Lean for the long haul
You would need to be well into your 90s to remember the stock market crash of 1929, which started the Great Depression. But the next worst thing, our own Great…
You would need to be well into your 90s to remember the stock market crash of 1929, which started the Great Depression. But the next worst thing, our own Great Recession, is still pretty fresh in our minds. It began in late 2007 and a key factor in its inception was the bursting of the U.S. housing bubble. For woodshops, the subsequent decimation of the construction industry has been dramatic. For those who survived, a new culture in management has evolved, one that takes very much to heart an adage quoted by Ben Franklin: a penny saved is a penny earned.
That concept — the idea of streamlining the manufacturing process in search of savings — is at the core of one new way of thinking. Called lean manufacturing, it began with a Toyota business model and has slowly pervaded all aspects of the U.S. economy, including even the service sector.
The most quoted slogan associated with lean culture is: “If it doesn’t make dollars, it doesn’t make sense.” But there’s a little ambiguity about the actual goals of the philosophy. Most analysts agree that its primary function is to increase profits, but others insist that the ultimate goal is to better serve customers and that lowering costs is just one way to do that. However, lean practitioners in our industry agree that improving the quality of cabinets, furniture and customer service is at the core of the concept. And one of the best ways to improve both quality and service is to eliminate waste.
Waste not, want not
Lean manufacturers define waste in several slightly different ways. The best definition is that waste is the use of any time, shop space, utilities or other resources that don’t add value to what the customer receives. The Japanese model for lean manufacturing identifies three types of waste: muda, mura and muri. In essence, muda refers to physical and temporal waste (materials and time). Mura describes uneven operations, where the segments of production are not in sync and muri talks about overburdening either people or plant (machines). What a woodshop owner needs to keep in mind here is that these concepts were developed for large mass-production facilities and the challenge is to find ways to apply their principles to small custom shops.
Perhaps the most effective way to do that is to reduce the amount of time spent on each activity. Henry Ford was the first manufacturer to implement the production line on a large scale and a couple of tenets of his methodology are key here. Letting cabinetmakers make cabinets, instead of asking them to sweep the floor or haul components to their workstations, would fit both the Ford and the lean parameters. Having components on carts immediately on hand, and perhaps ordering some parts already made, might also reduce the time it takes to build a cabinet. Upgrading from hammer and nails to pneumatic staplers is a simple example of efficiency, while exploring the option of wood welding to cut down on clamp downtime is a more complex candidate. Having parts prefinished before milling and assembly (as in sheet goods that arrive at the shop with a coating already applied) can dramatically reduce the time it takes to bring a cabinet through the building process.
Time isn’t the only component that lean managers examine. Cash is a valuable asset, too, and sometimes we have too much of it tied up in inventory. Lean manufacturers try to produce only what customers demand and to stay as close to that edge as possible without leaving the customer short of product. There’s a fine line here and it is very dependent on how a shop is supplied. If your supplier can deliver sheet goods, hardwoods and hardware in hours or even the next day rather than in weeks, why would you tie up cash and shop space in inventory? Let the warehouse be your warehouse.
Shops in rural locations, far from a supplier, have fewer options here than woodshops in major cities. For those rural shops, a more creative solution must be found. For example, they can streamline parts so that all of their stiles are the same width so they don’t have to carry wide widths of raw stock. Or perhaps the number of species they offer can be reduced, so they don’t have to warehouse so much veneered sheet stock.
For companies that supply stock cabinets in addition to their custom work, adding a week or two to the user’s order time might allow the shop to purchase components only as they are needed, rather than having to inventory standard size boxes, doors or drawers. If the supplier only takes a few days to fulfill a component purchase order, why not ask the client to wait that long?
Never satisfied
Lean proponents have identified several states of existence that together form their philosophy. These are being lean, continuing to become leaner, thinking lean and doing lean. The idea here is that the culture should be pervasive and inhabit all aspects of a business, and consequently influence every decision.
Being lean is simple enough. Once efficient practices are identified, they should be practiced.
Becoming leaner implies that all aspects of production should be constantly examined to find new ways of making them less wasteful. Just because a lean practice has been adopted, it doesn’t mean it can’t be adapted. Being open to change is a fundamental aspect of change. If you aren’t open to new concepts, they won’t present themselves.
That’s the essence of thinking lean. A walk from the loading dock to the front office is wasted if one doesn’t look at everything along the way through the eyes of efficiency. Friday morning meetings, for example, are wasteful if they are just habit and the agenda actually needs to be created rather than presenting itself as a matter of need. Meetings should only be scheduled when needed, rather than being determined by the calendar. A daily or weekly e-mail might be more efficient, and thus less wasteful, than having several employees ignore their tasks and attend meetings in person.
Looking at lean as a set of tools is what is meant by “doing lean.” Various proponents have different tools in their toolboxes, many of which have Japanese names because the culture in large part began in Japan. Rather than explore all of the different tools in this limited forum, it makes more sense for a manager who is interested in the concept to explore this online in greater detail. There are lots of efficiency consulting firms who can not only present the concepts, but help a shop implement them.
In layman’s terms, lean manufacturing tools include standardizing work methods, instituting new problem-solving practices, creating audit paths and so on. Most of them are based on the concept of simplifying everything, eliminating waste and creating a smoother workflow.
Defining lean-speak
The jargon used by disciples of lean often list the tools as cellular manufacturing, “just-in-time,” product smoothing and total productive maintenance. Cellular manufacturing doesn’t refer to materials: it describes reorganizing the workforce into resource-based cells that, working together, can complete tasks more efficiently. In a woodshop, that resource might be a set of machines or a set of skills.
Just-in-time is all about controlling inventory and ordering parts just in time to be used, rather than too early, when they must be warehoused, or too late where they cause a delay in production.
Product smoothing is about inventory of finished goods rather than inventory of parts. In a custom shop, this isn’t as relevant, but it’s critical for outsource suppliers who sell components to custom shops. The latter, by their nature, are already practicing smoothing, because each job is custom, so there is no extra inventory.
Total productive maintenance can cover everything from sweeping the floor to topping up pneumatic-line lubricators. It addresses cleaning the belts in a wide belt sander, changing blades in the table saws and sharpening jointer knives. It encompasses switching burned-out light bulbs and getting the oil changed in the delivery truck. If, for example, all of these things were to be done at night by a separate maintenance professional rather than as needed by production staff (who normally have to stop what they’re doing to take care of things on that list), then maintenance will have a much smaller impact on the shop’s workflow.
Exploring lean management as a philosophy for your woodshop is not a simple task. Much of it was created by Toyota in the 1970s and 1980s and neatly wrapped up in an American business school format during the 1990s. Toyota started out as a small local business and grew into the world’s largest carmaker, so obviously they were doing something right. Their factory culture in a lot of ways reflected their national culture. It’s not surprising that this philosophy didn’t begin in America, where workers have traditionally been more focused on personal and individual values than corporate or collective ones. It’s also not surprising that U.S. businesses have adopted it and shaped it to fit their model. The genius of corporate America is not always original thought, but adaptability.
This article originally appeared in the April 2013 issue.
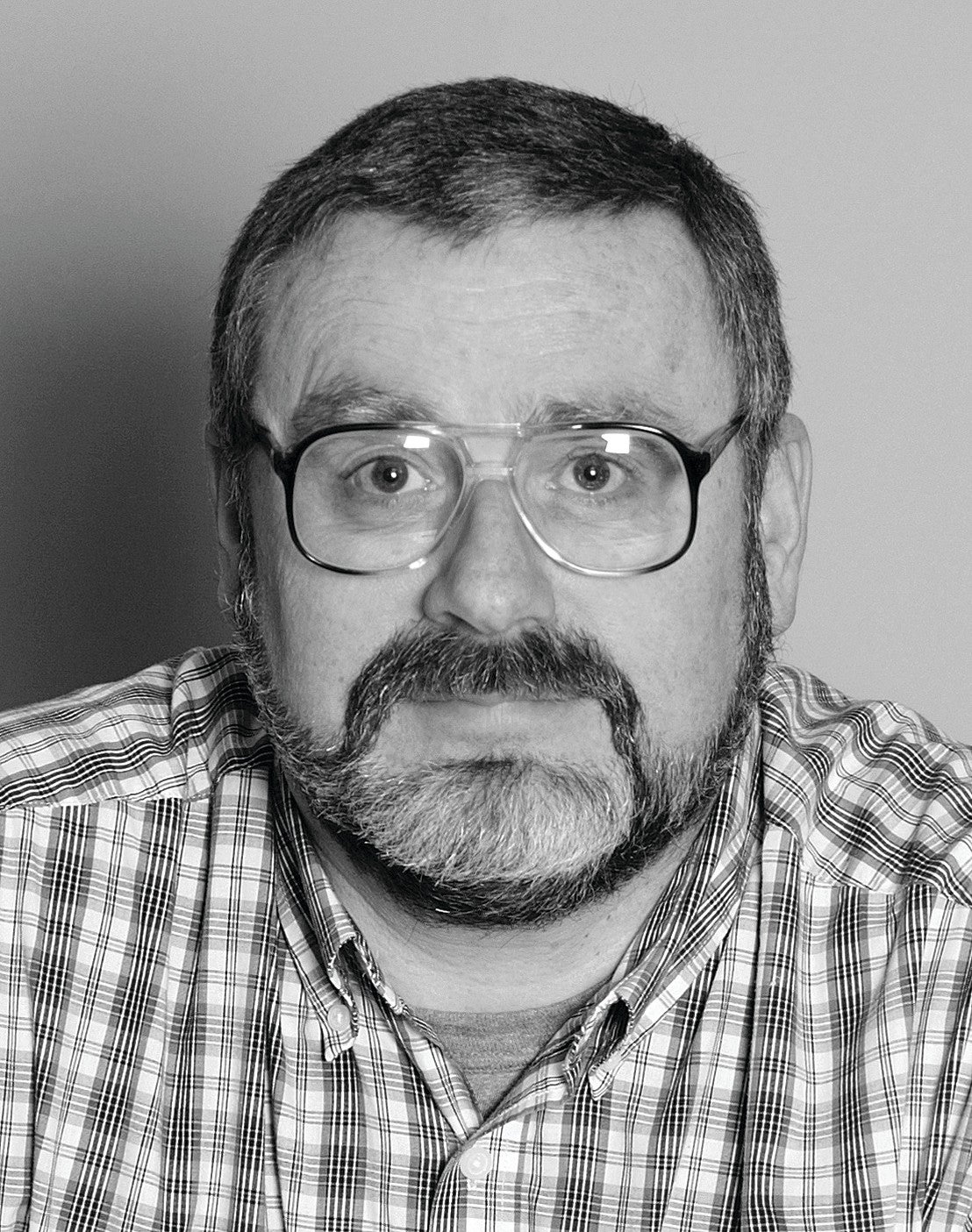