Nobody wants to see screw heads or exposed metal plates when they buy a kitchen, so the industry has always followed traditional furniture aesthetics when it comes to joinery. But building with hidden joinery can be time-consuming and expensive, especially when it comes to tasks such as chopping mortises or making perfect half-laps. So, manufacturers have developed a host of mechanical fastening systems that combine strength, speed and economy with visually pleasing results. Choosing among these usually comes down to a handful of critical requirements.
The first concern for most shops will probably be cost. Here, we’re not talking about the per unit cost of fasteners, which is generally quite low. The real costs are in the machinery and time required to create pockets or drill holes and insert the hardware. Many systems are manual, some are CNC-based, and a few require special machines. Each of these methods comes with a different time spectrum. If prepping parts for fasteners is going to require several steps and setups, it’s probably more suited to small-batch assembly. Costs are intricately tied to the scale of production.
The next consideration is the ability to allow manual milling and insertion initially, but also have the potential to automate down the road without having to switch fasteners. A shop might be using traditional machines or even a basic flat table CNC with an aggregate head to mill for manually inserted fasteners now. But the owner may wish to eventually upgrade to a dedicated 5-axis CNC or even a specialty machine that can mill for and insert a specific line of fasteners. Or perhaps the insertion will be done by a collaborative robot. The key here is that a shop doesn’t want to get comfortable with a specific hidden fastener and then have to switch to something new because there’s no way to upgrade the machinery.
Then there’s speed. Some connectors just pop in place and snap together, while others require the tightening of screws or perhaps using Allen keys or other tools to draw parts together. Multi-step connections take time. They can also open up a window for error if they’re a little too complex for newly hired help, or so unforgiving that a slight error can mean a whole part has to be jettisoned and rebuilt just because things won’t line up exactly. Operator errors and high defect numbers can quickly increase the cost of a seemingly inexpensive fastener.
Quality is perhaps the most important issue here. Nobody wants to assemble casework or furniture with hardware that will work loose due to the vibrations of daily use, doors or drawers slamming, changes in humidity or perhaps sheet stock. A shop needs to choose a line of fasteners that is ideally suited to the stock thicknesses and core densities that it uses to create panels and parts. The fasteners need to remain inserted and have enough shear and compression strengths to do their jobs over time. Sometimes a hidden fastener (metal, plastic or wood) needs to bond with an adhesive that’s also compatible with the core sheet, foil, laminate or even a coating being used. For example, how well does a standard polyvinyl resin glue work with a plastic dowel pin?
The bottom line is that choosing a fastener isn’t just about the fastener. It’s about machines, tooling, people, materials, time and money.
Innovations
As with most woodshop technologies, hidden fasteners keep on evolving. For example, the latest products from Lamello (imported by Colonial Saw) are a far cry from the compressed wood biscuits that revolutionized joinery in the late 1960s. Those are still available, but they have been joined by a couple of other systems that have kept pace with technology.
The P system from Lamello uses a tool called the Zeta P2 to cut slots, but the biscuits have ridges along their curved edge, top and bottom, so a cross-section of the slot looks like the letter T. The biscuit slides into either end of the slot, and once in place it can’t be pulled straight out – it has to be rotated back out. That creates an incredibly strong joint. The P system includes snap-in biscuits that just click together, cam-lock biscuits that are tightened with an Allen key, and slide-in connectors for shelves. The P system is very CNC-friendly. The newest member of the Lamello family is the Cabineo, which is a very fast and strong (200 lbs. clamping force) panel connector that slips into a CNC-milled pocket. There are three types of connectors for 90-degree, thin material, and knock-down applications.
Castle USA introduced the updated 110 Pocket Cutter last year, and the company is currently offering this benchtop production-grade machine in a Professional Bundle that includes a full range of accessories such as stops, router bits, Torx drivers, pilot bits, 1,000 screws, a face clamp and the Castle Tight Access Driver. This latter is a racket extension that lets the woodworker tighten hard to reach pocket screws.
Kreg Tool has redesigned its pocket screw hidden fastener jig and the new 720PRO model creates pocket-hole joints in materials from 1/2” to 1-1/2” thick. It has a one-motion clamping action with Automaxx, which automatically clamps and adjusts to the proper material thickness. It also has GripMaxx, an anti-slip system that holds material in place during clamping. There’s on-board storage for accessories and a Docking Station with material support wings for more storage and support for large pieces. Plus, a chip ejection port connects the jig to a shop vacuum.
Hoffmann Machine Co. is the U.S. division of a German parent company that is best known for a system of plastic dovetail keys that are used to create hidden (and sometimes exposed) joints in cabinets, furniture, windows, doors, architectural millwork, and more. The keys are now available in five widths and a variety of lengths and colors.
New from Knapp Connectors is the Quick-Set, a two-part locking dowel system for cabinet assembly that is available as a plug-in for Cabinet Vision. This is a simple, completely hidden, snap-together system that is self-tightening and self-locking, so it requires no glue.
Festool’s Domino connectors make knock-down joinery simple and stable. They let a woodworker quickly and easily assemble, separate and reassemble work for increased flexibility across a wide range of applications – from corner panel joints to center panel joints to joints between a series of holes. The newest family of connectors offers increased stability, speed, and flexibility.
Among the newest Striplox brand connectors is the Shelflox Extendable. This is a fully concealed, adjustable shelving system for installing horizontal shelves or vertical panels in existing cabinets. Working with depths from 8-1/2” to 23-1/2”, one half is inserted in the shelf edge and the other in the cabinet, and then the shelf is slid into place where it locks in position. Two shelves can be installed at the same height in adjacent openings.
Excel Dowel & Wood Products offers bulk wood biscuits, dowels and pre-glued dowels for hidden joinery. The fluted or spiral-grooved pre-glued dowel pins are coated with a Type 3 re-moisturizing PVA wood glue that is water activated. Simply replace the normal glue bottle with a water-filled one and the shop can eliminate glue buildup and squeeze out.
FastCap has come up with a clever way to fasten two parts of a countertop from the underside. Called the Qwikdraw, it doesn’t require any special boring or machining. It consists of two plastic plates with triangular ‘teeth’ and a whole lot of screw holes. The woodworker uses some of the holes to screw the two halves to the counters, leaving a small gap between them. Then clamps are used to draw the halves tight before driving the remaining screws to lock the joint in place. Special small clamp pads are available to get a good grip.
FastenLink is a uniquely shaped plastic dowel that lets even novices assemble cabinets with almost no tools and machining. The company continues to forge partnerships with major software companies such as EnVision, KCD, Cabinet Vision, Mozaik, Microvellum and CNC Automation, and also with machine manufacturers such as Weeke, Koch, Imal, Gannomat and Biesse.
Last August, Hafele introduced the innovative Ixconnect Claw Connector CC 8/5/30. The single piece of hardware connects wooden drawers quickly and easily without tools. All it requires is a few standard drill holes (front: 8 mm, side: 5 mm) to make a nice, tight fit. Wooden drawer panels as thin as a half inch can have a reliable, invisible connection when the claw bites into the MDF panels.
Hardware Resources offers several hidden fasteners including a metal cam for 5/8” panels (part 7C16) that can be used with single (5C36) or double (6CDB) connecting bolts for varying thicknesses of stock.
Outwater Plastics and Architectural Products offers a similar solution, along with a range of other knock-down fittings and connectors including several made of nylon and zinc that come with or without dowel pin outriggers. These work with 16mm and 19mm panels and are a drop-on application that uses the Klix locking system that is compatible with all screw-in and Quickfit System6 dowels. They’re ideal for high volume production case goods, closets and garage storage systems. There’s no edge boring required.
Lockdowel continues to innovate and expand, adding two new fasteners in the last year. The basic concept is a CNC-friendly, one-piece barbed connector that uses a keyhole slot to create the locking mechanism. The CNC creates an elongated hole where half of it is wider. The connector drops into the wide part and is slid home in the narrow part. It’s simple, strong and very fast.
The Irish manufacturer OVVO also offers plastic hidden fasteners, and those have won numerous awards over the past few years at European and U.S. trade shows. CEO Brendan Phillips tells Woodshop News that several new products are in the works and will be released shortly.
Finally, for shops that are looking for a hidden fastening system in outsourced casework, Cabinotch offers a cabinet box system with a patented interlocking joint. The company supplies the face frame, sides, backs, bottoms, tops and shelves, which slip flat and assemble in minutes.
This article was originally published in the June 2021 issue.
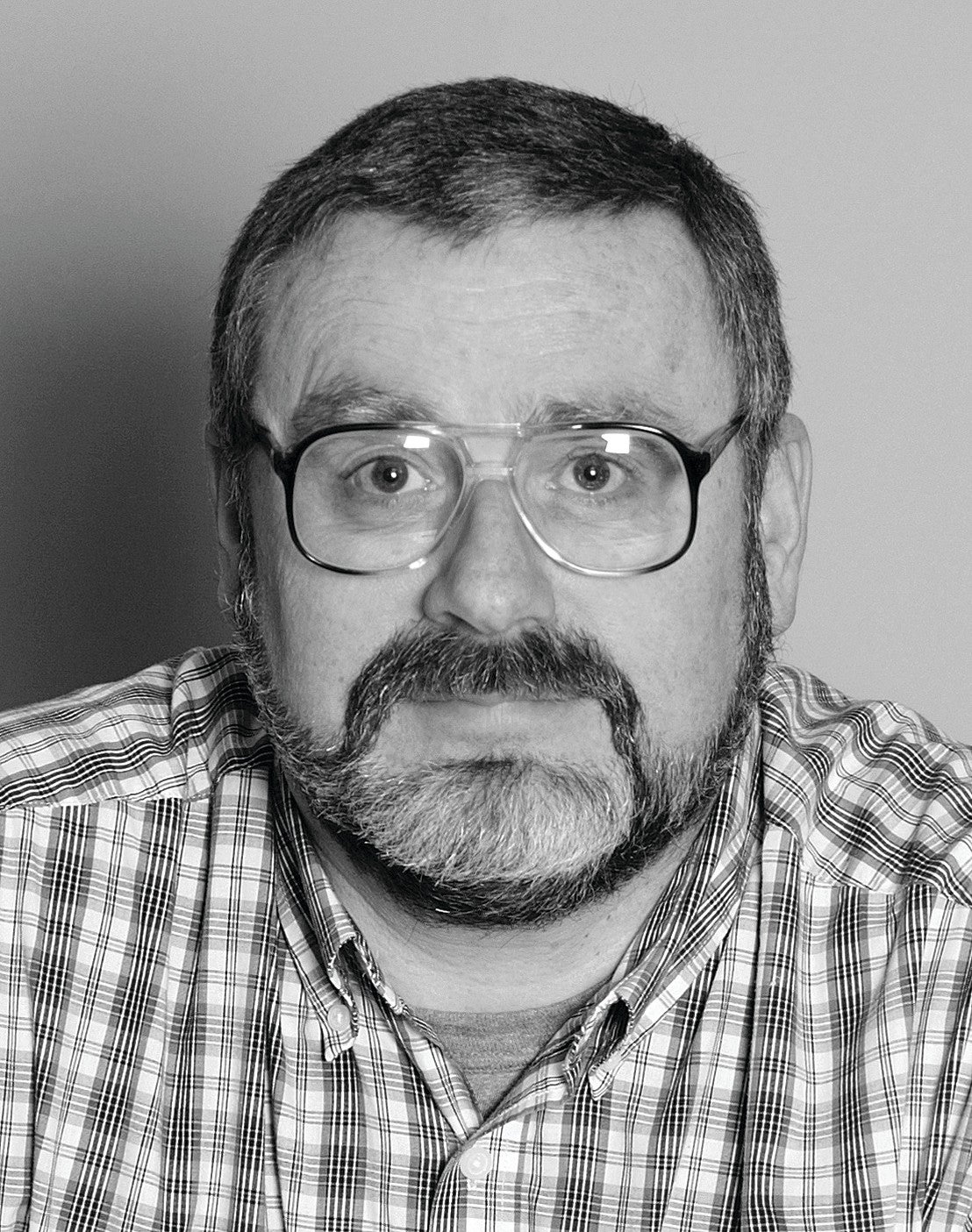