods tend to have more even color from tree to tree than those growing in the South or across the Appalachians. There also is less of a contrast between the sapwood and heartwood within each tree. Therefore, slow-growing Northern hardwoods tend to fetch a better price than logs from other parts of the country. So it’s a good practice to ask a supplier where his stock originated.
Hardwood grades
To avoid confusion, the hardwoods industry never talks about the “sides” of a board. Instead, they refer to edges, ends and faces. For many woodworkers, one of the most startling things they learn about hardwoods is that only one face of a board is graded. The theory is that this takes less time (and is therefore less expense) and most boards are fairly similar on both faces anyway. That’s probably true from a seller’s point of view, but not always so from the buyer’s. And just to confuse the heck out of us, some mills grade the best face, while others grade the worst.
The other thing to keep in mind when buying a board is that the woodworker is looking at it in terms of his/her project and is primarily concerned with appearance, while the mill has graded it according to the number of cuttings it will yield. Cuttings are usable pieces, so the mill grader will decide that a board could be ripped right up to both sides of a large knot and then crosscut so the knot is eliminated, but there is no other waste. In his eyes, the board had perhaps 1 percent defect. If that knot is right where a decorative ogee is going to be milled to create a table edge molding, the woodworker has a completely different set of values.
The lesson here is that it really pays (if one has time) to go to the yard and pick through the stock rather than having, say, 500 bf delivered to the shop. This is especially true if the woodworker doesn’t place regular orders because the supplier will quickly get to know regular customers and learn their specific needs and grading preferences.
How hardwoods make the grade
Grading is theoretically a very precise practice that could be replicated anywhere on the continent. In practice, small mills and even some retailers have their own systems and terminology that can be very confusing.
The following grades were developed by the National Hardwood Lumber Association, and are adopted by most industry groups and producers across the country.
• FAS/1F (Firsts and Seconds/Furniture): 6” and wider, 8’ and longer, 83.3 percent clear on its best face.
• Select: 4” and wider, 6’ and longer, 83.3 percent clear on its best face.
• No. 1 Common: 3” and wider, 4’ and longer, 66.6 percent clear on its worst face.
• No. 2A Common: 3” and wider, 4’ and longer, 50 percent clear on its
worst face.
• No. 2B Common: 3” and wider, 4’ and longer, 50 percent sound on its worst face.
• No. 3A Common: 3” and wider, 4’ and longer, 33.3 percent clear on its worst face.
• No. 3B Common: 3” and wider, 4’ and longer, 25 percent clear on its worst face.
A woodworker should be aware that these basic grading requirements are often relaxed a bit when it comes to less widely available species.
Color grades are quite subjective and can change from mill to mill. No. 1 and No. 2 White, and the term “Saps” are all grades for maple and birch that describe the amount of sapwood present. A few species are more valued for sap than heartwood, but oak, cherry, walnut, hickory and birch are more valued for brown (heart) color. Your salesperson can help with questions about specific species.
Information on surfacing, defects, sawmill cuts and more will appear in the April issue.
This article originally appeared in the March 2012 issue.
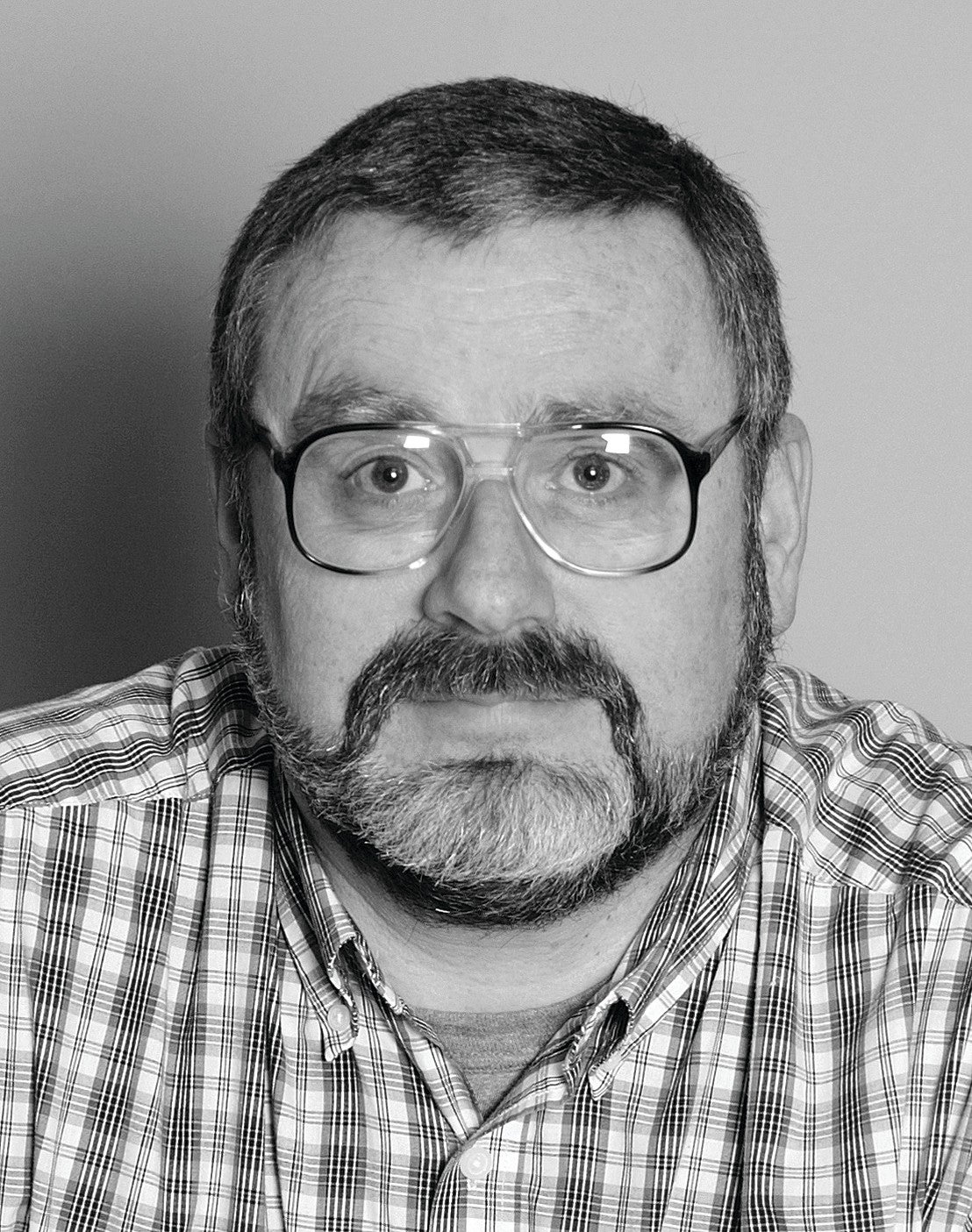