Lean and loving it
Anyone who has picked up a business magazine in the last couple of decades has read about lean manufacturing. It’s on cable, the Internet, in seminars, bars and boardrooms. And…
Anyone who has picked up a business magazine in the last couple of decades has read about lean manufacturing. It’s on cable, the Internet, in seminars, bars and boardrooms. And it’s as confusing as it is popular.
Lean manufacturing is also known as just “lean” or lean production. The core of the concept is that a company should do its absolute best to avoid spending money or other resources (such as time) on anything that doesn’t add something to the business’s product or service — and that “something” must be a perceived value for which a customer is willing to pay money.
That sounds complicated — and it is.
The simplest interpretation is that lean processes try to eliminate waste from the production process. But again, it’s a bit more complex than that. One must maximize the value that a customer receives, while minimizing waste.
Go to any of a dozen websites that discuss lean manufacturing and each one will give you a slightly different definition. The confusion could come from its cross-cultural heritage. Lean emerged from a Japanese corporate environment and since about 1990 American business schools, company directors and site managers have been beating it with intellectual hammers to make it fit into a traditional business model. Its origins are gray: some claim that it first raised its head in Michigan as the bastard child of Ford’s assembly line. Others watched Toyota rise from the ashes of war and, after three decades of refinement, create a theory that launched it into the stratosphere of profitability. Still others maintain that it’s a horse following the cart: that once Toyota successfully gained entry into European and American markets, its homogenized business culture of employee zeal and unquestioned loyalty was what created profits and the lean theory merely followed.
Slice it whichever way you want, lean seems to be here to stay. And the longer it’s around, the more refined and defined it becomes. The question to ask is not about its nature or history, but rather this: can some variation of it help a woodshop become more profitable?
The elements of lean
One of the most accepted definitions of lean is that it is a way to discover efficiencies and remove wasteful activities (called “muda”) that don’t add any value to the end product. No matter how efficient a shop’s production process is, there will always be room for improvement. Continually looking for and implementing improvement is the first element of lean, known as Kaizen.
Identifying waste is a broad concept. It might include recognizing that there are too many supervisors for a crew or that tasks have been divided unequally and one worker is always waiting a minute or two for the person in the step before him to finish. It might involve buying a 5x5 sheet of plywood instead of a 4x8, because there is 1 percent less waste when that sheet is optimized. Perhaps it’s as simple as moving a garbage can 3 feet to save two seconds a minute or having people use a time clock at their station on the shop floor instead of walking 80 feet to the lunchroom to clock in and out. Charting such waste is done on a Value Stream Map, which is essentially a diagrammed flow chart. Nowadays, there are numerous apps that will draw one for you.
Once waste has been identified, it must be analyzed. The idea here is to find the cause of the waste and the key is to avoid assuming that the obvious answer is the correct one. For example, if four people in a shop all experience kickback on the same table saw and production stops four times in reaction, the immediate assumption is that there is something wrong with the saw. Perhaps the fence is out of alignment or the blade is buckled or a splitter is bent. However, the real reason could be something else such as poor training or a batch of slightly warped boards or a slippery floor that creates unsound footing — or even a light that throws a shadow so that people can’t see well enough to keep the work tight against the fence.
The third step is to address the root cause of the waste. Implement a better training program, buy better boards, sweep the floor, move the light and maybe do more than one of these.
So far, lean sounds a whole lot like good old-fashioned common sense. The difference is that common sense is usually an impetus of reaction — it kicks in after the fact and helps minimize consequences now and works to avoid them in the future. Kaizen involves actively and continuously seeking unseen problems. It is designed to reveal inefficiencies that are not obvious.
Lean philosophy gives managers several tools to deal with identified efficiencies. The best known of these, developed by Toyota, is known as “just in time” or JIT. Remember that horse and cart earlier? Well, traditional American production models would push the cart, while lean models suggest pulling it (letting actual demand take precedence over expected demand). That is, U.S. companies are used to having a strong inventory of parts on hand and plenty of trained personnel available, so that they can deal quickly with fluctuations in demand. Part of that philosophy is to even out the highs and lows by making up lots of finished product ahead of time and warehousing it until customers need it. Look at any large car dealership and you’ll see millions of dollars of inventory sitting in the weather, waiting on a customer’s whim.
The most efficient lean managers only buy materials to make product when the finished goods have already been sold. Or they will, at best, produce goods ahead of time in very small batches to minimize the waste involved in storing inventory or the financial cost of the money used to buy components. In woodshop terms, they will stock only enough drawer slides for the current kitchen, even if by buying five kitchens’ worth of slides they might earn a small discount. Lean managers will always look at the terms of a purchase and avail themselves of any discount. If they are offered 2 /10 Net 30, they will always pay within the 10 days to gain the 2 percent discount. One big advantage to smaller batches is that if there are defects they affect fewer finished parts before they are discovered, so the overall quality of the product is sustained.
That brings up another item in the lean toolbox. Kanban is a subsystem that tells people when they need to reorder or even just go get something. It’s like those order forms in a box of checks that tells you they’re getting low. It lets employees reduce overproduction and order materials “just in time.” Kanban markers aren’t always as simple as a postcard inserted near the end of a pile. There is a sophisticated formula to decide when and how often a marker is needed and sometimes the marker is the actual size of a batch. For example, if drawer slides come in cases of 12 pairs, perhaps the marker is when one case is left or maybe two. When that number is reached, the employee needs to have somebody restock so that he/she doesn’t run out of inventory and thereby cause a stoppage, but by doing so sooner they would have caused the woodshop’s buyer to purchase more slides than were really needed, tying up cash and storage space.
Markers (cards) and containers (cartons of slides) aren’t the only Kanban signals: there are automated (usually electronic) markers, too, where for example a red light might turn on when the weight of drawer slides on a storage shelf reaches the renewal level. Such markers are more often used in industries that use liquids or granular components where volume or weight are more convenient ways to measure than physical counts.
The domino effect
Eliminating obvious waste often benefits a business in other ways, too. For example, a shop that has had a practice of prebuilding some components such as drawer sides might decide to reduce its inventory to a JIT level. The immediate savings are space, materials and employee hours, but there are also more subtle savings such as power to run machines. Perhaps the lights over a certain machine can be turned off or an infrared heater is no longer needed or somebody doesn’t need to spend a few minutes changing filters in an air line or a dust collector. In a production environment (as opposed to a service industry) costs are related to manufacturing, operating and inventory. A newly implemented efficiency in one area often creates a correlated efficiency (elimination of waste) in another.
Much as one efficiency engenders another, the culture of lean depends on the interaction of people. To work, lean philosophy must begin at the top of the personnel triangle and work its way down through every level. Everybody in the organization needs to be on board. Everyone must embrace and practice the concepts or there will be inefficiency and waste in the effort to combat inefficiency and waste.
Fighting waste
One of the keys to lean production is the goal of zero defects. The concept here is to get things right the first time through. How many times has a kitchen waited on the loading dock while one of the more experienced cabinetmakers has tweaked somebody else’s work? Perhaps there was a speck of dust in the lacquer or a hinge that was a little crooked. Maybe the cutout for the sink was a hair too tight or a couple of shelves weren’t sitting properly on the supports. Zero defects is a way of thinking that trains people to believe that no mistakes are acceptable, that good enough just simply isn’t good enough. The product needs to be perfect the first time through and relying on a final inspection to correct poor workmanship is not an option. Pride in one’s work is an ancient concept and one that is often ignored in a fast-paced production environment where deadlines have become the currency of success. When everyone is on deadline, it’s important to recognize that a lack of professional pride can cause delays.
Another tool used by lean managers to combat waste is Single Minute Exchange of Die (SMED). This is a technique that cuts down on the time wasted when a shop changes from making one component to another. In the woodshop, processes such as changing from sealer to topcoat or from a roundover to a rabbeting bit would be addressed by SMED. By developing a technique for rapid tool changes, the shop opens up the way to working with smaller batches. That, in turn, allows the facility to purchase materials just in time and to manufacture just in time, too.
The idea that every tooling switch can happen in less than a single minute is obviously preposterous, but the concept is that it should take the absolute least amount of time possible. For example, it might be more efficient to remove a router motor with the bit still locked in it and install a second motor in the router base with a different bit, rather than changing out just the bits. Exchanging motors can be a simple tool-free operation, while changing bits can involve wrenches, replacing bits in holders, making more height adjustments and so on.
Lean philosophy also employs a concept called 5S. The name comes from the fact that the method uses five words that begin with the letter “s” (well, they do when we write Japanese words phonetically in our alphabet). These are seiri, seiton, seiso, seiketsu, and shitsuke. Somewhere through the years, somebody took the time to translate those words into English and still came up with five words that mean the same thing and start with the letter “s.” They are sorting, streamlining (or sometimes straightening), shining, standardizing and sustaining.
Sorting means a shop should eliminate any tools or equipment that are not necessary. If there’s an old molder sitting in the corner that hasn’t been used in years, it’s time to put it on Craigslist.
Streamlining refers to organizing everything for the least amount of downtime. It’s that old concept of a place for everything and everything in its place. The essential element is flow: orderly organization means that no time is lost looking for anything.
Shining is an easy one: keep the workplace clean and tidy.
Standardizing refers to reducing options. For example, if a shop has four router tables, they should all use the same model router so that their motors are interchangeable. This means a quick fix is available if something fails (just switch motors), plus the shop needs to own fewer repair parts. There is also a shorter learning curve for employees who only need to familiarize themselves with one tool. And there is a better opportunity to duplicate settings and thereby save on setup time. Standardizing not only requires that all the routers are the same model, but that all the processes and ways of doing things in the shop are also formalized and uniform. For example, everybody using the drum sander is required to clean the belt before turning it off.
And sustaining means that these standards become second nature. Everyone is committed to the same set of rules and “almost” just doesn’t cut it. If the broom is supposed to be in a certain place, then it should never be left three feet away. If the next employee to use it has to look for it, the system is not efficient.
Some lean models add other “s” words such as security or safety, while purists feel that such meddling is in itself wasteful and counterproductive.
Downside
Sometimes lean philosophy shoots itself in the foot. A Minneapolis publishing house once installed new intranet communications software that allowed all of its supervisors and managers to communicate when they had time, rather than to physically attend production meetings where everyone met in an office for 45 minutes. They very quickly discovered that the software created day-long meetings where nobody could make a decision because there was a lack of consensus. What was missing? Body language, for the most part. A later experiment with laptops and cameras was a lot more successful, but still not as productive as a physical meeting where people spontaneously reacted to suggestions and contributed thoughts that helped the group arrive at creative and collaborative solutions. So while people eating doughnuts and making comments about last night’s football game was obviously inefficient, it was still better than e-mailing each other all day.
This article originally appeared in the April 2014 issue.
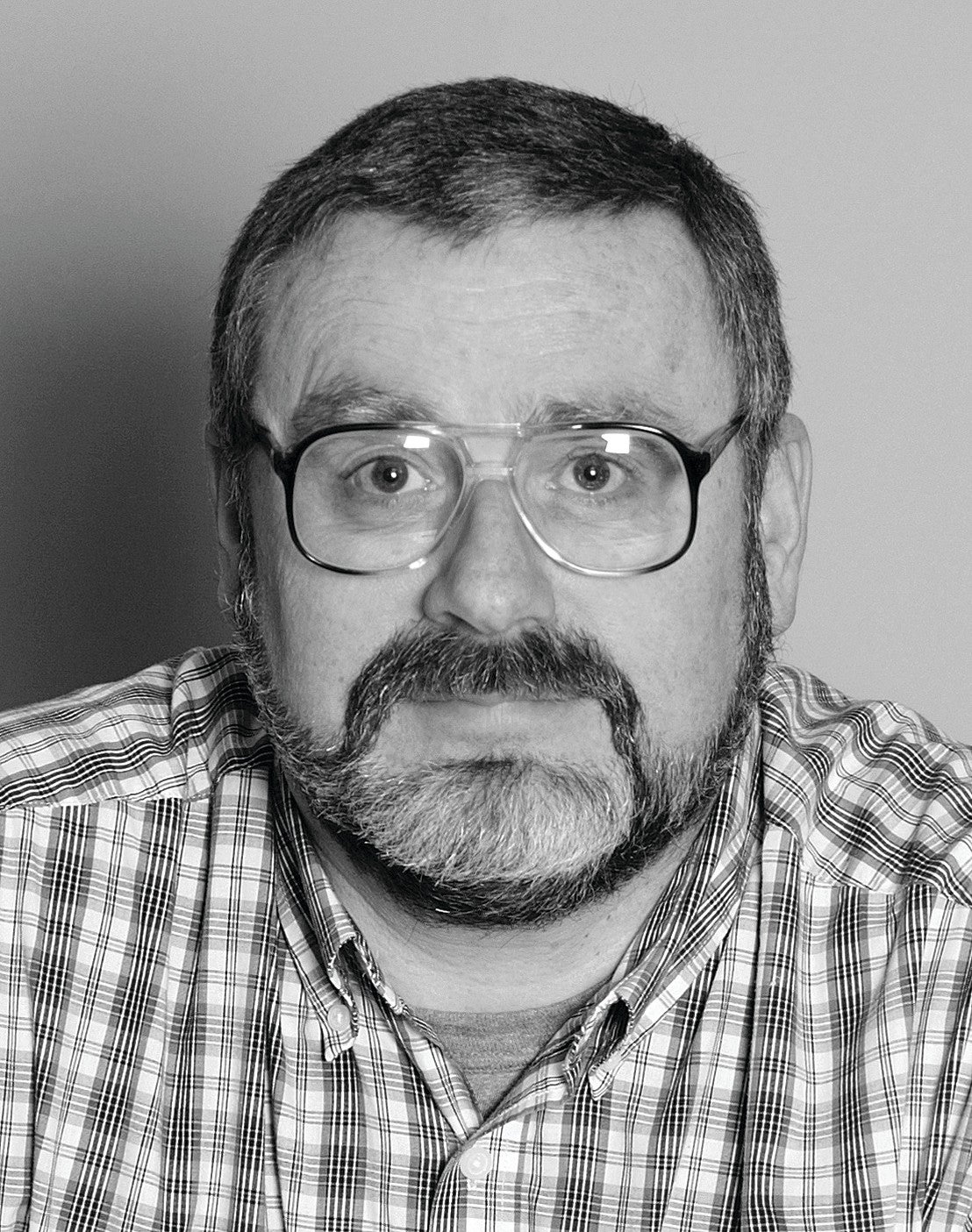