Are we swapping tenons for toolpaths?
The U.S. Bureau of Labor Statistics says that there are 163,500 professional woodworkers in America, and as of May 2017 their average pay is $30,850 a year.
The U.S. Bureau of Labor Statistics says that there are 163,500 professional woodworkers in America, and as of May 2017 their average pay is $30,850 a year. The bureau defines woodworkers as people who “manufacture a variety of products such as cabinets and furniture, using wood, veneers, and laminates. They often combine and incorporate different materials into wood.”
That’s a pretty unromantic definition of a woodworker. Most people, when they hear the term, tend to think of the kinds of artisans who belong to groups such as The Furniture Society, and who care as much about the art in their craft as they do about simply making a living.
Widening those parameters, the government says there are a hair over a million professional carpenters in the country (it fluctuates depending on the season) and they make on average just over $45,000 a year. And CNC operators, according to the Feds, take home significantly more, with an average gross of $55,770.
Those numbers are important when discussing woodshop education and training, because of the changing nature of the work. A few years ago, a woodworker was more in tune with that romantic notion – essentially somebody who used table saws, clamps and hand tools to build casework and furniture. Today, those artisans are fewer and farther between, as the vast majority of professional woodworkers are either assembling outsourced RTA casework, or using CAD/CAM technologies to program CNC machines to make parts.
And herein lies the rub. A strong background in traditional woodworking is still a desirable attribute for custom cabinetmakers and furniture builders. However, a knowledge of mortises and movement seems increasingly unnecessary for a new generation of cabinet builders who essentially load sheet stock into one end of a machine and snap casework together at the other end. A telling stat is that about half of those boxes no longer exhibit any natural wood grain. The doors are plastic or paint.
As Bob Dylan used to say, the times they are a-changing …
Colleges and courses
Woodshop education comes in a number of formats. There is the traditional on-the-job training that is sometimes formalized in a guild or union hierarchy, and can run the gamut from apprentice through journeyman to master. There are also many shops that train without that structure, and simply rotate people through various stations until they become accomplished. Then there are unaccredited courses that are taught by professionals in their own woodshops, and unaccredited schools of woodworking where a number of professionals form a core of instruction so that they can offer more courses with specialized options.
There are also an increasing number of accredited college level courses that cover everything from evening adult education classes to full four-year degrees or two-year certificate programs. These are of special interest to professional custom shop owners because the focus is often quite broad. They can include some forestry and conservation background (planting, harvesting, sawing and drying); a detailed survey of the physical attributes of timber (moisture, movement, grain and color); hands-on shop training in joinery, assembly and millwork; and more and more a strong immersion in the technologies of CNC work.
Among the more vigorous of these is the woodworking program at Cerritos Community College near Los Angeles (cms.cerritos.edu), which offers classes in furniture making, cabinetmaking, CNC woodworking and related topics. The campus includes 27,000 sq. ft. of shop space that’s equipped with more than 100 machines. Over 40 different classes cover topics including face frame and frameless cabinet construction, CNC woodworking, architectural millwork, table and case-good construction, hand tools, turning and veneering.
Many larger colleges and universities are also wading into the world of Industry 4.0. For example, Clemson University’s School of Architecture in South Carolina includes a facility that is now home to two CNC routers (an AXYZ 4008 and a Techno 4896) and instructs students in programs such as RhinoCAM, V-Carve and MasterCAM. Northcentral Tech in Wausau, Wisc., offers a CNC router certificate program that earns eight credits toward a full degree, and teaches students how to design in AutoCAD, then program and operate a CNC router. And it’s not just community colleges – Auburn, Fullerton, San Jose State, Pensacola State, Indiana University, Northern Michigan, University of New Hampshire, Oregon State, Virginia Tech and George Washington University among others all offer either wood science, CNC, luthier or general woodworking courses.
Almost every city of any size in America boasts at least a two-year college and/or some trade schools. Nowadays, virtually all of them offer CNC or CAD/CAM instruction, even if they don’t have a program that caters specifically to woodworking.
Private schools
Woodshop owners often want their CAD/CAM people to understand something of the materials they use, and the logic behind various methods and techniques. Wood isn’t as predictable as plastic or metal, and it’s good to know how it may behave. Those businesses may wish to send employees to a hands-on, short-term course that explains the basics, and also delivers a modicum of experience in a matter of days.
Among the most respected schools are Gary Rogowski’s Northwest Studio in Oregon, Yestermorrow in Vermont, Arrowmont and also Lonnie Bird’s school in Tennessee, the John C. Campbell Folk School in North Carolina, and Peters Valley Craft Center in New Jersey. Mississippi State hosts the Franklin Furniture Institute, which is a multi-disciplinary effort involving the colleges of Business, Forest Resources, Engineering and Architecture. Few institutions can rival the craftsmanship of the North Bennet Street School in Boston, which offers full-time and part-time courses in cabinetmaking, furniture building, carpentry and violin making, or the Furniture Making Program at the Furniture Institute of Massachusetts.
In Maine, Peter Korn and his team have assembled one of the world’s best woodworking programs at the Center for Furniture Craftsmanship in Rockport. The campus offers courses in furniture making and related skills such as carving, turning, marquetry and finishing. There’s everything from weekend community classes to an intensive eight or 12-week course, or a nine-month comprehensive. College credit for courses taken at the Center is available through the University of Southern Maine. The number of credits is determined by the duration of the course and a student’s meeting some specific educational goals.
The Marc Adams School of Woodworking in Franklin, Ind., is celebrating 25 years this summer and has nearly 40,000 sq. ft. of space. It includes four large bench rooms, three tool rooms, a dedicated turning center and a multimedia room, among other facilities. Each instructor’s bench is outfitted with a video system.
The Anderson Ranch Arts Center in Snowmass Village, Colo., offers an array of instruction is almost every art form, including woodturning and furniture design. Over the years, almost every notable name in furniture has appeared somewhere in the catalog, either as an instructor or as a visiting artist. Sam Maloof, for example, had a long and fruitful association with the Ranch. Located about eight miles west of Aspen, it’s a place where woodworkers go to enhance existing skills, primarily with hand tools and small machines. The atmosphere makes one contemplate design and technique more than production values.
In California, dozens of notable facilities are headlined by institutions such as the William Ng School in Anaheim, Palomar College’s cabinet and furniture technology program, David J. Mark’s studio in Santa Rosa, and the woodworking program at College of the Redwoods founded by Jim Krenov.
Other options
Most software and hardware suppliers have some form of online instruction available, and it’s usually related to a specific purchase. Most machines and design packages have user groups online that address just about anything that comes up. However, those don’t generally cover basic instruction, and are no substitute for hands-on learning or having a human instructor in the room. They fill a need but are often more of a two-dimensional solution to a three-dimensional challenge.
For smaller shops, many retail stores have an ongoing program where they present short classes on specific techniques.
Educational programs and instruction can be found through a number of professional organizations such as the Architectural Woodwork Institute, Cabinet Makers Association, Forest Products Society, The Furniture Society, Guild of American Luthiers, National Hardwood Lumber Association, Society of American Period Furniture Makers, Stairbuilders and Manufacturers’ Association, United Brotherhood of Carpenters and Joiners, and Woodwork Institute. These groups variously offer online education and training materials, some classes, tours of businesses, lecture series, publications, trade shows and other venues and events where woodworkers come together and learn from each other, or from experts in various aspects of the industry.
One of the most productive ways for employees (especially new ones) to learn is to offer them full use of the shop on their own time, after work hours. Many shops do this in the evenings or on weekends, as long as there’s a supervisor or shop foreman on hand too, who is working on his/her private projects. This generous approach allows woodworkers to explore options and solutions that don’t always present themselves in the normal workday – especially in businesses that tend to stick to a fairly tight design portfolio. It lets experienced people show newcomers how to run machines that they don’t always get to use during the workday. And it often allows the new guys to teach the old pros how to run a CNC to make more than flat panel doors.
The slow one now will later be fast.
This article originally appeared in the August 2018 issue.
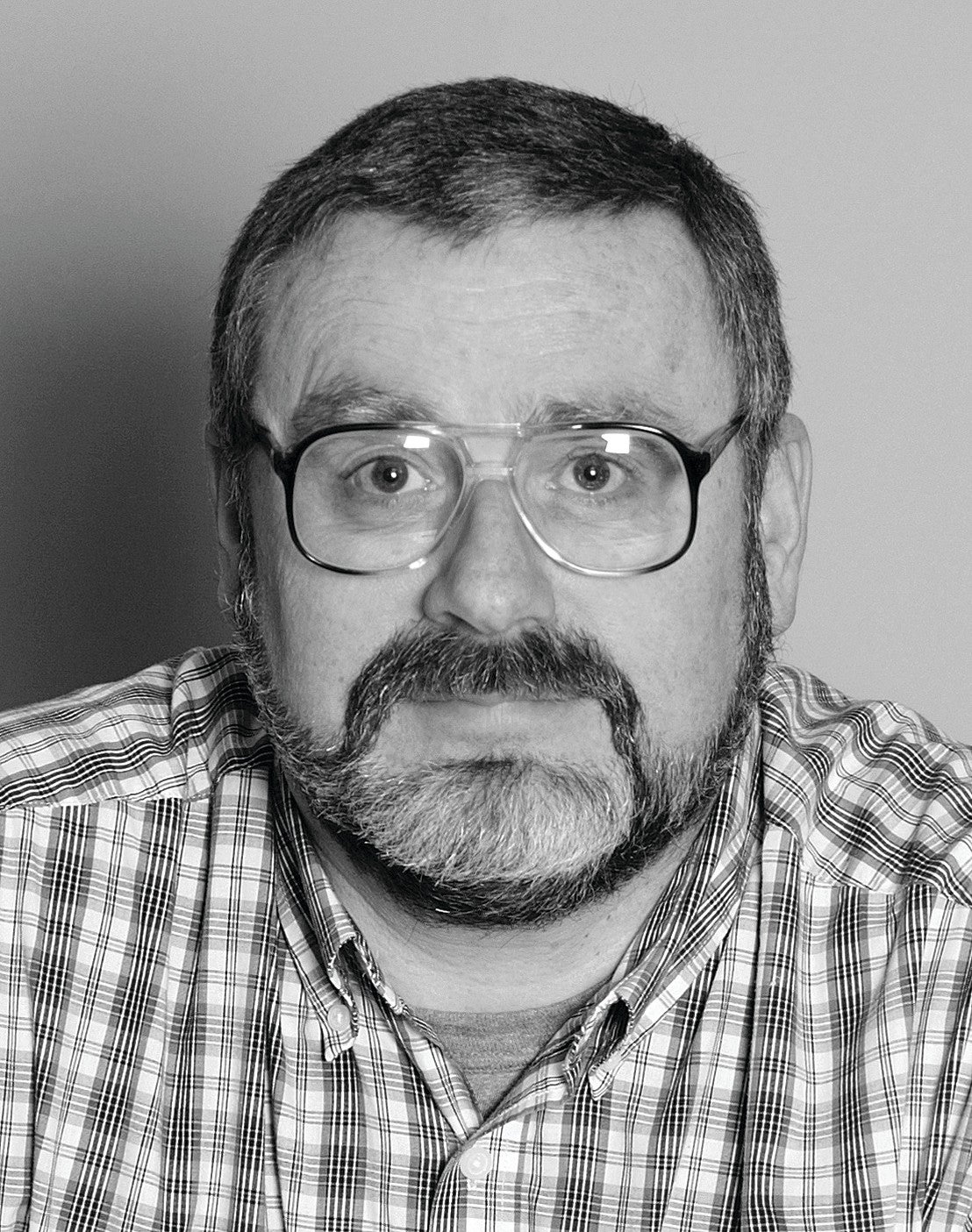