Living on the edge
Every now and then a customer comes in who wants something a little different. One of the most requested items is a table with live edges — where the bark…
Every now and then a customer comes in who wants something a little different. One of the most requested items is a table with live edges — where the bark has been removed, but the edges haven’t been machined straight.
In some parts of the country, woodworkers get to play with immense slabs of redwood and cedar, but most of us aren’t so lucky. We only occasionally come across a few thick boards with some decent live edge. To use those gems to build something spectacular, one needs to create most of the tabletop with standard milled boards and reserve those dramatic natural edges for the outside.
The maple table shown here is typical. If you’re thinking of branching out and offering something more than square boxes to your customers, this project brings up a whole lot of issues that might spare you some grief. And walking woodworkers through a specific project seems like the best way to share some ideas on how to deal with something out of the ordinary.
Unusual stock offers several challenges that require a little thought and planning. For example, the three main boards here were 9/4 and highly figured. Of those, the two outside boards with live edges has lots of bird’s-eye and the large centerboard had knots, spalt, heart and sap, plus a host of minor defects such as checking and voids. As if that wasn’t enough, the stock for the two “beams” in the table top was quilted. To the kind of woodworker who spends hours sorting through bins at the lumberyard to find uniform, straight, knot-free stock, these boards would have looked like firewood.
The test here is to match your tools and experience to the grace of nature, to find a balance between the conformity that makes us comfortable and the erratic dynamism of growth. You’ll need to marry nature’s art to man’s craft.
Acclimation
The initial step in working with challenging materials is achieving some stability. Our three wildest boards were harvested near the Olympic National Forest in Washington, sometime during the 1990s. They were air-dried locally after being run through a band mill. A few years later, they were transported to the high plains of western South Dakota, where they were stored in an outbuilding for more than a decade. So they grew in one of the wettest spots on the continent and lived in one of the driest.
The beams in the tabletop were made from well-behaved, kiln-dried, Appalachian soft maple. Although they, too, are figured (a lot of quilting), these boards were relatively stable. Mechanically dried to 6 percent, they were then stored at about 12 percent ambient humidity until they were shipped to our shop, where the air is a bit drier.
Considering the dramatic differences in their origins, all of the boards were allowed to acclimate at the shop for a couple of months before any milling began. This allowed them to reach equilibrium in a relatively stable environment. If they were going to change shape, the plan was that they would do so during this period before they were milled, rather than after they arrived in the client’s dining room.
A moisture meter test on the Washington lumber registered 9 percent on arrival and 7 percent a month later. The Appalachian stock was at 7 percent and stayed there. However, the test was run with a pinned moisture meter in the wide faces of the boards: a more accurate test would have been to crosscut the boards and immediately test the newly revealed cut end. That was not an option, as our table was to be as long as possible and we didn’t want to crosscut any of the stock.
Flat first
Erratic grain can often be an indication that one might be working with reaction wood. This is either compression or tension wood that will release energy in unpredictable ways as it is cut. Figured wood is often the result of abnormal growing conditions, where wind, gravity, drought or some other external factor (or combination of factors) has dictated the way in which the wood is formed.
Before running a figured board across the table saw, the first defense against reaction is to make sure that the bottom face is relatively flat. But figured lumber doesn’t like jointer or planer knives: it tends to chip and tear out. A really coarse grit belt on a portable belt sander (40 or lower) is a good way to eliminate high spots in a hurry. A stationary drum sander or wide belt sander is a better choice, as it will work on the entire width of the board.
If a wide sander isn’t available, very gentle passes (1/64”) on a wide jointer with sharp knives can shave the high spots. Scribble pencil lines all over the face being jointed, so that the high and low spots are more apparent after a pass. The pencil lines on the high spots will, of course, gradually disappear. If the wood is lightly dampened (but not wet), this can help, but be sure to unplug and then dry off the jointer bed and the board as soon as possible to avoid rust. Reverse the feed direction for the second cut and compare the results to the first pass. Sometimes changing direction can help, but with a lot of figure it’s hard to make grain work for you.
A hand plane can shave more gently than a thickness planer or jointer, but, man, is it work. Make sure the iron is very sharp, go with a high angle (55 or 60 degrees) and set the mouth thin. You might also consider a back bevel of maybe 10 degrees, but sometimes this can introduce a little chattering if you’re not used to hand tools. A card scraper works well on figure, but removes such a small amount of stock that it’s not a viable solution.
If the boards are wider than the jointer bed, one can always make an initial cut on the band saw and then joint the wide faces (and not the edges) of each of the two halves. One can then reassemble the board using the band-sawn kerf or joint the edges and use biscuits. If the band-sawn kerf will be used, it helps if the cut has followed a grain line: the resulting joint will be relatively invisible.
One mistake often made when judging whether a board is flat is to place it on a surface such as the table saw bed to see if it rocks. If it doesn’t, one might assume that it’s flat enough to saw. But that can be a fatal assumption. The board can just be suspended on three or four high spots. As the cut progresses, those dynamics can change and if the middle of the board nearest the blade then sags, it can bind on the teeth and cause kickback. The best solution is to eyeball the surface using a metal straightedge, mark the high spots and eliminate them by sanding or hand-planing.
Perhaps the best solution of all is to run the boards through a wide belt sander and this can be hired if the shop doesn’t own one. Be aware that a sander isn’t a jointer: if your board is bowed, it will come out smooth with the wide faces parallel to each other, but it might still be a little bowed.
Straight thinking
With the wide faces of your boards flat, it’s time to work on the long edges. The idea here is to harvest the live edges while creating a board that also has one long, straight edge that can be glued to the rest of the table top. As there are usually no straight edges to run against a table saw fence, you’ll need to create some. The simplest way is to attach the stock to a plywood base and feed it through the table saw, running the factory edge of the plywood against the fence. Attaching the board to the plywood can be done with screws driven an inch or two in from the ends, if there is a little waste available (that is, if you don’t need the full length of the board). One can also hot-melt-glue the board to the plywood: the suggested method here is to apply a dab of glue about every 16” along the board and use a pencil to mark the locations. The pencil marks allow the glue to be found and the two parts can then be separated with a chisel and mallet after the table saw cut is made. The disadvantage here is that glue residue needs to be sanded or scraped and also in some species one might have some tear-out if it sticks too well to the board.
Another option is to bring the boards to a hardwoods retailer or sawmill that operates a laser-guided straight-line ripsaw and pay them to do the job. But the easiest and cheapest method is probably to go with the plywood.
Normally, one would rip boards using a thin-kerf blade with perhaps 24 teeth. But because of the thickness, length and weight of these boards, we find that holding them on edge against the fence on the jointer later on can be difficult. So we like to get as clean an edge as possible on the saw. For that reason, we use a more precise, full 1/8” thick blade. Because of resistance, the cut needs to be made in a few incremental passes. After each pass, the blade can be raised about 1/2”. It takes a little longer, but the kerf is definitely cleaner. For the very last pass, we move the fence about 1/64” to the left, and this shaves the cut edge.
A full-thickness riving knife on the saw helps make sure that the kerf in this difficult stock doesn’t bind on the blade, causing kickback.
Jointing option
If your boards are manageable and you have access to a large jointer, then straightening the edges for glue-up isn’t a problem. However, if you only have a 6” or 8” wide jointer and you’re building a dining table with long, heavy boards, here’s a suggestion: clamp a metal straightedge to the board and barely clean up the saw marks with a long straight bit chucked in a portable router.
To establish the location of the straight-edge, install the bit and, with the tool unplugged, place the router base on the board. Rotate the cutter so that the carbide insert isn’t butting against the board and move the router so the shaft of the cutter is tight against the board. Mark the location of the router base, doing so at both ends of the board and also somewhere around the middle. Clamp the straight-edge to these lines. You might need to clamp some kind of low-profile support at the midway point, too, in case your straight-edge flexes. This can be a thin stick that is flat enough so that it doesn’t interfere with the router’s travel. Draw pencil marks along the edge of the board. Then take a very light pass. If all your pencil marks are gone, the edge should be flat and true.
Glue-up
Leave your boards as long as possible for now to avoid snipe. Don’t cut the table top to length until all the sanding on the wide faces is done.
Draw pencil lines across the top faces of the boards about every foot along each joint, to locate No. 20 biscuits. By doing this, the top of the table will be relatively even. If the boards are slightly different thicknesses, any discrepancies will appear on the bottom. Remember to stay far enough away from the ends to ensure that your final trimming doesn’t reveal half a biscuit. If the boards are more than 1-1/2” thick, consider doubling up on the biscuits. In that case, stack them one above the other with about 3/8” between them.
In general, it’s best to glue and clamp two boards at a time, waiting overnight for them to cure. That makes the process much more manageable, especially with doubled-up biscuits.
If possible, leave the bark on when the boards are being edge-glued. It acts as a natural pad to protect the sapwood underneath from the pressure of the clamp jaws. Use wooden hand screws to keep the bar or pipe clamps close to the board surface or the uneven edge could cause the clamp to open the bottom of the joint when pressure is applied. Alternate the clamps along the length of the joint (one above the boards, the next below), to spread the tension more evenly. And on the far end of the bar clamp, place the glue block low on the edge so that pressure is exerted toward the bottom of the board.
Flattening wide assemblies
My old friend (and impressive woodworker) Ken Froelich says that the best way to smooth a large table top is with a series of hand planes and scrapers. While he’s doing that, I like to load my projects in a pickup truck and take them to a local shop that has a wide belt sander. This machine can do in 20 minutes what it takes Ken three days to do with hand tools. And, frankly, I think it does a better job.
Be nice to the sander’s owner and use a scraper to remove as much glue as possible before passing the assembly through his/her machine. Belts are expensive.
The only drawback with most wide sanders (belt or drum) is that they are limited to 36” wide boards. I like to make dining tables that are a bit bigger than that. The table top shown here finished out at 1-9/16” thick, 42-1/2” at its widest, and 89” long when trimmed. Rather than make up two equal halves and join them symmetrically after sanding, I like to offset the final joint so it isn’t obvious. In keeping with that, this top was run as a 34” wide subassembly and an 8-1/2” wide separate board. It takes two or three people to handle an assembly this large, as it needs to be fed level with the floor. If it goes in tilted there will be snipe or a safety mechanism on the machine will shut it down. It’s also important to have somebody at the infeed side to make sure the workpiece is tracking properly through the machine. Working this close to the sander’s tolerance (within 2” of its 36” maximum width capacity) means that a small tracking error can accumulate over the length of the board and jam it against the sides, which will trigger the sensors in the machine that shut it down.
Because the biscuits were registered to the top faces of the boards, the top is probably flatter than the bottom. So, the initial passes need to be made with the bottom of the tabletop facing upward, so that this face is sanded first. The sander’s owner will suggest grits: if not, then start with 80 and work down to 220.
Removing bark
Most people working with live edges like to remove all of the potentially loose bark and bring the surface down to the sapwood. That way, bark doesn’t fall off during the next heating/cooling cycle in the client’s home, when the bark and sap expand or contract at different rates. (For some rustic furniture the bark is kept in place, but it usually needs to be stabilized using glue and finish nails.)
Removing bark without damaging the wood can be challenging, depending on the species. Plastic shims work well: one can tap the fat end with a hammer and the soft plastic doesn’t do much damage. A putty knife works in some situations, when one can slide the leading edge under the bark and twist the knife for leverage. On burls and other nice shapes, use a series of nylon brushes chucked in a corded drill. Cordless ones don’t generally have enough power. Wire brushes are too harsh for this delicate step. Dico Products of Utica, N.Y., makes 4” diameter gray 80-grit, orange 120-grit and blue 240-grit nylon brushes that are carried by most hardware stores. If necessary, follow up with Dico’s cup brushes: they’re a little gentler, and they can get into smaller places.
Some woodworkers use a pressure washer to remove bark. It seems rather violent and, of course, the wood needs to thoroughly dried afterward, but several people have reported good results. Practice on some waste material.
While Mother Nature was the artist, we are of course still artisans, so we are free to bring some of our own skills to the job. I like to use rasps, files and even an orbital sander to knock off pointy parts that might dig into a hip or to blend in areas that are a little out of character.
Closing thoughts
One can formalize a live edge top by using the leg set as a sort of picture frame — a way to tame the top and make it acceptable in an otherwise traditional environment. However, I don’t like going overboard here. Some builders like to attach live-edge tops to sparse metal legs and, while that might work in the stark environs of a minimalist room, it isn’t very warm or enticing in a normal dining room. I like to use dimensioned lumber to make sturdy legs that add to the work without interfering too much with one’s appreciation of the visual feast that is the tabletop. But I also like to remind people that nature is the artist and that can be done quite nicely by incorporating a couple of pieces of live edge in the legs. Suspending small natural panels in these formal frames is a great use for cut-offs, too.
When it comes to table-top finishes, there is almost always enough natural color in the boards, so I rarely stain. My preferred topcoat is a clear, oil-based, polyurethane, satin, floor varnish. This brings out the natural color, has enough hardeners to endure decades of dining and cleaning, is easy to renew, avoids glare and is widely available.
This article originally appeared in the February 2015 issue.
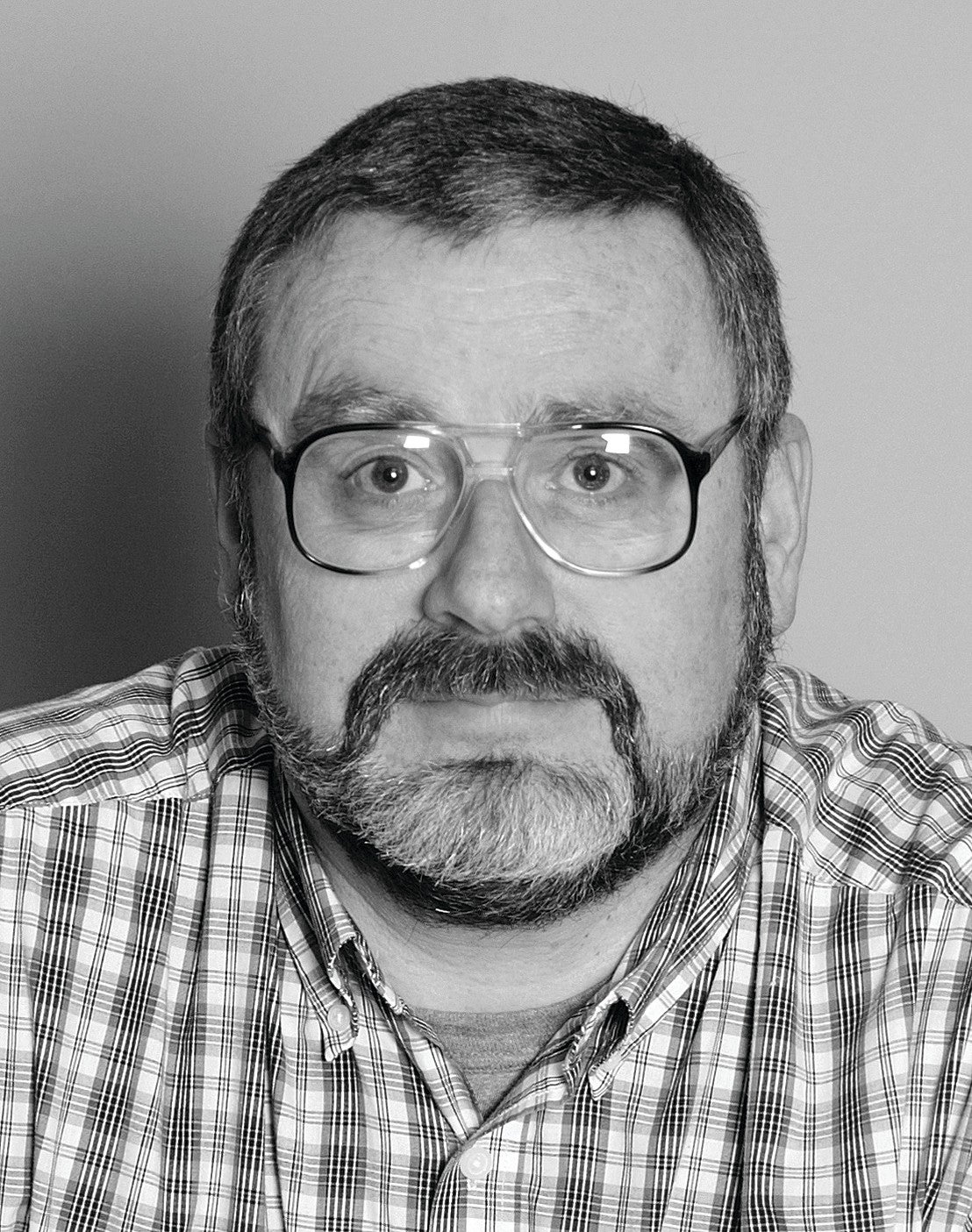