“Why, back in my day…”
The older one gets, the better the memories become. Unfortunately, not everything from the past was solid and sound. Remember the Ford Pinto?
Woodshop machinery is no exception, but a lot of the old cast iron, 3-phase behemoths are still quite serviceable, and some can be updated and upgraded at reasonable cost. While many of the classic machines have gathered up to a century of sawdust, machines from the past 20 years or so may also be eligible for updates, and that can be a whole lot easier. That’s because manufacturers often continue building the core machine and just upgrade the peripherals, so a slightly older dust collector might be a good candidate for a new HEPA filter and maybe even a bag shaker, or an aging planer might accept a new helical insert cutterhead.
So, upgrading can mean repairing and/or adding features to an existing piece of equipment, or actively searching for a chunk of classic iron that’s an improvement on modern options, or simply sending something old to Craigslist and buying a new machine.
For small shops, the decision to restore or repair probably boils down to cost and time. For bigger shops, it can be more complicated. Large new machines often need new infrastructure such as dust collection or 3-phase power, along with extra lighting, material handling solutions, employee training, and maybe even a whole new building.
Time is money
For shops thinking about going with an old machine and planning on minor restoration, rather than buying new, it can take a lot of hours to search through auctions and find the right machine, and the shipping costs can be substantial. For a machine that is already owned by the shop, the time investment will be in looking for manuals and parts to repair years of wear. Once that’s done, the search can begin for modern updates that will enhance performance or increase safety.
It’s not so much the money invested in physical parts that are a concern, but rather the time invested in finding them and then retrofitting them to old machines. There’s a professional woodworker in Minneapolis who spent two days retrofitting a riving knife to an old Delta Unisaw and he still won’t admit how much he spent, or even if it works.
Bigger machinery can make more money sense. An older CNC might be updated in many ways, as long as any play in the spindle or gantry can be corrected first. There’s no point in spending money on upgrades if the core is unhealthy. Upgrades such as adding vacuum tables or other fixturing, updating the spindle from air-cooled to liquid (and maybe upping the horsepower), installing better dust collection, or automating the loading and unloading processes can all add a great deal of value to a basic CNC. Travel times can often be improved with new motors, controllers, wiring or software updates, and even gantries can sometimes be raised to extend the Z. But there comes a time when a whole boxful of bandages just won’t cure the patient.
Besides which, new toys are more fun to play with.
On the other hand, a familiar machine is an old friend with a well-worn learning curve.
Is it complicated?
For many woodworkers, half the impetus to retain or acquire an older machine is that we get to spend some quality time restoring it. That pure pleasure may offset some of the expense. There’s a romance here akin to collecting and reinvigorating vintage automobiles. The machines reek of history and remind us of a collective past when America was the world’s factory.
When it comes to traditional floor machinery such as table saws, jointers, planers and shapers, it’s hard to beat classic brands like Powermatic, Northfield or Oliver. And a vintage Tannewitz band saw always makes an old woodworker grin (yes, they still make ’em). With a Tanny, one is probably just looking at replacing a power switch or some bearings, and maybe adding new Carter guides to create a machine that can stand with, and probably outperform, most of the new models built overseas.
But other machines can be a bit trickier than a band saw, where the doors simply open to reveal its beating heart. For a start, it can take a lot more time to access malfunctioning trunnions or bearings in an enclosed housing such as that of a table saw or shaper. And if cast-iron tables on a jointer or planer are worn, cracked, warped or severely rusted, they can add up to a costly repair. Grinding them flat is surprisingly affordable, but sometimes that won’t work if the damage is excessive.
Among the advantages of buying new equipment, safety looms large. Guards and splitters on older machines were often more of a danger when installed than going without them, so many old machines arrive with these missing. Some of those safety devices were invented by lawyers, not engineers. Today, we have finger-sensing technologies that drop saw blades or set off alarms when digits get too close to a blade. We have extraction ports right at the tool that eliminate fine dust in the air, and sliding tables with fixturing that keep the operator’s fingers far away from hungry carbide teeth. In a one-man shop, such safety exigencies might be ignored. That’s a choice – a poor one, but legal. If a sole proprietor wants to run a machine without a guard, so be it. But there are few legal recourses if there’s an accident. If the shop has employees, such concerns are a matter of both conscience and responsibility. It simply isn’t fair or right, or legal, to expose others to avoidable danger.
When it comes to portable tools, there’s little question that modern options are a better choice, especially with the advent of cordless tools. The weight alone is enough reason to forego those bulky cast routers and belt sanders from the post-war era. Never mind the noise and dust, and being tethered to an outlet.
Stationary machines, on the other hand, are usually at least worth considering, but there is the issue of apps. Most modern machines can be connected to manufacturers’ apps on a laptop or smartphone, so they can monitor everything from performance to employee hours and routine maintenance. That’s generally not an option with vintage machines, although there are some exceptions. A modern shop can be run from a coffee shop, a client’s kitchen, or even a trade show on the other side of the country. The owner can set up a laptop or tablet and watch in real time as a CNC processes a job. If that kind of convenience and oversight are already part of the shop’s culture, it could be quite complicated to upgrade an older machine to those standards.
On the other hand, not everything needs to be that tightly controlled. For example, there’s no question that new machines are going to be more accurate – but we work with wood. It’s an organic material, so a thousandth of an inch here or there doesn’t always make a whole lot of difference. Even when the joinery is perfect, the material eventually moves a little in response to its environment. And the machine’s role and placement in the processing sequence can determine the value of exquisite accuracy. An old table saw reliably breaking down sheet goods or rough-sizing stiles and rails before they are machined and sanded is probably as accurate as it needs to be.
A wide belt sander, on the other hand, can’t be afforded the same leniency: it usually needs to be spot on, especially if it’s thicknessing veneered sheet stock. And those cast iron tables mentioned earlier on jointers, planers and shapers need to be flat and true for production work. If they’re not, they will eat up maintenance time trying to achieve unachievable results. Or worse, they will deliver too many rejects and too much reworking to justify their salvation. The only upgrade left is replacement.
When to upgrade
Poor performance in most machines is caused by tooling. When bits or blades are worn or dull, accuracy suffers. But if new, sharp tools still don’t deliver perfection, then it’s time to audit the machine.
The first thing to look for is noise. If something is loose, it usually vibrates and that creates a hum. If it isn’t something obvious such as a sheet metal housing or maladjusted feet, then it’s time to have a pro check it out. Hopefully, it’s something simple but if the repair is going to cost a lot of downtime or serious cash, it might be an opportunity to upgrade.
If a machine can no longer be adjusted to cut square, flat or plumb, it will cause rejects and rework. If the parts are arriving late or with burned edges, and the tooling is sharp, then something else must be out of line.
If a machine simply can’t maintain the same production rate as the workstations before or after it, that’s a good indication that it’s time to upgrade. That might take the form of a bigger, faster machine, or perhaps even just adding a second unit. But odds are that in a production shop, there’s an automated upgrade out there that will more than pay for itself by speeding up the processing. And depending on the level of automation, the new machine might even eliminate some tasks, processes or payroll expense.
If a machine is constantly breaking down, it may be exhausted from overwork and need to be upgraded.
One other reason to upgrade is changing materials. Sometimes a machine was purchased to process one type of material and the shop has evolved into using something else. Along the way, the old machine has been adapted or persuaded somehow to work in ways that are a little foreign to it. For example, a shop that used to work with solid wood might have moved into coated or veneered panels, and the table saw doesn’t have a scoring blade or a sliding table.
Why upgrade?
One huge advantage to upgrading an older machine is that the shop usually ends up with a piece of equipment that was very expensive in its day but is now affordable. For the same money, the shop might end up with an older high-end, industrial, big production machine with no bells and whistles, or a medium-duty modern machine with glitz and gizmos. And here’s a sobering thought: if an old machine is still running after all these years, it wasn’t sub-par to begin with. It’s a bit Darwinian, but most of the garbage machines went to recycling long ago and only the best have survived.
Another concern is maintenance. New machines come with warranties, service departments, online user groups, and easily acquirable replacement parts. Older machines are more like us: they seem to accumulate lots of nostalgia, wear, and excess weight. But we don’t put Grandpa on eBay for many of the same reasons that we hang onto the old Oliver. We love them both.
Unfortunately, sometimes even replacing parts with salvaged ones from other machines won’t work. Take, for example, planers or jointers with clamshell heads. Early on, these machines had square cutterheads that swallowed a lot of fingers, so several manufacturers went to a cylinder and called it safer. But they just bolted the knives onto flat areas of the cylinder, so quite a few came loose when they hit a big ole knot or some squirrely figure. Rebuilding an older machine and just reusing the clamshell may not be a smart move. Having a new cutterhead made might push the old machine right back up there with a new one in terms of pricing, so it’s something to consider.
Another sticky problem for many restorers is Babbitt bearings. These are poured bearings that are a little softer than the moving part they support, so if something goes wrong the bearing fails, rather than a shaft. Babbitt material is a soft alloy with a low melting point. Woodworkers who aren’t also toolmakers or mechanically inclined may want to find the oldest worker in a local machine shop and take him to coffee to have a chat about Babbitt replacement before buying a machine that is so equipped.
Specific machines
Older drill presses with familiar brand names are usually a good prospect for upgrading as most don’t seem to have many run-out issues. Plus, the older quills often travel far enough to bury a long bit. Laser positioning is an easy upgrade on these machines, but electronic variable speed is a relatively new option so switching belts for speed changes is the only option. But then, how often do we need to do that in the average woodshop? In situations where there are only a couple of bits that are being swapped out frequently, the best upgrade may be buying a second, modern, less expensive press and just leaving a 35mm Forstner bit (or whatever is needed) chucked in it.
When it comes to lathes, most turners will shy away from trying to upgrade an older machine. The new ones have variable speed controls in a couple of torque ranges, larger capacities for swing diameter (although the old ones are usually longer between centers), and that all-important reverse switch that immeasurably improves sanding results. Some new machines even have sliding headstocks that allow very large outboard turning. That’s not a viable upgrade for an older lathe.
Adding a rotary axis to a basic old CNC is often a possibility. And sometimes an aggregate head can upgrade an older machine to perform tasks that are beyond the reach of XYZ.
One machine that most woodworkers will agree is a great candidate for upgrading is a vintage wide (more than eight inches) jointer. Many of the old cast iron tables on these were milled and dressed to the point that wood slid along them like the Jamaican bobsled team. And it still will, with a little TLC. Unfortunately, it can be a challenge to upgrade the knives to carbide inserts, so it’s a good idea to check on the availability of a spiral cutterhead before taking the plunge.
The supply bottlenecks a couple of years ago revealed a glitch in importing. It became difficult to find parts support for some machines that were built overseas. The world is no more stable now than it was then, so such supply woes may well become routine over the next few years. That’s a pretty good argument for researching new domestic machines, or stockpiling sensitive replacement parts, or upgrading older machinery that was made in the U.S.A.
When it comes to vintage iron, here are some great old names to look for, or perhaps hang onto if they’re already gathering dust in the back of the shop: Buss (1862-1964), Delta (1919-), Greenlee (1862-1985), Moak (1918-1992), Newman Whitney (1906-), Northfield (1920-), Oliver (1890-), Porter (1882-ca.1982), Powermatic (1928-), Tannewitz (1909-), Wadkin (1897-), and Yates (1925-). Many of these are still in production, although some have outsourced the machines to overseas manufacturers. But most were active in the heyday of American woodworking equipment, and some still even offer new parts for old machines, or their websites can help locate them.
This article was originally published in the March 2024 issue.
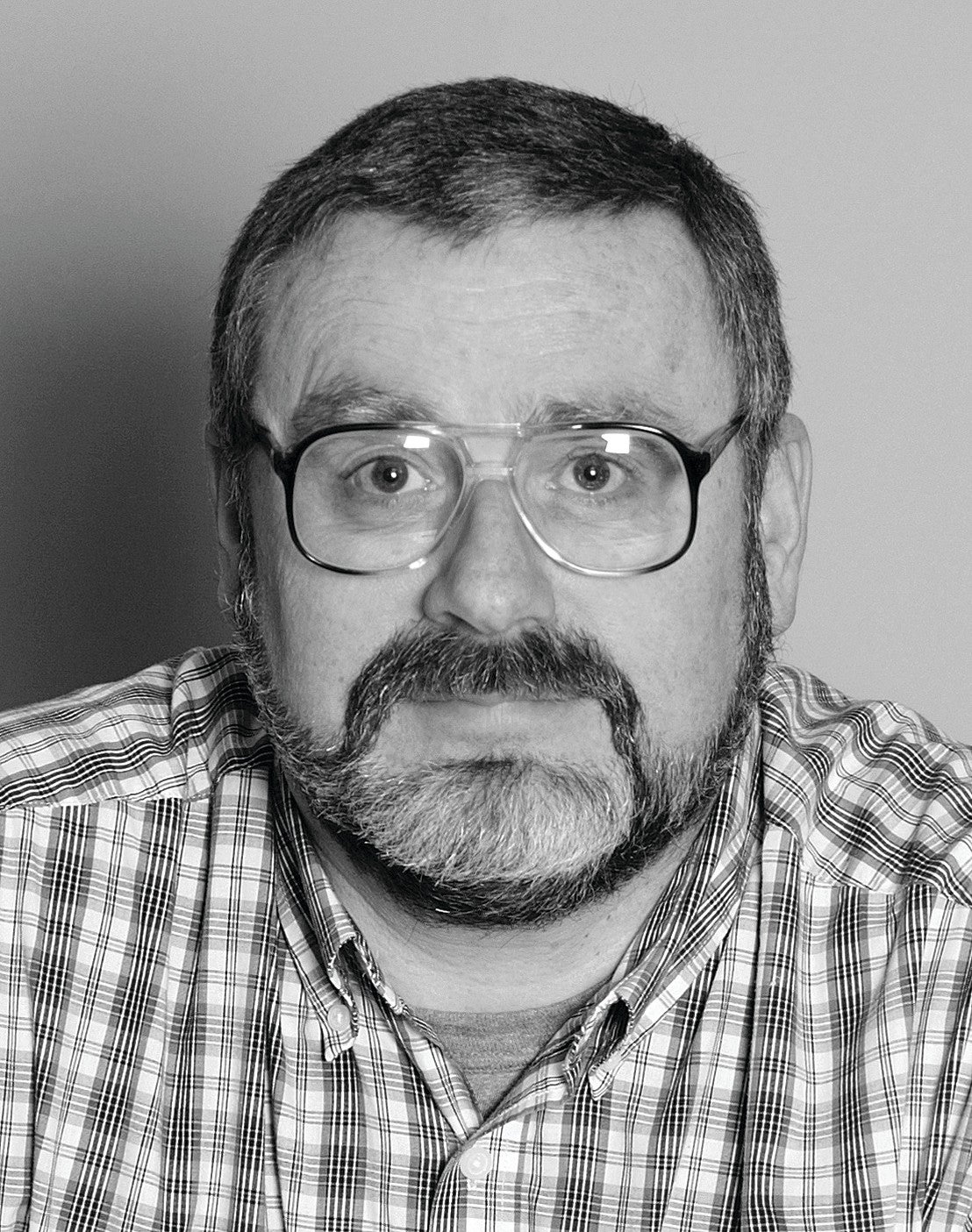