All on the same page
Happy people do good work. For many hardworking and practical shop owners, changing the woodshop environment to achieve a higher level of well-being sounds a lot like earth shoes and…
Happy people do good work. For many hardworking and practical shop owners, changing the woodshop environment to achieve a higher level of well-being sounds a lot like earth shoes and tie-dyed shirts. But there is a very real and factual basis to the concept.
Cultures all over the world, and especially those in the Far East, have long understood that work and well-being aren’t natural enemies. Who hasn’t seen videos of rows of workers exercising together outdoors in a park in Korea or Japan? And while the concept of a group of cabinet installers downing tools to do yoga every afternoon borders on the comical, there are lots of practical things we can do in our shops that help bring a sense of well-being and self-worth to the job.
America’s retail stores are bursting at the seams with imports from China, but one thing that originated in the Middle Kingdom won’t be found on an end-cap display. Free for the taking, the ancient philosophy of Feng Shui has become somewhat familiar to Western interior designers since the 1960s. That’s when the Cultural Revolution attempted to bury this metaphysical art, an act that indirectly vaulted it to wider popularity. Dating back 6,000 years, the origins of Feng Shui simply explored the relationship between man and the universe. On a personal level, it influenced the ways in which people built, inhabited, oriented and decorated their homes and places of work.
Today, Feng Shui has acquired some spiritual overtones, but historically it was far more practical. It was, in essence, the genesis of what modern business regards as the science of ergonomics. Both philosophies support the concept that it’s a lot easier to make a woodshop fit the workers, rather than trying to mold and change people and their habits so they fit a rigid business model.
Dust
Let’s begin with the most insidious and worrisome aspect of being a woodworker. We all think about dust every now and then and somehow most of us achieve a level of denial that allows us to put aside our concerns and reach for a sander anyway. The bottom line on dust is that the smallest particles are the ones that accumulate through the decades and cause us problems right about retirement age. There’s an unwritten covenant that says dust goes with the job, that it’s an acceptable risk, like hemorrhoids are for truck drivers or suntans for mailmen.
But it doesn’t have to be. Fine dust can, in fact, be one of the easiest problems to fix in the woodworking world. All it takes is a little money. The first step is to get a good handle on how well the filters on the central dust collector are working (or the bags/cartidges on individual, designated collectors in smaller shops). There’s an optimum filter size: if the holes are too small the system clogs and if they’re too large the fines get through. The best way to assess a system is to contact a fabric filter manufacturer or a dust collection system installer and ask for an audit. They’ll need to know how many machines you run, the airflow, particle sizes, ductwork specifics (diameters, lengths of runs, connections and bends), the volume and speed of the air your current system is pulling and a host of other data such as the cubic volume of the woodshop. It’s a royal pain to gather all the data, but it’s the only way to arrive at an efficient and effective solution.
Many owners don’t go through the process because they feel the only answer will be to replace their entire system, but that’s rarely true. For example, better bags and simpler ducting can go a long way to improving performance without a huge capital outlay. New fabrics being used in bags now can dramatically improve performance. Electronic (smart) blast gates can radically increase efficiency with a relatively small investment. Even just moving a collector closer to a machine or adding a second port to a sander might be all that’s needed to solve a seemingly daunting problem.
Using clear plastic curtain walls to isolate various work zones can have a huge effect on both dust collection and noise. That reduction in the cubic volume of free air around a workstation or a machine might be all it takes to make a ceiling-hung air scrubber work efficiently. By asking it to filter a small volume of air instead of trying to keep up with all the dust in the entire shop, strategically placed (and fairly inexpensive) air scrubbers can remove an astonishing volume of suspended fines from the environment.
Gathering fines at their source helps, too. Switching from traditional sanders to a new generation of orbitals designed around dust collection (such as the Rotex line from Festool) can be a little expensive, but it pays off in both employee health and wellness and also in the time it takes to tack cloth and/or vacuum projects before and during the finishing process.
Lighting
Two phrases that have become familiar in the last few decades, especially in shops that build kitchens or entertainment centers, are mood lighting and task lighting. The ambient (overall) lighting in a workspace can actually change the way a worker feels, especially in winter. While volume of light and the placement or orientation of lamps are both important, the color of the light is perhaps the most essential factor in determining one’s mood. Color is measured as temperature on the Kelvin scale. Cool (bluish-white) light is above 5000K, while warm (yellow to red) light is close to, or slightly below 3000K. Natural daylight is in the 5500K to 6000K range. Many bulb manufacturers, especially those making tubular fluorescent bulbs, will mark the approximate temperature on their products. Changing the temperature of the light in a workshop is usually just a matter of changing the bulbs.
Once the shop’s overall mood has been established, it’s time for specifics. Providing workers with concentrated, superior task lighting at each machine and bench is essential. In general, the brighter the light, the better the quality of their work will be. (There is a point of diminishing returns, where the light is so bright that everything always looks flawed.) A well-lit workspace will, in general, deliver much better quality work before finishing and, of course, help achieve a superior finish, too. Doing better work makes people feel better about themselves and this plays into the goal of ergonomics which is to “optimize human wellbeing and overall system performance.”
It’s an upward spiral. Happy people do better work and better work makes people feel happier.
Ventilation
Removing dust from the woodshop’s air is a basic need, but a companion requirement is to constantly introduce clean air. Ventilation doesn’t only refer to removing contaminants: it also recognizes that people need fresh air to feel good.
Many of the small things we do in a woodshop can release minute (and sometimes more significant) amounts of dangerous or unwelcome chemicals into the environment. In more extreme climates, where the doors and windows are often sealed up for months at a time to conserve either heated or cooled air, these particles can remain airborne or resettle on surfaces where they can be disturbed and become airborne again. Some of the more mundane activities that produce possible toxins are mixing or sanding small amounts of finish, touching up with a spray can or even a brush and using a resin block to clean an abrasive belt. But a sealed-up workshop can also contain minute furnace byproducts, emissions from PVC and other plastics and even residue from chemicals used to clean bathrooms or to polish cabinets and counters in the showroom. Various materials, especially sheet goods, can emit formaldehyde and other organic compounds. (In 2011, the U.S. National Toxicology Program described formaldehyde as “known to be a human carcinogen.”)
The key to good ventilation is constant air changes, but if the shop is located next to something aromatic like an oil refinery or a feedlot, that might be a problem. If moving is out of the question, then it’s a good idea to have the air tested regularly, especially if the neighbor is a potential source of pollution. Ionizing and charcoal filters can help. If the air in the neighborhood is relatively pollution-free, then most shops will want to conduct air changes through a heat exchanger, if they are located in a geographical region that requires heating or cooling. These are fairly simple devices that help a shop owner save some of the money he or she spends on heating and cooling. In winter, they run cold air from outside across a plenum or through a series of pipes that contain warm air that is being exhausted from inside. Some of the heat travels from the contaminated hot air to the fresh cold air, pre-heating it so that it doesn’t require as much fuel to bring it up to the same temperature as the air that remains inside the building.
Ventilation is also critical because of vapor buildup. Warm air tends to hold onto water vapor and high humidity inside a sealed woodshop just isn’t a great idea. Beyond rusting tools or contaminating finishes or even affecting compressed air, moisture can be a carrier for unhealthy mold, mildew and other organisms. A warm, moist environment is especially hospitable to bacterial infections. However, some new medical data indicates that a virus such as influenza can actually prefer a dry, cold environment. According to Coldandfluecentral.com, “a recent study suggests that maintaining an indoor humidity level between 40 to 60 percent can reduce the survival of flu viruses on surfaces and in the air. We’ve all come to rely upon humidifiers for relief of cough and cold symptoms throughout the years, but now we know they could play an important role in reducing the survival of the flu virus on both surfaces and in the air.”
So while good ventilation and frequent air exchanges are obviously in everyone’s best interests, treating the level of airborne humidity inside the workshop might be a little more subjective. As shops come in many shapes and sizes, a conversation with a knowledgeable HVAC contractor might be in order before one installs those heat exchangers.
Storage
A new meaning for an old word has crept into our vocabulary in the past few years in large part because reality television shows. ‘Hoarding’ is an affliction that causes people to find security in keeping a large volume of things around them, rather than discovering it in their own self-worth. While a woodshop wouldn’t survive long if it descended to the depths depicted on some of these shows, there are still a lot of shop owners who simply stack inventory, old machines, failed projects, raw materials and even unrelated items such as boats or bikes in the woodshop. An organized, efficient space has, as the Reverend Goodrich once said, “a place for everything and everything is in its place.”
One of the most treasured current business philosophies is an adaption of a Toyota Motor Corporation tradition that has become known as lean manufacturing. It’s all about not wasting any time, effort or money on anything that doesn’t affect the bottom line or increase the price being asked of the customer. In such a lean environment, storage and organization is at the core of everything. Here, the workers never need to waste valuable seconds looking for something or reaching for items that are placed a few feet beyond their reach.
Good storage and workstation organization also plays into most other concepts, such as Feng Shui and modern ergonomics. The former would embrace a space where a person feels at one with the environment and is not frustrated or annoyed that the right sanding disks or paring chisel can’t be found. The latter would celebrate the notion that everything is at hand or comfortably within physical reach and no major adjustments are needed. Good storage saves time and time is money. In that same vein, if members of the shop crew work at more than one station, then providing each worker with a tool cart can make a lot of sense. Walking around the shop looking for tools not only wastes that worker’s time, it will often disturb other people, too (especially if they stop for a chat).
If tools are being shared, a manager might consider instituting some kind of reward/penalty system to encourage people to replace equipment as soon as it is no longer being used. This can be a simple as a point system that lets one worker earn an employee parking spot each month. Or the worst offender might have to wait until the last turn to select his/her doughnut on Fridays. The object is not so much to correct an individual’s behavior as it is to create a team spirit where people encourage each other to succeed and do so in a lighthearted, but still slightly competitive, manner.
Good storage also helps with inventory management. If a shop has, say, three different stacks of 3/4” MDF in three different locations throughout the building, then somebody has to visit each pile to do a physical count before ordering. While it makes sense to keep some of each product close to a few different workstations, it might also make sense to set up a central area where a master list is stored for all materials and supplies. As people take a couple of glue bottles out of inventory, there can be a clipboard or chalkboard where they record this so there is a single record in one location of all the bottles in the shop.
On critical supplies that can’t be quickly replaced (perhaps something like a flitch of rift-sawn veneer or a custom stain), adding another step to the system can help a lot. Each night, or perhaps once a week, the crew can individually report how much of this specific item still remains at their workstation. Rather than having a manager spend a lot of time chasing down product and maybe occasionally missing a case or a pallet of materials, such a system transfers the onus to the people who are using the product. The sign-out sheet can be right beside the time clock, so that entering their inventory is the last task they complete every day before clocking out. Doing such an inventory before they leave only takes a few seconds and transferring even this small responsibility to team members can help engender a sense of pride and ownership, which in turn will add to their wellbeing. As Rear Admiral William Leahy once said: “You may be the boss, but you’re only as good as the people who work for you.”
Show your employees that you’re concerned about them and they will be more concerned about what they’re doing for you.
Happy people do good work.
This article originally appeared in the September 2014 issue.
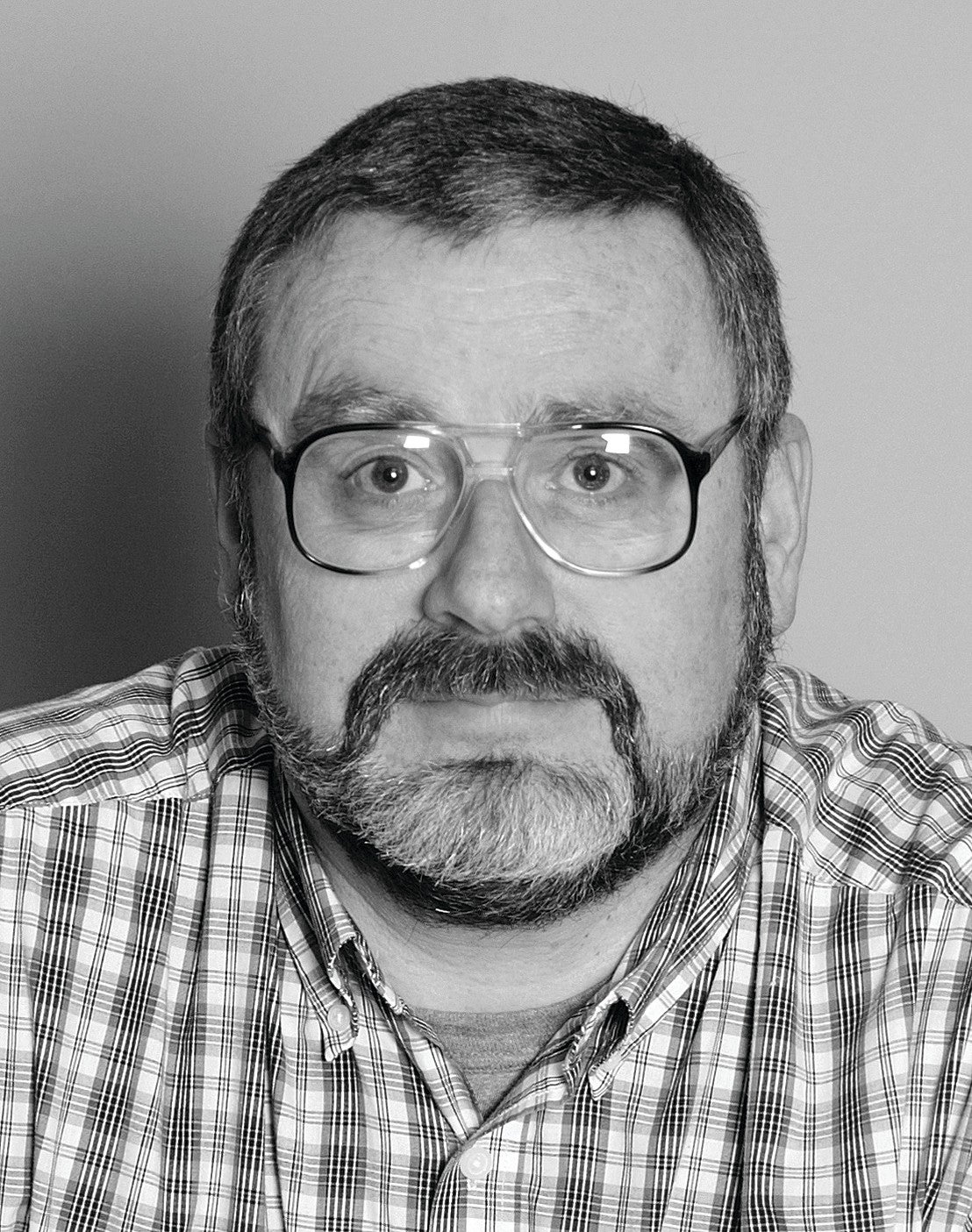