CAUTIOUSLY OPTIMISTIC
CAUTIOUSLY OPTIMISTIC: As the wood industry deals with challenges and economic uncertainty, continued growth is predicted.
Anyone who attended IWF in Atlanta last August got a good anecdotal overview of the wood industry. The tone was cautiously optimistic, with sound sales records to build upon but a wary eye on interest rates and tariffs.
Since then, one of the stories gathering steam has been the trade war with China. For example, in October the Wall Street Journal published an article on ways in which it says China is dodging American tariffs on plywood and other products by simply changing the import codes that U.S. Customs uses to flag taxable items. The newspaper reported that there are some 18,927 different codes, and Chinese companies just re-brand its product with one that fudges the line. This practice is apparently affecting everything from logs to sawblades.Arguing the other side of that issue, International Wood products Association executive director Cindy Squires released a statement that included: “The surge in code classification rulings reported is not an indication of questionable export classifications, but a sign that importers in this high tariff environment are checking if products are properly classified and asking for government rulings when it is unclear. Obtaining a classification ruling is one of the specified actions that U.S. Customs and Border Protection has stated demonstrated that an importer is fulfilling its legal obligations to comply with the law.” IWPA is an international trade association representing imported wood products in North America.
The two nations are also playing at brinkmanship. The USDA’s Foreign Agricultural Service said on Sept. 18 that “China’s State Council Tariff Commission announced that it would start enforcing additional import tariffs on U.S. products exported to China valued at $60 billion.” This was in response to the U.S. announcement of proposed additional tariffs on $200 billion worth of Chinese goods entering American ports. The new list from the Chinese government includes coniferous wood in chips or particles (which can be used in the manufacture of OSB, MDF and chipboard), sawdust and wood waste, coniferous wood in the rough including several varieties of pine, larch, Douglas and other fir, and spruce. Also included were hardwoods being exported, especially oak, birch, poplar, cherry, maple, walnut, ash and beech. Veneers were listed too, as was particleboard, fiberboard, OSB, plywood, and some finished products such as picture frames, cases, windows, posts and flooring, including wood marquetry and inlaid wood. Overall, the scene is set for another round of tit-for-tat tariffs early in the new year with nobody blinking, and that is despite a looming recession in China and huge budget deficits in the U.S.
Another major story in the wood industry is new home construction, which is of course related in part to the trade imbroglio. Primarily because of tariffs and a couple of large hurricanes, the cost of building a home skyrocketed over the past few months and has only just begun to settle. As a result of that and other factors including the cost of borrowing, new housing starts reported in October were down a bit. The Department of Housing and Urban Development had some querulous news about apartment buildings, stating that “privately‐owned housing units authorized by building permits in September were at a seasonally adjusted annual rate of 1,241,000. This is 0.6 percent below the revised August rate of 1,249,000 and is 1.0 percent below the September 2017 rate of 1,254,000.”
On the other hand, single family permits were up 2.9 percent over August, so there was a bit of good news there. Actual multi-unit housing starts were down 5.3 percent from August, and single-family home starts were down 0.9 percent in the same period. Plus, single-family completions were down 8.7 percent from August. As more tariffs kick in early next year and interest rates continue to rise, many economists are predicting a slowdown in home construction.
Robert Dietz, chief economist with the National Association of Home Builders, said in late October that “home price gains and rising interest rates are slowing down the housing market, particularly in high-cost areas and among entry-level buyers who are sensitive to price increases.” NAHB also reports that “new home sales rose 6.9 percent in the Midwest, while sales fell 1.5 percent in the South, 12 percent in the West and 40.6 percent in the Northeast.”
Woodshop orders are obviously tied somewhat to those numbers. Casework and furniture production tends to follow housing trends, albeit often several months afterwards as it takes some time for new homes to be completed and ready for cabinets.
And the materials being used in woodworking are changing, too. A report from the Ohio Forestry Association (ohioforest.org) that was published last spring includes a graph related to Eastern U.S. hardwood production. It notes the region’s output peaked in 1999 at about 12.6 billion board feet. But then the industry took a nosedive in 2008/9 during the recession, and only climbed back to a steady pace in 2014. Over the past three years, production has stabilized at much lower numbers than those prior to the recession (2017 was just 8.3 bbf). Part of that is changing consumer taste, which saw a switch from hardwood to painted, foil and other finishes in casework, and also an upswing in laminate rather than solid hardwood flooring.
Foreign trade
Forecon Inc. (foreconinc.com) is a forestry consulting firm that has served growers in the New York, Pennsylvania and West Virginia region for the past 64 years. The company reports some price declines for high value logs such as black cherry, maple and oak over the past few months, but is also quite optimistic about the new USMCA agreement that replaced NAFTA.
Most of the provisions of that deal won’t be activated until 2020, because the governments of the U.S., Mexico and Canada still have to approve it. Canada fought hard to keep Chapter 19 (an arbitration system) in place as part of the deal, and it succeeded in doing so. The Canadian government has used that provision many times over the years to successfully challenge U.S. restrictions on softwood imports. Canada supplies roughly one-third of U.S. softwoods, and last year (2017) the U.S. began imposing a 20 percent tariff on that supply, which of course increased prices. It’s important to remember that U.S. customers end up paying those new taxes, not the Canadian government. Plus, huge fires and pine beetles have also impacted supplies over the last couple of years, further edging prices upward. And it’s not just that the tree inventory has diminished, but the fires make access and transportation more difficult, too. Clearing forestry roads and building new ones adds to the cost of harvesting, and that ultimately means that products such as oak veneered plywood are more expensive.
The rule of thumb among foresters is that the construction industry gets about 8 sq. ft. of a new home’s footprint per tree, so a new home can use between 10 and 29 mbf of softwoods. The numbers here are substantial, when one considers there are a couple of million housing starts each month (single and multi-unit combined).
Custom shop owners who dismiss the softwoods market because they don’t build cabinets out of pine may want to keep in mind that much of the wood product substrate they use is made with softwood. As spruce, pine and fir prices climb, so will the cost of sheet stock cores.
Sales of existing homes
Beyond housing starts, another of the key indicators for trends in the woodworking industry is existing home sales. This market bears watching because such sales impact the amount of remodeling being done, which is heavily weighted towards kitchens and baths. They also reflect the availability of financing for second mortgages. Existing home sales have been falling for several months, as interest rates continue to climb. Currently, a 30-year mortgage for borrowers with excellent credit is about 5 percent, with another rate hike predicted for December. After peaking around 5.7 million homes sold in late 2017, this year’s number is 5.2 million, which indicates a decline of about 9 percent.
For real estate professionals, and consequently for woodshops, one of the most worrying aspects of the U.S. economy right now is a massive increase in the nation’s budget deficit – up almost 17 percent in 2018, according to the Treasury Department (the 2018 financial year ended on Sept. 30.) Most economists primarily ascribe this to a huge fall-off in corporate income tax that was part of a one and a half trillion-dollar tax cut passed by Congress last year, and also in small part to some increased military spending.
And tariffs haven’t helped much to offset the shortfall – the new ones only brought in $6.7 billion more than a year ago, while they cost industries an awful lot more than that. Personal income tax collections actually rose a hair this year, which may further discourage investment in real estate. But most disturbing here is the trend. The growth in federal revenue was five times higher (7.5 percent) back in 2014/15 than it was in 2016/17, and it actually dipped into negative territory by 2018. As the U.S. government competes more as a borrower against people who are buying homes, that trend is sure to both continue and accelerate. And as anybody who has ever spoken with a banker knows, the best time to ask for a loan is not when your income is shrinking. That’s when they raise your interest rate.
One more ripple in the economic waters has caught the attention of some savvy business owners. The Institute for Supply Management (instituteforsupplymanagement.org) has been around for more than a century and one task on its agenda is to track global supplies of parts/raw materials. It’s a nonprofit organization, and its October monthly report begins by stating that its Purchasing Managers’ Index fell 2.1 percent and new orders were down 4.4 percent. Production was also down 4 percent, and inventories dropped 2.6 percent – all in a single month. Prices, on the other hand, rose 4.7 percent over September’s reporting period. Of the 18 manufacturing industries that the Institute monitors, four contracted in size during October – and wood products was one of those.
The government view
One way to judge the health of the wood industry is to take a look at its employment numbers. The U.S. Bureau of Labor Statistics includes woodshops in a subcategory that it calls Wood Product Manufacturing, which includes “establishments that make wood products from logs and bolts that are sawed and shaped, and establishments that purchase sawed lumber and make wood products.” It doesn’t include forestry or sawmills.
The sector employs a hair over 400,000 people and if a woodshop is finding it difficult to find people with experience, here’s why: the industry currently has an unemployment rate of just 1.2 percent. That rate is actually rising a little: in August, it was 0.2 percent and in September 0.7 percent. Strangely, the lack of experienced woodworkers hasn’t translated into higher paychecks. Average pay rates for nonsupervisory workers in October were $17.96 an hour, which has only trickled up a tiny bit since January’s $17.70. That translates into an annual wage rise of just over 1.2 percent in an economy with an inflation rate of 1.9 percent. Shop floor workers are losing a little ground there.
The bureau also publishes predictions for employment over the next ten years (the latest numbers are for 2016 to 2026), and its statisticians see a woodworking workforce that grows 3.6 percent over those years, or roughly 0.36 percent a year. While most operations hold their own, and machining grows a bit, the number crunchers only identify two areas where they see jobs declining – in finishing (-0.4 percent) and saw operators (-0.3 percent). One assumes those mild decreases can be attributed to projected increases in the use of robotics and automation.
In the shorter term, both wages and hiring nationally showed continued strength in the October jobs report, where unemployment overall in the U.S. economy remained unchanged at 3.7 percent.
The bottom line
The wood market, and more specifically products made from wood, wood composites and related materials, is quite healthy and reflects similar trends in the larger economy. The industry’s current challenges include finding experienced or well-trained people to hire, rising interest rates and a consequent fall-off in home sales, plus tariffs and other factors that impact the costs of both imported and domestic materials and equipment. As the availability of overseas tooling and machinery tightens, U.S. products are subject to the laws of supply and demand. So, domestic pricing will see some gains.
There are lots of bright and encouraging long-term predictions for the industry, as new robotics and CNC-related technologies (such as more efficient material handling) continue to emerge. The cost of such technologies will continue to decline as they become more mainstream. Advances in both finishes and finish application technology are also making that area of production safer, more environmentally responsible, and consequently more insulated from legal challenges. And new apps from major machinery suppliers are helping trim the costs of both maintenance and oversight.
In international trade, the USMCA agreement may open some new avenues for settling trade issues regarding Canadian softwood imports. And the current slowdown in the Chinese economy may encourage that government to open the door a crack in negotiations about hardwood logs, sheet goods and completed products.
Industry 4.0 and other technological advances are making shops leaner and more productive, and this is in some part compensating for the shortage of trained workers. Plus, science is always opening new doors. Take, for example, tall buildings. In October, Oregon Business ran a story on veneer manufacturer Freres Lumber, a company that is running the first mass-plywood operation in the world. The factory is pioneering a new direction in the wood industry, where laminated panels are being built to replace large steel and iron structural elements. The ultimate goal here is to facilitate the construction of essentially wooden skyscrapers by replacing metal girders with laminated wooden ones. While this sector is still in its infancy, and it has had a few hiccups, it definitely shows a lot of promise.
On a much larger scale, the world population continues to grow at a steady rate, and hereto underperforming economies continue to emerge and become larger consumers of everything from kitchens to hospital cabinets and dining room tables. So, global demand looks pretty healthy for the wood industry. Even the domestic outlook is promising. The U.S. is still in the top 10 nations for personal income (now ninth, behind Iceland, Norway and Switzerland among others), and its gross domestic product (GDP) is still ranked number one in the world at roughly $20 trillion in market value for all goods and services produced within its borders. However, according to the CIA, the U.S. has now fallen to 19th in per capita GDP, and that’s a stat worth watching as other economies become more automated.
Finally, the World Bank still includes the U.S. in its list of the top 10 ease-of-doing-business rankings, coming in at eight (New Zealand got the top spot, followed by Singapore and Denmark). Considering the number of overseas companies represented at both IWF in 2018 and AWFS in 2017, that’s a critical element for the industry’s continued growth in the global economy.
This article originally appeared in the December 2018 issue.
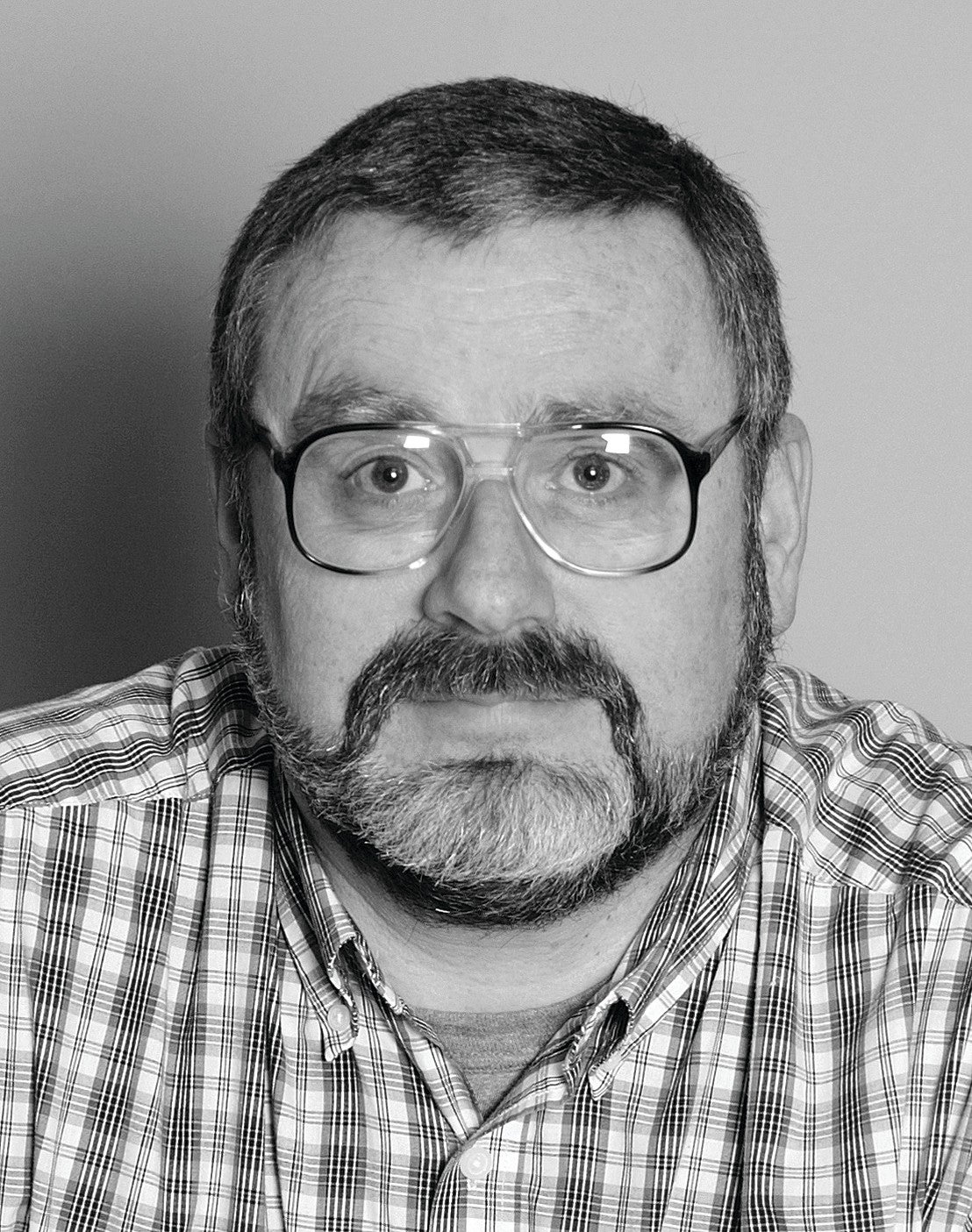