CNCs that ‘do It all’
Shops searching for multi-function machines have plenty of choices in today’s marketplace.
The European landmass is about the same size as the U.S., with two and a half times the population. And in western Europe, more than 80 percent of people live in cities that are very close together. Given those tight quarters, it’s no surprise that space is at a premium. That may account in part for the penchant among European woodworkers toward space-saving, multi-purpose machinery. And while there certainly are some U.S. shops that also espouse and treasure that option, most American cabinetmakers and furniture builders still prefer their single-purpose, stand-alone machines.
But that’s changing, in large part because the way that we build cabinets is changing. As more and more shops incorporate or expand their CNC capabilities, they’re asking those machines to do more tasks. Woodshops are now demanding that the next generation of CNCs is, well, multi-functional.
And manufacturers are listening.
Take, for example, the new ‘driverless’ Python XPR from CNC Factory (cncfactory.com) in Santa Ana, Calif. Produced in the U.S., it can be ordered with automated loading and unloading, spoil board self-cleaning, hands-free robotic labeling and printing, laser measuring for critically precise depth-cutting, and even part marking for post-production processes such as edgebanding and inserting fasteners.
“With these labor-saving and time-saving features,” says CNC Factory’s Chris Corrales, “the 2019 Python XPR lets the operator push a button and then collect the finished, labeled and marked product.” The technician never even needs to touch the panels.
Such machines are becoming possible because of advances in both programming and robotics. And they’re becoming more ubiquitous because the price tag on this leading-edge technology continues to drop. The opportunity to own such a CNC is now within the grasp of even the smallest shops, because these multi-function machines can replace more than one potential employee – and do so at less than the cost of paying those un-hired people for a single year. As such, for year two and all subsequent years of operation, the machines are theoretically cost-free.
They are also coming along at precisely the right time for the industry, when woodshops are having a difficult time recruiting qualified employees. The machines don’t just replace the need for muscles and brains, they also make the future of woodworking more attractive to a younger generation that prefers to program and run apps than heft MDF around the shop.
And CNC technology can be quite intimidating. This is, after all, high tech. A woodshop needs to seriously consider training and after-purchase technical support, plus in-house expertise when investing in a CNC. You can’t make these machines do what they’re supposed to do unless you know how to run them. That’s a very real concern, but there is help.
Since 1990, Stiles Machinery (stilesmachinery.com) in Grand Rapids, Mich., has trained more than 38,000 people through its Stiles University in such areas as machine operation, advanced CNC programming, effective troubleshooting, maintenance and related areas. And when it comes to taking advantage of that training, the company offers a number of machines that can do it all, including nested-based CNC routers, CNC vertical drills and twin table machines. In its CNC routing and machining catalog alone, there are some 39 Homag offerings. When a woodworker comes across websites with that much technology to explore, it’s probably best to contact a salesperson at the company and physically discuss exactly what one needs the CNC to do.
Another industry giant, C.R. Onsrud (cronsrud.com) in Trautman, N.C., also offers a dizzying array of machines (there’s a link at the top of its homepage to the latest catalog). Every machine is tailor-made and begins with one of the company’s standard frames. After that, the CNC is “built for optimum performance to the unique manufacturing specifics of your application,” according to the company. When shopping for a new CNC, keep in mind that one can buy off the rack or visit a tailor.
More than material handling
For custom woodshops, the most important feature of a new CNC has to be flexibility. Automatic loading and unloading, or the ability to print on parts are definitely attractive qualities, but the core machine must also have the potential to switch gears and make something other than the parts for a rectangular box.
Biesse’s new Rover A is billed as just such. It’s a single work center for many types of machining operations, and the company (biesse.com) says that it’s an ideal solution for shops that build casework but also windows, doors, stairs, worktops and furnishing items. That versatility comes from a 5-axis ability, with continuous rotation of the B and C axes. It also doesn’t need to rely on an operator with a tape measure: the machine is equipped with an electronic positioning system that automatically reconfigures the entire work area as needed, using separate motors to move tables and carriages without engaging the operating system. And one more reason this machine can “do it all” is that it has the capacity for up to 39 tools, so downtime after the initial setup is virtually eliminated even on complex custom projects. Biesse has locations in Anaheim, Calif., and Charlotte, N.C.
Another way that manufacturers bring versatility to CNCs is by adding an extra work table. Castaly (cncroutergroup.com) in La Puente, Calif., offers a couple of twin table models including the Twin 408 (with a work area of 4’ x 8’) and the Twin 510RT (5’ x 10’). One moving gantry serves both tables, which are set up end-to-end. The double work tables alternate processing, automatic switching and automatic feeding, so essentially two full sheets can be processed by one machine.
Among its 26 Format4 machining centers, Felder Group USA (felder-group.com) is now offering the new Profit H500 MT. Beyond its 5 axes and 34 tool positions, this machine shines in its smooth integration of in-house developed software that has clear menu guidance and intuitive operating. That concept of having both the machine and the software developed by the same supplier allows Felder’s CNCs to be impressively flexible and customizable. The H500 MT also comes with an aggregate interface with a cardanic (it’s a medical term meaning both flexible and rotating) 5-axes head. Label printing is an option, too, and woodshops can order the machine with a phenolic matrix table that allows for all kinds of vacuum hold-down options.
Another European manufacturer, Casadei Busellato USA (casadeibusellato.com) has a North American location in Duluth, Ga. The company offers several configurations and working areas for its Jet Master CNC, and the guiding principle in its design is flexibility. They have motorized panel supports that allow completely automatic management of the working table – the Jet Fast feature provides quick positioning of the panel supports, suction cups and clamps with no intervention by the operator. The Jet Master RT model’s table has a rectangular grid for processing with vacuum cups or nesting, and here’s a small but valuable feature – there are little plugs that can direct vacuum more efficiently.
For shops that need to work with large materials, AXYZ (axyz.com) offers woodshops an impressive scale of processing areas, all the way up to 128” wide and more than 50’ long. Its CNCs are available with two heads and up to 33 tool changes, an aluminum vacuum deck that can be manually or automatically controlled, and the AXYZ Vision System which uses registration marks on printed materials to adjust the cutting program for perfect alignment.
Integrated software
Weinig/Holz-Her (weinigusa.com and holzherusa.com) recently introduced its new Nextec, which it says will revolutionize the way woodshops work. Here’s how the company describes it: “Just a mouse click is all that is required to select the desired template from the comprehensive library. In just two steps you can adapt the furniture to meet custom specifications – from the dimensions to the material and fittings. Then simply position the material on the machine.” The Nextec software automatically generates all CNC processing programs, parts and material lists as well as the optimum nesting pattern for the workpieces. Designed for small to medium-sized shops, the software and machine system comes with over 300 customizable CAD cabinets and furniture in the library, and optional CabinetControl Pro software lets a woodworker design and configure cabinets, build libraries and define materials or fittings. Among the machines that match the software is a highly flexible 5-axis model with options such as an automatic pusher and conveyor belt, lifting table, and the ability to integrate into an automated panel storage system.
Libraries are also at the core of the Cut Ready Cut Center, an alternative to traditional CNC routers that comes from Indiana-based Thermwood (thermwood.com). These machines are designed for making a wide variety of products including cabinets, closets, furniture, doors, drawers and much more. The woodworker just tells the machine what to make and it does it. No programming is required. It’s an ideal option for shop owners who aren’t too comfortable with high-end technology, and for those who like to dabble, the company also offers a full range of 3- and 5-axes CNCs, plus some additive technology CNCs (very large 3D printers).
Man & machine
Anyone who has read Dan Brown’s novel Origin is familiar with his prediction of Technium, a future world where machines and humans fuse into a single new symbiotic species. It looks like SCM Woodworking Technology (scmgroup.com) is already there. Automation through integrated robotics will be the focus of the company’s “Smart & Human Factory” event being held at the beginning of February at its global headquarters in Rimini, Italy. It’s all about humans and robots working together to “do it all”. The event is built around new CNC systems that are more flexible, modular and easily reconfigurable, and are designed to provide an increasingly effective, quick response to the challenges of what SCM calls mass customization – the option to reconfigure quickly in order to process smaller batches. Keep an eye on the SCM website for updates.
Another leading-edge manufacturer, Diversified Machine Systems (dmscncrouters.com) builds a variety of 5- and 3-axis CNCs that are specifically designed to specialize in custom solutions. The company’s Advanced Manufacturing Center is an R&D facility designed to help clients bridge key manufacturing knowledge gaps. For woodshop owners who are new to manufacturing, or are re-tooling an existing business, this is a great way to witness man and machine at work together. On site technicians help clients figure out exactly how to make specific parts.
New Jersey’s Komo Machine (komo.com) manufactures all of its CNCs in the U.S. and this company also invites prospective clients to its facility. Komo will actually do a run of your parts and demonstrate real-time performance in person. The company says that “seeing pre-rehearsed, debugged CNC programs running at a trade show or demo center is one thing. Seeing your part programmed and run right in front of you is a more accurate measure of performance.”
New CNC (newcnc.com) in Holland, Mich., has a broad range of 3-, 4- and 5-axis machines. On the company’s Auto Load and Unload (AL/UL) model, sheets are loaded into the machine via lift table and then barcoded and fed into the CNC router automatically. A vacuum table secures parts during the routing and boring process, and then they’re moved from the router table to the outfeed table where the operators can stack parts while a vacuum system cleans the dust from the table.
Overwhelmed by the options?
You’re not alone. Most complicated processes are going to require several axes, perhaps an aggregate head and some specialty tooling. When it comes to the basic machine, NexTech Machinery (nextechmachinery.com) in Cornelius, N.C., says that its M900 5-axes router “will appeal to the entrepreneur and those buying their first five-axis CNC router. Just decide on your table size and whether an automatic tool changer is required. Almost everything else is included.” It’s a heavy-duty outfit with a massive gantry and it’s suitable for casework and furniture production. The M900 is equipped with separate controls for working speed, traveling speed and cutting speed, and comes in a couple of table configurations for full-sheet work.
Woodworkers who are looking for an entry-level system that can do all the things a small shop would want to tackle, might take a look at the lineup from Axiom Precision (axiomprecision.com). Its machines have no complex software and a powerful hand-held controller that is intuitive and easy to use. Axiom offers lifetime technical support.
Another entry-level option is a desktop model from NextWave Automation (nextwaveautomation.com). The new Shark HD4 Extended lets a shop install its own router, and work from its own PC. It comes with Virtual Zero software that maps the surface of the table or workpiece and eliminates problems caused by warps, bows and small inconsistencies in the table.
Martin Machinery (martin-usa.com) offers the Protec, a very compact and highly configurable CNC center for efficient processing of drilling, grooving and routing jobs. This machine has been developed specially for just-in-time manufacturing, as well as large batch production.
A woodshop that is looking at do-it-all machines might actually be searching for a standard machine that can be set up to do a very specific task. In that case, there may be another option. Laguna (lagunatools.com) has several standard CNC models in its line-up, but also caters to a number of niche artisans. Its catalog offers a multi-tool series that serves sign makers; some turning CNCs that can do 360-degree routing and deliver lathe-like results at an industrial pace, and the company’s LS4 Lockdowel machine that can drill and insert fasteners so a shop doesn’t have to deal with screws and glue. The company also offers stand-alone CNC controlled plasma and laser options.
Camaster (camaster.com) in Cartersville, Ga., also offers a machine dedicated to sign making. The SignPro will do both machining and digital cutting, and it comes with a 4-hp HD quick change spindle and an oscillating tangential knife. Options include the Optiscout vision registration system and automatic tool changing.
Jenkins (jenkins-systems.com) specializes in CNC sanders and shapers.
Among its many models, Techno CNC (technocnc.com) has an entry-level machine, the HD II 2136, which is a tabletop version of a full-scale CNC. It has a 20.5″ x 36″ processing area, with 7-1/2″ gantry clearance and a 9-1/2″ Z-axis stroke.
Legacy Woodworking Machinery (lwmcnc.com) has two entry-level Maverick CNCs (3’ x 5’ and 4’ x 8’), but the company’s larger Gemini model is the real gem for shops that want a CNC that does everything. The Gemini has three separate work stations – a 3-axis table; a 5-axis turning center that can turn, index, carve and machine between centers, even on a tapered component; and a 4-axis vertical clamping table that’s located at the end of the machine and lets the operator work on ends or edges.
For medium to large shop owners who are just beginning to explore CNC options, they can get a quick overall view of just how a CNC “does it all” by visiting Anderson America’s site (andersonamerica.com) to watch a video of the Stratos Pro pick up a sheet of melamine-coated MDF, place it exactly where it needs to be, mill parts for a cabinet, and then deliver the parts to an outfeed table as it simultaneously picks up the next sheet – all without a real live person in sight. The company operates a showroom and technology center with multiple demo machines in Charlotte, N.C.
Up the road in Durham, N.C. the engineers at ShopBot Tools (shopbottools.com) have worked hard to make 5-axis CNCs affordable for prototype builders and patternmakers. The 5-Axis PRSalpha CNC is a smaller version of full-scale machines, perfect for machining softer materials but not designed for production work in hardwoods. Here, the table rather than a gantry is moving. The work area is just 34” x 34”, although the X axis can be extended. The tool also offers an impressive 24” in the Z axis (approximate, depends on the length of the cutter), and includes a 2.20-hp HSD spindle. ShopBot also offers several models of full-sized, production capable gantry tools.
Other resources well worth a visit when shopping for a do-it-all CNC are the websites of Limtech (limtechindustries.com), SNX Technologies (snxtechnologies.com), Atlantic Machinery (atlanticmach.com), Hendrick Mfg. (hendrickmanufacturing.com – the HSR-V 5 axis is especially appealing to shops that work with curves), Masterwood (masterwood.com), Shop Sabre (shopsabre.com), Velox (veloxcncrouters.com), Vision Engraving & Routing Systems (visionengravers.com), and last but most certainly not least is the comprehensive catalog of U.S.-built CNCs at Dallas-based MultiCam (multicam.com). Here, woodshops will find tables from 2’ x 4’ to 10’ x 60’ and beyond. The company supplies vacuum tables and pumps for easy parts fixturing, spindles from 4- to 20-hp, and the vaunted MultiCam EZ motion control systems with multiple home positions.
There has never been such a great time to start looking at multi-function machinery.
This article originally appeared in the February 2019 issue.
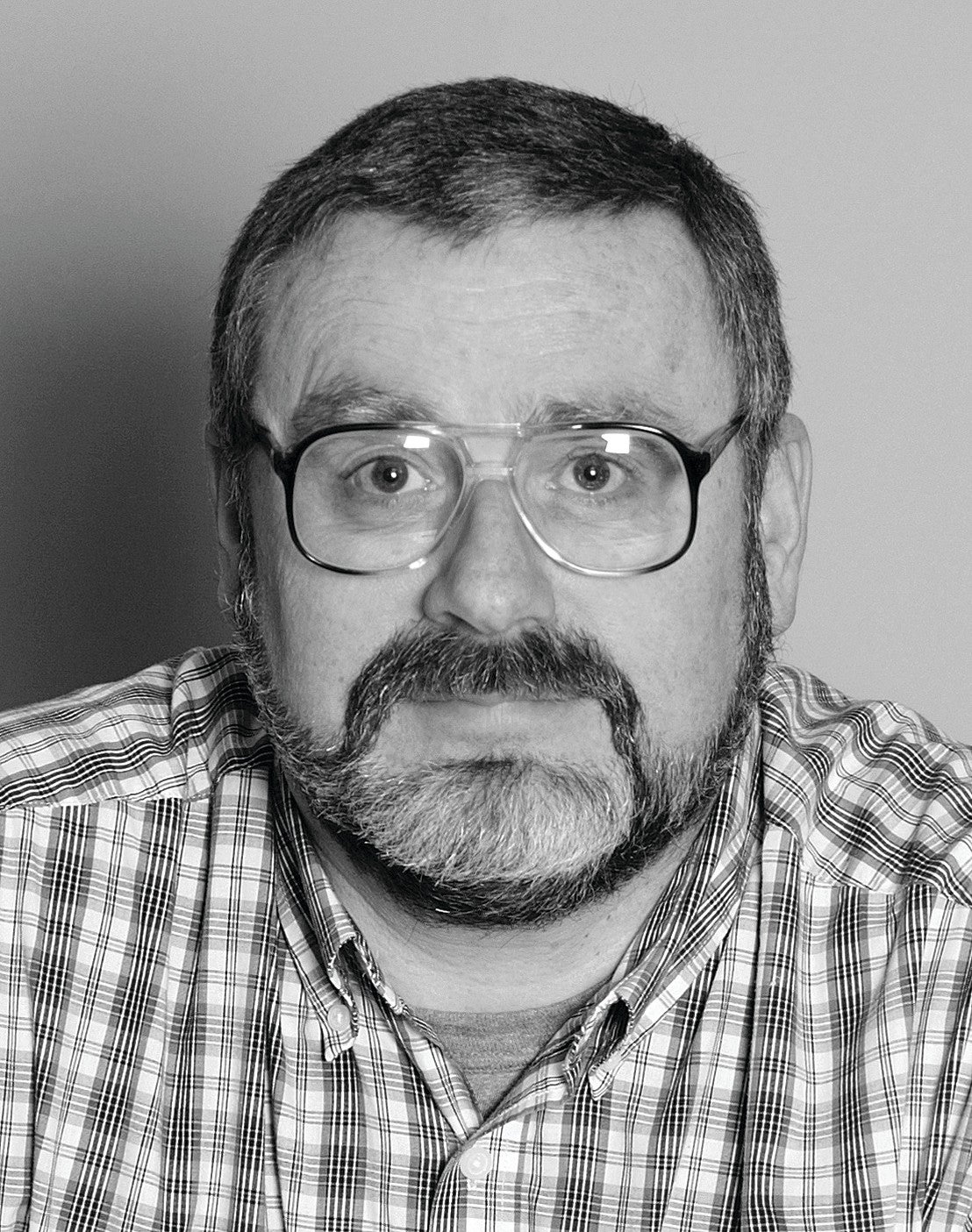