Crossing the finish line
Crisp joinery and great material choices are essential elements of a superior cabinet or furniture job. But applying a decent finish is perhaps the most critical task. The finish is…
Crisp joinery and great material choices are essential elements of a superior cabinet or furniture job. But applying a decent finish is perhaps the most critical task. The finish is the first thing that a customer sees and touches. No matter how skilled the woodworker, if he or she doesn’t have the right equipment, the magic of a glitch-free finish might always be just out of reach.
Spray booths
Starting at about $2,500, commercial cabin booths are within the reach of most small shops. In colder climates, makeup air can be a challenge and many communities have ordinances governing pollution and fire issues, so check with the courthouse before installing a booth. When buying a booth, everyone’s first concern is price and then regulations, but there are some other issues to consider, too.
The key elements of a booth are an enclosed space that contains vapors, eliminates dust and is still large enough in which to work; a spark-protected fan that won’t ignite volatile compounds; and personal respiratory protection. There should never be an electric outlet inside, or even very close, to a spray booth.
Booths are either negative or positive pressure. That is, the air pressure inside the booth is either less or more than that outside the booth. A negative pressure booth sucks air in (usually from outdoors) because the fans constantly reduce the air pressure within the booth. Positive pressure booths are more common when the makeup air needs to be tempered (heated or, in some cases, cooled). Overpressurizing a positive pressure booth can lead to contamination because it will literally open the doors and allow dust in, or it will create an unsteady airflow with turbulence that disrupts the even and controlled flow of finish from the gun. High pressure is often the result of clogged filters: the exiting airflow simply can’t keep up with the makeup flow.
Booths are generally made of steel and in humid areas cold-rolled panels can rust, so galvanized steel is preferred. Powder-coated interior wall panels will last a lot longer than bare galvanized. Gaskets between the sections of a booth and around the openings should be one piece, if possible, and should run continuously along all joints and openings. Square corners are notorious for gasket leaks (which allow dust to contaminate the finish), so many booths now come with doors that have radiused corners.
Good light makes good work and fluorescent tubes need to be placed in such a way that the worker never leaves a shadow on the work in front of him or her. Lighting should be simultaneously direct and raking (coming from the side) so that blemishes and runs show up easily.
Spray guns
HVLP guns and low-VOC finishes have changed the way we spray finishes and, for the most part, they improved things both for the planet, and the woodshop. The key to a good finish using an HVLP gun is to find the perfect balance between the viscosity of the fluid being sprayed and the amount of pressure the gun is delivering. Because the guns are designed for high volume and low pressure, the thickness of the fluid and the flow of air are absolutely critical. If there’s too much thinner in the finish, it won’t fill tiny voids, have much body or last as long as it should. If there’s too much air pressure, controlling the flow becomes difficult and this leads to overspray, dimpling and other quality problems. Checking pressure at the gun (rather than 100 feet away at the compressor) gives a woodworker a better picture of the actual air pressure at the nozzle. This can be done by disconnecting the gun and connecting a pressure gauge for a few seconds at the start of the spraying session. The air needs to be dry and filtered, but the compressor also needs to be large enough to deliver a constant flow of air at the required pressure. If the gun spends air faster than the compressor can deliver it, the flow of finish can fade away right in the middle of a pass.
HVLP guns have a small fraction of the pressure of traditional guns at the tip (usually a maximum of 10 PSI). The secret to a great finish is to atomize the material (break it down into very small particles) so that the solvent can evaporate properly and leave a smooth coating on the wood with very little dieback (fading of the gloss over time). Choosing a tip size is critical and the manufacturer of the finish will have specific recommendations. The tip size will help determine the thickness of coats and this, in large part, controls the drying time.
Guns usually have three controls. The flow or fluid control determines how much finish is passing through the gun. The fan control determines the shape of the spray pattern. And the air adjustment valve (some guns don’t have one: it’s automatic) controls the amount of air passing through the gun. Most finishers will start with the fluid and fan controls wide open and adjust them down until they deliver an elliptical pattern with a wet center that fades toward the outer edges. This test is usually done on scrap wood or even masking paper. Adjusting the airflow upwards will then make the droplets smaller (as it atomizes them properly). Sometimes, the fluid flow needs to be reduced, too.
When choosing a gun, it makes a lot of sense to find one that is a good match for the output of your compressor, rather than first buying a gun and then having to upgrade everything else. For smaller compressors, there are guns that operate on very low pressure. Yes, they take a little longer to get the job done and that’s a possible issue on very large parts where it might become difficult to maintain a wet edge. And when it comes to guns, one usually gets what one pays for. More expensive guns generally have more sophisticated controls that give the woodworker more options with more finishes.
If the shop doesn’t already own a compressor, it might be worth a look at the newest generation of four-stage turbines. These are smaller, lighter, self-contained units that can save a little money. They are essentially boxes filled with fans that deliver a constant supply of air. Early versions were noisy and sometimes unreliable, but they seem to have come a long way. Turbines are rated by stages (that is, fans). A four-stage unit has four fans (low end versions typically have just two fans). The fans run at very high speed, moving a lot of air (high volume) at low pressure. The fan speed and the size of the blades play a role in the amount of air being delivered but, generally speaking, more fans mean more air and that usually means better atomization.
Choose an air hose that isn’t so stiff that it prohibits your movement inside the spray booth or so flexible that it kinks and restricts airflow.
Respirators
Often overlooked as part of the arsenal of finishing equipment, personal respirators have come a long way in recent years. A good, basic respirator usually has a fabric pre-filter that traps larger particles and then a charcoal cartridge that soaks up the fine volatiles. The fabric filter’s primary goal is to stop the finer charcoal filter from being clogged. They usually last about one-third as long as the charcoal cartridges (sometimes called canisters). When you first spray a finish, if you can smell it, then it’s time to change the charcoal cartridge. If you spray for a while, you become less sensitive to the smell, so do that test at the beginning of your spraying session. The paint aisle at most hardware stores will offer a variety of cartridges. Look for one that specifically handles the finish you’re spraying. If not available locally, they are easy to find online.
As with spray booths, respirators are available as either negative or positive pressure models. Negative ones have that soft, rubbery mask that conforms to your face. Positive ones are battery-operated and have a constant supply of fresh air being pumped through a filter to your nose/mouth. Some models use a long hose instead of a filter, so they can supply fresh air from another room or outside the building. Positive pressure masks are more effective at protecting the user, but even negative pressure masks will still eliminate about 90 percent of contaminants.
Guys with beards have a problem with masks. Their facial hair lifts the edges of the mask, allowing much higher levels of contaminants through to the nose, throat and lungs. According to OSHA, the only viable solution is a full hood, rather than a mask.
Razors work, too.
This article originally appeared in the July 2012 issue.
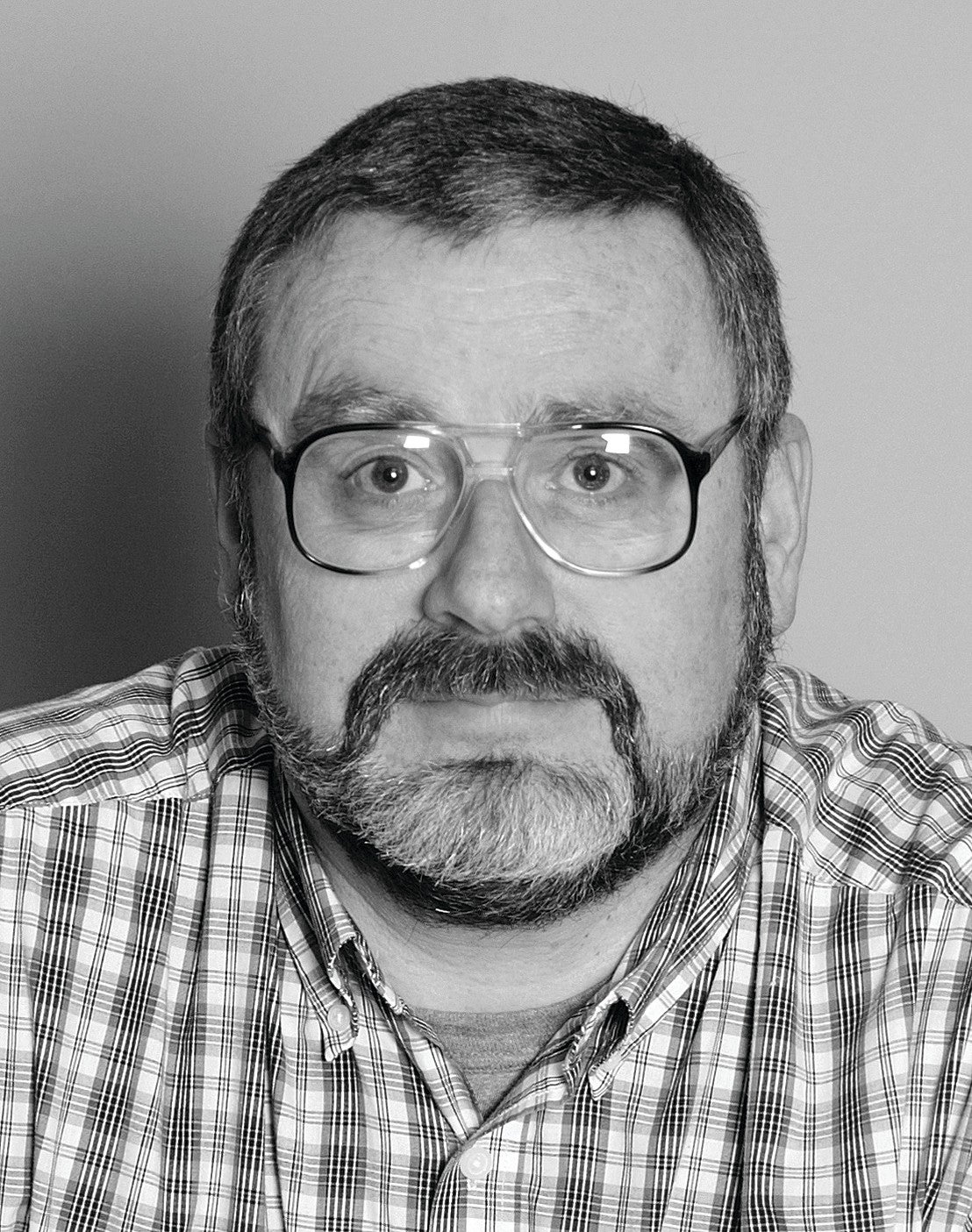