Making Safety Second Nature
Over the years, the word ‘left’ has become somewhat synonymous with liberal politics.
Over the years, the word ‘left’ has become somewhat synonymous with liberal politics. But for woodworkers of a certain age, it refers to being able to play the piano in your nineties. Back then, LEFT used to refer to the four areas of concern when it came to safety in the woodshop – Lungs, Eyes, Fingers and Trails.
Lungs included a good central dust collection system plus masks, filters, blast gates and collection at the tool. Eyes referred to goggles or full-face shields - especially when working on machines that create airborne particles, such as lathes and chainsaws. Fingers was all about push sticks, using only flat and straight boards, outfeed support, carving gloves, no jewelry, and using techniques that kept fingers away from bits and blades. And Trails meant having and maintaining an escape route in the event there was a fire, keeping aisles clear and floors clean so nobody tripped or fell, and proper lifting techniques.
Nowadays, we probably need a longer acronym. Personal safety can include avoiding online identity theft or treating coworkers with respect and dignity, hearing protection, and using VOC and formaldehyde-free finishes and adhesives, for example. It might also encompass avoiding machines when using prescription drugs (legally or illegally) or when suffering from depression or anxiety.
A new approach
Some things haven’t changed. The biggest problem with safety in the woodshop isn’t forgetting some basic rule. It’s still about managing to make the issue either interesting or automatic.
Somehow, discussions about personal safety always end up becoming self-righteous and boring lectures. The boss starts out well at the monthly meeting and everyone is paying attention, but five minutes in heads are bobbing and hands are hiding yawns. You can only tell people so many times that sharp cutters are safer, or to unplug the machine before changing the bit.
Instead, it’s wise to start breeding a culture in the workplace that treats safety as an essential element of lean manufacturing. Make it second nature, rather than something one needs to remember. For example, instead of telling an employee several times not to reach over a saw blade to retrieve cut-offs, the shop could install a large guard so that such an action becomes physically impossible. If somebody is feeling overly tired or distracted, make it culturally okay for him to take a break, or change tasks to something less dangerous. Have a dress code on the shop floor that includes safety glasses and allows no exceptions. Set up an alarm bell or flashing light that triggers if somebody removes a guard on a machine. Insist that nobody goes home until their workstation is clean, and give them enough time to accomplish this, on the clock, as a daily routine.
It’s a slightly different way of thinking about safety. Instead of posters and signs everywhere shouting time-worn instructions, it relies on quiet but intelligent consistency.
Obstacle courses
Woodshops can create an environment where almost every task with a degree of peril has some kind of safeguard built in, whether it’s mechanical or procedural. One simple approach is to create an obstacle that forces the operator to perform some task.
For example, a machine can be set up so that it won’t start until the dust collection port has been opened. Or perhaps parts can’t be slid across a table until a particular feather-board or hold-down has been installed correctly. An amateur woodworker had one of these on his table saw decades ago, long before we could video it with a phone. It attached to the table with a single bolt that was screwed into a hole he tapped in the cast iron top. When the saw wasn’t being used, it was installed backwards so that it blocked the path in front of the blade. It took just a few seconds to reverse it and make it operable: the bottom rested in the miter saw groove and the bolt locked it down.
It takes a little imagination, but most shops only have a handful of potentially dangerous machines, so it’s not an endless task. And the more sophisticated pieces of equipment such as CNCs and edgebanders already have some pretty advanced protection and a degree of remoteness built in. It’s the simple things that get us, such as drill presses, band saws and small table or miter saws. Outfoxing their dangers is usually a matter of turning something casual into a routine. For example, if you have a machine with a removable key for the On/Off switch, store it behind a push stick so that the employee has to physically pick up the safety device every time before he can turn on the machine. One can set up a drill press or router table with a pressure sensitive foot pedal so they stop running when the operator steps away.
It’s a relatively easy task to add built-in obstructions to jointers and router tables where the wood can pass through, but hands can’t get closer than three or four inches to the bit or knives. One can design the obstacle so that somebody has to use a sled or a push stick every time to complete the cut. Yes, there will be an occasional part that is too large or awkward to work that system, but in that case two things happen: the operator has to remove the device, making him much more aware of the danger; and the part is usually large enough to keep fingers out of the red zone.
The point here is not to give blanket solutions, but to start shop owners thinking about ways to remove the possibility of human error from each equation. Routines can be a big part of that. For example, the shop can have one or two people whose job is to check every single machine and tool for sharp cutters, bits and knives. That’s a lot easier and far more reliable than trying to train 30 employees how to recognize a dull edge.
Rules of engagement
Most of the suggestions above revolve around making it physically more difficult to do something in a dangerous way than in a safe way. Most of them also try to replace the need to remember with an automatic or built-in method. But we still have to think about what we’re doing, if we want to be safe. Most of the suggestions below are ones that the old hands may have forgotten and the new guys might not have heard yet. A few of them are intentionally vague, just so you have to think for a second.
- The edge against the fence needs to be straight.
- The work needs to be tight against the fence.
- The face of the work that rides on the table needs to be flat.
- Fingers should never be closer than a finger length to anything that can make them shorter.
- Constantly clean the floor in front of machines.
- Get a hair tie, or even a haircut.
- Jewelry and long sleeves can cause short fingers.
- Remove the chuck key before starting the drill press.
- Remove the chuck pins before starting the lathe.
- On variable-speed machines, take the time to learn about and select the correct speed.
- When ripping, remember that you’re not a catcher and stay out of the strike zone.
- Bits and blades can still cut you when they’re not running, so blow or brush dust away rather than sliding your hand across a machine.
- The next person probably won’t realize that you walked away from a machine without turning it off.
- Install featherboards before the bit or blade, so they don’t push the work sideways into the cutter.
- Short parts cause accidents. If necessary, use a sled.
- If possible, mill or shape on a wide board and then rip it to width.
- Set the table saw blade height so that the bottoms of the gullets clear the top of the work, and no higher.
- If you can’t clearly see each tooth, the blade hasn’t quite stopped.
- The table saw top is not a storage device: it should be empty except for the part being cut.
- Lift with your legs, not your back.
- Feed into the cutter. Climbing cuts on router tables are a recipe for disaster.
- Don’t feed parts between a router bit and the fence.
- Slow down, but not too much. If you’re feeding too fast or too slow, you’ll burn the wood, overheat the blade and/or motor, and possibly cause kickback. Going too fast on a band saw will usually cause the cut to wander. One exception is the jointer: going slow generally delivers a cleaner cut.
- Don’t pull work out of a cut. Hold the work firmly, turn off the machine and wait for the cutter to completely stop before removing the wood.
- Don’t smoke in or near a woodshop.
- Know where the first aid kit is.
- Where does everyone meet outside if the fire alarm sounds?
- And yes, it really is true: sharp blades are safer.
This article originally appeared in the August 2018 issue.
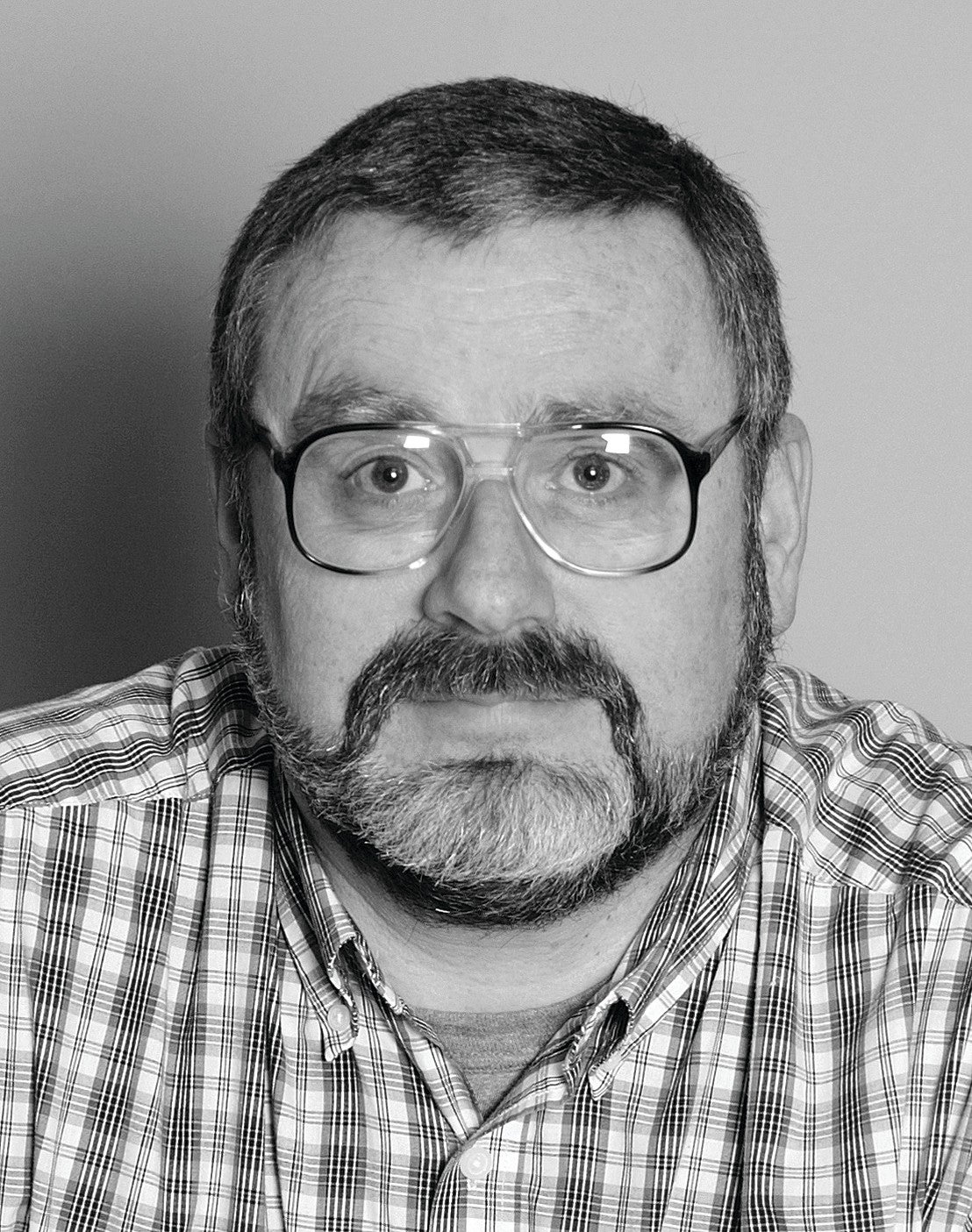