A few years ago, I was asked to make felloes for a wagon wheel. These are the wooden segments of a ring just inside the iron tire. I hadn’t done it before, so I ended up seeking the advice of a gifted Amish craftsman in Chetek, Wis. His shop was in a two-stall garage, and he had a gas-powered riding lawnmower parked close up against the building, chugging away in high gear. That, it turns out, was his power source. His sect doesn’t approve of electricity (the rules vary among communities), so he had rigged the lawnmower to power a shaft that ran the entire width of the building. Then, like an old mill running off a water wheel, he had connected a table saw, band saw and several other machines to the shaft with pulleys and belts.
I ended up hiring him to make the wheel parts. He was obviously smarter than I was.
Having seen this resourcefulness, it was no surprise to come across the Amish air-powered router from Cottage Craft Works (cottagecraftworks.com). It’s a DeWalt DW6182 plunge router connected to a Sioux air motor, developed specifically for Amish woodworkers. Connect it to your compressor and you have a quiet, 1-1/2-hp router that runs at 20,000 RPM. There’s also a fixed-base version and a laminate trimmer.
No screaming, no sparks. I’m tempted.
Making the case
Using pneumatics in the woodshop is nothing new. The tools aren’t as popular as electric ones, in large part because the hoses are cumbersome. And a whole new world of cordless convenience hasn’t changed that perception. But there are some very good reasons to reconsider. Pneumatics can make a whole lot of sense both at the workbench and on the jobsite.
In the shop, the hoses can be kept out of the way by just suspending them from the ceiling above a workbench. In fact, running an inexpensive hose across the shop by screwing a few hooks into the ceiling can be a whole lot less expensive that hiring an electrician to install new power outlets. Plus, you can move them easily and quickly if the bench needs to be shoved over a few feet to make way for a new CNC, or some other shiny toy.
Batteries are getting bigger. That makes some of the cordless tools kind of heavy by the end of the day, especially the larger ones that consume more juice. Pneumatic tools don’t have a motor, so they often weigh less than an electric counterpart that delivers the same torque to speed ratio. They also run a lot cooler and often quieter (as long as you have a quiet compressor, or leave the noisy one a hose length away, and preferably outside). That means that overloading or stalling aren’t concerns. If an electric motor stalls, it can heat up immediately. Not so with air tools.
Compressed air as a fuel is a lot safer and cleaner, too. There’s no fire hazard with sparks around propane tanks, or no possibility of electric shock when working in wet conditions.
Campbell Hausfeld published an article on its website, campbellhausfeld.com, that points out some advantages that air tools have over other options. The piece mentions the flexibility of being able to operate in areas where other power sources aren’t available. Air tools can also perform tasks that electric tools can’t and do others better – jobs such as spray coating or nailing a roof. They have a high power to weight ratio because they lack the weight of a motor, and that means they deliver a lot more work per pound. Air tools are often less expensive to own, too, because both fixing and running them are low cost as they have fewer moving parts, and a simple design.
Among the tools that a woodshop can hook up to a compressor are palm and inline sanders, drills and drivers, impact tools, various saws, ratchets and wrenches for assembling carpentry projects such as deck and docks, plus grinders for trimming bolts and easing edges. There is also a whole world of spray booth equipment, glue applicators, and of course all of the nail, staple and pin guns. There are things a compressor can do that are uniquely pneumatic, such as airing up the tires on a two-wheel dolly or blowing dust off a surface before staining it. Some furniture builders even use air tools to sand blast texture into surfaces, revealing 3-D grain patterns. And plastic nails in a pneumatic gun can be used to secure work on a CNC. If the bit cuts them, it won’t be hurt.
There is a world of difference in air hoses. The cheapest plastic ones will assume a position, no matter what you do. Their mechanical memory makes them coil awkwardly on the floor in the middle of the shop, with one strategic loop raised just enough to trip you. More flexible rubber hoses cost a bit more, but they usually lie flat and roll up nicely. Very thin spring-coiled hoses with small compressors. Check the internal diameter of a hose, not the external. Thin hoses can deliver less air than the tool needs. And if you work outside, read the temperature parameters before you buy a hose. Some of them stiffen like a corpse when it gets a little chilly.
One important note here – never use an extension cord with a portable compressor. Plug it directly into the wall and use air hoses to get where you need to go. The resistance created by long electric cords, even low gauge thick ones, can harm and even burn out the compressor.
Terminology
If you’re new to pneumatics, there are a few terms you’ll want to understand before you go shopping for a compressor or tools.
Air pressure is measured in pounds per square inch, or PSI. Remember those sunny spring mornings in junior high that you spent looking out the window in science class? Well, one of the things the teacher covered was Boyle’s Law. Robert Boyle was a physicist and chemist from Ireland in the 1600s, and his law stated that “for a fixed amount of an ideal gas kept at a fixed temperature, pressure and volume are inversely proportional.” In simpler terms, if you squish a certain volume of air into a bottle that is only half its size (say, two cubic feet of air in a one-cubic foot tank), then the pressure it exerts will be twice what it was. Squish it more, and the amount of pressure rises in direct proportion. Most tools have their preferred PSI rating stamped or printed on them.
Compressors are rated in terms of the pump motor’s horsepower, and that’s a handy rough guide to the power of the unit. But the real guide is cubic feet per minute (CFM), and this varies according to the amount of pressure the air is under. A common rating might be 3 CFM at 90 PSI. Most of your tools are going to be in the same PSI range (75 to 100), so to size a compressor, add up the CFM requirements of all the tools that you’ll use simultaneously and then multiply by one and a half – or even two, as you may buy a bigger nail gun soon.
Decibels are an important part of the equation, too. If it’s just you in the shop and you wear hearing protection, then it’s not really an issue. But if you’re taking a portable compressor to a jobsite, it might be time to invest in one of the new generation of quiet compressors. There are also companies that make sound boxes for compressors. If you decide to make an insulated box yourself, figure out a way to monitor heat build-up inside it. They get mighty hot, and even if it doesn’t start a fire, it will damage the compressor.
The tank is also something to look at. It’s easy to outrun the pump’s ability to keep up with tools. For example, a little pancake compressor that’s normally just used to run a pinner won’t do well trying to run an orbital sander.
Lubing can be done in the air line, but only for tools like nail guns. You don’t want to use an airline that has oil in it to power a finish spray gun. The residue will contaminate the finish. If you only occasionally use the compressor to run a gun (and the gun requires lubing; some don’t!), check the manual to see if it’s OK to put a drop or two of oil in the quick connector before you attach the hose.
It’s a good idea to attach a filter to the compressor and blow out the residue every morning. In dry climates, this isn’t as critical as it is in more humid areas. The filter will mostly trap moisture, but also some extreme fines. And the tank needs to be drained regularly, too.
Quick releases are the industry standard for connecting and disconnecting tools and hoses. However, the least expensive ones (and there are a lot of imports in that category these days) are made with base metal alloys and they often have little tensile strength. They can literally break and crumble when you tighten them with a wrench, or snap in two under very low impact. Spend a few bucks and buy a spare, too. You’ll be glad you did if the jobsite is several miles from a hardware store. Buy a couple of ear plugs while you’re there. The noise when you disconnect a hose can be startling. Oh, and a roll of white Teflon plumbing tape – it’s the best way to seal threads on air fittings.
This article originally appeared in the June 2018 issue.
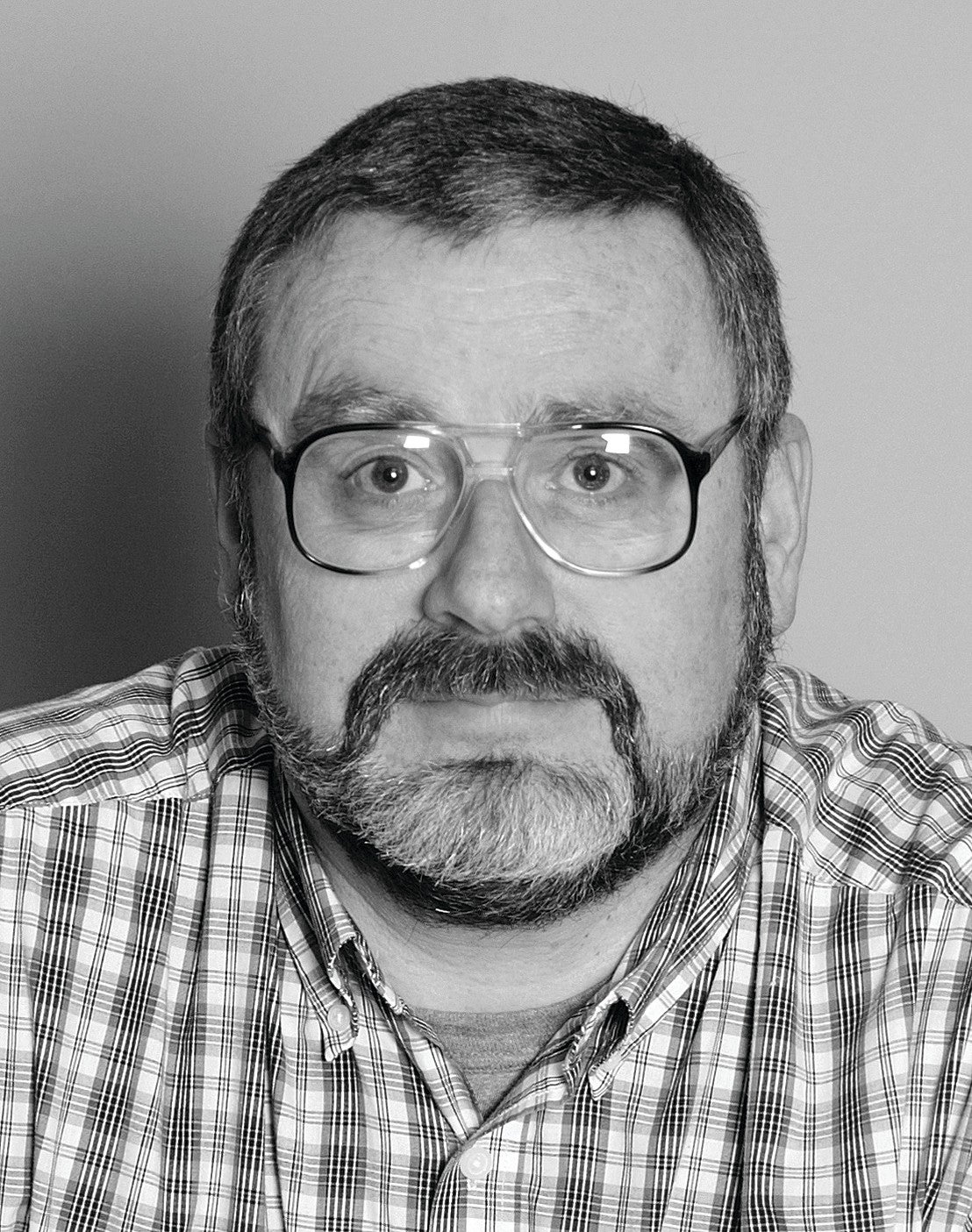