An exquisite solution
Aggregate heads can add some of the advantages of extra axes and 3-D milling capability to a basic 3-axis CNC router
A standard CNC spindle points the tool (router bit, etc.) down toward the bed of the machine and thus toward the work that is secured there. The bit is vertical. It can plunge into the work, travel across it (side to side, X) or along it (back to front, Y), and change its height and thereby the depth of cut (Z). Some bits can also use a side profile to shape edges.
But as long as they’re chucked in a standard spindle, they can only move in, out, up and down. They can’t undercut or mill at angles other than 90 (Z) and 0 (X and Y). There are a few workarounds such as programming multiple stepped cuts or using inverted profiles, but these can require a lot of setup and sometimes special tooling.
So, a 3-axis machine moves the spindle in X, Y and Z. Larger machines often add a fourth axis (A or B), and others a fifth (A and B) to this basic configuration. These can rotate the work while the spindle is moving in X, Y or Z (or in X and Z, or Y and Z simultaneously). An A axis allows the work to spin around the X while a B spins around the Y, and a C spins around the Z.
Confused?
OK, here’s a visual. You’re making a baseball bat on a CNC. The long, square blank lies flat on the worktable, where it is secured mechanically or by a vacuum clamp. The problem here is that a straight plunging bit can’t reach all the way around the bat (underneath) because it can only travel left/right, forward/back and up/down. So, it can easily mill the top of the workpiece and halfway down the sides, and that’s it. But if you add a fourth, rotary axis (similar to the headstock and tailstock of a wood lathe) which can slowly rotate the blank in suspension above the worktable, then the vertical spindle can complete the job. That’s because the rotary axis is able to present the uncut (formerly the bottom) face to the tool. So even though the bit stays vertical, it can now ‘reach’ parts that were previously inaccessible.
If one end of the bat could also be raised and lowered while the blank rotates, that would be a fifth axis.
A few small CNCs and most mid-size to larger 3-axis machines offer the ability to add an aggregate head, which can achieve somewhat similar results. This accessory fits between the spindle and the tool (cutter). Also known as just an ‘aggregate’ or as an angle head, it allows tools such as router bits, circular saws and drill bits to approach the sides and even the bottom of a workpiece at other than the standard vertical angle. It’s a less expensive way to add many of the capabilities of an A or B (or both) axis to an XYZ machine.
An aggregate head is not quite the same as a true fourth axis. When it’s mounted on a 3-axis machine, there is still a limiting factor because the spindle and aggregate head that are holding the tool are usually moving while the workpiece remains stationary. That’s not always the case, but it is generally so. So, a basic understanding of axes and their potential is essential when considering the purchase and use of an aggregate head. For example, a 5-axis router can move either the part or the tool along or around five axes simultaneously. Do you need this? Beyond being able to reach into all kinds of spots, there is also a time consideration. In most cases, the more versatile the machine becomes (that is, the more axes that are available), the less time will be required to move and re-clamp parts or change tools.
Aggregates can, of course, be used on 4- and 5-axis machines to improve their versatility. But small- to mid-sized shops that already own a 3-axis machine often find that adding a 0 to 90 degree aggregate head will solve almost all of their challenges. They’ll be able to cut, rout, sand and profile at any angle between zero and 90. One big advantage here is that a shop can move into a whole new method of assembly. For example, the CNC router will now be able to slot for mechanical connectors in the edges of mitered panels, which opens up new ways to build drawers and not-rectangular casework. Miters are not restricted to 45 degrees, because an aggregate head can work at any angle between 0 to 90.
However, there are some aggregate solutions that just don’t work without a C axis. These are often related to working on curved parts such as stairs, islands and windows. Shops that work in the round, especially in more than one plane (that is, they make parts with complex curves) may want to discuss their exact requirements in detail with a salesperson before assuming an aggregate head alone is the best way to address their needs. It may be time to add an additional axis, too.
Mechanical considerations
If an aggregate head was simply installed on the spindle, it would spin just like a router bit. So, a woodworker must transfer the rotational motion from the spindle through the aggregate to the tool, and this is done by using an anti-rotation solution such as a ring or block that grabs the torque pin on the head and holds it stationary. These are sometimes included and sometimes optional.
Adding an aggregate head will reduce the Z travel of your CNC router. What you are essentially doing is extending the length of the spindle, so it’s extremely important to pay attention to clearance. The bit or blade is now a little closer to the bridge, clamps, toolholder and other elements of the machine. Plus, it can reach around it in more angles. When a sawblade or a long bit is installed, there must be room for the entire assembly (spindle, aggregate head and tool) to move freely in all of the possible directions it might take.
When the addition of an aggregate head reduces the Z travel, and curtails travel near parts of the machine, that in turn reduces the overall size of the available work envelope. That is, the maximum size of the parts being made is going to be a little smaller in some dimensions. If a shop is already close to maximum tolerance, the addition of an aggregate might mean that large parts may need to be milled as sub-assemblies that can fit comfortably on the workspace and be assembled later to form a larger whole. Or, maybe it’s time to swap the 4x8 table for a 5x10.
Another consideration is torque. An aggregate head holds the tool farther from the spindle, so there is more shear (sideways) pressure. That can generate heat, and nothing wears out an angle head faster than excess heat build-up. It may also affect accuracy, especially if the cut is too deep (too high a chip load), the feed (travel) rate is too high, or the rotation is too fast or too slow. Aggregates come with different types of lubrication and cooling that include grease, or an oil and air mister. And most come with a built-in thermometer that lets the woodworker constantly check for problems.
Sometimes the workpiece isn’t absolutely flat, and if a standard cut is made the groove can vary in depth. This can be a problem when, for example, a rabbeted edge must seat fully in the groove. One type of aggregate, called a floating head, is designed to deal with this problem. It allows the machine to register the depth of cut from the surface of the work directly below the aggregate head, rather than from a standard pre-determined Z point. That is, it constantly ‘reads’ the surface and adjusts accordingly, which can be very useful when working with thin veneers or milling close-fitting joinery such as dovetails. The range of travel can be quite dramatic. For example, the Benz floater (item 727WT03601G10M4) has a range of 8mm (more than 1/4”).
The bottom line is that an aggregate head can add immense versatility to a machine, especially when combined with the addition of a fourth axis. But woodshops need to keep in mind the limitations of these heads, especially when it comes to intense usage in a higher volume production environment. They are an exquisite solution for small shops that make one-off parts, patterns and prototypes, or do short production runs. And they can be a valued asset for custom cabinet shops that build one case at a time, or furniture builders who need to work in more than three axes and who are not yet ready to move up to a machine that is capable of continuous 5-axis machining.
This article originally appeared in the April 2020 issue.
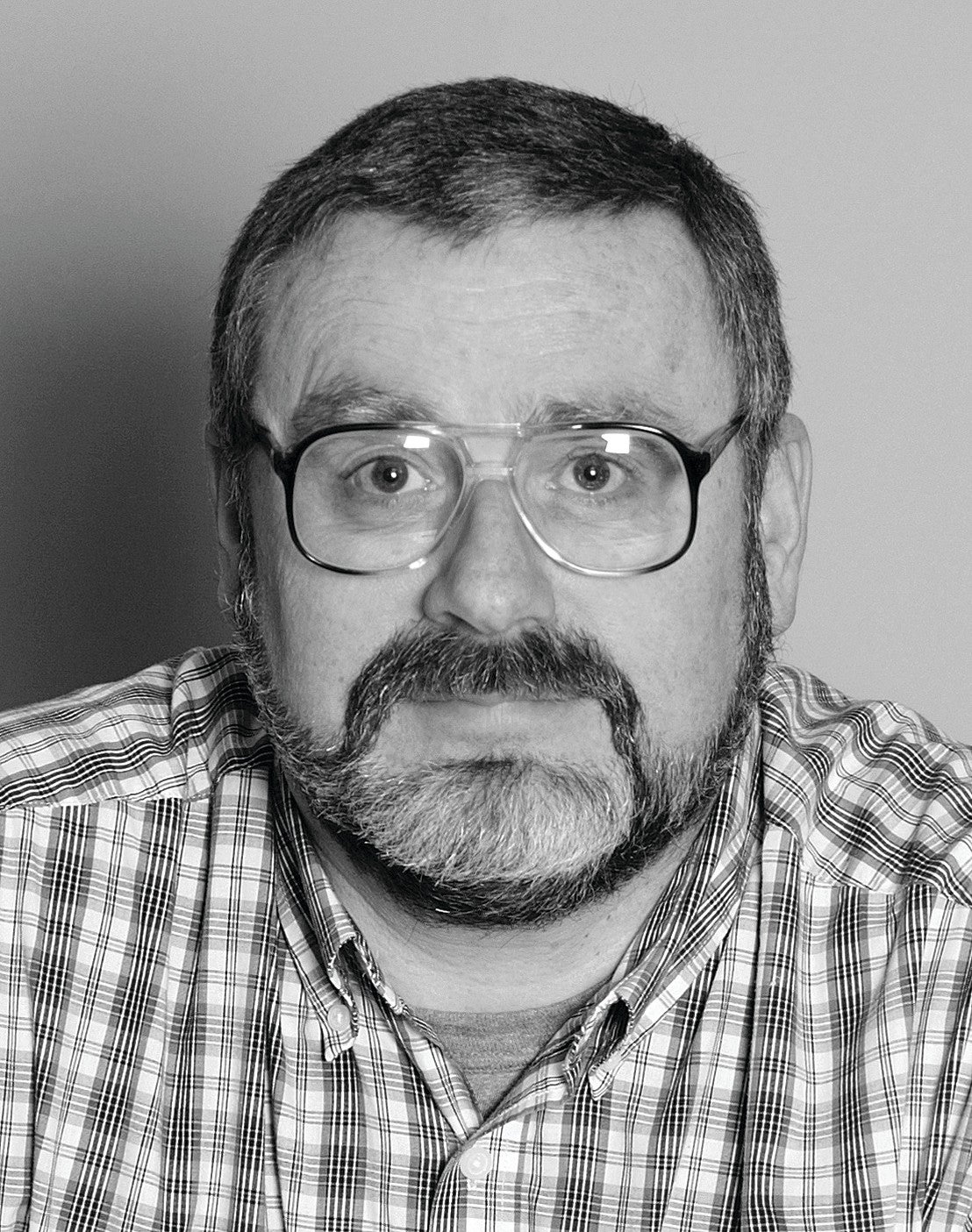