Comfort zone
The setup of a workshop has a big impact on the quality and quantity of the work produced in it. Everything that goes into making a shop easy to operate…
The setup of a workshop has a big impact on the quality and quantity of the work produced in it. Everything that goes into making a shop easy to operate is covered by a branch of behavioral science called ergonomics, which OSHA defines as “the science of fitting workplace conditions and job demands to the capabilities of the working population.” The goal of ergonomics in a professional woodshop is high productivity, avoidance of illness and injury risks and increased worker satisfaction.
While lighting, floor mats and even the radio station are all on the list of factors that affect productivity, perhaps the most important one is organization. Employees appreciate having work flow through the shop in a logical sequence, being able to store tools where they can be found, letting specialists have their own work area and having the ability to move completed jobs out of the way. Keeping aisles clear seems like a basic requirement, but many shops run out of space because of poor organization and the result is that woodworkers are constantly running an obstacle course. One key to solving this problem is putting supplies and finished cabinets (or furniture) on carts, especially if shelving and a forklift aren’t available. That lets a worker clear an aisle temporarily without causing too much downtime.
Sometimes work can be stored at the job site until it can be installed, instead of filling up the shop while the contractor waits for a plumber or an electrician to complete some part of the process. And homeowners are usually willing to make room in a garage for completed cabinets while they wait for granite countertops or some other element of their new kitchen to be ready.
Let there be more light
Lighting is probably next on the list of things that improve the workshop environment. There’s an old shop adage that says the quality of work matches the quantity of light — and there’s a lot of truth to that. Lighting in the shop should be brighter than the lighting at the install site, so that all blemishes show up before the product is delivered. Adding a portable light to each workstation, especially those involved in sanding and finishing, is a sound idea. When a woodworker can move a lamp around, he or she can check surfaces with raking light. This means holding the lamp to one side so that the light flows across the surface, creating shadows anywhere there’s a small depression or a high spot.
Fluorescent lamps are more efficient than incandescent ones (which are no longer produced in the U.S.) and are about five times as efficient as incandescents. That is, they use about one-fifth of the amount of electricity to produce the same amount of light (which is measured in lumens). They require a ballast to regulate the electricity (keep the flow even) and they are a little power-hungry when they start up. But once up and running, they’re amazingly efficient. A lot of the energy used by traditional bulbs becomes waste heat, but flourescents run cool. The electric charge in the bulbs excites mercury atoms and this produces short-wave ultraviolet light.
There are several options to consider when choosing fluorescent bulbs for the workshop. The first of these — color — plays the biggest role in the comfort of the shop environment. Color is essentially how a human perceives the light and it’s described scientifically using the Kelvin scale, which measures heat. The best way to describe the relationship between heat and color is to put it in terms of a forge. A steel bar is silver or black when cold and changes color (red, yellow, white and finally blue) as it gets hotter. Normal daylight is in the range of 5800K (Kelvin). Bulbs that throw a yellow light are at the bottom of the scale (about 2700K), and those at the top become first white, then blue.
Choosing the temperature of bulbs for the workshop affects how people perceive light. Yellow, cooler bulbs feel warm and comfortable (this is the common range for incandescent bulbs), but white or blue/white light can actually make people more productive and comfortable because it simulates outside sunshine. This neutral, hotter light also tends to show blemishes better and improve the quality of work.
On a side note, color temperatures in the daylight range (5000K to 7000K) work well for photography, especially for film cameras, while lower temperatures impart a greenish hue to photographs.
Task lighting is more important than general lighting in the woodshop. While lighting up the whole room with several banks of fluorescent tubes will definitely affect a person’s moods, individual lamps focusing directly on the workbench will have a bigger effect on their quality of work and their comfort level. It’s fairly difficult to have too much task lighting. And not having enough is stressful.
Cooling and heating
While the temperature of light is important, the temperature of the shop’s air also affects performance and comfort levels. Hot, muggy summers and cold, dry winters both take their toll on our bodies, and the fatigue they generate translates into lethargy and, sometimes, carelessness. Air conditioning in a 10,000-sq.-ft. shop with tall ceilings is expensive, so supplying each workstation with its own fan might be a more viable option. Floor model and bench-top fans blowing sideways can actually increase stress: it’s akin to working outdoors on a windy day. Ceiling-hung fans, on the other hand, create a reverse vortex that strikes a smaller target (we’re smaller looking down on us than looking sideways at us). Fans that are placed a few feet away from the workbench will cause less stress, as they don’t tend to move drawings, veneer sheets or other light objects across the bench.
Heat is a bigger issue. The most comfortable air temperature tends to change quite a bit depending on how much energy we are burning. Somebody sitting at a desk all day in front of a computer needs an environment in the neighborhood of 72 F, while workers stacking sheets of plywood on racks probably wouldn’t mind it being in the 50s. Even workers performing tasks at the same bench might have different preferences. If one is just assembling small parts, while another is physically sanding them, they’re burning different numbers of calories in their personal furnaces.
Shops with tall ceilings tend to be coldest near the floor, so there’s a huge advantage for companies building new facilities nowadays. They can install radiant floor heat, which is evenly distributed and very comfortable. Traditional hot air systems dry out the air, but the addition of a humidifier in the ductwork can lead to a huge improvement in comfort levels.
Heat travels in one of three forms. Conduction is the flow of heat through solids or liquids. An example would be heat traveling out from a campfire along a metal marshmallow fork. Convection is heat flowing through a liquid or gas and a good example is a kettle boiling. It transfers heat from the stove to the water at the bottom, which then rises, allowing cooler water to fall and, in turn, be heated. Radiation transfers heat by electromagnetic waves or photons, so it moves at the speed of light and it doesn’t need to heat the air, just objects. For example, the heat from the sun doesn’t heat the intervening 93,000,000 miles of space to the same temperature that it heats the earth. Radiant floor heat warms objects (and people) and these, in turn, heat the surrounding air by convection. In a workshop, radiant heat (in the floor or suspended overhead) can make a lot of sense. It’s more economical to heat objects than the air. Plus, dust building up in ductworks and furnace filters isn’t an issue.
Dust and noise
Speaking of dust, a good central dust-collection system is absolutely necessary for worker comfort and safety. Ceiling-hung air scrubbers are also essential as they can filter out particles below 1 micron that large vacuums expel. But perhaps the most dramatic and effective way to deal with dust is to collect it before it disperses. One can set up the shop so that all sanding is done over a downdraft table. Or you can use complete systems such as the line from Festool that marries a portable sander to a shop vacuum, so that dust is localized and collected before it contaminates the entire air supply in the shop. (See “Breathe Easier” in the November 2011 issue for a discussion on installing a complete dust-collection system). While the central collector traps dust from stationary machines such as planers and wide belt sanders, low decibel shop vacuums do the same job for portable tools.
That decibel (dB) level is very important to workers’ comfort. The National Institutes of Health (www.nidcd.nih.gov) have established guidelines on noise levels that can cause hearing loss. They recommend wearing earplugs or, preferably, EPA-approved earmuffs when involved in a loud activity. According to the NIH, regular exposure to sounds of 110 dB for more than one minute puts a worker at risk of permanent hearing loss. They have also established that prolonged exposure to any noise at or above 85 dB can cause gradual hearing loss. As a frame of reference, normal conversation is at about 60 dB, while a chainsaw emits about 100 dB.
Most woodshop machinery is in the 85- to 110-decibel range, especially tools such as portable routers and stationary planers. Earmuffs with a 30 dB reduction rating bring those higher volumes back into the tolerable range (55 to 80 dB). Unfortunately, training workers to act responsibly and wear earmuffs can be quite a feat.
Anti-fatigue mats and proper footwear are other key ingredients in the ergonomics of a woodshop. Many companies will offer to pay for a portion of the bill for decent work boots that replace athletic shoes on the shop floor, because they know their workers won’t tire so easily. It’s just one small way to improve worker satisfaction and productivity.
This article originally appeared in the February 2012 issue.
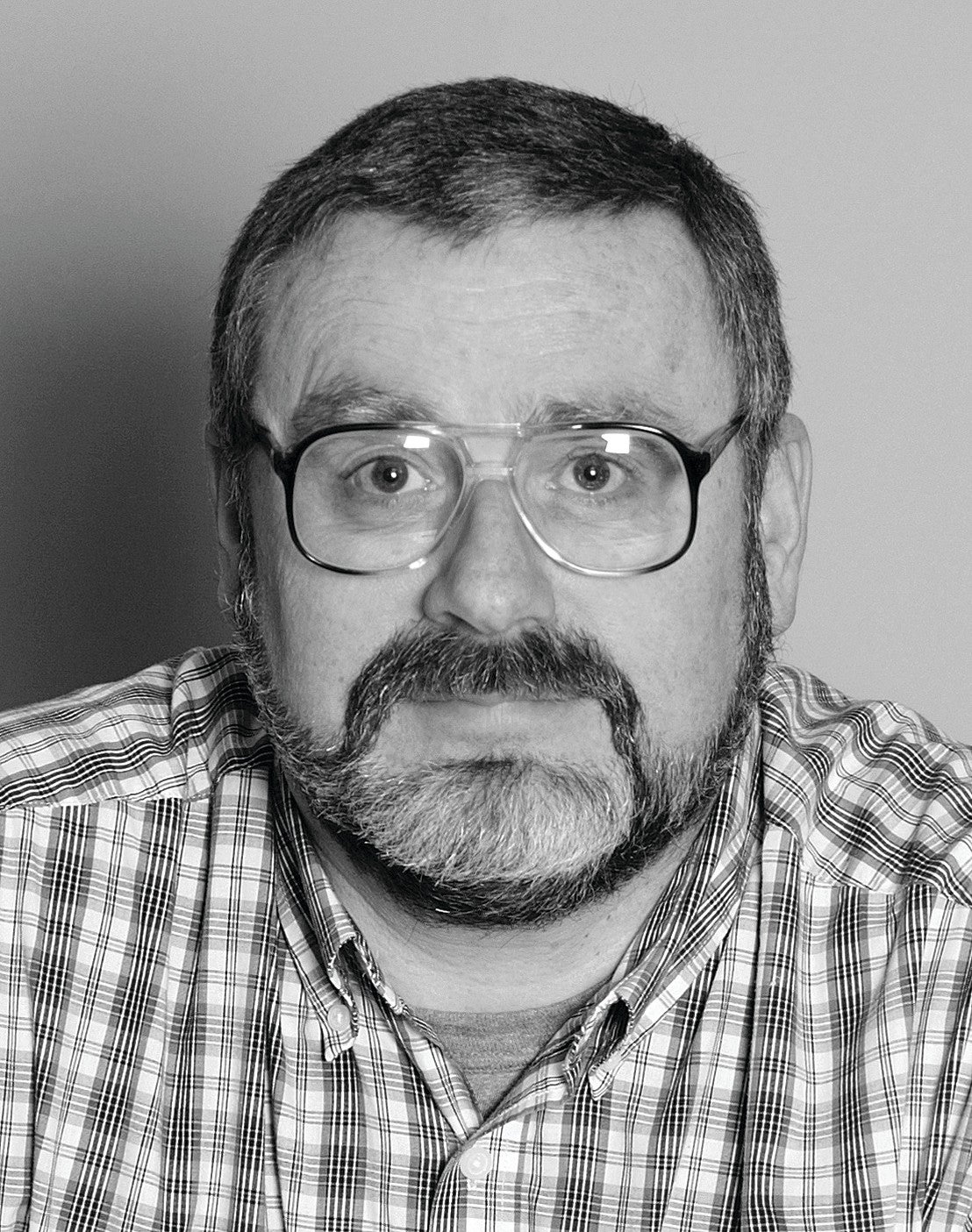