CNC hits a whole new level
Last summer, Woodshop News reported that Rockler had introduced two models of the Click-N-Carve, a compact CNC routing machine that turns digital input into detailed carvings. That product line has…
Last summer, Woodshop News reported that Rockler had introduced two models of the Click-N-Carve, a compact CNC routing machine that turns digital input into detailed carvings. That product line has expanded now to include three models of the CNC Shark. And what’s significant here is that these machines bring CNC technology to the home workshop or small professional shop for about the price of a decent hobbyist table saw.
There are several ways to compare small CNC devices, from the speed of travel in each of the three axes to the power of the motor or the size cutter shaft that they can accept. But as some come with a built-in spindle and others require a separate router, perhaps the most useful way to initially distinguish them is to list the largest capacity workpiece that each can handle. Once a shop knows that certain models can handle the size panels they need to mill, they can then visit the manufacturers’ websites (which we list here) and begin comparing all the other relevant attributes.
With that in mind, let’s note that the Rockler (www.rockler.com) entry-level CNC machines mentioned above have maximum capacities that run from 12.8” x 5.9” to 28.5” x 36”.
Rockler is by no means the first to tackle this market segment. Small woodshops — and larger companies that wish to experiment on a small scale — now have an arsenal of CNC technology available to them. For example, Biesse (www.biesseamerica.com) currently offers the Klever and Rover J routers that are billed as “the answer to increased production for growing shops.” These are full function industrial machines that cost about the same as a woodworker’s annual salary and their work capacity is considerably larger than the Rockler models (available sizes are 4’ x 8’ and 5’ x 10’).
While the smaller machines are designed to add an occasional accent to something like a sign or a cabinet door (the Click-N-Carve can translate digital photographs into extremely intricate carvings in just minutes), the two machines from Biesse can potentially revolutionize a production shop’s bottom line. The Klever is ideal for both panel processing and cabinet/furniture component manufacturing. It moves fast enough for high production and features a built-in controller for programming at the machine. Biesse’s Rover model is slightly less expensive and is ideal for smaller custom woodshops because it can cover a broad range of nesting applications such as making components and doors. It has a hand-held controller instead of a built-in one, a factor that helped shave a few dollars off the price.
Scanning the landscape
California’s Laguna Tools (www.lagunatools.com) offers the easy-to-use IQ, an entry-level CNC model that is referred to as a heavy-duty “desktop” machine. Assembled in the U.S., it’s designed for small shops entering the market and also for medium-sized shops that need a smaller format for light production, or perhaps to use as a prototyping machine. The IQ has a one-piece welded steel frame, 2-hp liquid-cooled spindle and “features the networking, connectivity and online troubleshooting typically found in Windows environments without the Windows baggage.” The IQ runs industry standard G-Code that can be created from any CAM software package.
Laguna also offers a complete line of small-to-large CNC upgrades that include the Swift, D, Smartshop and Puma models. Between them, they offer tables that range from 24” x 36” to 60” x 120”.
Similar to the Shark machines from Rockler are two desktop models from Redford, Mich.-based Romaxx Systems (http://romaxxcncrouters.com). The HS-1 has a 24” x 14” X-Y capacity. With its easily identifiable gold-colored gantry, the HS-1 is a cost-efficient option with a balance of precision, power and speed. The ways are adjustable and the drive system uses a high-tensile cogged belt that is commonly found in larger industrial CNC machines. Romaxx’s more expensive WD-1 desktop model is open-ended, so it can handle work that is any length by up to 25” wide.
Industrial CNC’s Renegade XR (48” x 96”) is a 3-axis, ball screw drive machine that was “specifically designed for the budget-conscious sign maker, woodworker and cabinetmaker.” It delivers full 3-D carvings and flat cutouts in plastics, wood, Romark, MDF, aluminum and sign foam. And Probotix (www.probotix.com) is a Peoria, Ill.-based stepper motor provider that offers a line of entry-level CNC machines called the Fireball line. It includes the X90 (18” x 18”), the V90 (12” x 18”), the Meteor (25” x 50”) and the Comet (25” x 25”), which the company says is the most affordable and complete CNC router in the world.
Zenbot (www.zenbotcnc.com), founded in 2006 by Shaun Morris, is a small company in Tulare, Calif., that has “a passion for creating affordable CNC machines.” Starting at $499, Morris’s product line certainly seems to be meeting that goal. The Zenbot Mini has a 9.575” x 13.5” table and travels just 6” in the X-axis and 8” in the Y-axis. His largest entry-level CNC is the Zenbot 4848 (with a 56-5/8” square table) with a drive system that features 3/8” wide Kevlar-reinforced urethane timing belts on all three axes. The package includes a router body (eight choices are offered), an optional control box and an optional $149 software package.
More sources
Other manufacturers worth investigating include SCM (www.scmgroupna.com), whose product line leans more to high-end production and also a line of four machines from Vision (www.visionengravers.com) that runs the gamut from the desktop 1624R (16” x 24”) to the VR48, a floor model that handles work up to 48” x 96”.
Familiar to most woodworkers, ShopBot (www.shopbottools.com) has been a leader in this market segment for a long time. The North Carolina company was founded in 1996 and almost 6,000 ShopBots are currently at work in small shops and larger production facilities across the U.S. and around the world. Its ShopBot Desktop can be ordered with either a Porter-Cable 2-1/4-hp router or an industrial spindle and handles workpieces up to 24” x 18”. The line runs all the way up to 144” x 60”, and each ShopBot includes PartWorks and PartWorks3D software. PartWorks allows you to design and create 2-D and 2.5-D parts, while PartWorks3D creates tool paths from the 3-D design software of your choice. Both programs simulate the cutting of parts, so you can verify that they will be created just as you intend.
Before settling on an entry-level CNC, one should visit the websites of Epik (www.raptorcnc.com), the 36” square Shop Sabre (www.shopsabre.com), the EG series from Eagle Eye (www.eagleeyecnc.com) and the Stinger 1 from CAMaster (www.camaster.com). While some of these are a bit more expensive than the basic desktop models mentioned elsewhere, most offer industrial strength in a small package.
Other machines to research include the LC Series from Techno (www.technocnc.com); Camtech and Pacer Series from AXYZ (www.axyz.com); the 5-axis S- Series from C.R. Onsrud (www.cronsrud.com); the iCarver from General (www.generalcnc.ca); the NXT Series 3-axis router from Hendrick Mfg. (www.hendrickmanufacturing.com); the Classic Series from MultiCam (www.multicam.com); a collection of five carving models from the venerable Oliver Machinery (www.olivermachinery.net); new and used high-end models from Omnitech (www.omnitech-systems.com); a complete line of automated wood carving systems from one of the oldest names in the industry, Thermwood (www.thermwood.com) and the extensive offerings from distributor Stiles Machinery (www.stilesmachinery.com).
As CNC technology has been around for a while, buying a used machine is a viable option. Shopping on government surplus websites or through used machinery dealers such as K.D. Capital Equipment (www.kdcapital.com) might allow a woodshop to acquire a sheet-goods-capable entry-level CNC setup for the same investment as a small new desktop carving machine.
Questions to ask
Perhaps the most important thing to bring up with your salesperson when searching for an entry-level CNC machine is the software compatibility. Will the machine accommodate high-quality aftermarket programs from companies like ArtCam, Cabinet Pro, CABmaster, Microvellum, Planit, Enroute and Vectric?
Ask, too, about the power source (some are 3-phase), the table size, feed rates, cutting speeds, dust control, the tooling diameters, whether a tool changer is available and what the amount of travel is in each of the three axes (the machinable area is generally quite a bit smaller than the actual table dimensions). If you build arched raised panel cabinet doors, be aware that some machines break arcs into small straight increments, rather than describing a true, smooth curve and the panels could then require extra sanding.
Speed might or might not be an issue. Think about how the machine will be used. If it will be making components all day long every day, you’ll need a lot more machine than a shop that will only use it only occasionally to create, say, decorative panels. The former might spend the same amount of money on a big, used machine that the latter spends on a high-tech, brand-new little machine that is designed to carve more than cut.
Before buying, check out the manufacturer’s reputation for support, customer service and even parts availability. The easiest way to do this is to search for online chat rooms and forums. Some machines even have user groups that post billboards online. Keep in mind that the supplier needs to get you up and running, but it’s also your responsibility to learn how to operate the system — and that takes time. Ask the supplier if it has a customer within driving distance of your shop who operates one of its machines. If so, most woodshop owners will be quite helpful and chatty and might even offer a demo. Some manufacturers reward customers for this type of contact, so ask if the company has a program in place.
One final thought: If your investment will be more than a few thousand dollars, you might want to consider going to one of the big woodworking shows in Las Vegas or Atlanta and seeing all of the manufacturers together in one venue. For the price of an airline ticket and a couple of nights in a hotel, you can enjoy a hands-on and personal tour of all the options.
This article originally appeared in the February 2013 issue.
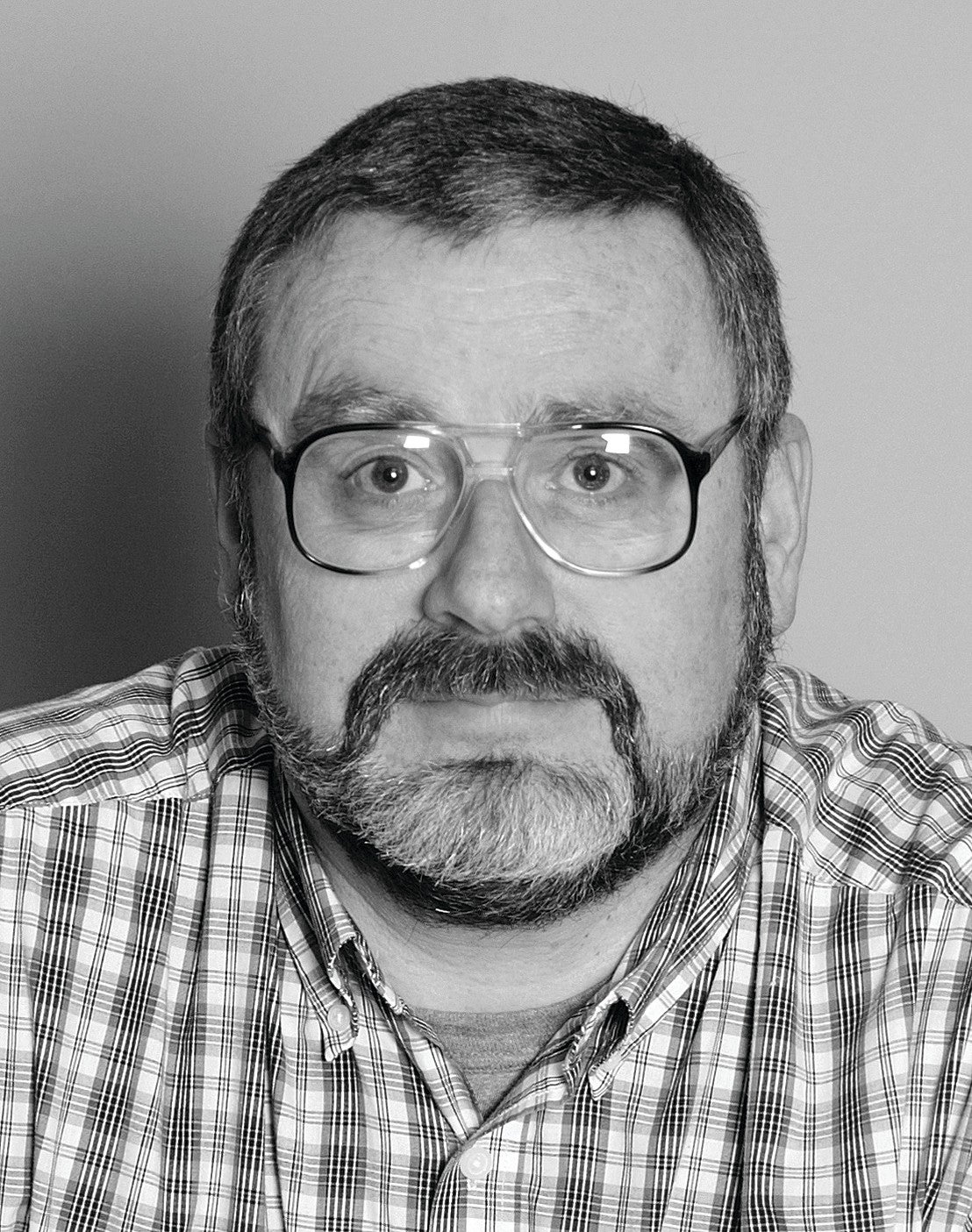