Living in Tomorrowland
Technology is advancing at a mind-boggling speed. For example, an impressive number of cars can park themselves now and driverless vehicles are just about here. In the workplace, the odds…
Technology is advancing at a mind-boggling speed. For example, an impressive number of cars can park themselves now and driverless vehicles are just about here. In the workplace, the odds are that most of your own car was made and assembled by robots, not human hands. A single cellphone today has more computing power and memory than NASA’s rockets did when President John F. Kennedy pointed us toward the moon.
So it’s no surprise that even the smallest woodshops are putting programming and robotics to work at an unprecedented rate. The trick is to decide just how much and which parts of the operation should be automated now and what can be done in the future. We know that things will change rapidly as technology evolves, so any system installed now needs to be able to grow with us. The rule of thumb is to start small, but be prepared for expansion.
In the world of CNC routers, the term “small format” generally means low-powered spindles or even over-the-counter routers and a physically small work area. For many shops, that might indeed be all that’s needed, depending on the type of work being done. For carving, engraving and creating accent panels, a small workstation might just meet both budget and space restraints and the learning curve on such a setup can be quite short. But if the shop wants to process panels, a bigger bed is in order.
A basic small format model, outfitted with a standard router, starts at about the price of a laptop computer. The cost of entry-level units with small, dedicated spindles begins at about twice that. For example, the basic AutoRoute Pro from Axiom Precision (axiomprecision.com) comes with a 24” square worktop and is listed at $5,499. And the ShopBot Desktop is in the same price range, beginning at $5,145. Buyers can then choose to add a router to the Desktop for $360 or a spindle for $1,595. One nice feature is that the Desktop is designed to grow as a shop’s needs develop. For example, it uses the same control and software as the company’s full-sized tools and a number of bed sizes are available.
For smaller shops that are building bigger casework, the work area needs to be large enough to accommodate sheet stock and the spindle and movement motors must be rugged and large enough to handle the workload. Entry-level machines with full 48” x 96” beds and cutting speeds in the hundreds of inches per minute are still surprisingly affordable for a shop that can keep the machine busy.
Smaller woodshops tend to look at adding CNC capability as a way to boost production without hiring lots of people or adding several other workstations. The most obvious potential benefit is an almost immediate increase in production volume. A secondary gain is better overall quality due to better machining. The latter can sometimes take a bit of time to kick in because there’s a learning curve as there is with any new equipment. And there are a few other little bumps in the road that a shop owner needs to consider before committing to a new CNC station.
Growing pains
Time is as big a part of the investment as cash. Beyond the initial installation of the machine, somebody on staff is going to have to learn how to operate the specific CAD (design) software that comes with the router and also how to run this particular machine. The latter often includes becoming familiar with a separate CAM program that tells the machine what to do.
While people are training, they’re not using existing machinery to get projects out the door and pay the bills. The shop needs to have sufficient cash (or at least credit) resources in place to handle the transition.
It’s a good idea to train at least two people in case one leaves, gets sick or goes on vacation and that adds to the initial downtime. Training takes time, even with the best programs. Software has come a long way in recent years and most of the entry-level programs are now very intuitive and learned easily. Building standard boxes on a screen has become routine (once one learns a little of the terminology) and a shop can very quickly build up a library of the products that it makes most often. Much of the design process is template-oriented: one just chooses from existing options, pops the cabinets in place on a floor plan and makes minor alterations if necessary. That’s especially true if the woodshop is outsourcing elements of each job: larger suppliers usually have a menu of products that dovetails nicely with the software program being used in the woodshop. And for parts being made in-house, most programs automatically generate cut lists and optimize (figure out the most efficient way to lay out or “nest” parts on a sheet of plywood).
Designing custom shapes can take a little time to learn – curves, offbeat sizing and so on. These are usually the elements that will be built in-house as opposed to being outsourced and this is where a CNC router can really shine. But it still takes some practice and experience before tackling highly technical design, unless the shop hires somebody who already has these skills. To get things up and running quickly, the ideal candidate is probably not a recent graduate from a technical college, but rather somebody who has also spent some hands-on time on the floor of a woodshop and is familiar with cabinet CAD. The machine supplier can offer some training and there are lots of online resources, but cabinet or furniture shops are by definition “custom,” so each one will need to figure out how to do things their way. That takes time.
Then there’s the physical part of the initial setup. Regular job production is going to be disturbed because of electrical and dust collection connections, plus physically moving things around to make room for the new machine – and both its infeed and outfeed spaces. There will also be connections to computers, scanners etc., and other impacts on the office such as perhaps designating a workspace and terminal specifically for CAD. All of this activity can ideally be scheduled for the slowest time of the year, but even then it still disrupts the flow of projects through the shop.
Beyond time and training commitments, a woodshop owner also needs to factor in the ancillary costs of upgrading to CNC. Yes, there are electricians and ductwork and maybe even a wall to knock down or move, but there are also some less obvious ongoing expenses. For example, there will be an impact on sheet goods inventory levels and shipping costs, the light and heat bills as more jobs are being processed, wages, insurance, interest on a loan or a lease payment, maintenance and new CNC tooling, just to mention a few.
CNC software
The transition from traditional machining to making parts on a CNC router is most likely going to be more gradual than planned. It will take a shop some time to understand what existing tasks can be performed on the new equipment. But once those are identified, the team can begin to explore new areas of production.
In shops that build highly individualized furniture, CNC software that includes advanced 3-D modeling can potentially eliminate traditional prototype building. Being able to see things in scale from different angles on a screen and instantly reshape them is a creative tool that dramatically enhances design possibilities. Yes, we’ve had 3-D software for a long time, but today’s programs are exceptionally fluid. They allow the designer to consider what’s possible, rather than what’s merely convenient. They open the door to adding more art to the craft.
Software can make a huge difference in the financial return on a CNC investment, especially for smaller shops. While large casework manufacturers can afford to experiment a bit and design custom software solutions, smaller shops need to get the machine up and running right away and keep it working profitably. That means they need access to both CAD and CAM programs that are immediately functional, at least moderately customizable, easy to use and able to grow with the needs of the business. They also need to be comprehensive, tackling several aspects of the production process from design and rendering through bids, cut lists and even the ability to deliver timing and part production reports.
The term “open architecture” means that a router will work with virtually all industry standard CAD-CAM programs.
It’s essential that a woodshop entering the CNC arena performs due diligence regarding its software options. Among the more reputable programs (some of which are CAD, some CAM, and some both) are Alphacam and Cabinet Vision from Vero Software (verosoftware.com); EnRoute (enroutesoftware.com); Autodesk’s ArtCAM (artcam.com); KCD Software (kcdsoftware.com); CabinetPro (cabinetpro.com); CabMaster (cabmastersoftware.com); CIM-TECH (cim-tech.com); MasterCAM from CNC Software Inc. (mastercam.com); Microvellum (Microvellum.com); Mozaik (mozaiksoftware.com); NUM (num.com); Rhinoceros (rhino3D.com); and Vectric’s suite that includes VCarve and Cut2D (vectric.com).
Many of these programs can be leased rather than purchased, which can affect both the shop’s budget and future updates to the software. Several companies offer free trails of their software, so a designer or manager can test drive a few different packages and find the best fit. Virtually every supplier offers comprehensive support packages that are structured in a few different ways: for example, you might have free support for a certain length of time, or a limited number of contacts, and after that a paid support package kicks in. Or all your support and education might be included in the lease. Check the fine print and compare apples to apples when purchasing. For example, what constitutes a support incident? And does the per-incident price include a follow-up conversation? Most software manufacturers also have user forums where a potential client can visit with current users, or just eavesdrop on chat-rooms prior to purchasing, and witness a good cross-section of the opinions of other woodworkers.
Support access is an issue, too. Can you talk directly and immediately to a real technician, or do you first have to exhaust several FAQ menus and various website pages while your crew stands idly by the silent machine, waiting for an answer?
Some design packages lean more toward cabinet jobs, while others court your creative instincts, so it’s important to be very clear when speaking with a salesperson and explain exactly what you expect the machine to help you produce. If you’re not quite ready to answer that question yet – if you don’t know what kinds of projects the shop will be building in a year – then a short-term lease might be a better move than buying a complete CAD-CAM package.
Some programs run on Windows only, while others run on Mac or Windows. That’s not as big an issue as it used to be. Most output can be viewed on either platform, and saved to either Microsoft’s ‘the cloud’ or Apple’s iCloud. A lot of CAD operators, especially those who attended a design-based college program, are more familiar with a Mac environment. If they are presented with a software choice that only runs on Windows, their immediate instinct might be to discount that option. However, that could be hasty: the platforms have grown quite similar over time and, though there are still some intuitive differences where one’s fingers begin to wander toward the wrong keys, the chasm is not what it used to be. Many programs will allow a user to import work done on a Mac and tweak it in Windows. Ask the salesperson, search the forums and check with other designers before saying no.
Or yes.
If a shop belongs to a professional woodworking association, it’s a good idea to ask at a monthly meeting what other regional woodshops are using for CAD and CAM: it can be handy to have somebody close by who is familiar with the programs plus local hardwood or sheet stock suppliers, and also the area’s outsourcing suppliers and the software that they use. Choosing software can be a bit overwhelming, and asking opinions can help reduce the number of choices.
One of the most comprehensive online resources for a woodshop looking at CNC software or hardware is the Woodshop News resource guide. On the website (woodshopnews.com), click on ‘Resource Guide’ in the horizontal menu bar near the top of the page and then click on ‘CNC Equipment & Services’ in the left-hand menu.
Sometimes the initial choice will be made for you, as many machine suppliers bundle software with the purchase of their hardware. That’s a good thing: the router manufacturer has already ascertained that the program is going to work well with the equipment, and if there has been some history any glitches will have been addressed. For example, ShopBot currently includes VCarvePro and Autodesk’s Fusion 360 with a new tool purchase, and the company also offers options on Vectric’s Aspire and Rhino 3-D (the latter is a very popular general-purpose 3D modeling program).
CNC hardware
For smaller shops, the first CNC purchase is most likely to be a single-head unit and the first big choice will be whether to invest in a 2.5-axis, 3-axis, 4-axis or 5-axis machine. That’s almost entirely based on the type of work being done. More axes means that the tooling (cutter) can approach the work from more angles. That can be a real boon with complicated profiles and odd shapes. But if all you’re doing is releasing rectangular panels from flat sheet stock, it’s hard to justify the investment in a setup that is capable of milling three-dimensional cogs. One option for shops on the cusp (milling flat parts now and possibly planning for more complicated work later) is to buy a 3-axis head that is capable of supporting an aggregate head down the road. An aggregate lets the operator install tooling at a different angle other than vertical.
Some CNC centers have a fixed bridge and one or multiple tables that can move parts around. Some have a moving gantry that travels while the work remains stationary. The size of the parts being made has some influence on the configuration you choose. And some tables offer sectional dust collection that can be rearranged for optimum performance.
Give serious thought to tool changers, too. They allow the operator to complete all of the setup before the job starts (usually up to about a dozen different tools). During the milling process, the machine will then automatically select, change and employ the right cutting profile as needed, without shutting down. This can really speed up production. On very small machines, tool changing is done manually, one tool at a time, but some form of automated tool changing is available on a surprising number of entry-level models.
High quality, maintenance-free, brushless servo or stepper motors are used to move the spindle on virtually all routers nowadays, and their action is very smooth. If you’re looking at used equipment, check whether its motors can be updated. Have a look at the hold-down mechanisms on various machines, too. There are several after-market mechanical, pneumatic and vacuum-based products that can simplify this, especially for oddly shaped work.
This article originally appeared in the October 2016 issue.
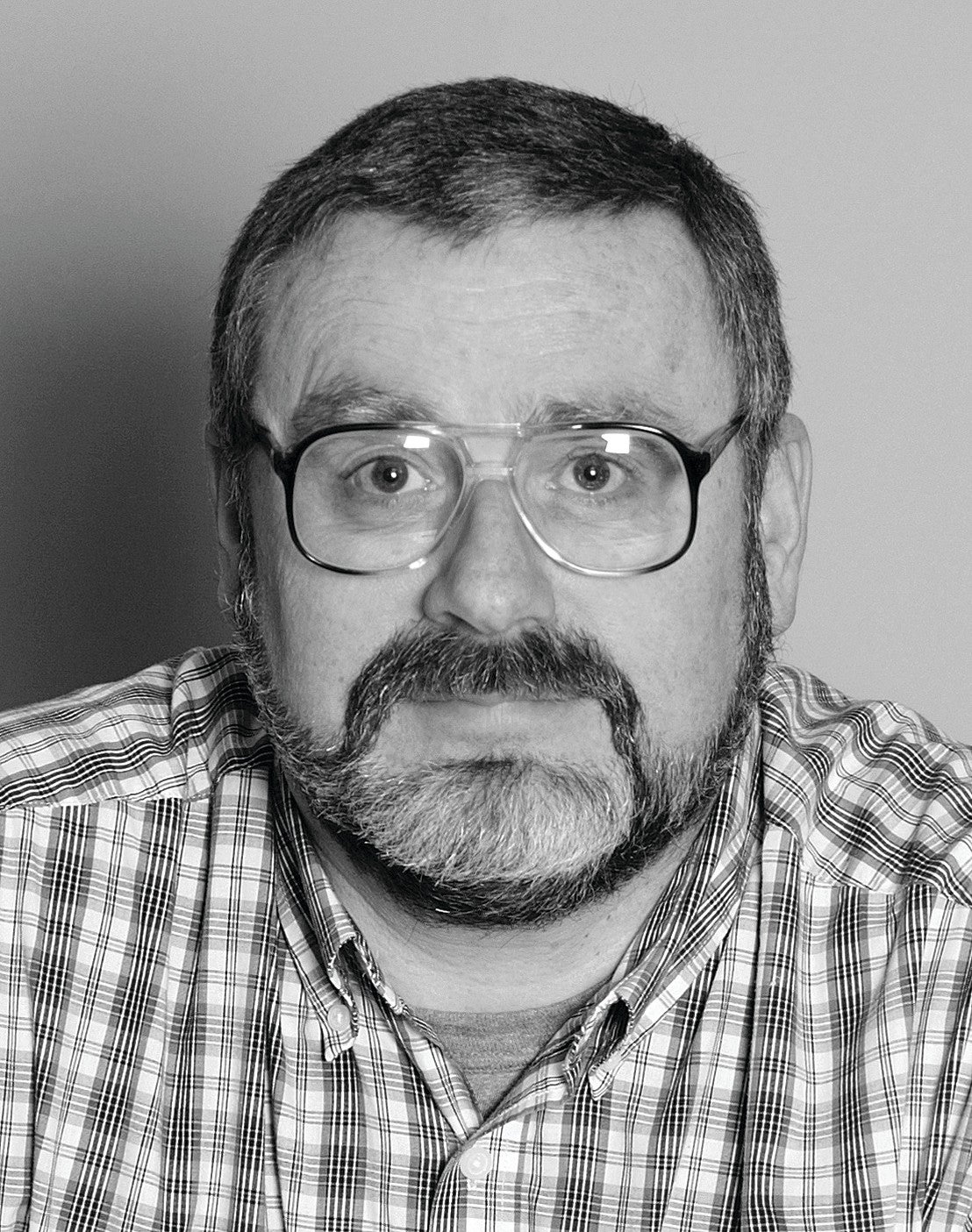