Magic in the air
Do you know the difference between positive and negative displacement or when kinetic energy is used in the woodshop? How about the ways that unidirectional and centrifugal compressors work? Neither…
Do you know the difference between positive and negative displacement or when kinetic energy is used in the woodshop? How about the ways that unidirectional and centrifugal compressors work?
Neither do I.
All those years as a cabinetmaker and, to me, the air compressor was just a big, noisy bottle in the corner that ran the nail guns, staplers, impact wrenches, drills, sanders and spray equipment. Who knew it had personality?
One doesn’t need to know much more than where the switch is located and how to dial pressure to be able to operate a pneumatic system. But the kind of mind that likes to turn 2-D drawings into 3-D furniture is usually interested in how things work, too. There’s a bit of magic in the notion of squishing a whole lot of air into a confined space and then harnessing it as it escapes to do our work for us.
So, for the inquisitive cabinetmaker, here’s a quick primer on pneumatics.
Single and two-stage
Most portable job-site compressors are single-stage. Such a device sucks air into the cylinder (and there can be two of them) as the piston moves in one direction and then forces that air into the tank as the piston returns. That is, it does all the work during a single stroke.
A two-stage compressor is usually a larger, stationary unit that stays in the shop. According to the Campbell-Hausfeld website, “two-stage compressors are much larger machines that are designed to be used by multiple users simultaneously because of their higher CFM output and their higher maximum working pressure of 175 psi.”
There are always at least two cylinders in two-stage units. The larger one is a low-pressure tank and the smaller one is under much higher pressure. The low-pressure piston sucks in air at the room’s regular atmospheric pressure (more on this in a minute). It then forces the air — often through a cooler, because compression causes heat buildup — into the larger tank. The high-pressure piston then forces that somewhat-pressurized air into the smaller tank at increased pressure. By compressing the air to 175 psi, there is enough volume in the tank to run two or three tools at the same time or to keep up with a spray booth’s air appetite.
The atmosphere of the planet is just a thin layer of gases (primarily nitrogen, oxygen, argon and carbon dioxide) that is held close to the surface by gravity. Ninety percent of it is less than 52,000 feet thick. That’s pretty thin when one considers that commercial airliners usually cruise at altitudes of up to 43,000 feet. Atmospheric pressure is, in simple terms, the weight of our planet’s air. The baseline for measuring it is sea level, because the pressure lessens as one climbs a mountain or ascends in an airplane. Engineers sometimes cringe at this simplistic explanation because it doesn’t account for variables such as heat or moisture. However, for non-scientists, a good working number is that the atmosphere weighs about 14.7 lbs. when measuring one square inch at sea level.
The volume of air used by pneumatic tools is measured in cubic feet per minute (CFM). That’s how much air will run through the tool when it is operating. The requirement varies according to how compressed the air is as it enters the tool. Imagine, if you will, a box that measures 12” in each direction. When the air is released from a compressor into this imaginary sealed box, it will be at higher pressure than the air outside the box. If the compressor is set for 100 lbs. per square inch (psi), then each of the square inches of surface inside the box — and there are 864 of them because there are six panels each measuring one square foot — is feeling as though there is a 100-lb. weight pressing against it. Well, technically, it would be a little bit less because the outside air, which is at 14.7 psi at sea level, would be pushing back a bit.
How big should my compressor be?
Some woodshop pneumatic tools are designed to run best at 100 psi, while others might prefer, say, 120. The owner’s manual will say how much air (CFM) a tool requires at a certain pressure (psi). That information is often listed on the tool, too, and it might list two or three choices: that is, the number of CFM at 100, 120 and perhaps 150 psi. A regulator on the air supply line or right on the tool can reduce, say, 130 psi coming out of a single-stage compressor, or 175 psi coming out of a two-stage compressor, to whatever the tool requires. Just turn the knob and dial the right pressure.
When figuring out what size compressor to buy, the manufacturers have made it relatively easy for a woodworker by sticking a label on every unit. This lists the CFMs that it can produce. Most salespeople will tell you to figure out your requirements by adding up the CFM ratings on the tools you will be using simultaneously (maybe one worker will be running a nail gun while the other is spraying lacquer?) and then buy a compressor with one-and-a-half times that maximum capacity. The idea is to make more air than is needed, so the pumps don’t have to run constantly to keep up. If a pump has to work too hard, it will get hot and that can eventually cause the seals to fail.
Maintenance
Tommy McGuire has run McGuire Air Compressors in Piedmont, N.C. (www.industrialaircompressors.biz), since 1981. Through the years, he and his staff of Certified Service Technicians have worked on compressors from 1/2 hp to more than 700 hp. When it comes to a woodshop maintaining its pneumatic equipment, McGuire notes that there are a few basic things that need to be done on a regular basis (below). And he has this to say about lubrication:
“Compressors may be shipped without lubricant in the crankcase. Before starting the compressor, add enough lubricant to the crankcase to register between the high and low marks on the dipstick or on the bull’s-eye sight gauge. Use the specified lubricant or consult the manufacturer for recommendations. Certain synthetic lubricants have proven, under extensive testing, to minimize friction and wear, limit lubricant carryover, and reduce carbon and varnish deposits. They will support the performance characteristics and extend the life of the unit and they are highly recommended. Refer to the manufacturer’s specifications to determine the correct amount of lubricant and viscosity to use for your model and application.”
McGuire recommends that one person in the woodshop be designated to maintain the pneumatic equipment so that there are no oversights. Here’s his recommended maintenance schedule for a woodshop running a commercial compressor:
• Every eight hours of running or once a day:
Check and maintain the lubricant level. Discoloration or a high reading could indicate the presence of condensed liquids. If the lubricant is contaminated, it needs to be drained and replaced. One also needs to drain the receiver tank, the drop legs (feeds coming off the main line) and the traps in the distribution system. Make sure nobody has removed the safety guards and check for any unusual noises or vibration. If your unit is pressure-lubricated, check that there’s 18 to 20 pounds-per-square-inch when the compressor is at operating pressure and temperature. High-pressure rated compressors should maintain 22 to 25 psig of lubricant pressure. While you’re at it, visually check for lubricant leaks.
• Every 40 hours of running or once a week:
Make sure the pressure relief valves are working. Clean the cooling surfaces of the intercooler and compressor. Check the compressor, pipes and hoses for air leaks. Inspect the lubricant for contamination and change it if necessary. Clean or replace the air-intake filter and do this more often under humid or dusty conditions.
• Every 160 hours or once a month:
Check the belt tension.
• Every 500 hours or once every three months:
Change the lubricant. You should do this more frequently in harsher environments.
Also check the lubricant filter if you have a pressure lubricated unit, again doing this more frequently in harsher environments. Torque the pulley-clamp screws or jam-nut to make sure nothing’s coming loose.
• Every 1,000 hours or once every six months:
Change synthetic lubricant. Inspect the compressor valves for leakage and/or carbon buildup. The lubricant sump strainer screen inside the crankcase of pressure-lubricated models should be thoroughly cleaned with a safety solvent during every lubricant change. If excessive sludge buildup exists inside the crankcase, clean the inside of the crankcase as well as the screen. Never use a flammable or toxic solvent for cleaning. Always use a safety solvent and follow the directions provided.
• Every 2,000 hours or once a year:
Inspect the pressure switch diaphragm and contacts and also have a look at the contact points in the motor starter.
OK, you’ve stayed with us this long, so here are quick answers to those questions we asked up front.
The difference between positive and negative displacement in compressed air is that the former traps air in separated segments and forces it into a tank, while the latter provides a continuous flow.
Kinetic energy is used in the woodshop when an air compressor converts power from an electric motor or a diesel or gasoline engine into compressed air that, in turn, is used to do work.
And unidirectional compressors use a piston, while centrifugal compressors are found in larger units and use an impellor (fan) to move and compress the air.
This article originally appeared in the June 2014 issue.
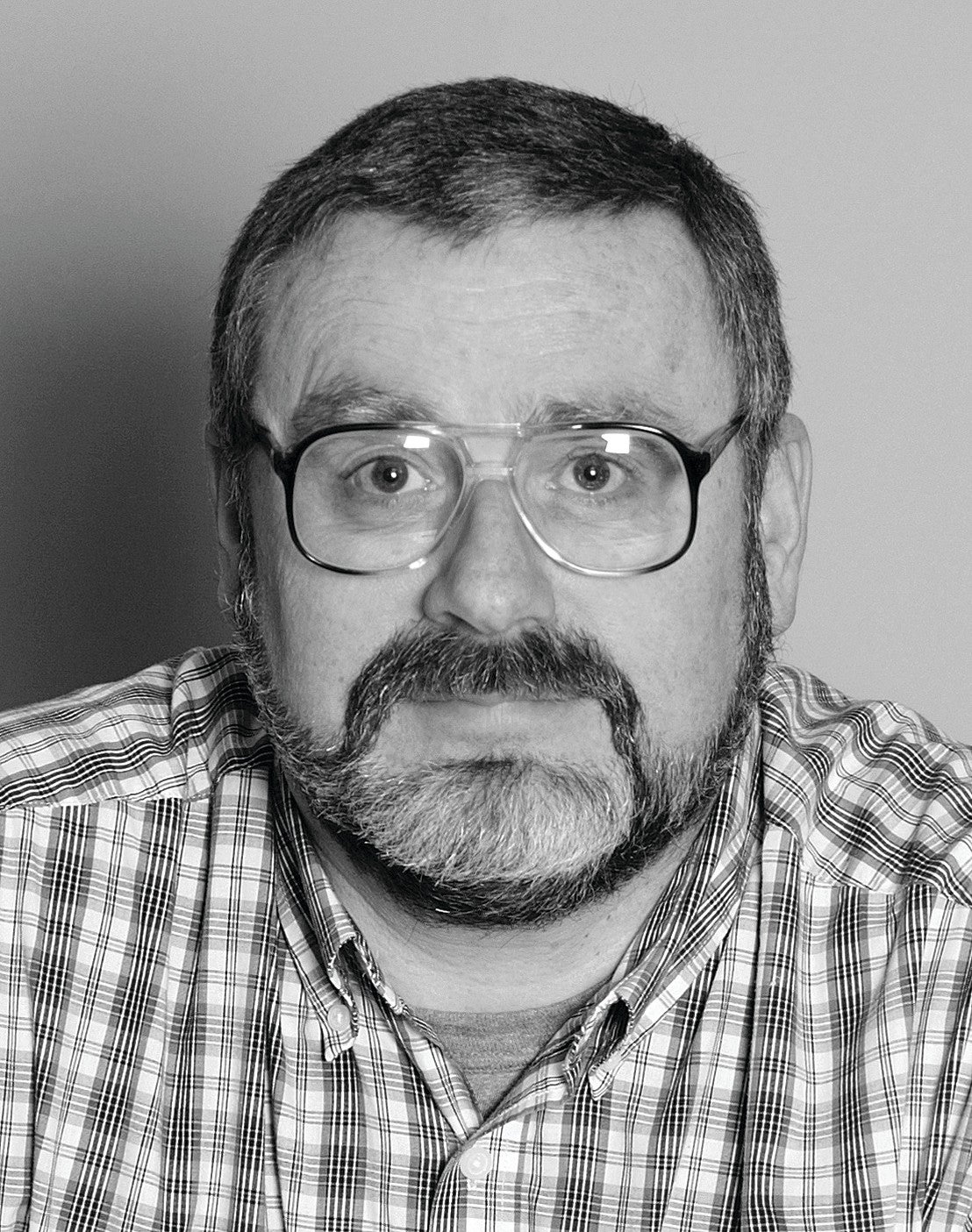