Green equals green
Coatings manufacturers seem to be notching up their green identities this year at a faster pace than we’ve seen in awhile. And they are not only accepting the role that…
Coatings manufacturers seem to be notching up their green identities this year at a faster pace than we’ve seen in awhile. And they are not only accepting the role that watchdog organizations play, but they are actively embracing and sometimes even involving these environmental groups in decision making.
In February, Paoli Furniture Co. switched to a formaldehyde-free wood coating system that was developed by AkzoNobel. These are big hitters: Paoli operates a 2.1 million-sq.-ft. facility in Orleans, Ind., and has more than 500 employees. AkzoNobel is headquartered in the Netherlands and employs some 47,000 people in 80 countries around the world.
What’s notable here for woodshops is that the new coating meets current air quality standards in the U.S., but it also meets the indoor air quality standards of groups such as the Business and Institutional Furniture Manufacturers Association (BIFMA) and the Greenguard Environmental Institute.
If you’re building casework and not office furniture, you might not be too familiar with BIFMA. It’s a not-for-profit trade group that has represented the interests of the commercial furniture industry since 1973. A lot of those interests are now centered on balancing environmental compliance with product quality, so it wasn’t a big surprise that in April BIFMA held its second Chemicals Summit at the Merchandise Mart in Chicago. While it was expected that the speakers and panels would discuss the future of chemical responsibility in the furniture industry, what’s noteworthy is that the keynote speakers included Michelle Moore of The Well Building Institute (a public benefit corporation whose mission is to improve human health and well-being through the built environment) and Brendan Owens of the U.S. Green Building Council (developers of LEED certification).
Manufacturers are not only listening more to activists, communities and government, but also to woodshops and other end users. It’s a difficult path for them as they try to meet everyone’s expectations. But there seems to be substantial progress of late. For example, most new coatings are being developed as compliant products that will work with existing delivery systems. AkzoNobel regional sales manager for wood coatings in North America Ron Cooper put it this way: “The challenge was to develop a new system that would work on Paoli’s existing finish lines and maintain the high-quality look and performance achieved with the existing system.”
Another trend is that woodshop owners, who have traditionally been a little skeptical about core changes in coatings, now have some bigger guinea pigs out there testing new ideas before they become mainstream. For example, one of the first things Paoli finishing supervisor Troy Apple noted was that the new formaldehyde-free finish “allowed us to achieve indoor air quality certification while improving the finish with better clarity, depth and durability.” In the past, some environmentally friendly products haven’t been too shop-friendly and, because of that, woodworkers have had difficult decisions to make. They have had to balance their concern for the health of the planet against the quality of finishes they have supplied to their customers. And they have occasionally been disappointed by actual results achieved by products — especially waterborne ones — that were touted as being every bit as good as the petroleum-based, high-VOC traditional coatings they were designed to replace. When big operators with sound reputations such as Paoli attest to the quality of a coating, such performance claims carry quite a bit of weight.
Another new wrinkle in the coatings world is that manufacturers are finally beginning to “get” how confusing and overwhelming core shifts in both indoor air quality standards and product usage can be for small-shop owners. If you only have a few employees, you simply don’t have the time or resources to research all the options when choosing finishes and also make sure that what you’re doing complies with all state and federal regulations. Rather than leaving shop owners to rely on secondhand information, some manufacturers are stepping up to the plate and giving shop owners direct support in this area.
Take, for example, Old Masters, a coatings manufacturer that has been mixing finishes since 1953 in Orange City, Iowa. On the company website (www.myoldmasters.com), there is a nice tool named the ‘VOC Compliancy Map,’ where a woodworker can simply click on his/her state (or even a county in California, Arizona and Virginia), and a list of the company’s stains and topcoats that are regionally VOC-compliant pops up to the right of the map. Rust-Oleum, an RPM international company, publishes a California-specific VOC compliance guide on its website (www.rustoleum.com).
In that same spirit of support, Valspar has created an industrial wood coatings site that is designed specifically for woodshops (www.valsparwood.com). The company, which also manufactures Cabot and Guardsman brands, now has 22 Greenguard-certified Zenith coatings. The most recent addition is G-1 Self-Seal, a solvent-based topcoat that uses existing spray line equipment and, according to the company, offers “excellent moisture, chemical and mar resistance, as well as superb performance in flow, leveling, build and appearance.”
For cabinetmakers and furniture builders, one of the nice byproducts of the surge in natural wood floor installations over the last two decades has been the amount of finish that these products require. That volume has encouraged a lot of research and development by manufacturers. For example, Valspar has just started supplying coatings to American OEM in Only, Tenn., for a plant that turns out 10,000 sq. ft. of flooring an hour. What’s really interesting here is that the new facility uses specialized color mixing equipment that greatly reduces tint and chemical waste involved in color formulation and reproduction and, in many cases, the process actually eliminates waste completely.
Understanding VOCs
While most woodworkers are familiar with the term volatile organic compound (VOC), many of us are not as acquainted with their nature.
The EPA defines a VOC as “any compound of carbon, excluding carbon monoxide, carbon dioxide, carbonic acid, metallic carbides or carbonates, and ammonium carbonate, which participates in atmospheric photochemical reactions.” A simpler approach is to say that VOCs are chemicals (both natural and manmade) that change from liquid to gas at low temperatures, so they evaporate at room temperature. If you smell something in the air, it’s virtually always a VOC. The most familiar VOC in coatings, formaldehyde, has an incredibly low boiling point (-2 F), which means it begins to sublimate from the liquid as soon as you open the can.
Not all VOCs are dangerous, but a fair few are — and rather than presenting an immediate or dramatic toxic affect, they tend to be more harmful over long-term exposure. Many governments and international organizations have either regulated or created advisories about a class of chemicals called “anthropogenic” VOCs. These are essentially compounds that have an effect on the environment resulting from human actions (such as making or using them). The theory is that if people actively create them, then people can actively control their impact. In that vein, Congress passed a bill in 2010 that addressed the use of formaldehyde in plywood, particleboard and MDF, limiting emissions to .09 ppm. And in 2011, the National Toxicology Program (a program of the Department of Health and Human Services) listed formaldehyde as a substance known to be a human carcinogen.
Gone green
Originally known as Cash Coatings, AquaCoat offers a full line of waterborne wood coatings, including topcoats, stains, sealers and grain filler that “provide an environmentally safe, easy to clean up, OSHA- and EPA-compliant alternative to toxic and flammable solvent finishes,” according to the company.
M.L. Campbell Co. manufactures a number of Greenguard-certified products including Azoton dyes, EnviroMax formaldehyde-free precatalyzed sealer and varnish, and WoodSong II waterborne stain base.
The Sherwin-Williams Co. has a slew of products that meet guidelines set forth by LEED, Greenguard, California Air Resources Board and other organizations. Too many to list here, but they are easily found at www.sherwin-williams.com.
Are you worried about extended dry times, product performance, look, feel and costs of waterbornes? Pro Wood Finishes asks that very question on the company website (www.prowoodfinishes.com) and claims that: “architects as well as builders can be confident specifying Fuhr Wood Coatings for all U.S. Green Building Council’s LEED Program projects. Fuhr Wood Coatings are also recommended by Green Seal for environmentally friendly projects.”
Eco Safety Products manufactures EcoProCote, made from bio-based ingredients that are designed to replace and replicate the characteristics of petroleum solvents, without compromising performance or cost, according to the company. The line includes wood stains and sealers.
Monocoat produces what it calls a “natural” oil finish, made from plant-based oils. It comes in a clear version and 30 colors. As the name suggests, it applies in a single coat at a rate of about 1,500 sq. ft. per gallon (it comes in liters). Not only is a second coat not required, the finished wood will not accept a second coat. The same action protects against overlaps and color variance and causes the process to complete in one coat.
PPG Architectural Coatings has been around for more than a century and includes such household names as Deft, Glidden and Olympic. Many of the lines, such as Deft Clear Wood Finish Waterborne and Interior Polyurethane Water Based Acrylic meet both LEED and Greenguard standards. And Deft also makes an oil-based modified urethane (called Interior Oil-Based Polyurethane) that has a 350 g/L rating.
The CrystaLac Co. is a division of Becker Labs and says it “will only manufacture products that are well below EPA regulations.”
Seagrave Coatings in Carlstadt, N.J., makes a catalyzed, water-based acrylic polyurethane called Aqua Polytane.
Penofin has a line of wood stains called Verde that can be used in both interior and exterior applications. Based on Brazilian rosewood oil, they have no odor, VOC ratings of less than 1 g/L and come in 18 colors, according to the company.
McCormick Paint manufactures several products that carry Green Wise certification and meet or exceed the VOC requirements of LEED.
H. Behlen has developed a low VOC tabletop urethane varnish called Rockhard that is compliant in most districts.
Chemcraft is an AkzoNobel subsidiary and is the manufacturer of Airguard “formaldehyde free-catalyzed lacquer.”
Benjamin Moore makes Benwood Stays Clear, which the company says combines the attributes of acrylic and polyurethane resins to render a clear, durable, scratch-resistant and non-yellowing finish.
A little bit of Europe
If you’re not familiar with European finish manufacturers such as Milesi, you might be soon. Milesi (booth 6529 at AWFS) is an IVM Chemicals brand and offers a complete range of coatings for the kitchen cabinet industry. (The parent company, IVM, operates all across Europe and has a presence in more than seventy countries worldwide.)
Thanks to low or no-VOC polymer and water-based formulations, Milesi says its products are “designed to contribute to a steady reduction in indoor air pollution and a lower environmental impact.” The product lines include polyurethane and acrylic-polyurethane coatings, Hydrocoat water-based coatings for interiors, polyester and styrene-free polyester coatings, as well as water- and solvent-based stains.
Europe has more stringent regulation on VOC emissions than the United States. For example, France requires a compulsory label showing VOC emissions for all products applied indoors. Because of environmental regulations, many EU manufacturers are a little bit ahead in terms of green processes. Many are leaning toward radiation (UV) in the curing of coatings. That process delivers fast results, low VOC emissions, some cost savings and, in many cases, a better finish. UV uses high-intensity light beams rather than air-drying to cure coatings.
Many American shops use the process to cure adhesives in bentwood applications, where time is of the essence. With radiation, there are no solvents or carriers that need to evaporate, so there is essentially no air pollution. Some curing booths also reduce the oxygen level in the ambient air before introducing UV light. This curtails the need for expensive UV photo-initiators in the finish and also delivers a finish that manufacturers claim is more scratch resistant. Radiation also has a positive environmental effect on ozone creation.
As the global economy continues to eradicate political borders and developed nations combine to combat pollution, woodshop owners can expect two things during the next few years: more regulation on VOCs and a growing presence in North America of both European and Asian coatings and finishing methods.
This article originally appeared in the August 2015 issue.
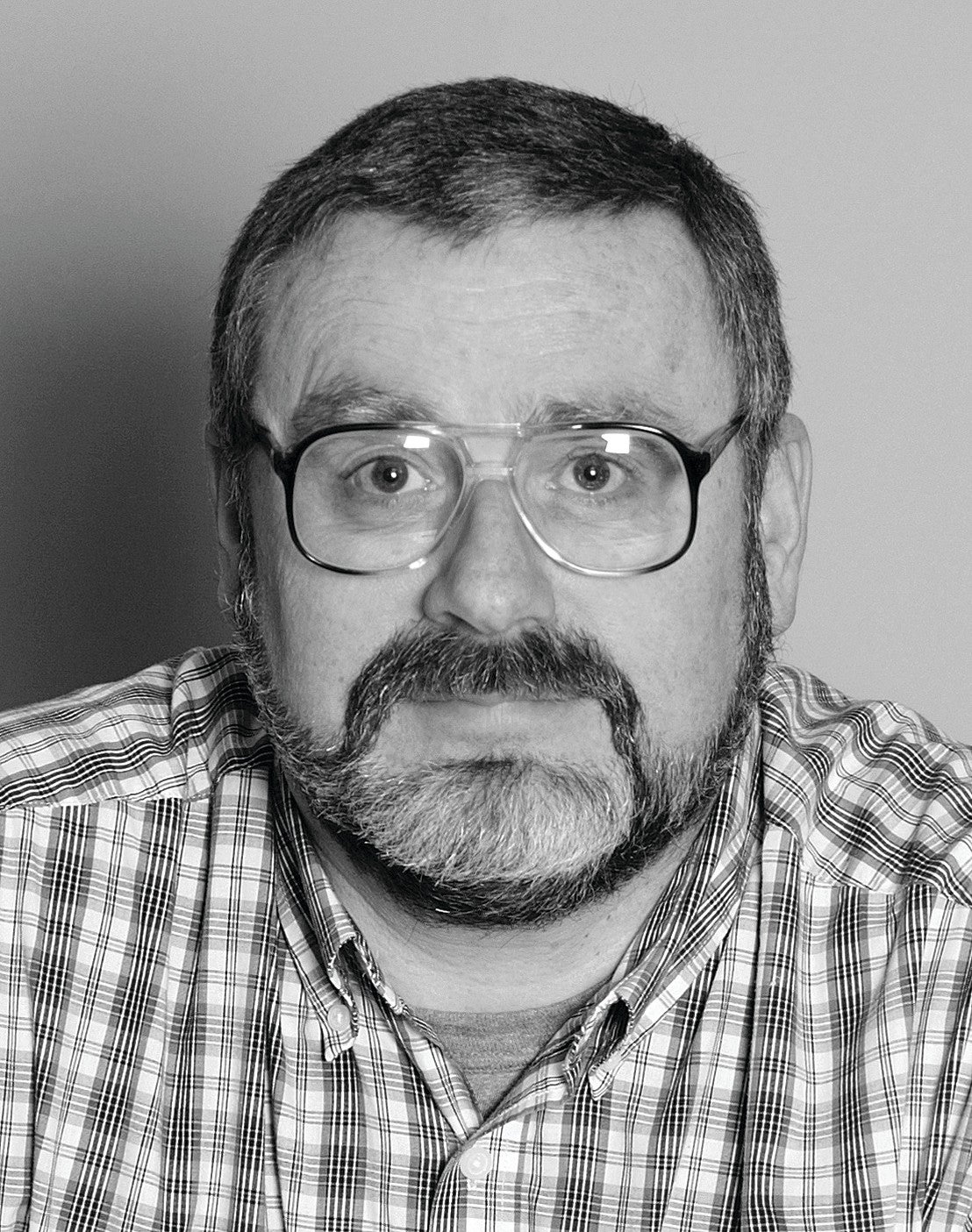